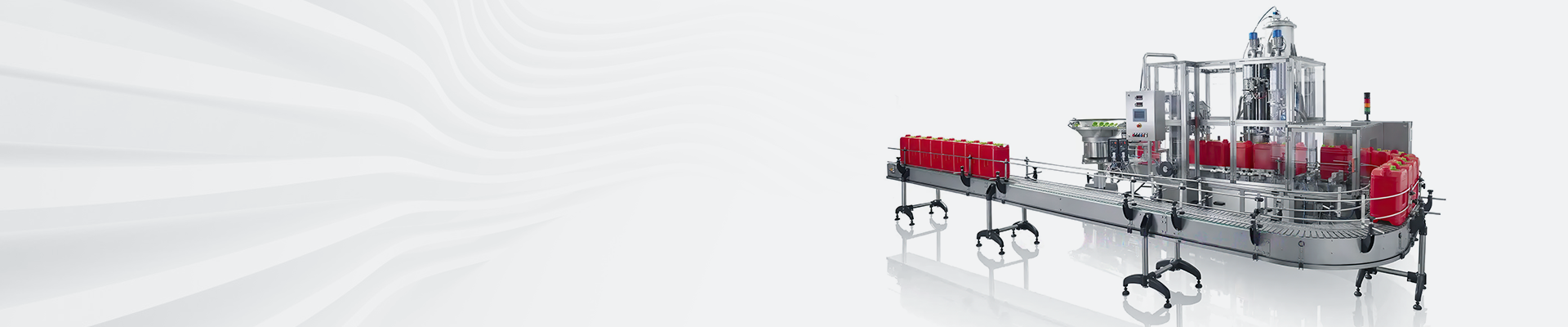
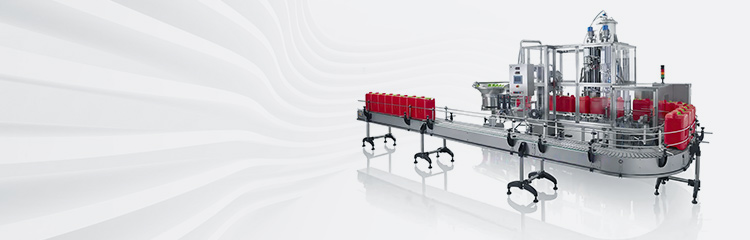

Summary:The operation of the automatic filling machine includes: tare weight verification → fast feeding → slow feeding → weighing verification → unloading.The control system checks the tare weight. If the tare weight is not zero, weight compensation sets the filling weight.
Gravity filling machine working principle and problems
Measurement of filling machine operation includes: calibration tare → fast feeding → slow feeding → weighing calibration → unloading. Control system calibration tare, if the tare weight is not zero, weight compensation to filling set weight to ensure that the net weight of the weighed material is not affected by the weighing hopper tare, the total to maintain the user's set value. After checking the tare weight, the control system outputs a fast-feeding signal to the feeding device, so that the fast-feeding cylinder in the feeding device controls the feeding door to open quickly, and the material flows into the weighing hopper with a larger flow rate. At this time, the control system through the reception of sensor signals, constantly monitor the weight of the weighing hopper changes, when the weight of the material into the weighing hopper is close to the weight of the fast charging settings, the system controls the fast charging cylinder quickly closed, fast charging signal to slow charging signal, the material at this time to a smaller flow into the weighing hopper to ensure that the system to a higher precision control of the inflow of the material in the weighing hopper. The control system through the system mathematical modeling operations, can accurately predict an amount of advance, stop the entire feeding process, so that the final weight of the material in the weighing hopper for the user to set the weight of the system after the end of the feeding into the weighing verification state. The purpose of weighing verification is in the fast and slow feeding are stopped, the system to further confirm that the weight of the material into the weighing hopper in the user's set weight error within the allowable range, if within the error range, the system will unloading operation, otherwise the system alarm, waiting for the operator to deal with, the operator to deal with the completion of the system continues to run.
After the system is finished unloading, the unloading door in the weighing hopper will be closed immediately, so the system has completed a cycle of operation. At this time, if the operator is set to continuous operation, the system will start the next cycle of operation. Has been filled with material filling bag falls on the bag feeding device, for the next folding, sewing, transfer and other processes.
Weighing filling machine working principle can be seen, gravity filling equipment in the feeding section of the two-stage filling, large flow rate to do fast filling, when the amount of material to reach the set weight of 80% ~ 90%, changed to small flow rate to do slow filling, until the target value is reached. The mathematical model is:
Where: Q is the actual dosing volume; qi is the dosing flow rate of the ith section; ti (i=1, 2) is the dosing time of the ith section δj (j=1, 2, 3) is the weighing error, control error and other errors.
