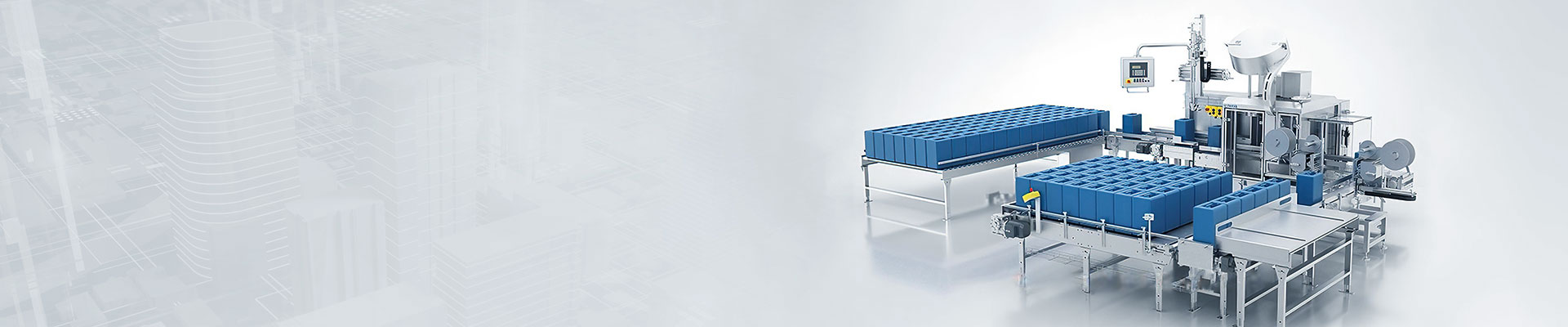
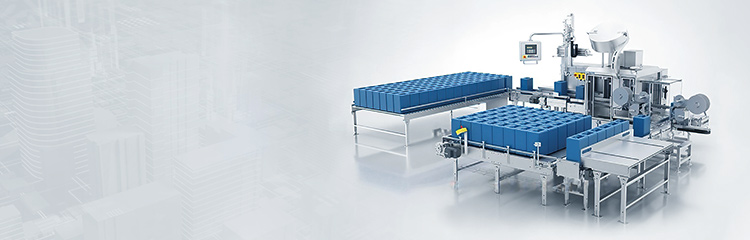
Lubricating oil filling machine set control plastic drum disinfection, bottle delivery, quantitative filling, cap feed and cap rolling and other functions in one, controlled by the frequency converter continuous rotation operation of the large plate using the barrel positioning technology to achieve the feed of the control drum, the whole circumference of the rotating plate is evenly divided into multiple groups, each group has multiple barrels to be filled at the same time, when the filling signal arrives, A plurality of filling needles are controlled by a CAM mechanism operating in coordination with the rotary plate to drop to a certain depth in several drums, and at the same time run synchronously with the rotary plate and fill.

Automatic Filling machine by the weighing sensor platform under the control of microcomputer program to set the measurement, is a high-precision, high-tech product. It is a new type of machine that integrates machine, electricity and instrument. Changed the traditional flowmeter filling quantitative accuracy and can not measure the more viscous liquid defects, is civilized production and national regulations after the elimination of lever scale, integration of weighing and filling ideal filling equipment. When filling, the tare weight is removed automatically, and the material is injected into the container in large quantities and fast filling and then corrected and measured in small doses at a slow speed. The operator only needs to put the container into the platform and align the barrel mouth with the filling nozzle. At this time, the program starts, the filling nozzle is lowered, and the filling valve is opened to feed.
The main function of the weighing filling machine is to fill the liquid medium into the packaging container to achieve filling, sealing, weighing, stacking and other functions. The Filling system adopts sequence control, motion control, communication, data management microprocessor technology and communication technology to filter, judge and store the input signal, and transmit the output signal to the executive mechanism of the filling system to complete the filling command, real-time control of the bucket position in the online container, pre-pressure of the filling barrel with pressure control, and adjustment of the conveying chain speed. When the container on the conveyor chain is blocked, it is also necessary to coordinate the feed speed of each drag point of the entire production line. The coordination signal is dragged to other conveyor chains in the production line, and the control system also carries out real-time detection and control on the place of empty/full drums, stacking, capping, opening/closing the filling valve, etc. The PLC signal drives the motor and other transmission mechanisms to drive the manipulator to move, and at the same time drives the encoder with the motor to feedback the number of abusive pulses to the driver. The driver compares the two kinds of pulses and determines the deviation, and the correction signal obtained after calculating according to certain control laws is used as the given speed controller in the servo driver and then is adjusted by current and amplified by power. Make the grasping manipulator move in the direction of eliminating the deviation, so as to realize the stacking positioning of the manipulator.