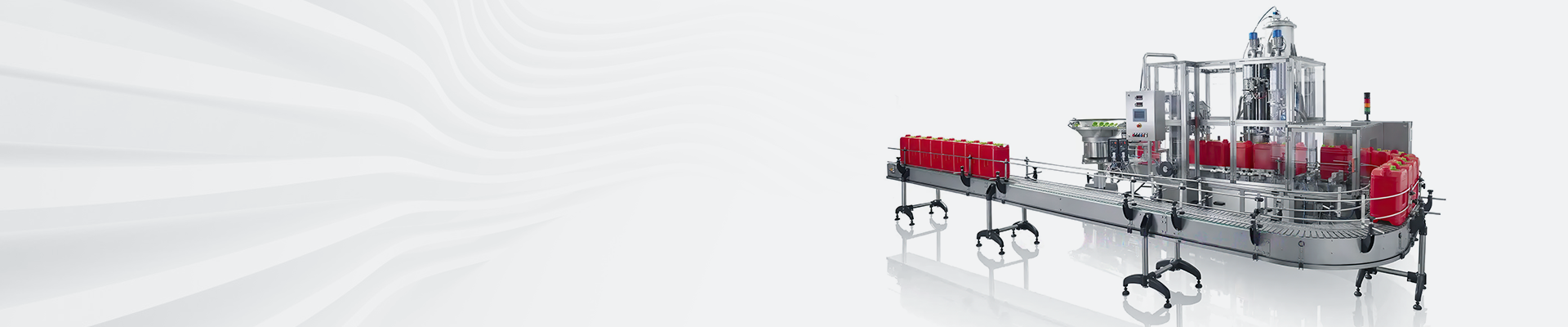
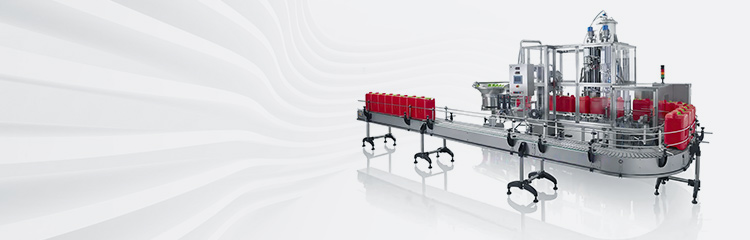

Summary:The working principle of the 12-channel suppository filling machine was analyzed, the mechanical structure of the filling machine was designed, a filling machine prototype was developed, and a continuous filling experiment of 10,000 suppositories was conducted.The experimental results show that there is no dripping or hanging on the wall during the filling process, and 100 pills are randomly selected and weighed. The error between each pill and the set filling weight is within +1%, and all performances can be achieved. Design requirements.
1 Introduction
12-channel suppository metering and filling machine is used for suppository filling process of fully automatic special equipment, due to its high production efficiency, occupies an area of less, good product quality, not hanging wall, no dripping, etc., in the major foreign suppository manufacturers have been widely used, but due to the cost of expensive, the use of this advanced equipment in the country is subject to greater restrictions.
2 suppository filling machine working principle
Suppository filling machine is an important station of the filling system, will have been dispensed with the liquid medicine added to the thermostatic barrel, stirring through the drug pipeline into the perfusion body, according to the needs of the device and the program control is automatically poured into the suppository bag bubble type, and then into the cooling machine to cool themselves to complete the perfusion.
3 filling mechanical system components design
3.1 structure composition
This set of equipment includes the following parts: filling body, electrical control system, electric heating system, hot and cold liquid circulation system. The mechanical system consists of a frame, filling head, metering mechanism, main coupling, holding mechanism and so on.
3.2 Design of filling head mechanism
Filling head is the main part of the whole filling machine, which is composed of 12 insertion rods, 12 filling rods and filling body respectively. It is connected to the main coupling through the positioning pin at the back of the filling body, and then through the cooperation of cylinder and servo motor to complete a series of actions such as pumping, inserting people, filling, returning to the position, and so on, to complete the filling of the station.
3.3 Measuring mechanism design
Measuring mechanism is to determine the filling amount of components, is composed of coupling by the coupling of the silk rod and servo motor. Through the number of turns of the screw to control the filling volume of the liquid. The material of the silk rod and silk mother are 40Cr and ZCuSn10P1 respectively, which can reduce the wear and tear and improve the service life. The screw is M20x1 fine thread, fine turning and the mother with grinding, so as to ensure that the gap between the screw and the mother with M20x1 fine thread can more accurately control the filling volume of the liquid.
3.4 Main coupling structure design
The main coupling consists of the main body and the left and right support combinations, through the main body and the support to make the filling head and metering mechanism combined into one. The main body of the main coupling is connected to the carrier of the filling head, there are 3 electric heating tubes on the main body, used to maintain the temperature of the liquid in the cavity of the filling head (generally maintained between 40 ℃ ~ 50 ℃). It can ensure that the drug solution does not solidify and does not change its nature in the case of stopping the machine. Left and right support is the metering mechanism connected to the filling head to form a whole.
