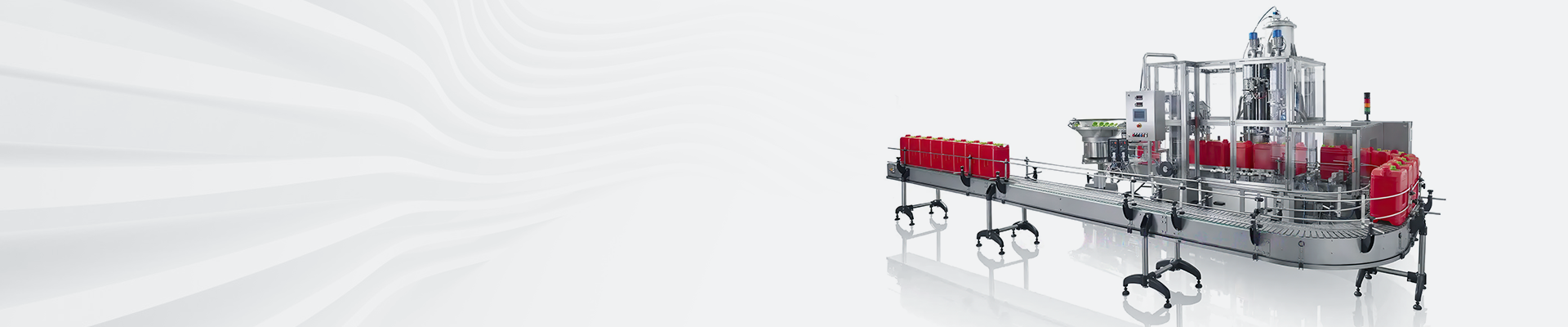
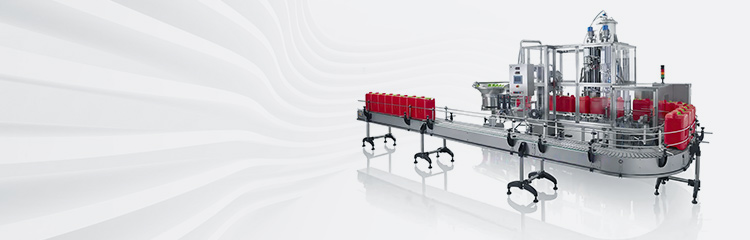

Summary:The communication function between the liquid filling machine and the electromechanical product enables the transmission motor and the drawing motor to start/stop and adjust the speed directly on the touch screen, and realizes the speed following between the servo and the main motor.
The communication function between the filling machine and electromechanical products realizes the direct start/stop and speed regulation of the drive motor and the pulling motor on the touch screen, and the speed following between the servo and the main motor. It makes the operation of the operator intuitive and convenient. Utilizing the servo's PR mode (internal multi-segment position mode), the customer's mechanical flower-pulling becomes electrical control, and the distance and speed of flower-pulling can be adjusted by the end user on the touch screen. The distance and speed of pulling can be adjusted by the end user on the touch screen, which makes the adjustment of the customer's pulling pattern convenient and flexible. Greatly improve the production efficiency.
Filling system is usually composed of 4 parts:
(1) the main drive part: the main drive adopts intermittent speed reducer output drive sprocket drive, drive the bottle plate to carry out by workplace material bottle, the main drive motor 2.2KW, using frequency converter speed control, speed reducer ratio of 30:1, the main motor to turn 30 laps speed reducer output 1 lap, the bottle plate to move a workplace, after which the speed reducer there will be an empty stroke of about 1.5 seconds, left for the workplace for the Various process actions. The frequency converter used in the main drive with 485 using the standard MODBUS protocol and PLC communication, changing the original way of switching control, this control can be directly in the touch screen to start and stop control and speed control, a variety of state monitoring and so on. Saved through the analog or external potentiometer control of the tedious, external wiring as long as two shielded wires on the line, internal programming because all electrical products, only a read a write two instructions on the line. Simple and stable.
