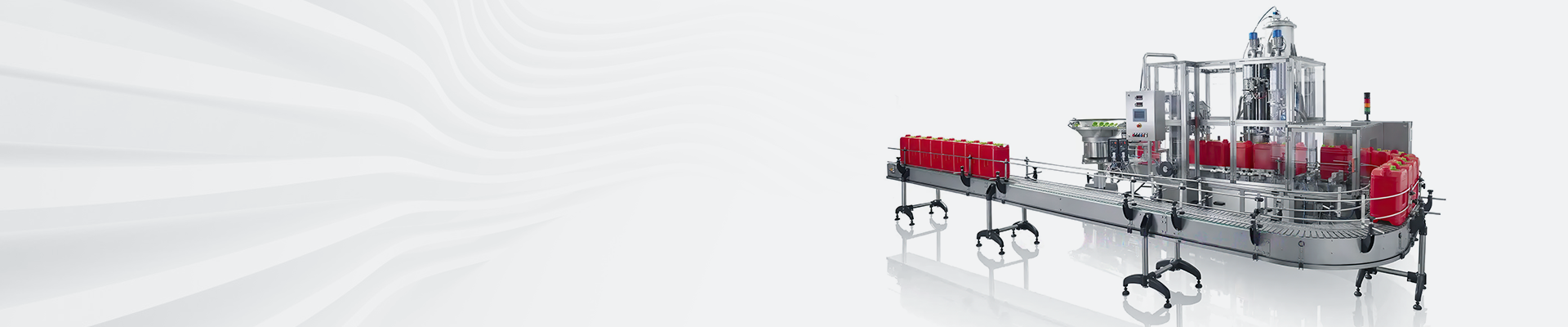
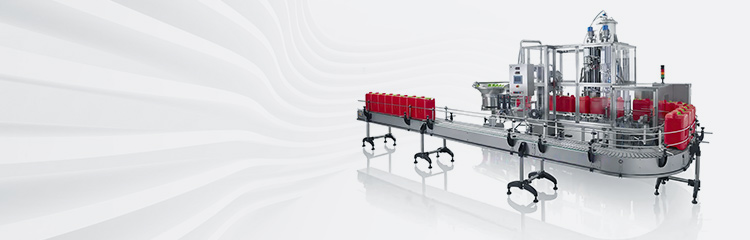

Summary:The automatic batching system forms certain process conditions by adjusting temperature, pressure, and weighing of pigments, and batches fabrics under relatively stable water level, pressure, and temperature conditions.Closed-loop control is implemented for each control variable, and compensation is adjusted in real time based on feedback to achieve stable control effects.
With the continuous development of science and technology, with the increasingly close international and domestic exchanges of weighing technology, it seems that the traditional plastic batching weighing has kept pace with technological progress. On the basis of fully digesting and absorbing domestic and foreign weighing technology, a new type of electronic scale with weighing instrument and weighing module as the core has been introduced. The batching system composed of this new type of electronic scale has been applied in the transformation of weighing system of floating plastic factory and has been successful. This provides a new starting point for the progress of automated weighing technology in the domestic plastics industry.
In this paper, by comparing with the more popular batching system in the current market, omitting the same part, focusing on the different points, to reflect the advantages of the new system.
1 traditional electronic scales and the composition of the system introduction
1.1 weighing instruments and weighing modules composed of electronic scales + manual calibration + school scale weights to periodically confirm the accuracy of the model is the initial calibration to manually carry weights placed on the scale, after calibration, regular calibration of scales with school scale weights, if the display value is found to be biased with the weight value of the weight of the school scale, you need to manually carry weights to calibrate again.
1.2 Weighing system failure can be judged to the instrumentation
If the weighing system failure, if it is the damage of the instrument, it can be displayed accurately, if the specific to which weighing module can not do anything, only through the multimeter to the field weighing module junction box to check the school. If the production process of a weighing module weighing error, it can only have been wrong until the next calibration weights of the periodic confirmation.
1.3 Minimize the impact of vibration on the small material scale to achieve accurate weighing of small materials.
In order to ensure that some small formula materials weighing accuracy, many factories to increase the vibration damping measures, or increase the thickness of the concrete floor, as far as possible to reduce the vibration of the site of large vibration sources such as mixers, belt conveyors and other vibration. But the effect is generally not very obvious, so some factories simply will be small materials to manual weighing. The result of such manual intervention will lead to leakage, wrong addition and the decline of automation management level, it is difficult to control the quality of raw materials from the source.
1.4 Intelligent degree of the system
Due to the limitations of the control mode leads to a variety of control equipment and PLC data exchange between the amount of very little, in addition to the common weighing instruments to achieve some of the data bus communication, others, such as vibratory feeder is generally manually adjust the speed of the site of fast and slow feeding, screw feeder is generally manually adjust the speed of the computer screen of the speed of fast and slow feeding. Therefore, the system's prediction of faults and automatic correction of errors can only be limited to manual observation and spot replenishment combined with automatic adjustment of the suspension amount of control, unable to realize the whole process of intellectualization.
1.5 The degree of realization of remote support function of the system
The remote support function can only diagnose to the computer and PLC level through Ethernet, which can not help the user to find out the cause of the failure of the field equipment remotely in time.
2 Characteristics of the new plastic batching weighing with weighing instrument and weighing module as the core
The new plastic batching weighing system with weighing instrument and weighing module as the core is shown in Fig. 2.
