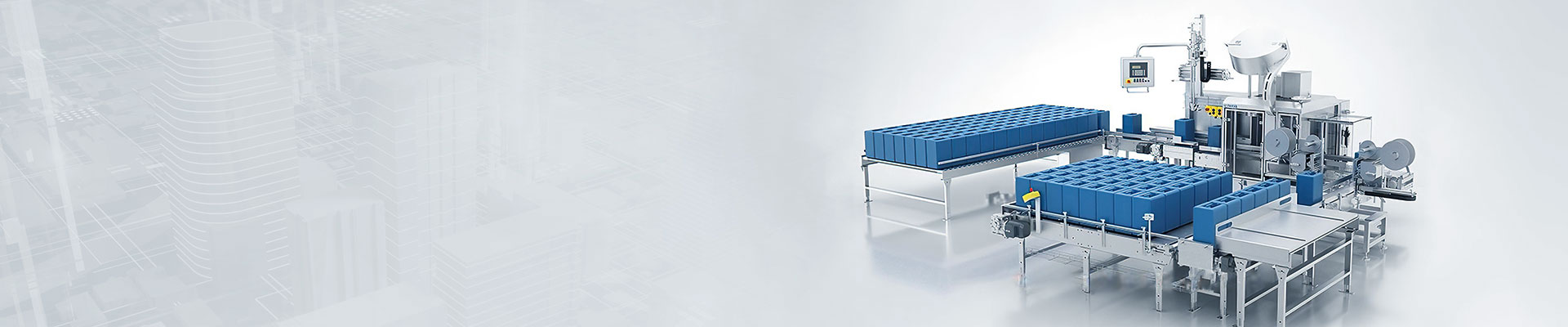
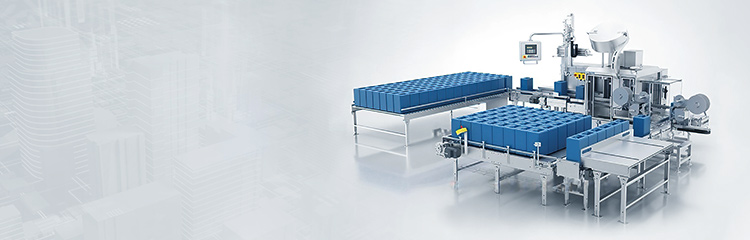
Liquid filling machine adopts the distribution switch quantity input, analog quantity input signal real-time acquisition of filling quality, switching quantity output control pump and solenoid valve action, PLC system has two ways of working, using the main program call subroutine structure, reduce scanning time, measured value conversion, stop and emergency stop external management.

Liquid Filling machine is mainly composed of seven parts, such as bucket separator, buffer roller, bucket selector flow controller, weighing filling machine, capping machine and electrical control system. The electrical part is composed of PLC, weighing instrument, man-machine operation interface, frequency converter and so on. According to the user's personalized Settings, the process of bucket feeding, bucket separation, bucket positioning, weighing filling bucket conveying and capping can be fully automatic control, which can achieve fast and high-precision multi-station filling.
The automatic filling machine adopts high precision weighing instrument to synchronously control the filling process of multiple stations. The weighing instrument can easily set the parameters of target filling weight value, large drop lead, drop lead, tare weight comparison and so on. The dynamic response speed is fast, the influence of environmental vibration can be automatically removed, and the requirements of filling accuracy can be fully guaranteed.
Weighing machine with humanized man-machine interface, man-machine interface design to human operation habits as the design starting point, all modes have humanized operation interface, to provide convenience but also with a variety of protection functions, users can set personalized work parameters according to actual needs, after setting can be directly into the working state. The operation is simple and convenient, and there is no need to wait for complicated operations such as restart.
The whole filling production line has a comprehensive dynamic self-test function, which can automatically detect the congestion, overload and other anomalies in any position on the line. Abnormity can be automatically suspended, abnormity can be quickly resumed after elimination, simple operation, fast recovery speed, safe and reliable.
Basic parameters:
Maximum weight: 30kg
Minimum sensitivity: 10g
Filling error: ±10-20g(depending on filling speed)
Filling speed: 100-150 barrels/hour (depending on feed flow rate)
Applicable container: ≤ 350xh500mm small mouth bucket, open bucket
Explosion-proof class: EXdiaIIBT4
Power supply: AC220/50Hz
Air source: 0.4-0.8Mpa
Operating temperature: -10℃-40℃
Control mode: 2 speed pneumatic control
Filling method: Insert type, liquid surface
Scale size: 400×400mm
Temporary table: 400×1000mm
Structure material: SUS304 stainless steel.
Head pipe: SUS304 stainless steel and tetrafluoride (optional 316L)
Material interface: DN40 quick installation pagoda connector, optional flange connector.
Air source interface: 8mm gas pipe access