(2) filling part: filling part by a dozen linear arrangement of filling stations, the implementation of different by the corresponding valve control, PLC to accept the main drive encoder transmitted over the angle signal (360 lines, corresponding to a bottle cycle), ES series PLC is the control center of the entire machine, according to the set value of the angle of the control valve open and close.
(3) There are flat cups and egg cartridges for liquids, the pulling refers to the egg cartridge part, and the flat cups do not need to be pulled. Liquid flower part of the main function is to fill the liquid poured on the style of good-looking cream, flower control is mainly controlled by two parts, one is the non-stop rotation of the flower pulling motor to drive the head of the rotating flower pouring cream, the other is to drive the head of the flower to do the lifting movement of the part of the majority of domestic manufacturers are the use of mechanical cam structure, when the flower needs to be altered, only to replace the different shapes of the mechanical cams, which will greatly affect the production efficiency of the machine. This will greatly affect the productivity of the machine. Flower pulling is a very important part of the liquid production. The shape of the flower pulling head, the speed of the flower pulling rotating motor, the accuracy and speed of the flower pulling lifting position, these three major elements directly affect the beauty of the flower pattern. In fact, the lifting part of the main control parameters are two: the speed of each section and each section of the flower pulling distance. That is, the unit distance and unit speed adjustable, so the flower pulling rotary motor is also used inverter control and the use of A series of servo to complete the work, in the touch screen to do the speed of 8 sections corresponding to the speed and distance setting screen, the use of A series of servo PR mode, through the PLC to the servo of the three switching combinations to start each section distance, speed through the communication mode to give. Users in the adjustment of the parameters of each type of flower, can be saved through the screen's recipe function, the next time you use just call out.
(4) Temperature control part: the filling machine has three places to be temperature control: batching, mixing, heating. All use high-power heating tube, K degrees thermocouple temperature detection. Temperature upper limit of 300 degrees. If the PLC is used to control the temperature, it must be added to the temperature detection or control module. These modules are usually expensive and need to be programmed in the host computer. From an economic point of view and from the point of view of interchangeability, a thermostat is used.
Filling system design
Automatic filling machine is the main weighing itself constitutes the weighing closed-loop filling, when the setting is determined, through the closed-loop regulation to eliminate the impact of disturbances, so that the weighing is stabilized at the set value, the main weighing closed-loop automatic filling machine belongs to the constant value of automatic filling. The input quantity of the second closed-loop automatic filling machine is the product of the weighing signal and the ratio coefficient after detection and transmission. The filling machine consists of a sub controller, pump frequency converter, sulfuric acid pump and detection point transmitter, etc. The filling machine is designed for the hardware and software aspects of the paint canning production line control. The hardware design part includes the design and installation of the external circuit of FX2N-32MRPLC; the software part includes the design and debugging of the program. According to the realization requirements of the PLC, motor, weighing module, relays and other external equipment to select the model. The completed design of the paint filling production line can realize the following functions:
(1) Set = to automatic operation mode by switch, once started, the drive motor of the conveyor belt starts and continues until the stop switch is actuated or stops running when the paint pail is transferred under the filling machine; after the pail is filled with paint and capped, the drive motor of the conveyor belt must be automatically started and maintained until the next paint pail is transferred under the liquid filling machine or the stop switch is actuated;
(2) When the barrel is transferred and positioned under the liquid filling machine, stop 1s, the liquid filling machine starts to work, for large barrels filling 8 seconds, small barrels are 5 seconds, the filling process is completed after the paint barrels on the cover operation, the cover time is about 2 seconds. The entire filling and capping process should be equipped with an alarm display, to be capped after the completion of the alarm is no longer displayed; alarm mode for the red light 0.5s interval flashing;
(3) Packaging process, for small barrels: 40 barrels for a large package, 30 barrels for a medium package, 20 barrels for a package; for large barrels: 20 barrels for a large package, 15 barrels for a medium package, 10 barrels for a package;
(4) can realize the production of products for automatic counting and can manually clear the counter to zero.
