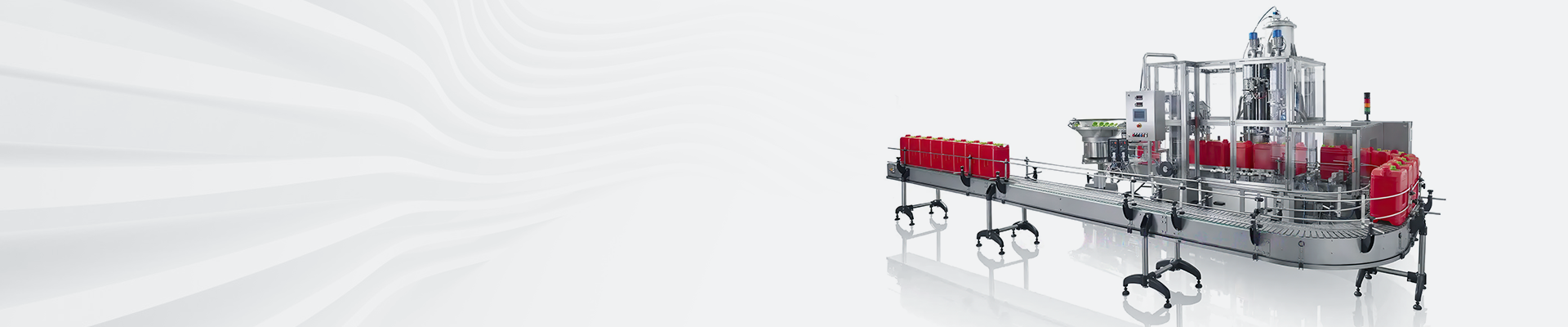
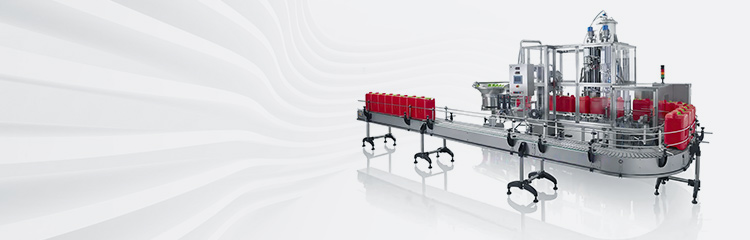

Summary:The liquid filling machine mainly consists of empty barrel conveying, filling machinery, inkjet printer and palletizer. It is composed of No. 1 filling station and No. 2 filling station. The whole process only requires manual loading and pressing of the barrel. Covers, from positioning, barrel feeding, filling, weighing and palletizing, are all completed automatically.
1.1 Equipment operation principle
Lubricating oil plant 200L1 machine mainly consists of empty barrel conveying, filling machinery, spraying machine and palletizer, filling machine consists of two parts, No. 1 filling station and No. 2 filling station, the whole process is only manual barrel and cap, from positioning, feeding barrels, filling, weighing and palletizing are all done automatically.
1.2 Equipment condition
200L-1 weighing and filling machine is one of the key equipments for vat packing in the packing workshop of the lubricating oil plant, which is mainly used for filling industrial oil. Due to the equipment is always in full load operation, the metering filling machine nozzle control part of the seal wear, the program part is not perfect, the delay time is not appropriate, the oil pressure is too large when the filling nozzle is not closed in time, resulting in the emergence of oil; palletizing part of the parts of the wear and tear is serious, mechanical fatigue, resulting in wear and tear of the track chain pull off, the frequency converter is burned out, palletizing warehouse deformation and other failures have occurred many times; the weighing control system is a monolithic control, part of the control components have been discontinued. The weighing control system is a microcontroller, some control components have been discontinued, and the control impulse is large, the buffer effect is not obvious after parameter adjustment, and the measurement error is also large. For this reason, with the consent of the lubricating oil factory, finally decided to 200L-1 filling system transformation.
2 transformation method and realization process
2.1 mechanical part of the transformation removal
Lubricant factory 200L-1 automatic filling machine palletizer originally used an independent control system, palletizing part of the main by the trolley, pallet bin, heavy barrels conveyor several parts. The trolley is under heavy load for a long time, which generates mechanical fatigue, resulting in track wear, chain breakage, inverter burnout, palletizing bin deformation and other faults occurring many times, which can not guarantee the equipment's "long, full, safe, stable and excellent" operation. Moreover, the maintenance quantity is large and the consumables are large. Therefore, it is decided to dismantle the palletizing part and design and process the transformation separately. The specific transformation is as follows:
1) In order to ensure the stable operation of the whole filling line. Remove the original heavy barrel conveying part of the roller, replaced by a bilateral free roller without power conveying, mainly by gravity slope down, reducing the control point, saving energy, reducing maintenance;
2) Keep the original diverter, reduce one heavy barrel conveying motor in this section, and only keep 1 motor as heavy barrel conveying;
3) Separate design and processing of coding conveyor heavy barrel conveyor belt, requiring the use of power rollers, bilateral chain drive;
4) the whole set of filling machinery transmission part according to the spray code power conveyor part, heavy barrel diverter part, heavy barrel conveying part of the arrangement of the assembly, the requirements of the heavy barrel diverter part of the exit to the heavy barrel conveying part of the adjustment of 3 ° slope, and the rest for the level;
5) in the front section of the spray code conveyor to be added to the stacking signal, remove the original palletizing control cabinet, will be transformed into the control cabinet of the filling machine control section added to the original metering filling machine PLC to make the appropriate program changes, and then the corresponding processing; 6 in the original filling machine to remove, retaining the original mounting bracket, the installation of a set of Taiwan's maximum load of 300kg, the accuracy of +0.15%, the display of the smallest graduation value of 0.1 kg, allowing an instantaneous impact load of 350kg 2 sets of electronic scales, and is equipped with weighing display controller 2 sets; in the original filling nozzle into the oil pipeline to add 2 sets of material control valves (fine irrigation and coarse irrigation requirements of integrated control) to remove the transformation of the 200L-1 "filling production line).
