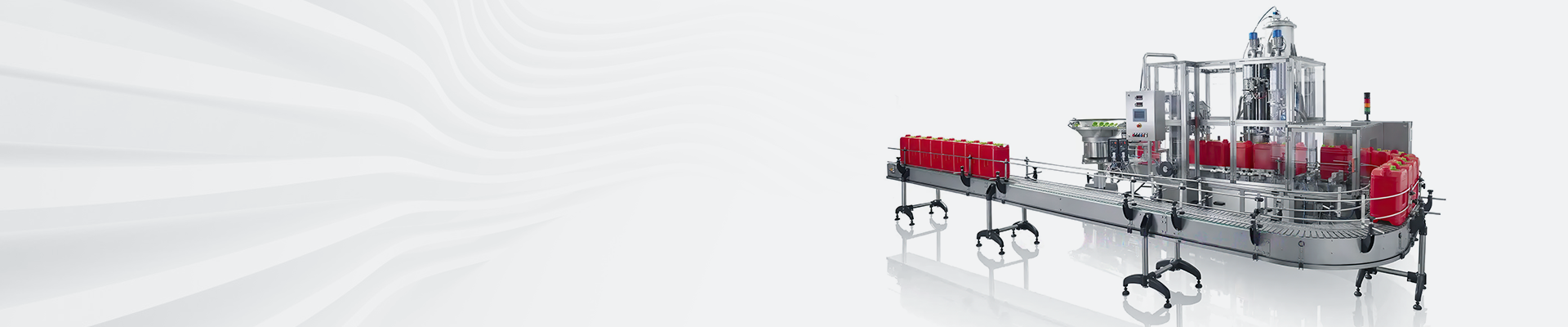
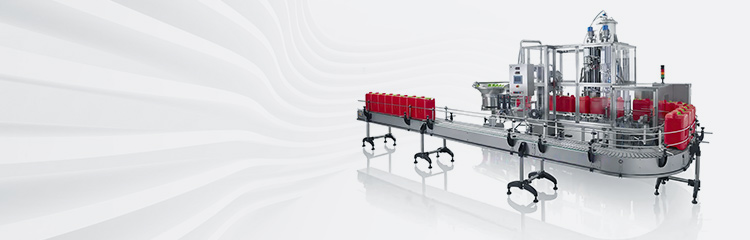

Summary:The application of advanced metering facilities such as tank weighing control system, automatic batch blending system, synchronous metering blending system, and fully automatic liquid filling machine in lubricating oil plants, through period verification, statistical process control technology, and batching systems and other advanced measurement management methods have improved the measurement accuracy of lubricant production enterprises, reduced oil loss, reduced transmission links, and reduced the probability of production accidents and personal injury accidents.
Lubricating oil plants have adopted advanced metering facilities, such as automatic weighing control system for storage tanks, automatic batch blending system, synchronized metering and blending system, automatic liquid filling machine and other metering facilities, which systematically improves the metering accuracy of lubricating oil producers, reduces the transmission link, improves the safety of oil storage and transmission process, and reduces the loss of oil products. At the same time gradually applied during the verification, statistical process control technology, batching system analysis and other advanced measurement management tools to improve the level of measurement management.
1 Application of advanced measurement facilities
1.1 Application of automatic filling system for storage tanks
Tank automatic dosing control system consists of tank front processor and tank star software. It can automatically measure and display the quality, level, temperature, volume and other values of the oil in the storage tank, and the relevant measurement parameters can be displayed in real time on site. It is through the pressure or differential pressure transmitter to measure the oil medium acting on the bottom of the tank static pressure method to measure the quality of the tank, i.e., using the static pressure method. Pre-tank processor using the United States Rosemount company's two-thousandths precision 3051S-A1014 differential pressure transmitter, MDT-0 digital temperature transmitter and FPU-H3 pre-tank processor, and installed in the control room of the computer hardware and software to form a "tank automatic control system" Tank Star software is installed in the operating room of the computer, receiving the output of the pre-tank processor. The Tank Star software is installed in the computer in the operation room, which receives the corresponding data output from the pre-tank processor, and displays the temperature, oil quantity and other production available information through certain programming.
The mass of the liquid in the tank is only related to the static pressure of the liquid and the effective cross-sectional area of the tank, but has nothing to do with the density and temperature of the oil in the tank. In comparison, the manual scale, temperature and density measurement operations have unavoidable errors, and thus the hydrostatic method for oil quality measurement is more superior than the volumetric method for oil quality measurement, and the calculated quality is more accurate. At present, the quality measurement accuracy of the automatic weighing control system in the tank area is better than 2%o, the oil level measurement accuracy is ±3mm, the temperature measurement accuracy is ±0.5℃, and the density measurement can be accurate to 4 decimal places.
