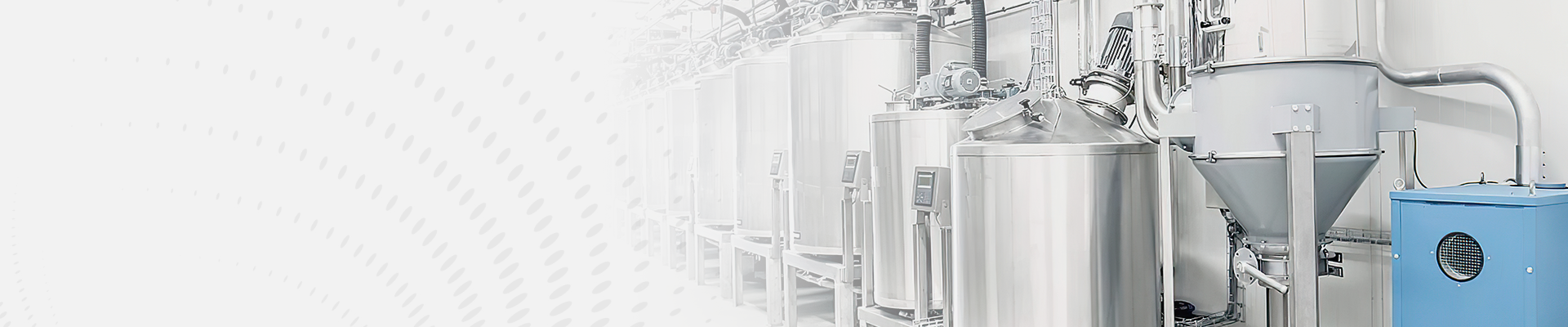
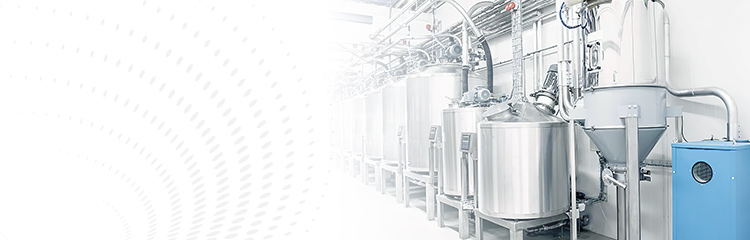
The automatic filling machine adopts Japan Mitsubishi PLC, electrical components of Yadek and German motor to ensure the stable and reliable performance of the equipment, which provides guarantee for the filling machine to work continuously for a long time. Personalized design of one person operation (can be added to the drum buffer and capping device), filling height adjustable, suitable for round, square, flat, a variety of cans and calibers of high-viscosity liquid filling; all-in-one model, easy to move, multi-purpose; two-speed filling "fast and accurate" good stability, filling speed, weight and quality of stable and bring the enterprise reputation, reduce losses and save money, reduce the pressure on the workers, increase production capacity.
The storage tank is located in the upper part of the filling machine, which is an atmospheric tank with liquid level sensor and feeding solenoid valve. The material sent from the previous process is put into the tank through the solenoid valve, and when it reaches the appropriate liquid level, the liquid level sensor sends out a signal to close/stop the feeding; when the material level drops to the specified position, the feeding solenoid valve will be opened automatically to feed the material. The lower part of the storage tank has a discharge port connected with the suction pipe of the filling host through the pipeline, and the host will pump the liquid in the storage tank into the piston cylinder when it is working, and then fill into the bottle through the nozzle.
Automatic filling machine to complete the filling action of the main device, the front of the host is equipped with a number of filling head, both sides are equipped with liquid pumping cylinder, each cylinder corresponds to a filling head. The liquid in the storage tank is pumped into the cylinder and then pressed out to be filled into the corresponding bottle through the filling head. There is a miniature cylinder on the filling head to drive a small piston to open and close the nozzle of the filling head, acting as a valve. In the filling is about to start, the nozzle will be inserted into the bottle, and at a certain distance from the bottom of the bottle to open the small piston to start filling liquid, filling head while filling rising until the liquid filling is completed when the nozzle is closed, and rise to the bottle position. On both sides of the filling table, there are two stopper bars driven by pneumatic cylinders (one is located at the entrance of the bottle, the other at the exit of the bottle), together with the bottle mouth device on the filling table to realize accurate filling.
