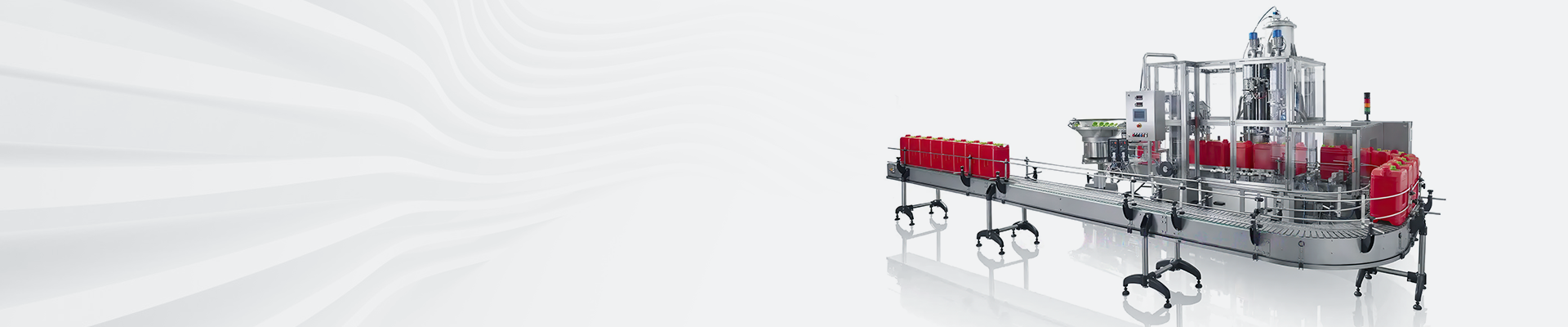
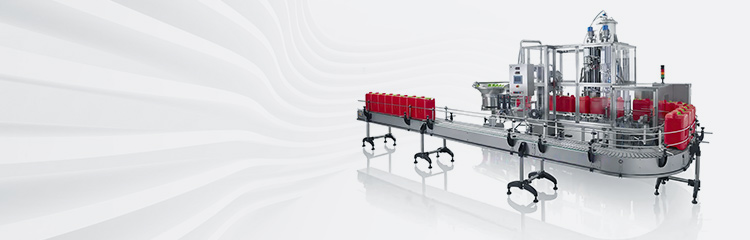

Summary:The manual spray paint automatic liquid filling machine can realize a series of production process actions such as automatic tube feeding, filling, tube sealing, tail cutting, and chip blowing. The production efficiency is high, up to 100 pieces/minute.
Filling technology program configuration
The main electrical components of the explosion-proof filling machine, in addition to the low-up electrical appliances (low-up circuit breakers, AC contactors, intermediate relays, master buttons, indicator lights, etc.), position sensors (photoelectric sensors, color-coded recognition sensors, travel switches, etc.), are not described here.
Filling technology program
The weighing and filling machine adopts DOP-A series 10.4-inch human-machine interface as the upper computer, which can set and display the liquid explosion-proof filling machine running action and process parameters, and the main controller adopts Slim series PLC, and 12SC11TP PLC has the functions of high-speed pulse input and high-speed pulse output, which can collect the spindle rotary encoder AB-phase pulse signals, and then be converted into the spindle rotational speed value, pulse signal value and its value of color-coded identification sensor. Through PLC program processing, it can be converted into spindle rotational speed value, pulse signal value and other time domain change reference value which is the key of process action.
The two-axis high-speed pulse output drives two sets of servo systems simultaneously to realize the rapid rotation of the tube to be filled, and the servo drive stops immediately after the color-coded sensor detects the mark at the end of the tube, thus realizing the photoelectric positioning action. By adjusting the operating frequency of the spindle rotary frequency converter, the rotational speed of the main camshaft can be changed, thus changing the efficiency of the filling product processing.
The following is a description of the various process actions of the filling machine according to the human-machine interface screen program.
First of all, we should set up the host time domain parameters, these parameters determine the timing of the relevant process action as well as the start and stop, the so-called host time domain parameters, is based on the main camshaft shaft encoder rotating one week of the number of pulses generated by the PLC adopts two times the frequency of the AB-phase counting, the encoder 1000 lines, so the main camshaft rotating one week of the number of pulses 2000, when the system detects the zero switch signal, the counting value of the value is cleared to zero, and re-measure the next week of the number of pulses to Measure the number of pulses for the next week, and so on. In the weekly digital range of 0 to 2000, divided into a number of small zones, defined as the host time domain parameters, the PLC program according to different time domain range, in order to perform different process actions.
After the debugging is completed, the user enters the operation screen, starts the spindle rotation of the explosion-proof automatic filling machine, and automatically carries out the processing actions such as feeding the tube, filling, sealing the tail, cutting the tail, blowing the chips and so on, so as to realize the process of hand spraying paint filling and encapsulation.
First of all, set the frequency converter operation frequency, press the start button, the spindle material cup wheel disc began to select, according to the set time domain parameters, in turn, a number of workplace action, first into the tube action, empty tube loaded into the material cup (mold), the next step in the inspection of the tube, that is, to detect whether the material cup is loaded into the empty tube, the next step in photoelectricity positioning, to confirm the direction of the empty tube, to ensure that the end of the tail sealing, the tube body of the symmetry of the text on the front and back, after the completion of positioning Enter the filling station, after filling, enter the sealing station, install the front cursor to detect the positioning position, carry out high thermoplastic sealing, and then cut at the end of the tube, and finally blowing chips station, clean up and then manually boxed.
The production management screen can display the production information of three production shifts in a working day, respectively, the statistical display of shift production, daily production, and production in the last three days, effectively providing a production manager to control the production progress and production.