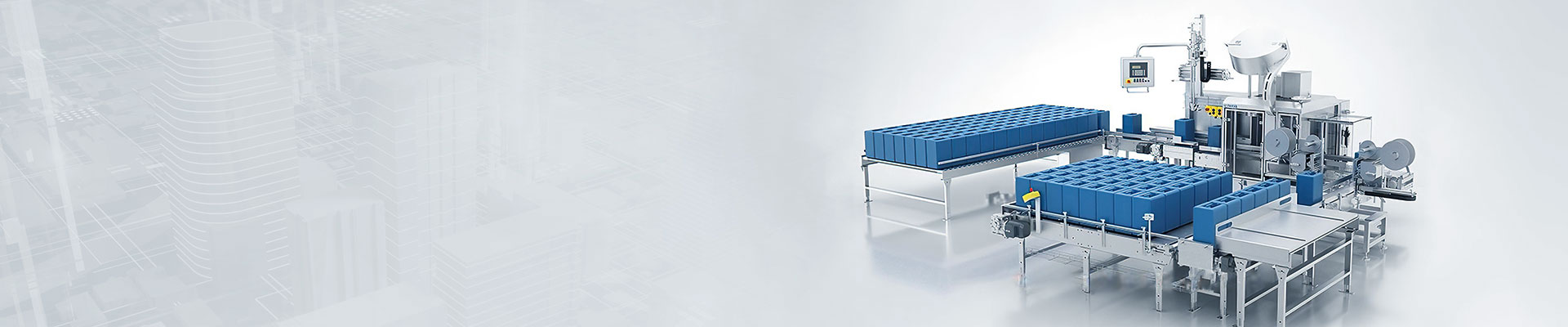
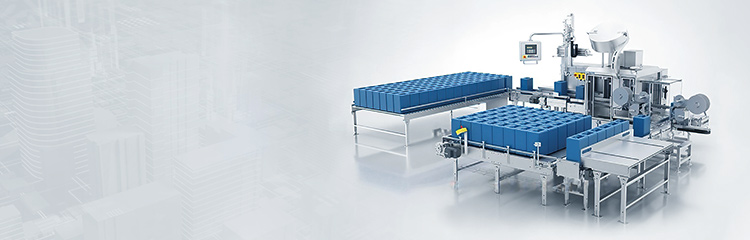
Solution filling machine is a special equipment to realize automatic metering and filling of liquid products, which is mainly composed of automatic transmission system, weighing system, machine vision addressing system, automatic charging port addressing system, non-drip automatic charging system, filling data query and management system, and only need to place the container in the input end of the transmission system. The rest of the operating procedures (except opening and closing the cover) are automated.

The automatic Filling machine is divided into suction and filling module, liquid level tracking module, automatic control module and detection module according to the design and assembly principles, while the suction and filling module contains 4 modules, namely, metering module, suction and filling drive module, flow distribution module and nozzle module.
In the liquid absorption module, the metering module adopts piston metering pump, the drive module adopts servo motor driven ball screw, the flow distribution module adopts cone valve check valve; the liquid level tracking module is realized by the stepping motor driven ball screw; the automatic control module adopts the widely-used PLC as the control center; and the detection module adopts the method of automatic weighing. In order to improve the operability, the human-machine interactive interface, which can easily select and call the filling parameters and intuitively obtain the filling results.
Filling equipment for each barrel filling, servo motor rotation generates driving force, in the ball screw drive, drive the piston rod up and down movement, screw and piston rod connected through the slider in order to ensure the smoothness of the movement of the slider, in the left side of the installation of the slider linear guide; 2 in the service motor drive, the piston rod up and down reciprocating movement of the piston metering pump, metering pump for the cylindrical structure, the distance of the piston rod movement Corresponding to the volume of the metering pump suction and filling; selection of check valves as a flow distribution mechanism, in the suction, the inlet check valve open, the outlet check valve closed; in the filling, the outlet check valve open, the inlet check valve closed, so as to complete the suction and filling process; filling nozzle through the steel wire hose connected to the flow distribution structure, filling containers are placed in the tray, the level tracking module adopts stepper motors and ball screw, the stepper motor and the ball screw will be the stepper motor, and the filling container will be placed in the tray, and the level tracking module adopts the stepper motor, the ball screw will be the stepper motor, and the stepper motor will be the stepper motor. The ball screw converts the rotation of the stepping motor into the up and down movement of the pallet to ensure that the distance from the nozzle to the liquid surface of the container is constant, reducing splashing and foaming during the filling process. In the human-machine interface to change the filling volume, filling speed and other filling parameters PLC can be based on the input parameters to the servo motor, stepping motor to send the appropriate control signals to achieve different filling parameters.
Basic parameters:
Maximum weighing capacity: 300kg
Minimum Sensitivity: 0.1kg
Filling error: ±0.1-0.2kg
Filling speed: 200L about 50-80 barrels/hour
Control mode: 2-speed control
Filling method: Insertion, liquid level up
Gun head line: Teflon gun head, valve + Teflon hose
Structure material: Liquid filling machine host SUS304 stainless steel, conveying palletizing carbon steel anticorrosion paint.
Weighing platform size: 800 × 800mm (304 stainless steel power raceway)
Empty barrel raceway: 800mm × 2500mm (304 stainless steel power raceway) with another 1200mm slope without power roller
Heavy drum raceway: 800mm×2500mm (304 stainless steel power raceway, 2 sets)
Separate barrel device: for 200L barrels, carbon steel anticorrosive paint structure, 304 stainless steel raceway.
Palletizing equipment: pan-transfer type, suitable for pallets 1200×1200×140mm, including supplying pallets, palletizing, and lower pallet conveying.
Pipe pressure: 0.2-0.6MPa (related to material properties).
Material interface: DN40 flange connector 4, according to the user to provide interface standards
Air Connection: User supplied 12mm air hose connector for quick coupling connection
Power supply: AC220/50Hz (user-supplied to one side of the machine)
Using air source: 0.4-0.8Mpa (provided by the user to the side of the machine)
Use temperature: -10℃-50℃
Basic conditions: active agent flat solid concrete floor, concrete thickness should be more than 10cm. optional models: standard type, explosion-proof type filling