The conveyor motor is controlled by a frequency converter for stepless speed change and economical operation. After the motor is started, the inlet cylinder retracts and the empty bottles are fed from the conveyor belt to start bottle feeding; then the outlet cylinder extends and the fed empty bottles are intercepted by the outlet stopper. The photoelectric switch is set at the bottle feeding place to detect the number of bottles feeding, when the number is the same as the number of filling heads, the inlet cylinder extends and blocks the inlet from feeding bottles, and the conveyor motor stops. After the filling is finished, the filling head rises, the outlet cylinder retracts, the conveyor motor starts to rotate again, and the filled bottles are sent out.
Main Functions:
Digital input to set the target weight, easy operation, fast filling speed, accurate measurement.
Automatically detect the barrel and start the filling and program, effectively preventing no barrel filling of the wrong action
Automatic protection of barrel mouth, collision protection, tare weight is too light and too heavy
Adopting two feeding methods, large and small, to improve the accuracy of dosing.
Automatic zero clearing at start-up, display of various working statuses during operation, emergency stop and automatic reset protection in case of power failure.
Multi-purpose, adjustable filling height and barrel positioning device on the scale platform, suitable for different heights of square, round and flat barrels of various types
Optional computer connection or real-time printing of filling date, serial number, net weight, tare weight, cumulative weight and other filling parameters.