1.2 Application of passable ball pipeline system and automatic ball sweeping system
In terms of oil transfer, in order to avoid measurement error caused by oil residue in pipeline and to enhance the safety of oil storage and transfer, the lubricating oil plant adopts the passable ball pipeline convergence system and automatic ball sweeping system.
1.2.1 Passable Ball Pipe Sink System
The passable ball pipeline convergence system is a device used for interconnecting and dismantling multiple pipelines, which consists of a basic frame, a mechanical arm system, a hydraulic system, a double elbow, a horizontal short pipe, a vertical short pipe, a hydraulic cylinder, a control cabinet and other parts. All movements are powered by the hydraulic system, the movements of all mechanical parts are detected by sensors, and the rows and columns are composed of short pipes. In the parts that need to be connected you can open the short tube, the system will be double elbow release, through the hydraulic cylinder action of this row and column, the row and column pressure, the connection is successful. Tube sink adopts triple sealing: rubber sealing ring, hydraulic system, mechanical clamps. The application of the pipe sink reduces the pipeline laying, eliminates the valve, greatly simplifies the operation and avoids mixing and stringing oil accidents. There is no possibility of affecting the quality of the product due to leakage, and there is no additional problem of cross-contamination of products with each other.
1.2.2 Automatic ball sweeping system
The automatic ball sweeping system utilizes compressed air to push the ball in the pipeline to empty the pipeline. The system mainly consists of ball pass special equipment, precision pipeline, pipe cleaning ball parts, ball pass launching station, receiving station and intermediate station. Among them, the ball special equipment includes the patent ball with replaceable seals, receiving and sending ball ball valve, on-line ball valve, receiving and sending ball valve and on-line ball valve composed of clarinet valve group, twin ball valve, three ball valve, multi-pass ball valve and so on. The body of the through-ball valve is designed with a stopper, so that in the event of a problem (e.g., sweep line overspeed), only the stopper is damaged and can be replaced quickly without having to replace the entire valve. As a result, the entire pipeline will not be out of service due to valve maintenance.
The maximum residue in the receiving and sending station and oil and gas discharge branch pipe of the automatic ball sweeping system does not exceed 40 m. The maximum residue in the ball sweeping line does not exceed 100 m after a single single ball sweeping in every 100 meters of pipeline (viscosity range: 100~150mm'/s when the oil temperature is 40℃).
The automatic through-ball sweeping system can transport different products to different destinations without contamination through a single pipeline, reducing pipeline investment and saving space to a greater extent, minimizing contamination and reducing product loss.
1.3 Measuring facilities for product blending process
Lubricating oil plant is equipped with a set of U.S. FMC tank-type automatic batch blending system ("ABB"), synchronized metering and blending system (hereinafter referred to as "SMB"), direct weighing and measuring of oil products, high metering accuracy, can be added directly to the solid additives, can clean the blending kettle, the oil can be added directly to the solid additives. The blending kettle can be cleaned, and the oil blending production is flexible, allowing for quick product changeover. The use of these high-precision metering facilities in the blending process improves the accuracy of metering, reduces the number of transmission links, and reduces the risks of production accidents and personal injuries brought about by frequent operation, thus improving the safety of the blending process.
1.3.1 Application of ABB
The system consists of steam tracing jacket, weighing module, cleaning head, vertical high-speed stirrer, feeding valve, automatic discharge valve, blending kettle and so on. The blending kettle is mounted on the weighing module and utilizes a high-precision metering module to achieve feed metering. Various kinds of base oils and additives are sent to the blending kettle by pumps, and the operating system automatically displays the dosage, and when the dosage reaches the given value, the feed valve closes and the pump stops. When the feeding is finished, the stirrer will be turned on to stir, and at the same time, the pneumatic valve of the heating coil outside the mixing kettle of ABB will be turned on automatically to stir while heating until the materials are stirred uniformly and blended into products. The system can control the metering error at ±7.5kg when mixing 10t of oil per batch and +5kg when mixing 2t of oil per batch.
