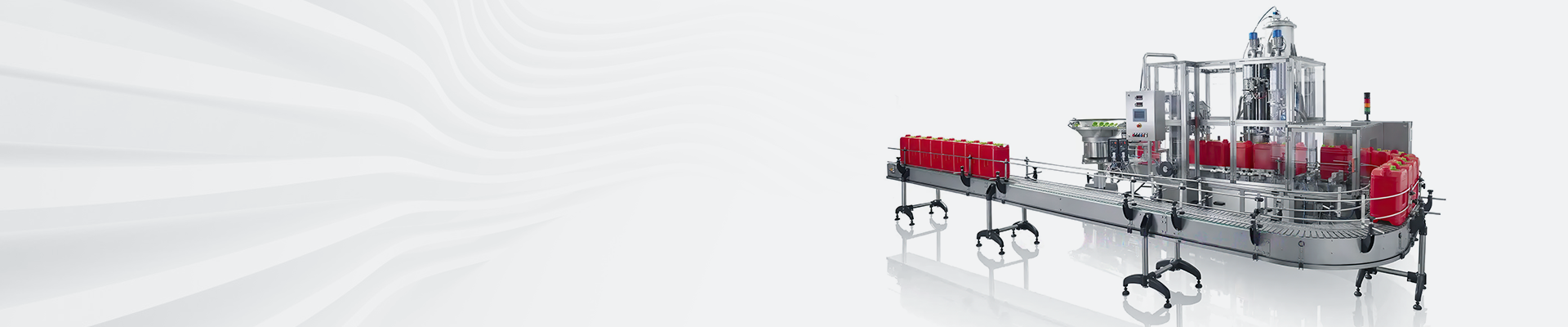
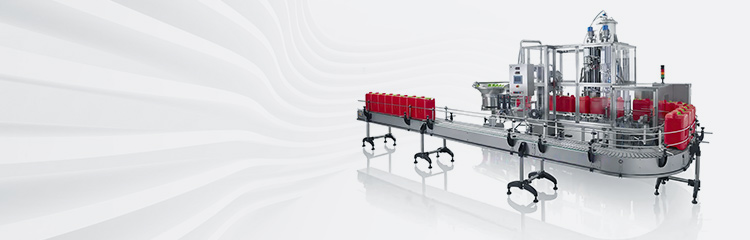

Summary:The liquid filling machine integrates servo control, weighing control, counter functions, etc.Using industrial microcomputer measurement and reading, the PLC controls the start and stop, material sending and receiving on site, and reads the status signal of the volume tube position detection switch to obtain the reading value of the weighing module in the standard section of the volume tube.
1 automatic filling machine to achieve the function
Explosion-proof filling machine according to the actual situation and design requirements, in addition to smooth operation and accurate measurement, but also need to realize the following functions:
1) real-time acquisition and display of on-site operating parameters (a total of 23 analog, 3 pulse, 3 switch inputs, 3 switch outputs); when certain key parameters occur over the limit, sound and light alarms are issued to prevent accidents;
2) Establish network between on-site weighing modules and remote dispatching room to realize remote real-time monitoring of on-site data;
3) Realization of real-time and historical trend records of parameters and alarm records, with the ability to query the data of any historical moment within a month;
4) Realize automatic printing and random printing of daily (once a day) and shift (once every 8 hours) reports of field parameters;
5) Automatically measure the mixed oil volume and pure oil volume of each day and each shift; automatically calculate the standard density of oil products after manually inputting the apparent density;
6) online calibration of 3 weighing modules in combination with standard volume tubes on site, and online correction of the reading error of the weighing modules.
2 Structure and working principle
2.1.1 Composition of weighing and filling machine
The whole set of weighing and filling machine consists of on-site one and two instruments, filling machinery, filling production line, control room a PLC, two IPC (each configured with a network card), a printer, two hubs and other components.