3.5 Holding belt mechanism design
Holding belt mechanism includes two cooling plates, two holding belt plate, bracket, connecting shaft and two cylinders combined. Holding belt mechanism through the two cylinders to drive the connecting shaft in the self-lubricating bearings to complete the holding and loosening of the two actions. In need of filling, the suppository shell belt through the bracket transfer to the holding belt plate, holding belt plate holding tight suppository shell belt, so that the suppository shell belt can be fixed, so that the insertion rod can be stable and accurate inserted into the suppository shell belt filling liquid, filling is completed after the release of the shell belt to make it into the next workstation. There are liquid inlet and outlet on the cooling plate, the cold liquid enters from the liquid inlet, and flows out from the liquid outlet through the channel in the cooling plate to achieve the cooling effect.
3.6 Mechanical system assembly
The whole equipment has 12 identical stations, and all movements have only a unique movement trajectory and starting and stopping position, which requires that the accuracy achieved by the 12 stations must be high. Through the analysis, we found that the following key processing and assembly quality determines the accuracy of the 12 stations.
(1) The 12 channels of the perfusion body should be completed on the CNC boring machine to complete the processing of 12 channels, which can ensure the consistent spacing between each hole (17.4mm) and the accuracy requirements of each hole.
(2) The 12 insertion bars and perfusion bars are required to have the same size so that interchangeability between them can be achieved.
(3)The sealing ring on the 12 insertion rods and filling rods is very main, it has high requirements on the choice of material and precision, because the temperature of the medicine in the suppository canister is completed at 40℃~50℃, so that the choice of the rubber ring is a temperature-resistant material to guarantee its service life. Its machining precision should be tight with each channel to improve the filling precision and eliminate the phenomenon of medicine dripping.
4 System Design
Automatic filling machine using a special industrial process controller, through the RS485 bus and the central control room to achieve communication, both independent control, but also to achieve PLC online control. It can realize real-time process data monitoring, simulation display process flow, real-time data record access, operator privilege setting, process parameter setting, setting running process event alarm and manual and automatic control switching. The computer downloads the program and monitors the operation of the equipment through the Ethernet PLC on-line. The touch screen communicates with the PLC through Modbus 485 communication protocol, displaying the operating status of the equipment and setting the operating parameters for starting and stopping the equipment. The actuator is responsible for the execution of PLC commands, the specific implementation of the corresponding action.
Liquid filling machine complete system adopts explosion-proof standard manufacturing, fast and slow two-stage or fast, or slow, slower three-stage filling mode, the target amount of free setting. Selection of high-precision, reasonable range weighing module and filling actuators, start/stop control of discharging, through the weighing instrument TR700 into the PLC, through the PLC and TR700 cooperation, the servo controller to control the stepping motor to run precisely to the designated station and accurate unloading, filling production line in the program set up interlocks, to ensure that the moving/unloading mechanism when filling the operation of an orderly and reliable. For the convenience of actual operation and maintenance, under the manual operation mode, the personnel can operate each mechanism on the site through the lighted operation buttons on the stainless steel analog screen on the surface of the controller cabinet, and observe the equipment operation intuitively. PLC communication is used to collect and process weight data, as well as to send tare signals to make the meter tare. In the quantitative filling mode, PLC as the main controller receives data from the weighing instrument, processes the data and sends a series of signals to control the filling action to complete the quantitative filling. After the filling is completed, the professional manipulator will accurately take out each barrel each time and accurately transport the barrels to the specified position through the power rail, and carry out real-time picking measurement and control on the full barrel in place, stacking blockage, lowering the lid, opening/closing the filling valve, etc. Use PLC signal to drive the motor and other transmission mechanism to drive the manipulator to move, and at the same time drive the motor comes with the encoder feedback bit (pulse) to the drive driver to compare the two kinds of pulses and determine the deviation, according to a certain control law after arithmetic operation of the calibration signal as a servo drive in the speed controller is given and then by the current regulation and power amplification, so that the gripping manipulator towards the elimination of the deviation of the direction of the movement, thereby Realize the stacking and positioning of the manipulator.
The metering signals of the weighing and filling machine are converted into PLC through the metering display controller and weighing modularization respectively, and the output of the filling machine is a parallel BCD code which is converted into binary code through the program and stored in the data register of PLC. The output voltage signal of the weighing module is converted through the A/D conversion of the explosion-proof electronic scales, accumulated and transmitted to the weigher through the junction box, which displays in real time the weight of the material in the current weighing (reactor weighing). The liquid filling machine passes the displayed weight data from the electronic scale via serial communication to the PLC, which compares the collected weight of the weighing module with the weight set in the touch screen (or computer) of the electronic scale, in order to control the behavior of the entire reactor weighing module. After configuring the computerized dosage system, it dynamically displays the working status, prints the measurement data in real time, saves the historical data records, and allows the user to monitor the working status of the reactor tank and find the historical data.
5 Conclusion
The designed 12-grain suppository filling machine is reasonable in structure, high in precision and low in cost, and can be popularized and used. After continuous completion of 10,000 suppositories filling experiments show that the filling process does not appear dripping and hanging wall phenomenon, and in which 100 randomly selected for weighing, each grain and the set filling weight error are within +1%, the performance of all can meet the design requirements.