1.3.2 Application of SMB
The system consists of 6 channels for base oil delivery and additive delivery. Each metering channel consists of an automatic inlet valve (for each component), mass flow meter, flow control valve and check valve. The blending media is discharged through the SMB system output manifold to the product tanks via an automatic manifold. After the raw material name, tank number and addition ratio are determined correctly in each process program, it enters into the recipe preparation, through the steps of creating recipe, generating recipe, recipe running and other steps for production blending. High efficiency in large-volume blending, strong adaptability to the recipe, for any recipe can be the maximum flow rate of the pump at the same time metering and delivery of raw materials. Since the final product is not in the manifold, it is possible to deliver the additives first and clean the line with base oil at the end: due to the possibility of using two-position control and the fact that the metering channels can be shared, i.e., some of the metering channels can be used more than twice during the blending of a batch. When the blending volume is 2 tons/batch, the metering accuracy is 0.3%; when the blending volume is >4 tons/batch, the integrated metering accuracy is female 0.25%.
1.4 Product filling process measurement facilities
The lubricating oil plant has 16 filling lines for various lubricating oil packaging oil specifications, with volume filling machines and weight filling machines, which can fill different specifications of packaging oil products from 1L to 1000L.
1.4.1 Adoption of fully automatic filling line
The 4L filling line adopts full-automatic metering filling machine, which consists of full-automatic filling machine, full-automatic wrapping machine and robot palletizer with 20 independent weighing filling heads. When the viscosity of finished oil changes, the filling speed can be compensated automatically. Its coarse to fine filling process and valve closing operation can be carried out gently to avoid air bubbles. The filling precision is high with standard deviation ±2.0g and average deviation ±0.5g/100 barrels. The fully automatic filling machine is a high-speed, high-precision rotary weighing and filling machine, with a filling speed of 6,000 barrels/hour, a standard filling accuracy of ±2.0g/barrel, and an average deviation of ±0.5g/100 barrels. Empty barrel conveying adopts vertical curve-type conveying chute, which is simple, practical and inexpensive, and no manual operation is required. The operation part of the main machine adopts touch panel, which can be used for conveying the empty barrels, filling oil, placing the inner cap automatically and tightening it, placing the outer cap automatically and spraying code on the barrels, and the whole series of processes only need one person to monitor and complete all the operations, which really realizes low cost and high efficiency.
Full-automatic wrapping machine mainly consists of turning barrel area, feeding barrel area, carton population area and molding area, the wrapping speed is 1200~1250 cases/hour; the whole wrapping process adopts automatic chain control, the wrapping speed is divided into three grades of high, medium and low, which can be chosen independently when operating, which is convenient and practical. Modular aluminum alloy bow frame design, easy to disassemble; full automation flow operation design, more convenient operation and use; motor, reducer, cam, tighten the arm operation in one, packing performance is excellent, less failure, easy to maintain; packing action is soft, durability is excellent, the overall function is perfect; packing molding with automatic spray glue adhesive sealing, environmentally friendly and low-consumption.
Weighing and filling machine is set up with a lack of barrel detection system, which is to solve the phenomenon of lack of barrels when entering the wrapping area due to the combination of barrels not being in place during the high-speed operation of the wrapping machine. In the normal production process, when the barrel passes through the detection area, the detection metal will use the favorable mechanical structure of the metal sheet to accurately contact the barrel, while counting photoelectric will count. If the barrel is missing, the metal detects one less barrel, and the counting photoelectricity will count one less time, then the counting photoelectricity will return the error signal, the alarm device will sound automatically, and an I0 switch output will stop the current state of the 0CME wrapping machine without interrupting the original workflow of the 0C-ME wrapping machine. This system has a simple structure, easy to install and maintain, without manual operation, without changing the structure and control system of OCME itself, completely solved the problem of the lack of barrels that existed in the whole parcel machine part, and guaranteed the quality of the product at the same time, greatly improved the safety of the equipment operation, and avoided personal injury in the process of dealing with the fault.
1.4.2 Adoption of the box missing barrel weighing checkweigher
The 4L-3 and 1L filling lines in the lube oil plant use automatic sorting scales. This series of electronic scales consists of standard positioning bracket, belt conveyor and checkweighing disk. The equipment occupies small space and can be installed between the production lines according to the specific conditions, runs noiselessly, safely and smoothly, and operates 700 cases per hour. At the same time, according to the specifications of the production products, different groups of upper and lower limit weights can be set to weigh the packages and finished products, and if there are finished products that do not meet the set weight range, the alarm will be prompted to facilitate the operator to make timely adjustments to the products. During the operation, it can be turned on and off at any time according to the operation requirements of the production line.
In production, the automatic checkweigher installed in the back of the sealing machine, packing tape after packing, the product through the scale conveyor belt, the weighing instrument can show the actual quality of the product, if the product within the set range, it will be smooth through the conveyor belt, and at the same time for the spray code.
