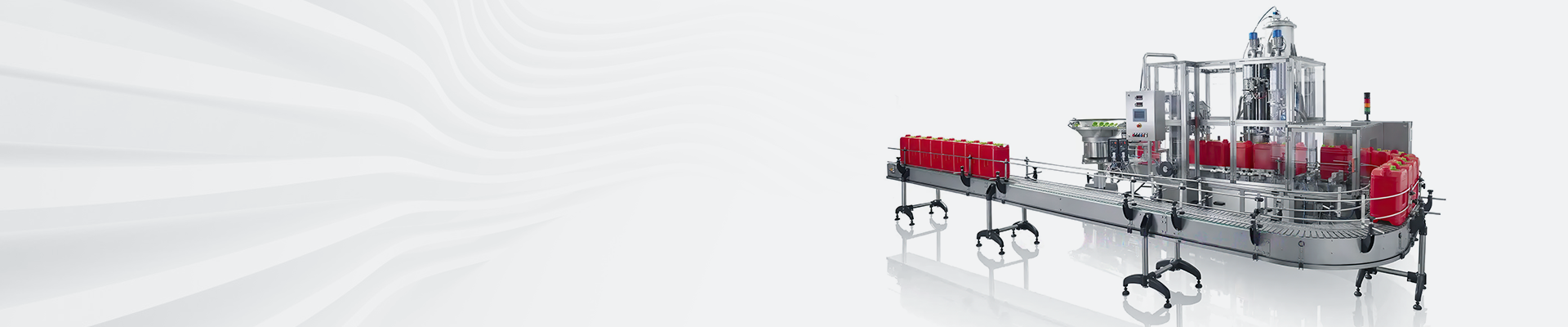
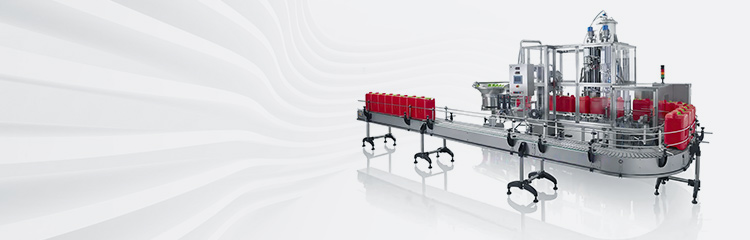

Summary:The liquid filling machine consists of a bottle feeding mechanism, an online weighing device, a main conveyor belt tracking filling device, an oscillating stoppering device, and a bottle discharging device.The bottle feeding mechanism consists of a bottle feeding mesh belt, a bottle dividing screw, a small conveyor belt and a dial. The small conveyor belt adds power to the transportation of medicine bottles, so that the bottles can be transported smoothly at the required speed.The structure of the online weighing device and the entire transmission mechanism are independent of each other, ensuring the weighing environment; combined with the weighing module, high-precision weighing is achieved.The oscillating stoppering device uses a cylindrical cam mechanism to realize the tracking function of the filling machine, and uses dynamic sealing technology to complete the stoppering process.
1 filling machinery is an important part of the packaging machinery, food filling is basically automated production. Food filling should be in line with GMP (food production quality assurance specifications), for the filling of the accuracy, safety and stability of the higher requirements. PLC control has a simple program, reliable, easy to use and so on, and can be through the human-computer interface to monitor the operating state, online modification of the operating parameters can be better maintenance of the machine's operation. Therefore, in the field of filling machine automatic control is more and more widely used. In reference to foreign fully automatic filling machine on the basis of advanced models, combined with the actual situation of domestic liquid filling, independent development, design and manufacture of a new type of fully automatic liquid filling machine, its performance can completely replace the import of similar products, has a good cost-effective, to meet the requirements of the enterprise, in the intellectual property industry has a broad application prospects.
The filling equipment adopts Mitsubishi PLC to realize control, 12 head filling at the same time, the highest filling speed of up to 600 bottles / minute, to avoid the phenomenon of bottle jamming, pouring bottles, weighing high precision, and greatly improve the filling efficiency. The process flow is bottle filling - weighing - corking and dispensing. Among them, the reasonable and orderly completion of the bottle is the key to the realization of the subsequent process, but also the filling machine can be a prerequisite for stable operation.
2 structure overview
Automatic filling machine consists of bottle feeding mechanism, online weighing device, main conveyor belt tracking filling device, vibration corking device, bottle discharge device and other components. The bottle feeding mechanism consists of bottle feeding mesh belt, bottle separating screw, small conveyor belt and dial, etc. The small conveyor belt increases the power for bottle conveying, so that the bottles can be transmitted smoothly according to the required speed. The structure of on-line weighing device is independent from the whole transmission mechanism, which ensures the weighing environment; combined with the weighing module, it realizes high-precision weighing. The oscillating corking device utilizes a cylindrical cam mechanism to achieve the tracking function of the filling machine and dynamic sealing technology to complete the corking process. The online filling system and the vibration stoppering device are the two main innovations of this metering and filling machine. After being cleaned, sterilized and dried, the bottles are transported to the bottle feeding mechanism, separated and sorted out by the bottle separating mechanism, and then transported to the main conveyor belt according to a certain spacing and speed to be filled with liquid and other subsequent processes. The coordinated movement of the bottle feeding mechanism plays an important role in the normal operation of the filling machine. Reasonable control of the bottle feeding is the basis for the completion of subsequent processes.
