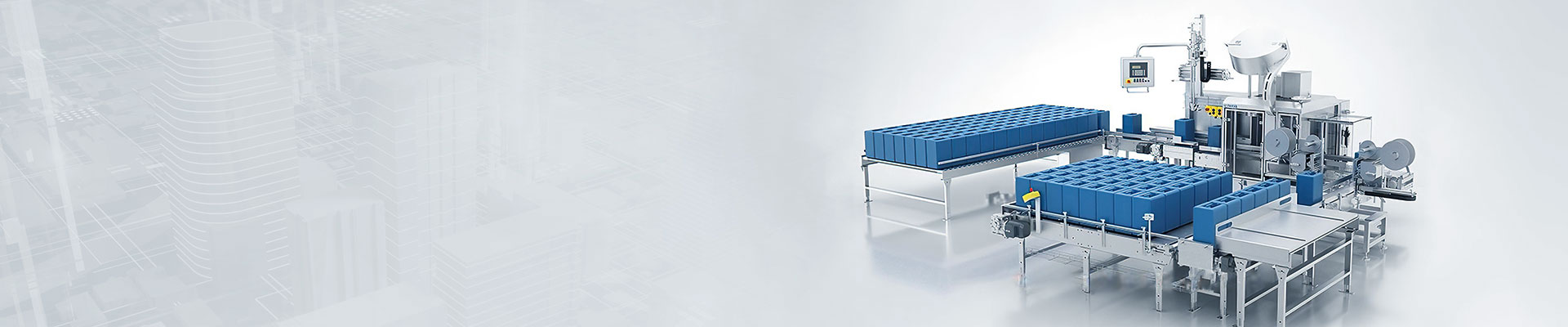
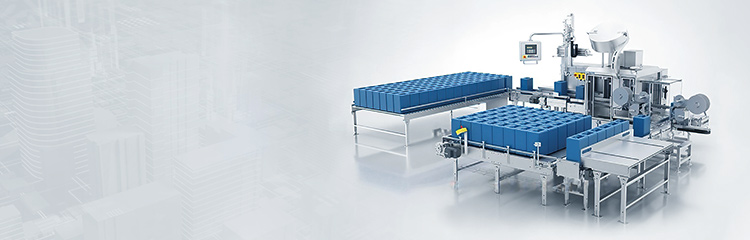
Methanol auxiliary filling machine adopts two-stage automatic filling method of size material, adopts barcode recognition, wireless transmission, automatic weighing, PLC control, mechanical and electrical, computer interface and other automation technologies, and independently develops intelligent filling weighing and inventory management system to prevent wrong materials in filling, ensure weighing accuracy and ensure the accuracy of filling process. Each batch of filling data is recorded and traceable, and the principle of first-in-first-out is followed when the raw materials are sent out, which effectively solves the waste of raw materials.

Liquid Filling machine adopts two-stage size material automatic quantitative filling machine filling method and one-button operation: start - filling gun down - automatic tare - start filling - finish filling gun up, Japan Mitsubishi PLC programmable controller and other high-end electrical accessories manufacturing Reliable performance; manufactured using the "QB/T2501-2000 gravity automatic loading scale" standard, Electronic scales in line with OIMLR61 international recommendations.
Automatic filling and filling machine adopts two-stage size material automatic filling method, adopts bar code (two-dimensional code/RFID) identification, wireless transmission, automatic weighing, PLC control, electromechanical, computer interface and other automation technologies, independent development and completion of intelligent filling weighing and inventory management system, to prevent the filling of wrong materials, to ensure the precision of the weighing, to ensure the accuracy of the filling process, so that each batch of filling data is recorded Traceability, and follow the principle of first-in-first-out when the raw materials are out of the warehouse, effectively solving the waste of raw materials.
Automatic filling machine refers to the Weighing system that integrates weight information collection, amplification, transformation, transmission, processing and display, and controls each sensor, relay, switch and solenoid valve through PLC program. Drawing on the advanced technology and techniques, and combining with its own long-term experience, it integrates the inventory management, filling management, filling and weighing, process control, and product traceability into one.
Basic parameters
Maximum weighing capacity: 1200kg
Minimum Sensitivity: 100g
Filling range: 100-1200kg
Filling Error: ≤0.1%
Filling speed: 30-45 barrels/h (depending on flow rate and pulse force)
Head material: SUS304 stainless steel (optional SUS316)
Applicable container: ≤Ф600xh950mm
Power supply: AC220/50Hz
Using gas source: 0.5Mpa
Use temperature: -10℃-50℃