2.2 Control part of the transformation
The 200L-1 filling system adopts Mitsubishi PLC, model FXIN-60MR-001. Since the palletizer was removed, it was necessary to solve the operating conditions of the whole line. On the basis of the original control of the external wiring and program for the corresponding transformation, and debugging accordingly.
Firstly, 2 CB920X dosage controllers were added to the electronic scale part, and the internal parameters were debugged and set up, and it was required to:
1 set the target quality;
2 set the coarse measurement;
3 set the amount of overshoot;
4) Calibrate the signal sensitivity and connect to the corresponding terminal of PLC.
Secondly, in the addition of 2 sets of material control valve for the corresponding control program, the requirements of the weighing instrument to start, the coarse filling valve and fine filling valve open at the same time, when the meter display reaches (the target value is displayed for the value of coarse metering), the coarse filling valve is closed to reach (the target value is displayed for the value of the amount of overshoot) when the valve is closed to the fine filling, the amount of overshoot for the amount of auto-corrections. Maintain the original filling nozzle control structure, external addition of 2 sets of material control signals, with coarse and fine filling signals at the same time to control the filling nozzle, material control valve, so that the filling nozzle can be realized to switch the double insurance, even if there are problems with the filling nozzle structure, the material control valve will be dealt with accordingly, and will not be bubbling oil. This completely solves the running phenomenon caused by abnormal operation and holding pressure.
Finally, the palletizing part is dismantled and replaced by bilateral free rollers without power conveyor, which slides down the slope by the gravity of the heavy drums themselves until the heavy drum stacking area, which can store up to 12 drums (photoelectric detection), and when the heavy drum stacking area is enough to store 4 drums, the car can be moved at one time with the drum lifter. If the heavy barrel stacking area is more than 8 barrels (photoelectric detection) or more, the heavy barrel storage area will sound and light alarm, prompting the forklift to deal with the heavy barrel stacking work in a timely manner, if not dealt with in a timely manner, when the stacking reaches 12 barrels, the whole line alarm, the whole line stops. Subsequently, according to the transformation requirements and control ideas for system debugging, so that the whole filling production line can run smoothly.
3 after the transformation of the equipment running process
When the operator closes the main circuit, in the air pressure to reach the calibration value, press the automatic operation button, at this time, if there is no fault prompted by the operation indicator light, the equipment began to run automatically. Manually push the barrel onto the belt conveyor, if the detection switch is not blocked continuously at the same time, the belt conveyor will continuously convey the barrel to the filling unit. The belt conveyor stops running after detecting a buildup of empty drums and resumes lifting after the buildup is lifted.
The filling fork is set to release pails after the detection switch is not blocked from light, and returns to the position after blocking from light. The filling conveyor stops after the detection of the filling station is blocked, the clamping cylinder moves and starts the mouth-seeking motor, and the mouth-seeking starts. After the pre-searching detection is closed, the pre-searching cylinder moves, and the searching motor stops after a signal is detected in the searching position, and the filling head is lowered. After the filling head is lowered to the low position, reset the small gripper cylinder and start filling. After the filling is completed, if the capping work detects light transmission, then release the heavy drum and start repeating the above process. Heavy barrels out of the filling machine after the manual screw cap, and then after the spray code conveyor spray code; spray code after the heavy barrels into the lane machine to detect the first switch is blocked to start the lane machine, when the heavy barrels touch the toggle switch after the lane machine stops, the heavy barrels into the heavy barrels conveyor free area stacking, waiting for the forklift bucket lifting lift away.
4 Conclusion
The transformation of a total of three parts of the transformation, first of all, the removal of the highest failure, the largest consumables, maintenance of the most time-consuming and labor-intensive regional palletizer; secondly, completely solved the problem of oil and oil leakage of the filling machine, to achieve the production of safe and environmentally friendly concepts; and finally solved the electronic scales are not allowed to measure the amount of impulsive and other reasons for the failure of the impulsive and too large. This transformation reduces 1 control gauge, 36 control points and 4 motors; the reduction of control points saves energy and wearing parts, and greatly reduces the maintenance workload.