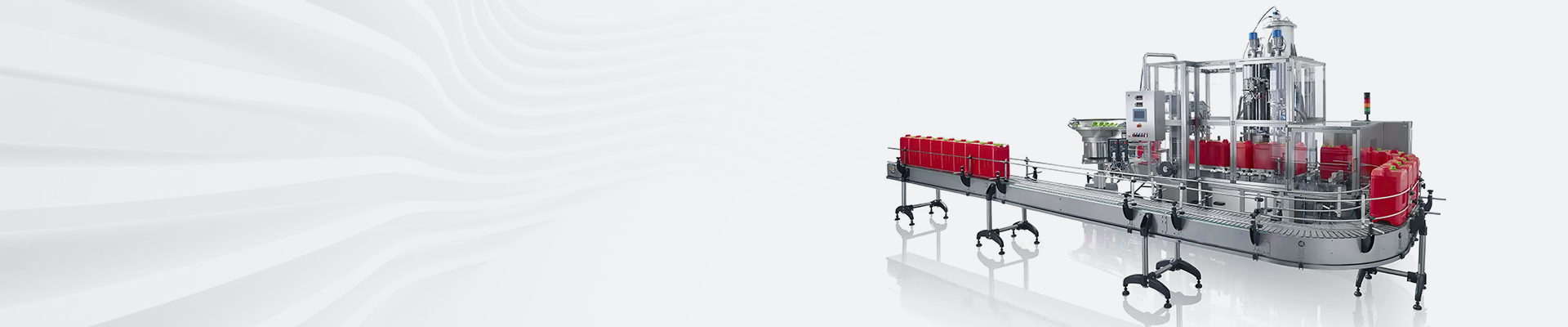
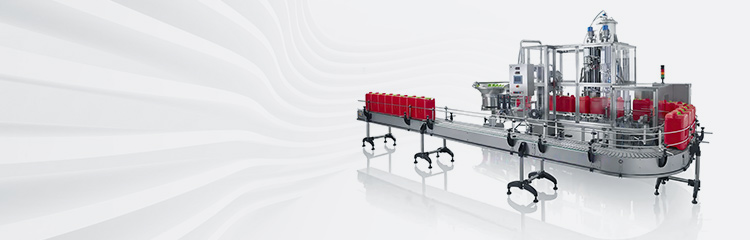

Summary:The liquid filling machine is an ideal equipment for weighing and feeding bulk materials. It integrates transportation, weighing and quantitative control for continuous feeding, and provides accurate measurement data for production control and management of various industrial sites. .
Discussion
With the expansion of the scale of the enterprise and the increase of production tasks, the automation degree of the production workshop is also increased, and the weighing and filling machine is widely used. Combined with the actual operation, the application of weighing equipment of filling scale in polyurethane filling is described. In the automated production line of polyurethane filling, the filling of liquid materials is an important link. Usually, iron drums with a capacity of 200 kilograms of liquid material are used for filling and dosing. In early packaging, the reacted liquid material is added to the discharge chute in the discharge chamber and the filling equipment is gravity fed into the iron drum and measured by electronic scales. The temperature is controlled between 70-80y for liquid polyurethane discharge, and the toxic gases produced by the volatilization of methanol have an impact on the personal health of the workers. In addition, as the temperature decreases, the viscosity of the product becomes larger and larger, thus prolonging the discharge time. In practice, in order to shorten the discharge time, workers often discharge the product at a temperature higher than that required by the process, which is very easy to scald the operator. In addition, the higher the temperature, the higher the volatilization, and the gas spreads to the whole discharge chamber, which brings a great threat to the personal safety of the operator. Therefore, it is especially important to carry out automatic transformation of the discharging and filling device. Automatic filling machine through the expansion of weighing equipment input and output, with the system to achieve the design and control of the discharge automation program transformation.
Liquid filling machine is the ideal equipment for continuous weighing and feeding of bulk materials, which is a high-tech product integrating conveying, weighing, measuring and quantitative control, and a new generation of products improved according to the existing process conditions in China, which is known for its advanced technology, stable and reliable, cost-effective and durable. Can adapt to a variety of production environments, a variety of block, liquid materials for continuous feeding, measurement, production control for a variety of industrial sites, management to provide accurate measurement data. Equipped with RS485 upper computer communication interface, can be formed with the central control machine DCS system.
For the traditional automatic filling machine control in the low degree of automation, based on the PLC PID control algorithm of the material liquid filling machine metering device, can effectively meet the actual situation of the industrial material quantitative feeding process, the following describes the structure of the weighing and filling machine and PLC hardware composition; according to the technical requirements of the process, from the weighing of the filling machine hardware configuration to the design of the application program. The results show that the filling machine performance is stable, reliable operation, weighing instrumentation intuitive and flexible, the realization of the various functions to meet the process requirements, and achieved good application results.
1 structure design
Automatic filling machine controlled by weighing instrumentation, according to the process design program is divided into three parts: barrel import equipment control, measurement, filling control and barrel export equipment control. For the control of the filling and feeding equipment, after the completion of the manual opening and positioning of the barrel, the switch action is detected, and the weighing equipment scans the input/output ports, starts the stepping motor, and pushes the barrel-filling trolley to send the barrels to the weighing platform of the electronic scale of the filling device. The discharge pump runs, the discharge solenoid valve opens, the filling takes place and the electronic scale starts measuring. When the measurement is full, the discharge solenoid valve closes, the circulation solenoid valve opens, and the discharge pump continues to run. When the liquid filling machinery measures full and the discharge solenoid valve works, the synchronized feed motor starts and pushes out the liquid drum until the door of the discharge room, then the workers transfer it to the warehouse by forklift. The filling equipment uses two stepper motors to push the small flatbed trolley carrying the dosage drums in and out along the track respectively. The small flatbed trolley is positioned by the position detection weighing module of the filling machine, which is simply positioned without the need of Siemens stepper motor control module FM353 control. A solenoid valve is used to connect the cart. The purpose of this design is to ensure accurate measurements. Once the small flatbed trolley loaded with buckets has been pushed onto the weighing platform, the other equipment is separated from it so that the electronic scales can weigh it individually. In order to improve the reliability of the weighing and filling machine, a touch screen is used as the interactive interface, with various input and output special modules and special signal conditioning circuits to form a complete control weighing and filling machine.