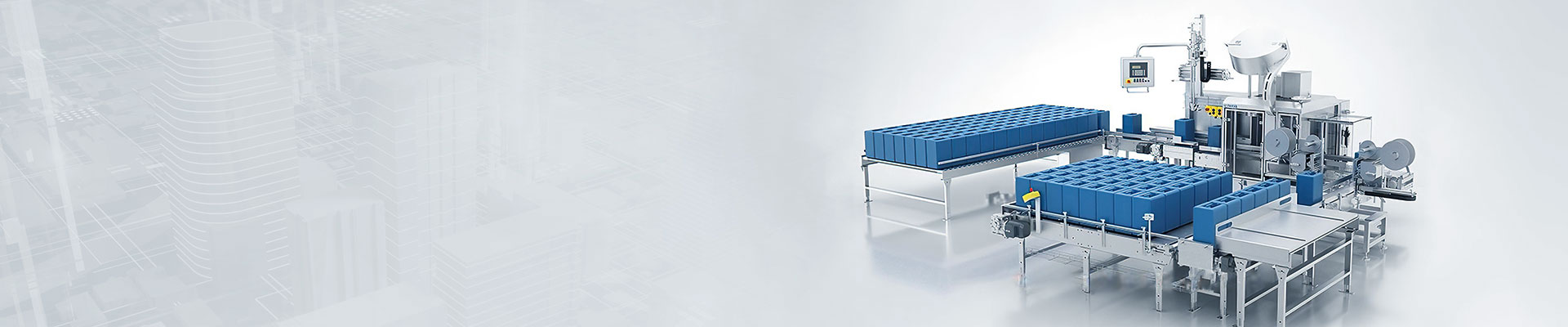
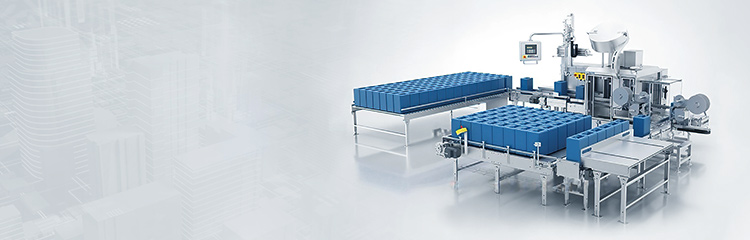
The weighing and filling machine integrates computer technology, automatic control, communication technology and weighing technology into one, and adopts programming software and field equipment library in accordance with IEC-1131 international standard, providing continuous control, sequential control and high-level language. The field device library provides a large number of commonly used field device information and function blocks, which can greatly simplify the configuration work and shorten the engineering cycle. SCL can be used to program user function blocks, using the IEC-1131 standard, the function blocks generated by SCL can be called many times in the CFC. The user can program the mathematical model of the process and the optimal control strategy into function blocks with SCL and download them directly into the controller. In this way, the optimized control of the process can be fully realized.

Weighing and Filling machine selects high-precision, reasonable range weighing module and filling actuator to start/stop control of discharging, which is transmitted into PLC through weighing instrument TR700. Through the cooperation of PLC and TR700, servo controller controls stepping motors to run to the specified station precisely and unload accurately, and the filling production line is set up with interlocking in the program to ensure the moving/unloading mechanism operates orderly and reliably when filling. The interlock is set in the program to ensure that the moving/unloading mechanism operates orderly and reliably during filling. For the convenience of actual operation and maintenance, under the manual operation mode, personnel can operate each mechanism on the site through the lighted operation buttons on the stainless steel analog screen on the surface of the controller cabinet and observe the equipment operation intuitively.
Automatic filling machine from the HPS installed on the touch screen through the multi-material function, you can complete the site filling control and weight collection, with production monitoring, filling management (confidentiality), batch statistics, alarm prompts and reports to print a wealth of functions, through the supporting communication interface can also be related to the production information uploaded to the data server or ERP, to realize the sharing of information.
Basic parameters:
Maximum weighing capacity: 1200kg
Minimum Sensitivity: 0.2kg
Filling error: ±0.2-0.5kg
Filling speed: about 50-80 barrels/hour
Control mode: 2-speed control
Filling method: Insertion, liquid level up
Gun head line: Teflon gun head, valve + Teflon hose
Structure material: host SUS304 stainless steel, conveying palletizing carbon steel anticorrosion paint.
Weighing platform size: 1200×1200mm (304 stainless steel power raceway)
Empty barrel raceway: 1200mm × 2500mm (304 stainless steel power raceway) with another 1200mm slope without power roller
Heavy drum raceway: 1200mm×2500mm (304 stainless steel power raceway, 2 sets)
Separate barrel device: for 200L barrels, carbon steel anticorrosive paint structure, 304 stainless steel raceway.
Palletizing equipment: pan-transfer type, suitable for pallets 1200×1200×140mm, including supplying pallets, palletizing, and lower pallet conveying.
Pipe pressure: 0.2-0.6MPa (related to material properties).
Material interface: DN40 flange connector 4, according to the user to provide interface standards
Air Connection: User supplied 12mm air hose connector for quick coupling connection
Power supply: AC220/50Hz (user-supplied to one side of the machine)
Using air source: 0.4-0.8Mpa (provided by the user to the side of the machine)
Use temperature: -10℃-50℃
Base condition: Ammonia solution flat solid concrete floor, concrete thickness should be more than 10cm.
Optional models: standard, explosion-proof filling