2 advanced measurement management tools
2.1 The implementation of the period of verification of sampling scales
Period verification is in the measurement equipment in the adjacent two calibration or verification period, the use of credible methods of its use of functionality and measurement performance of a verification to verify whether it is effectively maintained, that is, to confirm the credibility of the calibration status of the measurement equipment. In lubricant plants, each filling head is subjected to mandatory calibration before the filling machine is used. Due to the long interval between calibration cycles, lubricant packaging products are assembly line operations, due to equipment, operation and other issues will lead to inaccurate measurement of the filling head, filling accuracy does not meet the national standard requirements, causing quality accidents. Management, the requirements to strengthen the measurement of sampling, each filling line set up a high-precision electronic scales, each line of each filling head product sampling, compare the weight of the product to meet the requirements. Random check scales are used to verify the measurement errors of packaged products and filling heads of filling lines, and period verification is used to verify the measurement capability of the random check scales.
The period verification of each sampling scale of the filling line is carried out by using standard weights and weighing and metering. The weights are sequentially labeled and the weights are calibrated once a year. Each sampling scale is required to be placed in a fixed position, and the accuracy and index value of each scale cannot be adjusted without authorization. Reasonably determined the requirements of the indicators during the verification of 2e (e is the index value of each scale): when the scale shows the value of the difference between the mass of the scale and the weights <1e, normal use; when the scale shows the value of the mass of the scale and the mass of the weights <2e, the observation of the use of the scale; when the scale shows the value of the mass of the scale and the mass of the weights >2e, stop using, and report for repair or re-checking. And determine the daytime of the 10-15th of each month to complete the measurement period verification of each scale of the ton box. During the daytime of 10-15 days of every two months, the verification period of other sampled scales will be completed.
By sampling the electronic scales during the verification work, we can avoid the risk that the scales do not meet the metrological requirements, resulting in the measurement of the filling line can not be adjusted properly, the measurement of the excessively poor. Avoid the loss of measurement and reputation impact brought about by the shipment of products. In particular, the period of verification of the ton box scale, to a large extent, to strengthen the scale inspection, self-calibration and maintenance, and improve the accuracy of measurement.
2.2 Volumetric filling machine using statistical process control technology (hereinafter referred to as "SPC")
The implementation of SPC is centralized and managed by production and quality related personnel. For several filling lines of volumetric type, it is required to ensure the effective application of SPC tools in the production process. At the beginning of each year, the packaging unit is organized to prepare the SPC Implementation Plan to ensure that each volumetric filling line carries out a process capability analysis at least once a year, so that the filling capacity of the filling line meets the requirements. For the volumetric filling line to carry out process capability analysis requirements, the "Filling Process Capability Analysis Guidance Book" was issued. The implementation unit is required to prepare the Filling Process Capability Analysis Report based on the results of SPC implementation.
SPC requirements to determine the appropriate grouping, usually take the sample capacity of 4, the number of samples 25, a total of 100 data, analysis. The corresponding analysis, calculation process based on the relevant software can simplify the operation, analysis of the judgment can be based on relevant SPC control standards.
Requirements for the implementation of the unit according to the results of SPC implementation, the preparation of "filling process capability analysis report". For process capability is insufficient to take appropriate measures to improve.
2.3 Application of batching system analysis (hereinafter referred to as "MSA")
At the beginning of each year, the relevant quality, measurement management personnel are responsible for organizing the dosage system using unit personnel to prepare "dosage system analysis annual plan".
Determine the measurement of dosage system analysis equipment, evaluators, measured characteristics, analysis methods. Priority should be given to the analysis of the control plan in the feeding system, from the normal operation of the personnel of the testing equipment to select the evaluator, select the most stringent requirements of the characteristics of the product being measured characteristics of the feeding system analysis, and according to the requirements of the actual use of the feeding system to choose the appropriate research method. Take the MSA of a fully automatic viscosity tester in a lubricating oil factory as an example. Take certain data, repeatability and reproducibility analysis, linearity judgment, stability analysis.
3 Conclusion
Lubricating oil plant adopts advanced tank weighing and filling system, ABB, SMB, automatic filling machine and other metering facilities, which systematically improves the metering accuracy of lubricating oil producers, reduces the transmission link, and reduces the loss of oil products. It greatly improves the safety of oil storage and transfer process, simplifies the operation link in the tank area, and reduces the probability of production accidents as well as personal injury accidents.
In the process of lubricant production management, the lubricant plant adopts advanced measurement management methods such as periodical audit, SPC, MSA, etc., which further ensures the accuracy and effectiveness of measurement and improves the level of measurement management.