2.1.2 Hardware configuration
Filling production line consists of metering filling machine, capping machine, sealing machine, coding machine, the entire production line by the conveyor belt throughout, responsible for the delivery of containers. Filling machine is the main equipment of this production line, and its performance plays a decisive role in the function and efficiency of the whole production line. In order to improve the performance of the filling machine, designed by the DSP-based servo control metering, stepping control, programmable logic controller (PLC), human-machine interface, conveyor belt frequency control, pressurized pneumatic part and photoelectric sensors, such as the composition of the machine, gas, electricity integrated automatic control.
Programmable logic controller (PLC) S7-300 and DSP are used as its control body. In the hardware connection, PLC as the control of the automatic filling machine in the lower computer, and a variety of underlying equipment in direct contact. PLC filling system communicates with the upper computer, access to product information and production parameters, as well as based on a variety of sensors in the production line, the control of the filling head of the logic of the action, the control of the filling conveyor belt speed, drive stepper motors to control the filling head of the filling to realize the two-dimensional precise positioning and filling inlet flap of the precise positioning; DSP based on the PLC, the filler head is a two-dimensional precise positioning and filling inlet flap of the precise positioning. Precise positioning; DSP according to the PLC liquid filling device to give the filling volume, complete the servo drive and filling capacity compensation, drive the pressurized hydraulic cylinder action, to achieve the adjustment of the filling capacity, and at the same time through the compensation algorithm to calculate the compensation volume information, added to the adjustment of the filling capacity. In terms of the software of the programmable logic controller, according to the workflow of the production line, the production line control program is compiled using the ladder diagram form using its special programming software and written inside the programmable logic controller, realizing the overall control logic and production function of the production line; in terms of the software of the DSP, the capacity calculation and servo automatic filling device control program are compiled; the network control part includes A computer (upper computer) and lower computer (PLC), in which the computer as the upper level of the control of filling machinery, to achieve the control and management of the whole plant's multiple filling machinery, specifically for the management personnel, mainly for the change of filling containers as well as generating, printing and management of the production line of a variety of reports to show the operational status of the production line, once the fault, to the administrator to report in a timely manner, if necessary, the management personnel can be through the If necessary, the manager can stop and start the operation of the production line remotely through this server.
2.1.3 Control room part
1) Industrial microcomputer IPC: Advantech IPC610 type industrial microcomputer, which is widely used in China at present, is selected to ensure the high reliability of the filling machine. The entire automatic filling machine has two IPCs, one on-site duty room, the other in the remote dispatching room, two IPCs are equipped with a network card, the middle of the line connected to two D2Link hub to ensure the quality of data communication.
2) PLC: Select Schneider's MicroTSX3722 PLC as the control core of the metering and filling machine, which is characterized by small size, strong functionality, scalability, a variety of special function modules to meet the needs of different special occasions, with a high performance/price ratio. The following are its specific configurations.
a) Host: MicroTSX3722 (built-in power supply, CPU);
b) Analog input (AI) module: TSXAEZ802 is selected, which has 8 high-level analog inputs, can input standard signals such as 0-20, 4-20mA, 12-bit analog/digital conversion accuracy, with input overshoot monitoring and measurement filtering and anti-jamming function; for future expansion, this automatic filling machine uses 4 blocks of TSXAEZ802 to collect 23 analog quantities from the scene;
c) Switching input/output (DI/DO) module: TSXDMZ28DR is selected, which has single-ended isolated 16-channel 24VDC inputs and 12-channel relay outputs, and provides internal overload and short-circuit protection; 1 TSXDMZ28DR is used to collect 6 switching quantities (3 switching inputs and 3 switching outputs) of the field standardized volumetric tubes, so as to control the starting and stopping of volumetric tubes, and to calibrate the weighing module. The weighing module is calibrated;
d) High-speed counting (HSC) module: TSXCTZ2A is used, which has two counting channels and can count two pulses with a maximum frequency of 40kHz at the same time. This automatic filling machine utilizes two TSXCTZ2A modules to count the number of pulses from the pulse transmitters of three weighing modules, and calculates the crude oil flow rate (including instantaneous and cumulative amount) through the program;
e) Communication (CMM) module: TSXSCP114 module (supporting TSXCM4030 communication cable) combined with Advantech ADAM8520 232/485 converter is selected to realize bidirectional transmission and exchange of data between PLC filling device and IPC, and the communication protocol is MODBUS.
