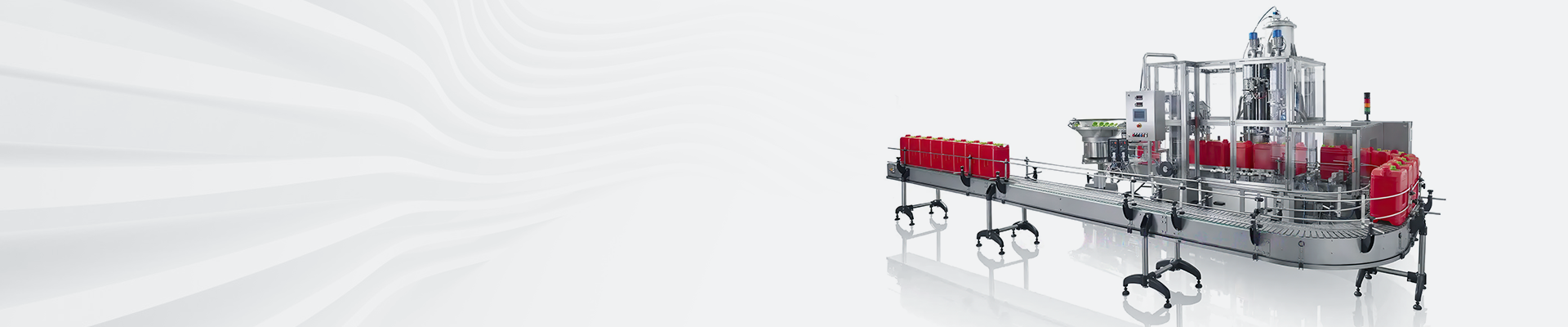
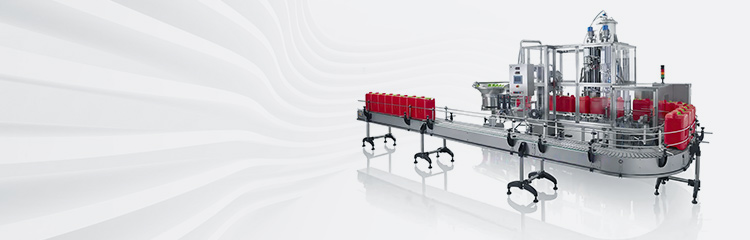

Summary:The liquid filling machine uses PLC to accurately calculate the filling of the solution and achieve real-time control. The speed of the frequency converter is controlled by the size of the received analog signal to change the feed flow rate.
In recent years, the rapid development of China's industry has led to rising labor costs, which has led to the imminent need for automation upgrading and transformation of the labor-intensive manufacturing industry. This paper develops a set of washing, filling and spinning three-in-one weighing and filling machine based on pneumatic drive, frequency conversion transmission, mechanical transmission technology, with PLC control technology as the core, which can realize automatic cleaning, filling, capping and other processes, reduce the demand for general labor, improve labor productivity, and increase the benefits for the enterprise.
The adjustment of the filling volume of the automatic filling machine is decided by the user according to the volume or weight of the material to be filled, because the specific gravity of the material is different, so the data in the loading counter is different. By adjusting the program control switch, it can be adjusted to the user's required filling volume and precision. According to the different principles of the implementation of the basic functions of filling and dosing, there can be the following three different types of packaging forms: First, the first filling and then dosing. Currently in use filling valve is in the final stage of filling through the fixed level (level sensor or exhaust pipe) indirect measurement of quantitative, this filling is commonly used in aerated beverage packaging (isobaric filling). When the cylinder moves forward, pulling the piston backward, the front cavity of the cylinder produces negative pressure. The material in the supply barrel is pressed into the feeding tube by the atmospheric pressure, and enters into the feeding tube through the check valve of the inlet and outlet. Weighing and filling machine refers to the process of automatically loading liquid substances of set weight into containers. It is a high-tech product integrating machine vision, automatic control, metering detection and electromechanical-optical integration technology, and consists of functional modules such as automatic cap opening, metering filling, automatic cap closing, automatic capping, automatic labeling, automatic palletizing, etc., among which automatic cap opening, automatic metering filling, automatic cap closing, and automatic capping all adopt vision addressing The automatic cap opening, automatic metering and filling, automatic cap closing and automatic cap pressing all adopt visual addressing technology. Users can choose the above function modules according to their needs to form a fully automatic filling system with visual addressing.
