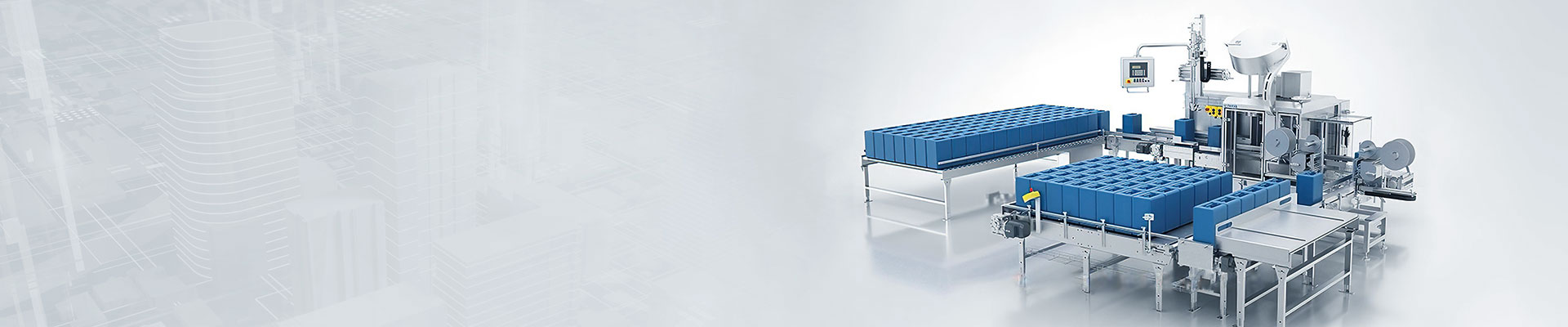
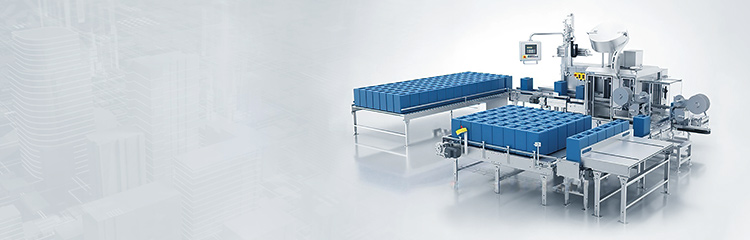
The mixing dosing system outputs a certain number of square wave pulses through PLC programming to control the Angle of the stepper machine and then control the dosing feed of the servo mechanism. The loop pulse distributor distributes the control pulses output by the programmable controller to the corresponding winding according to the power sequence of the stepper motor. The pulse distribution of the stepper motor controlled by PLC can be realized by software such as batching, capping, sealing, palletizing, weighing equipment and corresponding conveying.

The feeding system adopts a touch screen display, which monitors four aspects, namely, the process of discharging from the storage bin, the batching process, the discharging process and the batching process. Operators in the main control room can monitor the whole process of this technology from all directions, without going to the scene can also fully understand the site production conditions, to avoid the control technology can not control all the abnormal faults. Automatic batching technology application of the development of the benefit prospects of the technology after the field operation to prove that the technology hardware is reasonable, software design is perfect, full-featured, to ensure the stable operation of the production process, improve the quality of the product and yield, reduce energy consumption, improve labor conditions.
Dosing control system is used for continuous conveying, dynamic measuring and weighing dosing equipment for powdery and bulk materials. According to the requirements of production process, weighing and flow control of materials are carried out through the upper monitoring system and PLC, so as to realize accurate measurement and batching. As a dynamic continuous measurement, batching of the whole automation control device, but also for a variety of industrial production control, management of the site to provide accurate measurement data and control means.
Batching is the process of mixing various materials of different strengths and properties in a certain proportion, and the whole production process is realized by automatic control. Raw materials are stored in the storage silo, the use of electric vibration Feeder to control the amount of material, the material is respectively under the three batching silo, PLC through the analog input template, real-time sampling and monitoring control of the batching silo under the material. Below the dosage bin, the frequency conversion control dosage, bin configuration of raw materials automatically transported to the reactor waiting pot. The raw materials are stirred in the reactor, and the PLC controls the time and automatically discharges the materials.
The automatic dosage algorithm is designed by VB language and the data is transferred to FIX software through the upper computer. The production operator inputs the type of production products, the technical parameters of various ingredients and the total weight of the accompanying materials on the computer, and the computer can automatically calculate the proportioning weight of various materials and automatically download it to the PLC as the basis of weighing control. The operator can also manually input and/or adjust the proportion of various materials on the computer. The modification of the dosage and the total weight is valid only after the end of the dosage process, and the modifications made during the dosage process cannot affect the dosage ratio.
The PLC automatically controls the discharging quantity of the electric vibration feeder according to the ratio value output from the upper computer. For the dosing hopper, the order of various materials should follow the process of discharging in accordance with the proportion from large to small. The overshoot of the automatic dosage process is automatically and dynamically adjusted according to the difference between the given value and the actual value, which ensures the accuracy of the dosage to the maximum extent. Vibration feeding weighing technology adopts two-step vibration material, both fast vibration material 90%, slow vibration material 10%. Using microcomputer control of the whole vibration material dosage process, according to the last vibration of the final value of the material and the set value of the difference between the vibration material value compensation. According to the characteristics of this technology for a certain material repeated support amount, can use the past weighing error data to the future space material amount of the estimated compensation, keep the error in the smallest range of fluctuation.