2.1.4 Field part
The field part is mainly for primary and secondary instruments, including pressure gauge, thermometer, integrated pressure transmitter, temperature transmitter, weighing module and standard volume tube for calibrating the weighing module. Among them, the primary instruments are all general-purpose instruments; according to the site conditions, the secondary instruments are selected as explosion-proof standard DDZ2Ⅲ type instruments, pressure transmitters and temperature transmitters are selected from Kaifeng Instrumentation Factory, the flow rate instruments are adopted from Japan OVAL company's UF2Ⅱ rotor weighing module, and the flow rate conversion and transmission part is the OVAL company's PG30EP type pulse transmitter.
2.1.5 Self-software configuration
Automatic filling machine application software mainly includes filling platform software, PLC software.
Programming software and IPC configuration software.
1) Filling system platform software: WINDOWSNT410 as a platform, set the password and operator instructions, shielding some of the functions of the software to limit the operation to prevent illegal users from entering;
2) PLC programming software: Schneider's TLXLPL7MP10E is a programming software suite based on the WINDOWS environment, support for ladder diagrams (LD), Instruction Statement List (IL), Sequential Function Chart (SFC) and other language modes with online programming, diagnostics and online simulation and debugging functions, can support MODBUS, MODBUS, MODBUSPLUS, JBUS, UNITELWAY and other communication protocols or communication buses.
3) IPC configuration software: the choice of the current domestic better industrial control software KingView5.1, the software can run on the Win95/98/NT platform, the full Chinese menu, configuration is convenient, the alarm function of a variety of ways, with a fast sampling speed, strong, reliable and high characteristics; real-time, historical trend curve is simple to produce, and other applications such as VisualBasic, VisualFoxpro, EXCEL and so on to realize seamless link, flexible and convenient to realize data calling and report printing.
2.1.6 Working Principle
Weighing filling machine in order to accurately control the filling volume, the quantitative filling machine in the use of position servo control filling to accurately control the stroke of the piston cylinder, but also to achieve precise control of the filling volume. Filling liquid temperature, viscosity changes caused by volume changes caused by fluctuations in quality, between a non-linear relationship, DSP acquisition of liquid viscosity, temperature, pressure, through certain compensation algorithms, to achieve the piston cylinder stroke compensation, the DSP receives PLC weighing and filling machine issued by the location of the command signal, the PLC given the location and the compensation of the location superimposed on the location of the position of the total position as a position of the position given the position signal by the The position signal is adjusted by the composite feed-forward controller in the position loop to form the speed command signal, and the deviation signal after comparing the speed command signal with the speed feedback signal is adjusted by the proportional-integral controller in the speed loop to generate the current command signal, which is transformed by vector in the current loop and then output the torque current by the SPWM to control the operation of the AC servo motor. The position control accuracy is controlled by the number of pulses generated by the rotary encoder per revolution.
1) PLC through the analog input module to read the field data (standard 4 ~ 20mA signal), according to the different ranges of the instrument, the program is converted to standard engineering units; through the high-speed counting module to read the pulse signal of the weighing module, the main program called the instantaneous amount of crude oil, cumulative amount of measurement of the subroutine, according to the pulse / flow rate ratio of the calculation of instantaneous and cumulative amount of crude oil; through the switching volume Through the switching input and output module, the calibration of the weighing module is realized by reading the switching state of the volumetric tube position and controlling the start and stop of the volumetric tube;
2) The on-site IPC uses the communication module to read data from the PLC weighing and filling machine and record them into the history database of the machine, the application program reads and displays the on-site data and the instantaneous and cumulative values of the flow rate; at the same time, the PLC weighing and filling machine also reads and executes the operation commands of the on-site IPC by means of the communication module;
3) Configure one network card in each IPC, and use a strong anti-interference capability between the two IPCs.