Under the premise of time and filling volume set by the filling system, in order to ensure the filling speed, fast dosing section t1 time within the dosing volume q1. as large as possible, but also hope that the value of t1 is as small as possible; in order to ensure the filling accuracy, slow dosing section t2 time, the smaller q2 needs to be, the larger t2. But the material from the fast feeding to slow feeding conversion process, due to large changes in the amount of material, the material on the weighing hopper will have an impact, and make it vibration, weighing instrumentation sampling has a great impact, this is the two-stage charging method can not be avoided the main problem. The larger the fast charging flow, the more obvious impact vibration, because in the whole charging process, the weighing instrument constantly sampling, and the sampling results with the set weight comparison, when the maximum amplitude of the weighing hopper more than the set amplitude of the system, the weighing instrument will be used as a signal to set the weight of the abortive slow charging, the results of unqualified filling volume, so too large fast charging volume not only will not improve the speed of weighing, but also may affect the precision of weighing Or extend the entire weighing time. In order to avoid this shortcoming, the current common practice is to increase the filling volume of slow dosing, that is to say, to extend the slow dosing time, at the expense of filling speed to ensure filling accuracy. Therefore, the use of two-stage dosing not only can not improve the filling speed, but also has an impact on the accuracy. How to eliminate the shortcomings of two-stage dosing, which is the focus of this paper.
Principle of three-stage variable speed filling system
To eliminate the shortcomings of the two-stage filling and to reduce the impact of the fast-filling material on the weighing hopper, it is necessary to solve the system's filling method, and the measures taken are as follows.
Feeding hopper charging (the first stage of charging)
The basic idea is to add a set of flow on the original feeder adjustable feeding bucket, the two-stage feeding into a three-stage feeding, its structure is shown in Figure 1, the role of the feeding bucket is to reduce the user's silo in the material to the height of the weighing hopper to achieve a reduction in the weighing hopper from the material to the impact of the large flow of material to ensure the accuracy of measurement.
Where: Q1 for the first section of the charging volume, its size and charging hopper in the lower part of the flow regulator plate and the upper part of the charger between the amount of stored material; q1 is a constant, the amount of material per unit of time; t1 for the first section of the fast charging time.
Variable speed fast dosing (second stage dosing)
And as mentioned above, fast and slow feeding two double-acting cylinder control feeder in the shut-off door action, but in the fast and slow feeding switching process, that is, fast feeding will end when the state, the material has a greater impact on the weighing bucket, the experiments found that the use of variable-flow feeding can be avoided fast and slow feeding switching due to the fast feeding large flow on the impact of the weighing bucket to reduce the measurement error. The use of two one-way throttle valve to control the fast dosing cylinder speed of one-way speed control circuit.
Liquid filling machine using inlet speed control, its purpose is to use the inlet throttle speed control, speed control valve near the cylinder installation, the average speed of the piston is low, fluctuations in the entire stroke, the piston speed gradually increased; cylinder filling pressure rises slowly, to reach the gas source pressure is also slow, in addition, and then with the valve 1 and valve 2 spool adjusted to a suitable number of laps, so as to ensure that the fast dosing cylinder piston rod extends out fast, return slow, and thus achieve the control of fast dosing material gate. So as to achieve the control of fast feeding material door opening and closing speed.
Slow filling (the third section of the filling)
In order to ensure the filling accuracy, filling system in the end of the fast filling, fast filling door quickly closed, slow filling door open. This section of the filling volume than common gravity automatic filling machine slow filling filling volume, to reduce 5% to 7%. The total filling amount of the three-stage variable-speed feeding system will be derived from the expression for the total filling amount of the three-stage variable-speed feeding system:
The control system compares the total filling quantity Q with the system set weight Qs, if it is within the accuracy range Δξ, the discharging device is operated, otherwise, the system alarms. The working model is as follows: Q-QsΔξ system discharge; Q-QsΔξ system alarm.
Realization and Conclusion
The principle of three-stage variable-speed feeding of automatic filling machine is tested on Wuhan Rentian CJZD-50 large bag automatic filling machine, which selects small granular edible iodized salt with good fluidity as the filling material, and the filling volume is 50kg, which results in the filling speed of up to 12 packets per minute, and the filling accuracy can be controlled at ±1‰. Now this product has been used in most of the domestic salt factory, sales have been more than 30 sets, the operating effect has been good.
For the inadequacy of the current two-stage charging, put forward the three-stage charging principle, the use of charging bucket charging and variable speed control charging door action, so that it is quickly opened, closed at variable speed, to reduce the fast charging of the material on the impact of the weighing hopper.