Flexible movement, explosion-proof configuration, simple operation
The mechanical part is made of SUS316 or SUS304 stainless steel, suitable for food and highly corrosive liquids Humanized design, easy to disassemble, maintain and clean.
The electric control part adopts EXDII4 explosion-proof control box, internal configuration of programmable controller (PLC), and high-performance control head, so as to achieve the ideal effect of accurate quantification, small error, and single operation through perfect cooperation.
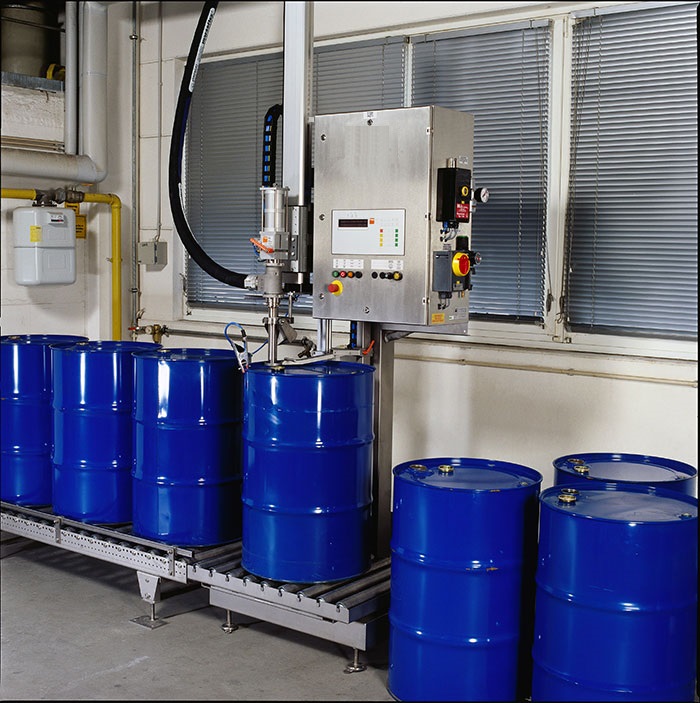
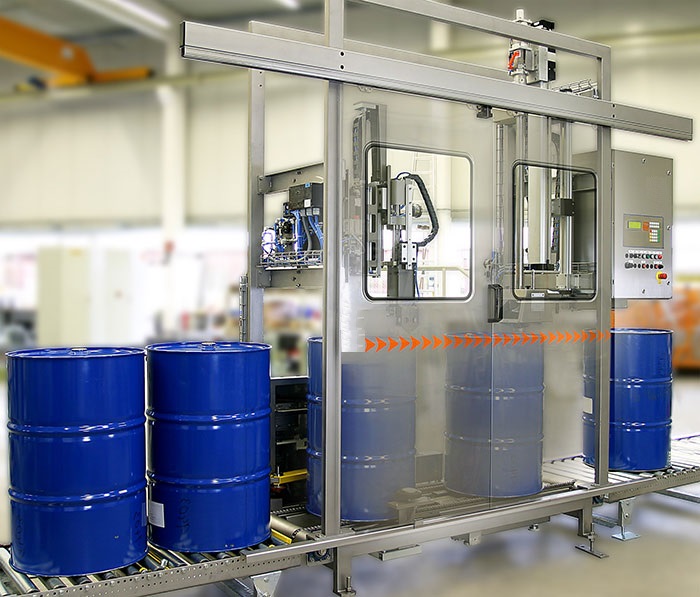
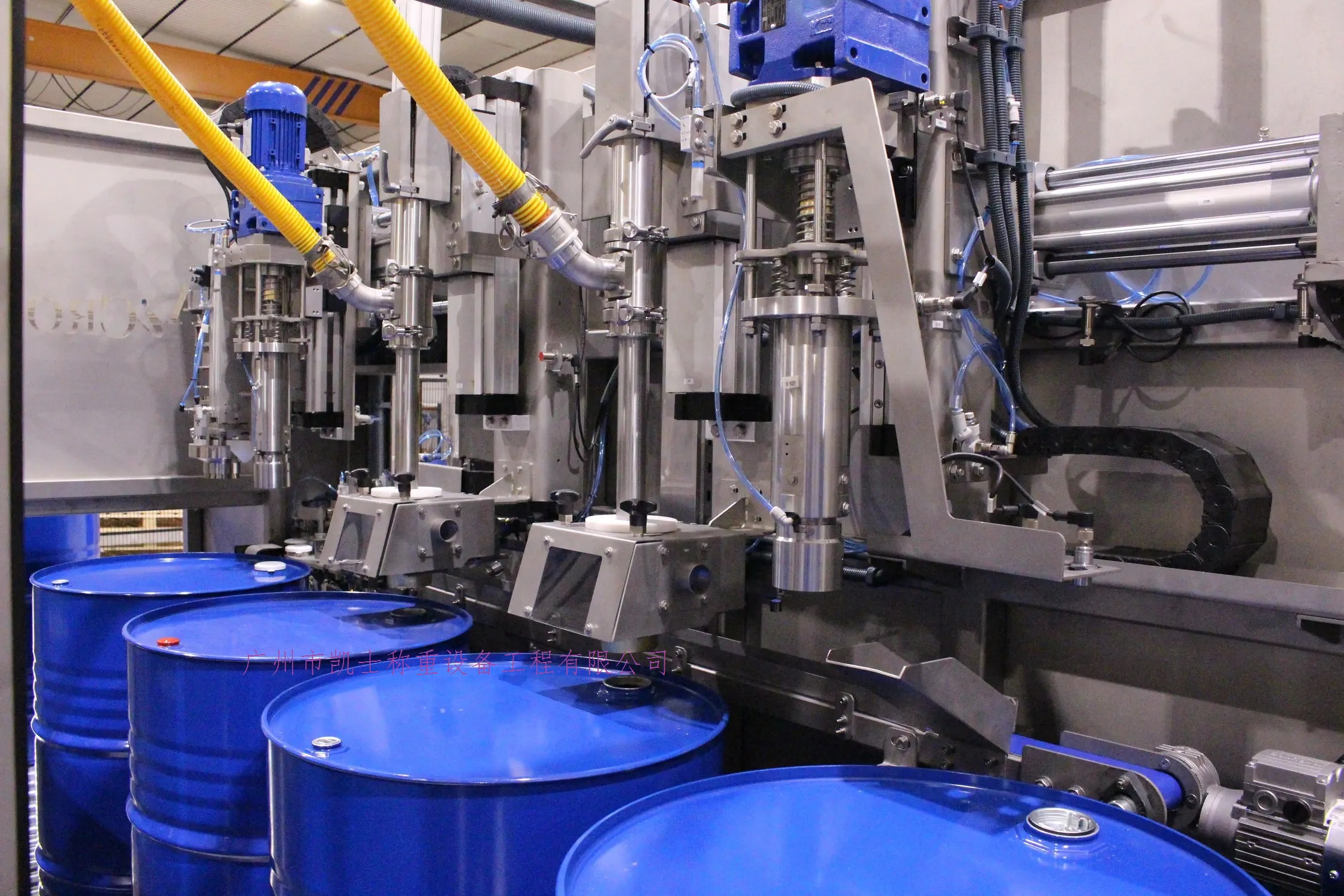
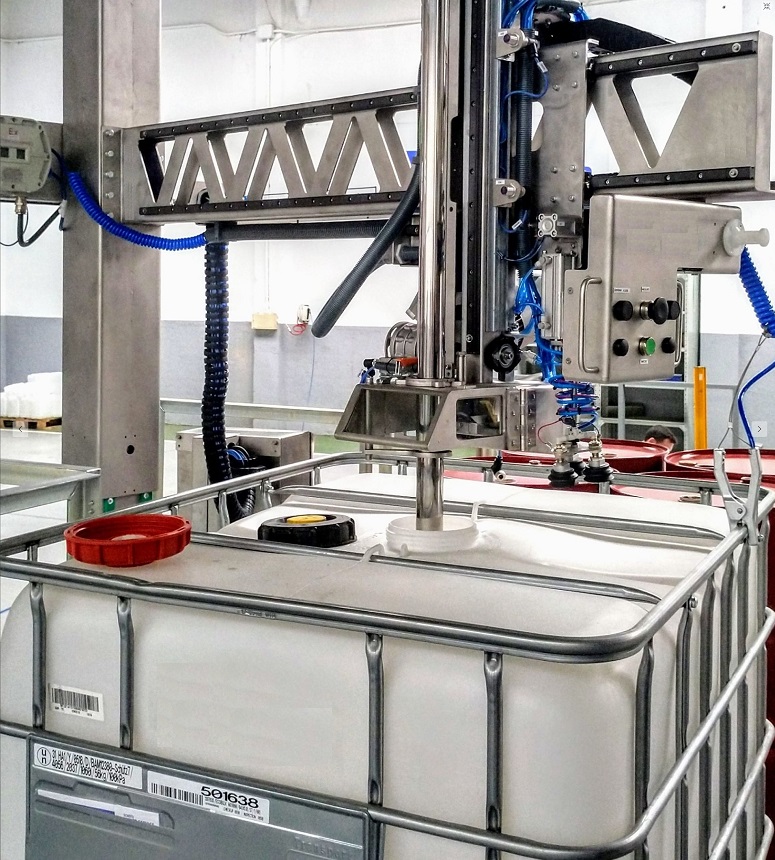
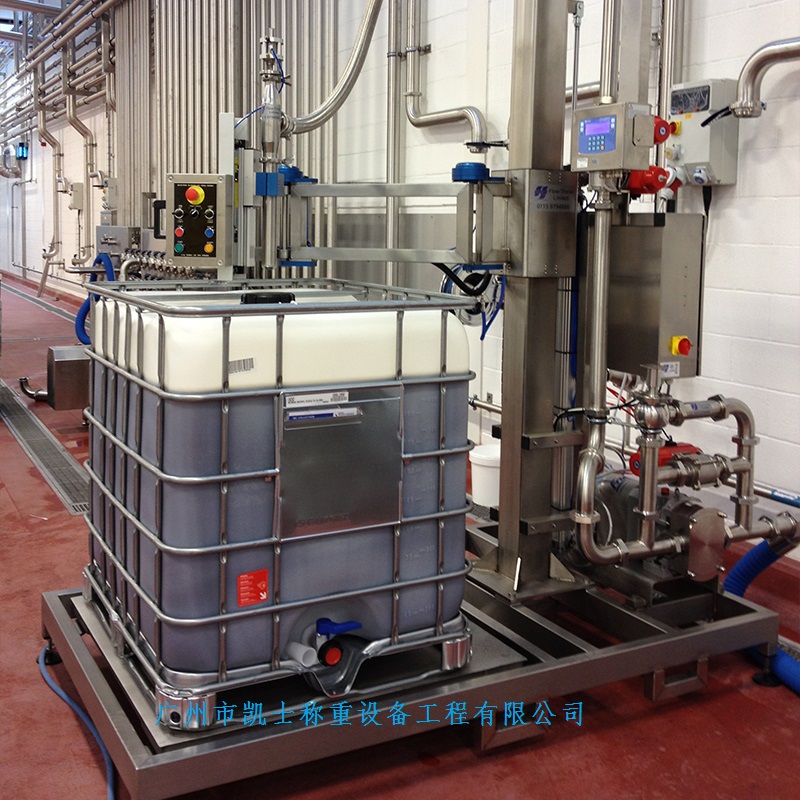

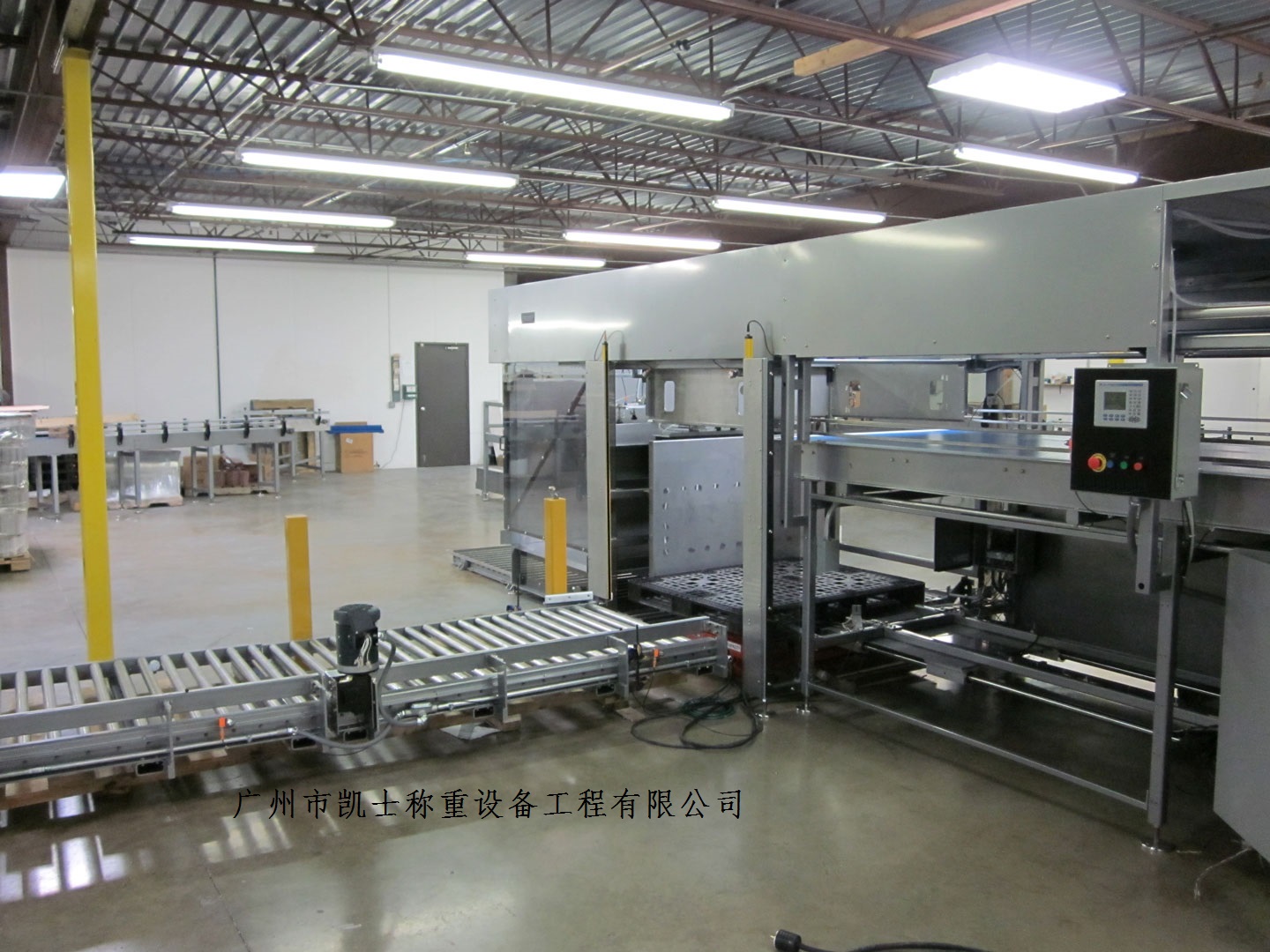
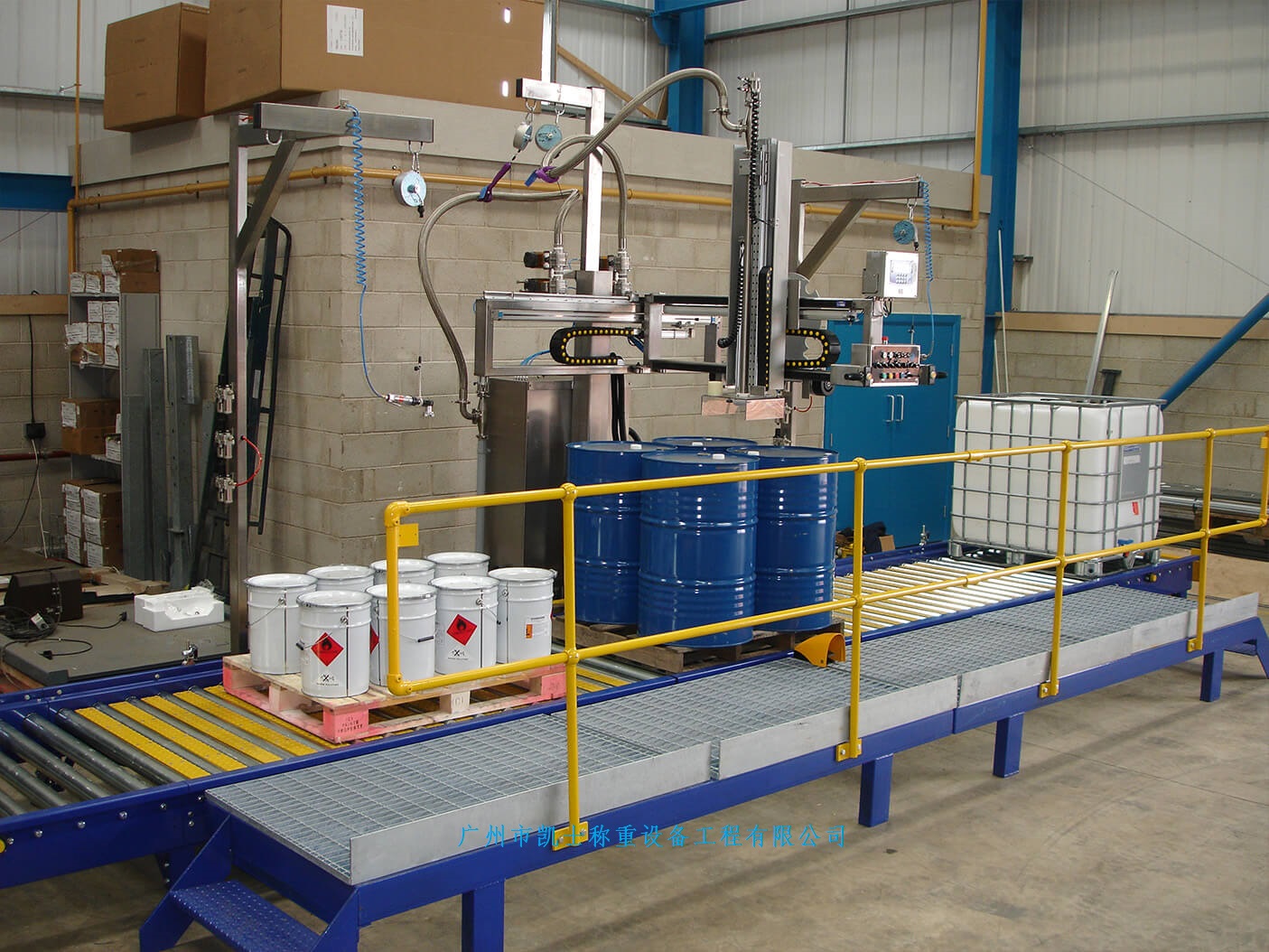
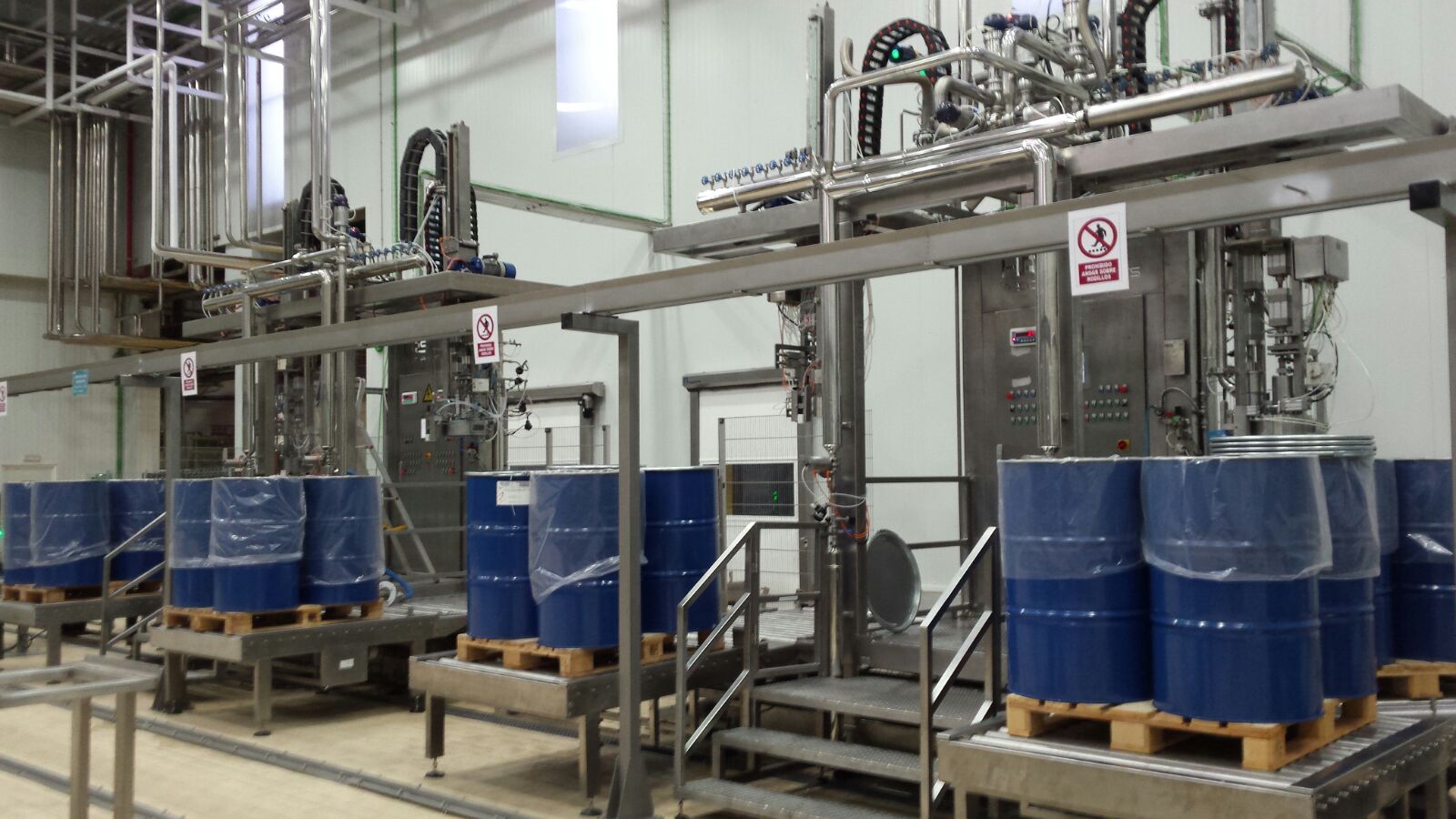