A network connection is established between the two IPCs by means of a Category 5 shielded twisted pair cable with strong anti-interference capability. In order to ensure the quality of signal transmission, two hubs are added in the middle of the line, and the remote IPC reads the data from the on-site IPC through this network.
3 Software Design
3.1.1 Software structure
In order to facilitate the operation of the duty personnel, the process screen, calibration screen, reading error correction screen, parameter display and over-limit alarm screen, automatic measurement screen and real-time and historical curve screen of each parameter are compiled, which can automatically record, monitor and alarm each data. There are two ways to switch between different screens: mouse and shortcut keys, which makes the operation flexible and convenient.
The PLC application program includes the main program, parameter acquisition subroutine, parameter overrun alarm subroutine, automatic metering subroutine, error correction subroutine, online calibration subroutine and so on.
3.1.2 Realization of parameter alarm
When the field parameters exceed the specified values (such as inlet and outlet pump temperature/pressure over/under, inlet and outlet pressure over/under, etc.), PLC calls the alarm subroutine to execute the subsequent procedures of the alarm, such as starting and stopping the pump, etc., and the color of the exceeded parameters in the on-site IPC display screen changes and flashes, and the buzzer sounds.
After each alarm occurs, it is necessary for the on-site duty personnel to confirm the alarm and key in their name and work number when confirming. The on-site IPC stores each alarm and acknowledgement information into the historical database for reference.
3.1.3 Realization of automatic metering
As long as the on-site metering module is in operation, the PLC keeps calling the crude oil metering subroutine, using the high-speed counting module to read the number of pulses from the pulse transmitter of the weighing module and convert it to the crude oil flow rate value according to the pulse/flow rate ratio, and then continuously calculates the real-time cumulative or instantaneous flow rate value.
At the same time, the IPC on site uses DDE (Dynamic Data Exchange) to read the database of crude oil standard density and crude oil volume correction coefficient stored in the hard disk, determines the appropriate correction coefficients according to the real-time temperature and pressure of the crude oil, and automatically calculates the standard density, standard volume, standard flow rate of the crude oil, as well as the mixing volume, pure oil volume, and water content of the crude oil for each day and each shift, and prints out the data report.
The specific content of the measurement process is roughly as follows:
(1) Dividing the material into a number of specified quantities to ensure that unit quantities are formed for ease of transportation or sale;
(2) Calculations (including degrees, measures, and scales) are made directly on the production line for the materials being used in accordance with specified error requirements;
(3) Identifying and calculating the completed products for product calculation accuracy control or product classification and selection.
3.1.4 Calibration of weighing module
Each weighing module needs to be calibrated to ensure its accuracy after running for a certain period of time, and the calibration device is generally a standard volume tube. The calibration device is usually a standard volumetric tube. Using PLC to control the start and stop of the volumetric tube, read the status signal of the volumetric tube position detection switch, so as to obtain the reading value of the weighing module in the standard section, and convert it into the flow value under the standard conditions, and then compare it with the standard value of the volumetric tube flow. If the accuracy requirements are met, the weighing module is put back into operation; if not, the weighing module is automatically corrected to meet the accuracy requirements and then put back into operation. So far, a calibration process is completed.
4 Conclusion
The whole set of weighing and filling machine has been running stably for more than one year after installation and commissioning, and the total amount of crude oil transported is nearly 500kt. The degree of automation is high, and all the performance indexes have fully met the design requirements, and the high-speed counter module of PLC is matched with the pulse sender of weighing module, which has a high measuring accuracy and greatly improves its reliability, and it avoids disputes and disputes between the handover units due to the man-made measuring errors; the display screen of the machine is displayed on the screen of the weighing module. The display screen of the filling machine is rich and intuitive, and the operation interface is simple, friendly and easy to use. It reduces the workload of the duty personnel, improves the working efficiency greatly, and achieves good economic benefits.