Filling control process analysis
(1) metering filling machine to ensure that the host and servo electrical zero and mechanical zero position consistent.
(2) Filling start and close through the encoder angle signal control, can be set on the touch screen.
(3) The servo follows the host to run, and the running position and speed are adjusted manually on the touch screen.
(4) Host speed can be adjusted on the touch screen.
(5) Production counting control function.
Hardware architecture design
Weighing and filling machine is composed of mitsubishi fx2nc series plc,, frequency converter, metering screw, electromagnetic automatic filling machine and so on.
(1) mitsubishi fx2nc series plc: fx2nc series plc has high performance to volume ratio and communication function, it can be installed into the space which is much smaller than the standard plc. i/o type connector can reduce the wiring cost and save the wiring time. the number of i/o points can be extended to 256 points, and up to 4 special function modules can be connected.
(2) Corrosion-resistant pump: sulfuric acid is a corrosive medium, the transfer pump must be corrosion-resistant pump. This quantitative filling machine adopts ihf6550-160 type fluorine plastic centrifugal pump, pump inlet diameter 65mm; outlet diameter 50mm; impeller nominal diameter 160mm; rotational speed of 2900r/nin, weighing 25m3/h; head 32m; motor power 5.5kw. Sulfuric acid pump adopts frequency conversion speed control. For pump equipment, should be selected for pumps special frequency converter. ihf6550-160 fluoroplastic centrifugal pump drive motor power of 5.5kw, choose Siemens mm430 pump special frequency converter, the frequency converter with built-in a filter.
(3) Siemens frequency converter: the flow speed of powder in the spiral is calculated indirectly by the motor encoder output pulse, if the motor speed stability is not good, it will affect the normal work of the metering spiral. For this reason, the German Siemens mm440 vector control inverter, power supply voltage 380vac, rated output power 5.5kw, rated output current 13.2a. In order to stabilize the rotational speed of the spiral shaft and calculate the flow rate of powder, weighing and filling machine with speed encoder vector control. The frequency converter needs to increase the pulse encoder pulse processing template (encoder template for short) and encoder.
(4) Measuring screw: potassium chloride is powder granular material (referred to as powder). Metering spiral is the powder for conveying, dynamic measurement and weighing control equipment. This design adopts the measurement spiral (spiral electronic weighing).
(5) electromagnetic automatic filling: widely used to measure the conductive liquid and liquid-solid two-phase fluid volume weighing, measurement results with the fluid temperature, viscosity, density, pressure and liquid-solid composition ratio has nothing to do with the conductivity in a wide range of changes will not affect the measurement results. Therefore, it can be used to measure the weighing of other conductive liquids or liquid-solid two-phase fluid mediums only after ordinary water calibration.
System debugging
1 Zero debugging
In the initial debugging, did not do the host zero, the results of debugging found that the machine running time is a little long, the encoder's angle and the mechanical position corresponds to the cumulative deviation. For this reason, in the program to add a section of the zero, boot first zero, through the encoder signal (interrupt acquisition) to clear the zero, because the zero and mechanical position is always corresponding, so no matter how much the value deviation, every turn of the zero can be corrected over. The servo also has the same problem of position offset, so the zero point of the servo is set at the highest point of the mechanical position. This zero point is found when the machine is turned on. The mechanical position corresponding to the zero point of the servo and the host is changing, so the servo immediately reverses after finding the zero point to find the starting position corresponding to the zero point position of the host, which is set by the customer on the screen, and the host is prohibited from running during this period.
2 Host speed limit
The host and the frequency converter are connected by communication, because the servo follows the host to run, the speed has a multiplier relationship, so the host in order to meet the customer's production speed under the premise of the speed limit processing.
Conclusion
The project has passed the debugging, the function of the filling system fully meets the requirements. The project fully demonstrates the technical ability of electrical products in the packaging industry mechatronics applications.