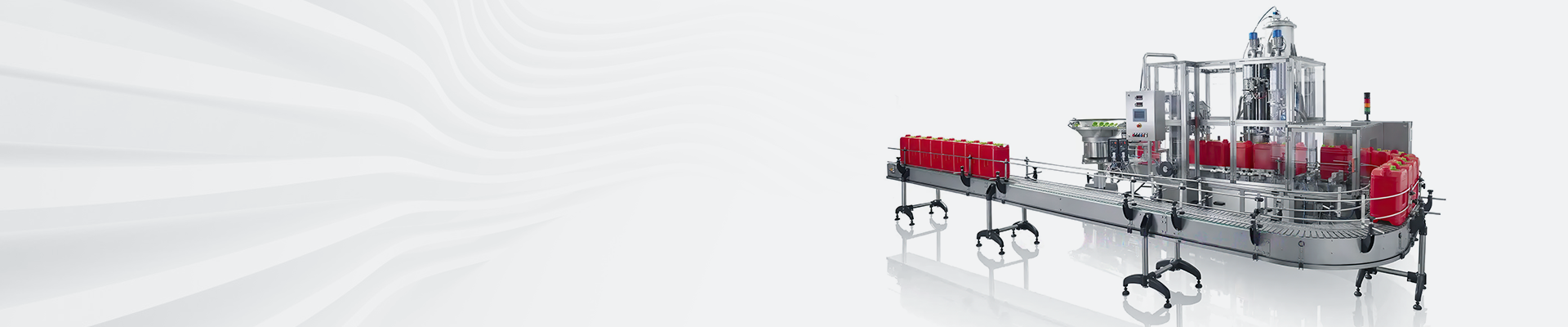
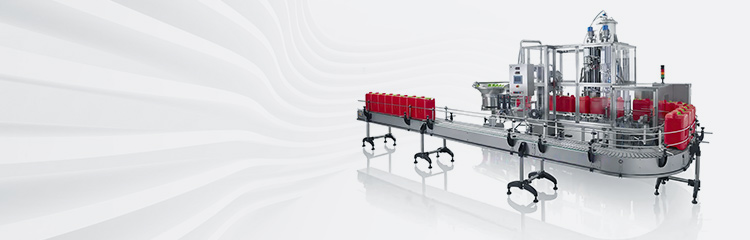

Summary:The batching system provides three different raw materials for the materials. The injection process is divided into three positions: low, medium and high. In actual applications, the number and high and low positions of the liquid level sensors can be changed at any time according to different process requirements.The core part of the feeding system is Siemens 57-200 PLC. The monitoring system software PLC developed by KingView is responsible for collecting input signals and issuing control commands to the auction agency after being processed by the program.The PIC and the host computer are connected through a communication electric field, and the input signal is transmitted to the PLC at the same time.The PC will also obtain the data and display it synchronously through KingView.
Automatic dosage system for the material enough to provide three different raw materials, injection process is divided into low, medium and high three being position, the actual application can be changed at any time according to the requirements of different processes the number of liquid level sensors and high and low position. Stirrer is responsible for the mixing of three kinds of liquids, the discharge cabinet will unload the mixed materials to the finished product reaction tank and then close the group. When the liquid level in the material tank is over low, set a delay time of 30 seconds in order to empty the material, in the case of discharging room is closed to start Ia material pump to provide the material medium with the first kind of body, the body reaches the low level, stop 1 # material poly, open 2 # material pump. Fill the second liquid for the material science tank. When the liquid level reaches the middle liquid level, stop the material pump, open another material pump to refill the third liquid in turn.
When the liquid level reaches high, stop the material pump and start the mixer motor. The mixer stirs in the forward direction for a set period of time and then stirs in the reverse direction. This cycle stops after N times. Open the material room, through the weighing module information to know the liquid level information, when the liquid and down to the lowest level and then delayed for 30 seconds, in order to empty all the material tank and wait for the next cycle.
When the system is interrupted due to power failure, the material tank will be emptied manually when the power is abnormally supplied. By other reasons caused by the system in the new, the system should have a record billion function, material mixing system using manual and automatic control, manual control is mainly used for emergency treatment and process debugging, configuration interface does not involve this content: automatic control of the core unit for the PLC. with the group interface and other actuators.
Fault states include material pump motor and agitator motor overload and various emergency stops, at this time the status indicator will be flashing at a frequency of 1 Hz, while the alarm sound signal. The alarm will not stop until the fault is completely cleared.
Configuration screen settings: initial screen displayed at power-on, equipment status screen, user operation panel, alarm screen, curve graph for displaying real-time changes in mixing motor and liquid level. Establish the material mixing display window, create database variables and complete the attribute definition. Through attribute definition, space, strategy and other segments, complete the design of the dynamic screen, set the storage attributes of data variables, and establish data query and curve browsing. Establish the communication connection of external equipment and parameter setting to realize the function of transportation monitoring and data management.
The whole control system is mainly the design of PLC control program and upstream and downstream computer communication (fine state king software and S7200 communication).
PLC program contains three parts: the main program part, mainly responsible for the selection of hand total/automatic processing process, the judgment of entering the liquid level processing subroutine, the display of the alarm lamp under the fault state and control system cycle; there are two subroutines, respectively, the liquid level processing and automatic operation. The liquid level processing subroutine is mainly responsible for judging the height of the liquid level in the material tank by comparing the collected liquid level information with the set value, and the liquid level signal will determine the opening and closing status of the material pump. When the collected input value exceeds the maximum allowable value of the set flow level, the system will automatically limit it to a reasonable range to avoid abnormal situations. The working process of the automatic operation subroutine is the main part, in the absence of other abnormal situations and the selection of the manual state, the mixing system will always be in accordance with the requirements of the system process flow back and forth cycle, the values of its parts will be synchronized to display in the group of the Zhi interface, so as to allow the control personnel to refer to and monitor. In the process of setting up the upper and lower computer connection, first of all, we need to establish the communication connection in the software of Configuration King, and the PLC model used in the dosage system is Siemens 57200-224CN, and the address is selected according to the actual situation of Shunshun. In the configuration parameter setting, create variable V, set the relevant data type, address, read/write type, through this variable and the PLC in the storage of the collected data in the VW unit to establish a connection. For example, the current signal collected from the liquid level sensor is stored in the VW100 unit of PLC, and the established V variable is inline with V100, so that the contents of VW100 can be accessed at any time when the relevant data are displayed in the interface of Configuration King. To synchronize the acquisition and display.