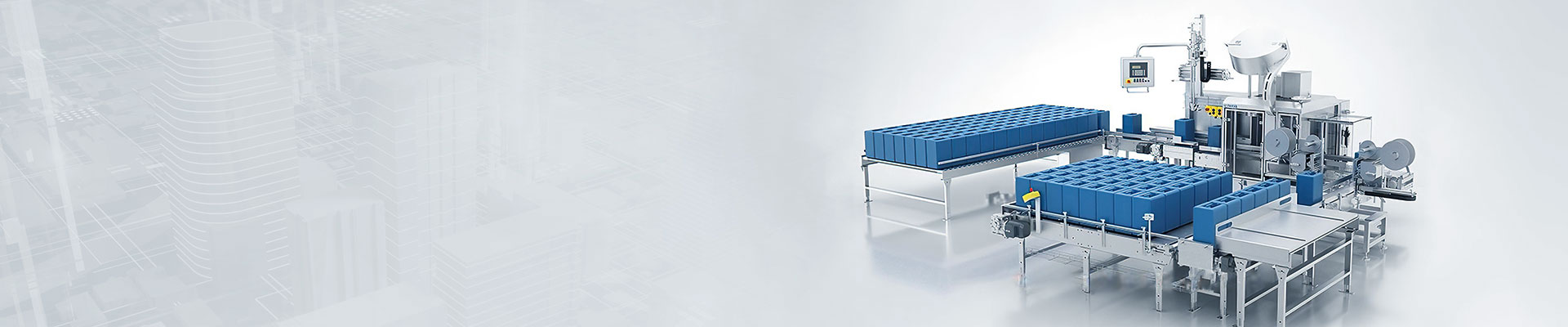
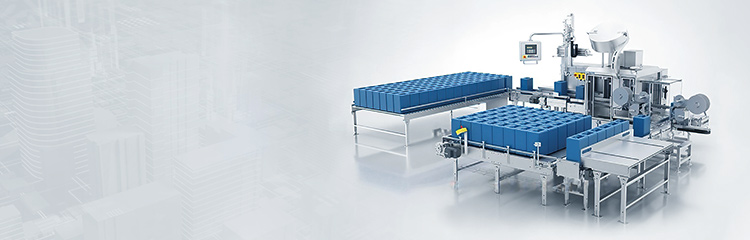
Liquid filling machine using open bus, field information acquisition, weighing system communication adopted automated filling system, project management, processing, archiving and establishment of documents. With humanized man-machine interface, provide convenience and also have a variety of protection functions, the user can set personalized working parameters according to the actual needs of the user can be set directly into the working state. Simple and convenient operation, no need to wait for restart and other complex operations.

The automatic Filling machine is mainly composed of bottle feeding conveyor mechanism, bottle washing machine, filling machinery, capping machine, star wheel conveyor mechanism, etc. The process flow is bottle feeding - washing - filling - capping - bottle discharging. The mechanical device is used to rotate the container at high speed - stopping sharply, and then the reflector is matched with the camera to take continuous serial filling images without perspective deviation. The filling device accelerates the container that enters the rotating area and stops accelerating when the container is about to leave the rotating area, leaving the container free to rotate (reducing air bubbles caused by oscillation). When the container "completely into the emergency stop area, the light inspection machine will control the mechanical device to make the container emergency stop, the liquid in the bottle due to inertia will continue to rotate, at this time the camera through the reflector began to shoot the container's continuous sequence of the reflector rotates accordingly at a certain angle, to ensure that the camera can track to capture the sequence of images of the container. Containers continue to transmit forward, the reflector also continues to make the corresponding rotation, until the container completely into the emergency stop area, at this time the reflector immediately return to the filling machine shown position, start tracking the next container. At the same time, it also completes the acquisition of a continuous sequence of images of the container.
WinCC-flexible, the latest product of Auto Filler, is an HMI-oriented configuration liquid interface with better openness, scalability and compatibility, which improves the configuration efficiency of the user interface and brings new creative concepts of device-level automation. In SIMATIC products can be used to configure all WindowsCE-based operator panels, from the smallest panels to touch control panels, multifunction panels. Due to all these advantages, the configuration of touch panels is designed in conjunction with the control core of the PLC, the CPU313C from the SIMATICS 7-300 series. Designed to realize industrial automation. Since it has some good functions, including manual operation, fault alarm, recipe management, trend graph (display and analysis) and print results.
Technical Parameters
Weighing range: 10~300kg
Filling precision: ±0.1~0.2%
Filling speed: 3~5 buckets/min (200kg)
Power supply power: P ≥ 0.6MPaQ ≥ 0.4m3 / min
Equipment weight: 350kg
External dimensions: 1000mmL×930mmW×1350mmH