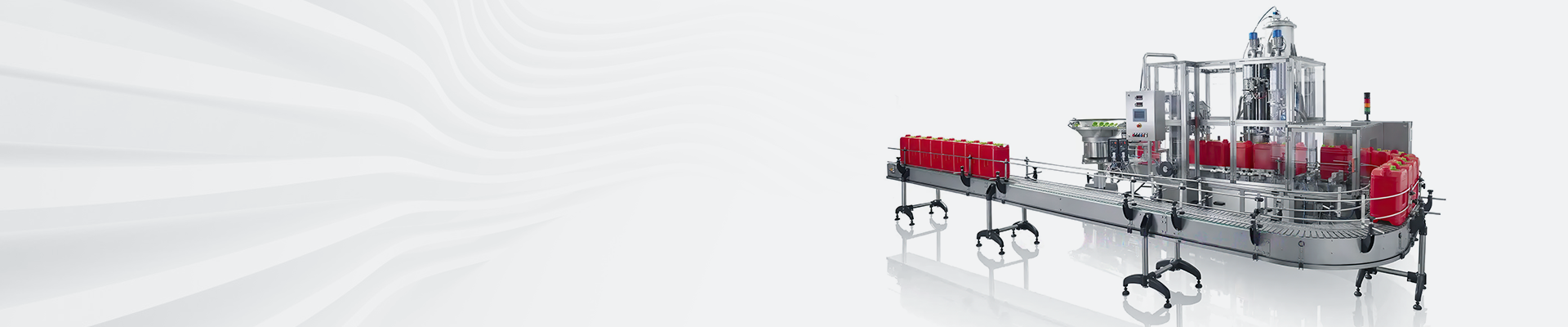
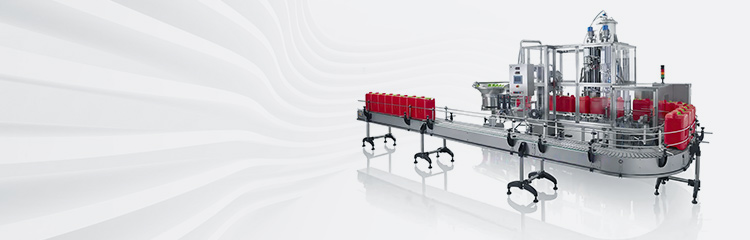

Summary:The automatic filling machine recognizes the identity of the barrels and scans the barcodes of the barrels to be filled one by one. The weighing module sends the barcode data to the server to obtain the barrel file data, and then sends it to the filling scale through the weighing module. The barrel file data can be realized Single or batch updates are read and stored in the FLASH chip through the weighing module interface.
Automatic filling machine in the filling process of the identification of the barrel identity is an important guarantee of the information management of the barrel filling, the use of portable scanners to scan the bar code of the barrel to be filled one by one, the weighing module will be sent to the server to obtain the bar code data barrel archive data, and then through the weighing module sent to the filling scale, the weighing module storage to improve the performance of the filling with a controller compatible with the USB2.0 protocol, using the K9FXX08 series NAND FLASH chip to store the barrel archive data, the data can be single or batch update through the weighing module interface to read the stored in the FLASH chip, when scanning the barrel before filling. The K9FXX08 series NAND FLASH chip is used to store the bucket file data. The bucket file data can be updated individually or in batches, and is stored in the FLASH chip through the weighing module interface, so that when the bucket barcode is scanned prior to filling, the bucket file data is read directly from the FLASH, and when the ZigBee communication is not working properly during the filling process, the filling records will also be stored in the FLASH until the next time when the communication is restored. When ZigBee communication is not normal during the filling process, the filling records are also stored in FLASH and uploaded to the server after the next communication restoration. It is responsible for receiving the polling signals sent from the server to the base station and giving the answer information through the serial port processing, and if the communication frame is the data frame sent from the server to the base station, it directly sends the data sent by the weighing module to the serial port sending buffer, and sends the received data to the serial port receiving area after the data is verified and parsed in a simple manner to ensure the stability of the signals. Through the automatic filling scale composed of the business layer, composed of wireless base station data transmission layer, composed of back-end server data management layer. The ZigBee communication module of the filling electronic scale receives the filling records generated by the filling scale in real time and sends the filling records to the base station. After obtaining the token from the server, the base station polls the filling scales under its jurisdiction within a time slice. If the wireless communication module of the filling scales has data to be sent, it must wait for the query local command from the base station before sending it, or it will not make any response. The base station is responsible for relaying the collected information.
The automatic filling machine needs to transmit the filling records to the ZigBee base station. The base station is responsible for receiving and forwarding data, i.e., the data received from the ZigBee communication module is put on the CAN bus, and the data received from the CAN module is sent out through the ZigBee communication module. The selection of the main controller needs to take into account the functions realized by the current system, future upgrades and expansion, as well as cost and other factors. S3C6410 is selected as the base station controller. S3C6410 is a microcontroller based on ARM11 core, with a main frequency of 667 MHz and rich on-chip resources. NXP LPC2388 is selected as the main controller of the filling electronic scale, which is a processor based on ARM7TDMI-S core with rich peripherals such as USB controller, SPIIC UART interface and other peripherals to meet the needs of the filling electronic scale.
The automatic filling machine can flexibly choose a variety of filling methods according to the actual situation, real-time communication between the management center and the filling system, the filling records are uploaded to the management center database through the wireless mode, the electronic scale itself can also be offline storage of 8000 filling records. It can display the filling data information of each barrel and the daily filling quantity; it can count the barrel filling information by time period, barrel specification and batch, etc.; according to the barrel barcode, it can manage the traceability of each barrel. No need to install and maintain communication lines, ready to use, automatic tare, automatic zeroing of the scale, automatic cut-off at the set quality. It has 3 filling modes: gross, net and standard and 2 filling modes: automatic and manual. It can automatically match the barrel type according to the current quality of the weighing platform. Weighing and filling machine in the use of mm430 frequency converter control pump load, in the pipeline and pump specifications are determined, the corresponding weighing starting frequency is also determined. Frequency greater than 19hz before the weighing output. For this characteristic of frequency conversion speed control pump, measure the frequency of the pump - weighing characteristic curve. The control algorithm is developed based on the measured starting frequency. Below the starting frequency, the open-loop control mode is used, and the input signal of the frequency converter is a ramp function, i.e., a linear incremental voltage signal. After the starting frequency has been reached and weighing has been established, the machine is transferred to the closed-loop control mode. For the closed-loop control mode, it is divided into two modes: proportional (p) control and proportional-integral (pi) control. Proportional control is operated first, and when the actual weighing is close to the set weighing, then it is transferred to the proportional-integral control mode. The use of multimodal control eliminates large fluctuations in the weighing, improves the following performance of the weighing and eliminates the steady state error.