2.1WAVERSAVER vibration ignore
(1)Vibration in process control will cause unstable weight display and inaccurate weighing weight, WAVERSAVER can be quickly ignored.
The WAVERSAVER quickly ignores vibration in industrial and mining equipment and in process production until it is below 0.25Hz, providing a stable weight reading;
(2) Accurate weighing improves product quality and eliminates product waste.
2.2 C2 Second Generation Weightless Electronic Calibration and Integrated Plant IT Diagnostics
(1) C2 calibration does not need to remove the material already in the weighing system;
(2) C2 calibration immediately know the functional integrity of your weighing system;
(3) C2 calibration does not require heavy weights to be repeatedly moved up and down from the weighing system for weighing calibration;
(4) The weighing system can be installed before online C2 electronic calibration and operational verification;
(5) IT provides an in-house diagnostic technique for the system;
(6) IT allows the user to act as a fault inspector through the system's internal diagnostics thereby reducing overhaul costs.
2.3 Safety Memory Module (SMM)
(1) Stores configuration, calibration, and instrument setup data;
(2) Protects all information from destruction;
(3) When a new parameter is entered, the safety memory module
will automatically update the data and store it;
(4) The data is stored in one meter, you can unplug the memory module and load another new meter, it will automatically download the data to the new meter.
2.4 The degree of intelligence of the constituent systems and the corresponding improvement of the control method to improve the increase
The control system is fully intelligent, realizing the true sense of the electric scale weighing
Weight adaptive control. Through the field bus combined with PLC analog acquisition and control, all the key control data such as the scale feeding the target value of suspension, spiral feeder or vibrating feeder speed value, the expectation of automatically completing the control of the value of the time range of the constraints and objective functions with uncertainty and imprecision fuzzy, and come up with the goal to make the various objectives are more "satisfactory". The fuzzy optimal solution is obtained to make each objective more "satisfactory". Through this control method can be easily realized in the specified time PLC automatically adjusts the feeding speed to complete the task of accurate feeding, and can even be extended to the mixer out of the material and crushed plastic discharge of accurate fabric, so that the two do not need to keep manually adjusting the speed due to changes in the formula, so as to achieve the system's prediction of the failure and automatic correction of errors to achieve the whole process of intellectualization.
2.5 Degree of remote technical support for the new system
Due to the built-in chip in the weighing module and the remote control function of the weighing instrument, the new system breaks through the bottleneck of the traditional remote technology which can only support the PLC, and realizes the remote control of the weighing module in the field, which is of high practical value to help the user to find out the cause of the failure of the field equipment remotely in time.
3 The main application principle of the new instrument and weighing module
3.1C2 second generation electronic calibration
3.1.1 Working principle
(1) Before leaving the factory, each weighing module is tested and all the original calibration data are stored in the memory chip and installed in the weighing module;
(2) All the instruments are tested and stored with corresponding standards;
(3) When the instrument is connected to the weighing module, you just need to press the C2 calibration button, the instrument will read out the calibration data on the weighing module and do the mathematical conversion.
3.1.2 Benefits of C2 calibration
(1) Calibration and verification are completed synchronously, saving automatic calibration weights as well as installation space.
(2) Saves time and money during initial calibration, especially when time is of the essence.
(3) C2 provides a desired calibration value and therefore points out problems in weighing quickly and clearly.
3.1.3 Differences from conventional calibration
(1) Ideal curve for conventional calibration;
(2) The actual situation in the production application, the weighing module is not completely linear state, they have hysteresis curve;
(3) Because different weighing modules have different hysteresis curves, even if they are calibrated at full scale, the error at weight increase or decrease will still exist.
3.1.4 Solution for C2 calibration
If you want to test the weighing module with the most suitable weight, it is necessary to know the hysteresis curve of the weighing module to achieve the full range calibration. The application of C2 is to carry out the full range to zero test along the calibration point of the hysteresis curve on the weighing module. At the same time minimize the non-linear hysteresis error, make the weighing module the best when designing the metrology module, and solidify all the parameters into the chip inside the weighing module.
3.2 IT Diagnosis
3.2.1 Principle of IT
(1) Continuously monitor the open or closed circuit status of the excitation current of the built-in chip of the weighing module and the damage status of the line from the meter to the junction box;
(2) Continuously monitor the change state of the excitation current of the meter.
3.2.2 Advantages of IT
(1) No need for any fault detection tools, the fault point can be read out directly from the meter.
(2) No need to have a professional metering engineer to deal with on-site, general operators can find faults.
(3)Through the built-in field bus module of weighing instrument, the fault can be sent to PLC and upper computer system in real time.
(4)It can find out the problem of instrument or weighing module in time in the budding state of failure, reduce the time of fault finding, eliminate the generation of wrong material, so as to realize the stability of plastic quality.
4 Conclusion
Whether from the economic or technical point of view, the continuous improvement of weighing technology is the task required by social development and technological progress. In order to better do with the international level, we need to accelerate the improvement of production equipment and the use of scientific and technological content and efficiency. Through the research and application of weighing instrument and weighing module, it is fully proved that it is more perfect than the current popular weighing technology, and there is a significant improvement, laying the foundation for the updating of weighing technology and equipment. At the same time can bring the majority of users more simple equipment, more stable performance, more economical investment, operation and use of humanized many benefits. We believe that this weighing control mode of application of new technologies to enhance the level of batching technology and improve the quality of plastic products, there are dual application value.