3 into the bottle program
The weighing and filling machine is a 12-pin simultaneous filling, which is required to achieve a filling speed of 600 bottles per minute, with a loading error of ≤ 1%. Filling system in the process of filling liquid, the use of two online weighing device were empty and fill the liquid of the same bottle for weighing. Each in-line weighing device is designed with a collet to take out and put back the vials from the main conveyor belt, so there must be enough space for the collet to enter and exit the main conveyor belt next to the vials to be weighed to avoid tripping over the vials next to it. This places a premium on the type of bottle feed that is required. Empty bottle positions are used to realize the positional space for the collet to enter and exit, by controlling so that one empty bottle position is reserved on each side of the bottle to be weighed, which is indicated by the symbol xOx; three empty bottle positions are set up at the position where the collet is put back into the bottle, which is indicated as xxx.
Each of the two in-line weighing devices uses a metering module to detect the empty bottle position information. When the weighing module on the left side detects the xOx signal for the first time the in-line weighing 1 is actuated and clamps the empty bottle for weighing, and when the sensor detects the xxx signal, the bottle is put back to the middle empty bottle position on the conveyor belt, which is followed by the xOx signal; the bottle is filled with liquid and then continues to be conveyed, and when the sensor on the right side detects the xOx signal, the in-line weighing 2 clamps this bottle for weighing, and when the sensor detects the xxx When the sensor detects xxx signal, the bottle is put back to the conveyor. Weighing of one bottle position is completed.
In order to weigh the bottles at all 12 bottle positions, a cycle consisting of 12 parts is set up. In a weighing cycle, the order of bottle entry (right side first) of the bottles entering the main conveyor belt is such that the bottles whose weighing is completed at the previous bottle position are placed in the position of the empty bottles that start weighing at the next bottle position, in order to shorten the cycle time and to improve the filling accuracy.
4 PLC control system design
4.1 Control flow design
The setting of the bottle position is completed by the bottle separating screw. The bottles transferred in from the bottle feeding mesh belt are separated by the bottle separating screw at a --- fixed spacing and speed, and then transferred to the main conveyor by the dial. The bottle separating screw is driven by a servomotor, which controls the bottle position by changing the motor speed. When the servo motor rotates at the initial speed n, the screw delivers bottles at an average speed of u, and delivers 4 bottles at 4 stations, which can be expressed as OOOO; when the motor speed becomes n/2, the screw delivers bottles at an average speed of w/2, and delivers only 2 bottles at 4 stations, which can be expressed as OxOx, and produces the signal for the bottle position of xOx; when the motor speed becomes n/4, the screw delivers bottles at a speed of w/4, and delivers 1 bottle at 4 stations, which produces the signal for the bottle position of xOx; when the motor speed becomes n/4, the screw delivers bottles at a speed of w/4, and delivers 1 bottle at 4 stations, which is the same as that of the bottle position of the bottle position. When the motor speed becomes n/4, the screw feeding speed becomes w/4, and 1 bottle is fed at 4 stations, which can be expressed as Oxxx, and xxx bottle position signal is generated. Installation of fiber-optic sensors at the junction of the bottle-splitting screw and the dial is used to count the bottle position, according to the order of feeding bottles, and design the control process. Here is the method of deceleration, can also be used to stop the motor to set the bottle position, because the motor restart requires a certain amount of acceleration time, and frequent starts and stops will produce shocks, is not conducive to the stable operation of the machine tool, but also to shorten the service life of the machine tool, so it is not appropriate to use the method of stopping.
4.2 Hardware configuration
Quantitative filling machine using Mitsubishi 001 CPU and OD70 positioning module to realize the bottle screw servo motor motion control. OD70 is used in the multi-axis system does not require complex control, there are two types of control: speed control and position control, through the output of pulses to achieve control. Various parameters and data are input by the OD70, and the PLCCPU is used to execute the control to realize complex positioning control. The signal collected by the sensor used to count the bottle position is used as the PLC's input; the PLC's output module connects the contactor of the servo motor of the bottle-splitting screw and each actuator; meanwhile, the servo amplifier of the servo motor is connected to the OD70 module.
4.3 Program design
The PLC control system program is written by GXDeveloper software and OD70 utility package (GXConfigurator-PT). The utility package is used to make initialization settings, auto refresh settings and monitoring/testing of the motor shaft. The initialization setup mainly includes the setting of parameters, manual operation and positioning data, while the automatic refresh setup displays the current advance feed value of the axis, the current speed, and the running status of the axis. The positioning control program of the motor axis includes: parameter setting program, PLCREADY signal ON program (initialization program), OPR request OFF program, axis positioning control program, positioning control start program, speed change program, restart program, error reset program and stop program. Among them, parameter setting is done by GXConfigurator-PT.
5 Summary
Through debugging this bottle feeding control method can achieve the filling requirements of this filling machine. The overall control and realization of the weighing and filling machine is very complex, and the various parts, from bottle feeding, filling and weighing to corking and discharging, are coordinated with each other and work together to maintain the stable operation of the filling machine. The deceleration method of bottle feeding adopted can effectively reduce the impact of the filling machine, and the use of PIC to control the movement of the bottle feeding mechanism enables the subsequent process to be completed smoothly. The good realization of the bottle feeding control is the basis for the realization of the subsequent process, and the realization of the subsequent process also puts forward the requirements of the bottle feeding control. As long as in the analysis of all the functions to be realized by the filling machine, as well as the possible problems that may arise after the specific bottle feeding control processing.