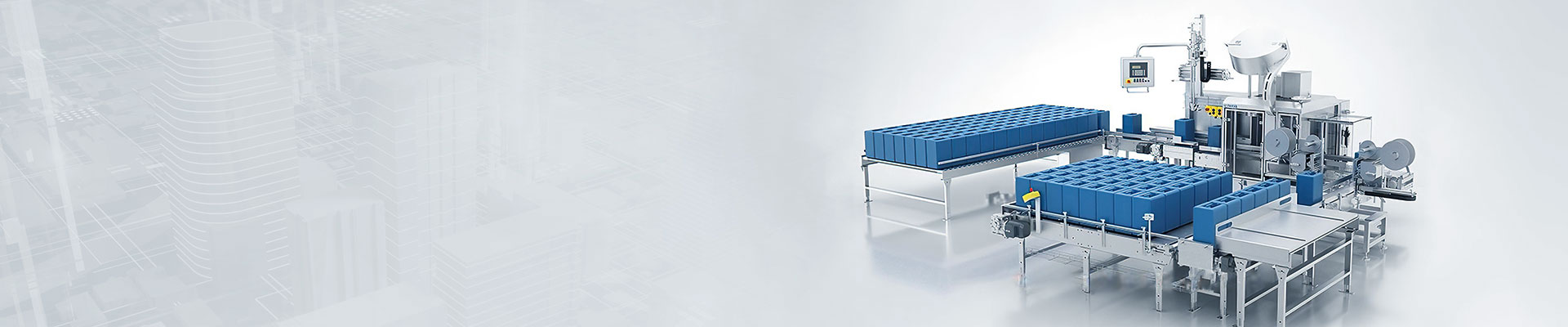
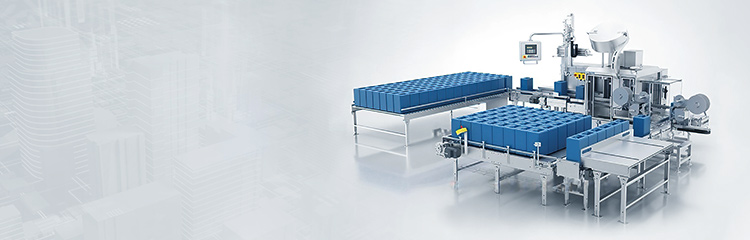
The liquid filling machine is composed of main conveyor belt, defective conveyor belt, filling system, defective driving device, photoelectric sensor (positioning), weighing module, etc. Real-time monitoring of liquid filling machines, detected by sensors. The start and stop of the motor, the filling of the weighing system, the detection, pushing and counting of defective products are controlled by the PLC.

The automatic Filling machine uses the working principle of weighing to control the filling amount at the same time, and the material flows into the container to be loaded by itself (or through the pump to feed and transport). The filling flow rate is adjustable, and the double pipes are opened at the same time during the initial filling. After filling to the fast filling set quantity, the thick pipes are closed, and the thin pipes continue to fill slowly. Up to the set overall filling volume.
The measuring filling machine is composed of main conveyor belt, defective conveyor belt, Filling system, defective driving device, photoelectric sensor (positioning), weighing module, etc. Real-time monitoring of the filling system, detected by sensors. The start and stop of the motor, the filling of the Weighing system, the detection, pushing and counting of defective products are controlled by PLC. After pressing the start button, the production line enters the automatic working state. When the working conditions are available, the bottle enters the filling process with the conveyor belt. After the filling is completed, the conveyor belt continues to start running. When the bottle smoothly enters the filling rack along with the main conveyor belt, the photoelectric sensor signal of the filling rack is sent to the PLC, the main conveyor belt stops for 1 second, and the bottle clamping device is fixed, one second later, the electromagnetic valve of the canning rack opens, the cylinder starts the canning material, and the canning will stop automatically after the canning reaches the quantitative measuring range (and the can is full), there is an alarm during the filling process, and after the canning is finished, the bottle will be filled. The main conveyor starts to start, through the weighing module to detect whether the bottle is full, not full by the push rod into the defective conveyor belt. Check the count during the full bottle process (genuine and defective products are counted separately).