1 work requirements
The process of quantitative filling machine is as follows: after placing the filling barrel on the conveyor belt, the conveyor motor will transfer it to the filling position; at this time, the proximity switch arranged in the filling position automatically senses and transmits the sensing signal to the PLC; the PLC controls the conveyor motor to stop rotating, and at the same time, it controls the lifting cylinder to drive the roller arm to rise up, and then the filling barrel will be moved to the position of the filling gun; at this time, the photoelectric sensor located in the port of the filling gun automatically senses the position of the filling barrel, and then it automatically senses the position of the filling barrel. At this time, the photoelectric sensor located in the port of the filling gun automatically senses the position of the filling barrel and transmits the signal to the PLC; when the filling barrel reaches the predetermined position, the PLC controls the synchronous motor to stop rotating, and at the same time, the suction cap device starts to suck the cap away; then the filling gun begins to fill the liquid in the filling barrel, and the weighing sensor transmits the weight signal of the liquid in the barrel to the PLC; when the predetermined weight is reached, the PLC controls the filling gun to stop filling, and the suction cap device automatically seals the cap on, and starts the conveyor motor to start the filling gun. When the predetermined weight is reached, the PLC controls the filling gun to stop filling, the cap suction device automatically seals the cap, and the conveyor motor is started to transport the filling barrel away.
The working task of this filling machine is to realize the full automation of cleaning, filling, capping and other processes for beverage bottles. It adopts two-speed filling mode with liquid level up or liquid level down and weighing controller, which is suitable for many kinds of liquid materials. Uniquely designed nozzle device is easy to operate, filling fast and accurate, and maximize the prevention of residual liquid dripping leakage at the end of filling; filling operation is simple, the filling process does not need to be peeled, the device can be automatically peeled and weighed.
Liquid filling machine to SCADA software as a platform, the secondary development of filling functions on this platform, to achieve intelligent filling process management and control. Automatic filling machine and traditional information management is different, the function around the filling and other high degree of automation equipment, the establishment of services to automate the control process, the use of computer recognition technology, printing technology, automatic control technology, information technology, the formation of an intelligent filling system to meet the customer for the filling process automation, information technology, intelligent requirements.
2 overall design program
This metering and filling machine is mainly composed of bottle feeding and transferring mechanism, bottle washing machine, filling machinery, capping machine, star wheel transferring mechanism, etc. The process flow is bottle feeding - cleaning - filling - capping - bottle. The mechanical device is used to rotate the infusion bottles at high speed and stop sharply, and then the reflector is matched with the video camera to capture a continuous sequence of filling images without perspective deviation. First, the mechanical device accelerates the bottle into the rotating area, and then stops the acceleration when the bottle is about to leave the rotating area, and the bottle rotates freely (reducing air bubbles caused by oscillation). When the infusion bottle "completely into the emergency stop area, the light detector will control the mechanical device to make the infusion bottle emergency stop, the bottle of liquid due to inertia will continue to rotate, at this time the camera through the reflector began to shoot the infusion bottle" continuous sequence of reflectors rotate accordingly at a certain angle, to ensure that the camera can track and capture the sequence of images of the infusion bottle. (Note that at this time, due to the need for a certain amount of transmission time, the infusion bottle force-1 has not yet fully entered the emergency stop area). Infusion bottle" continues to transmit forward, the reflector also continues to make the corresponding rotation, until the infusion bottle n-1 completely into the emergency stop area
WinCC-flexible, the latest product of Auto Filler, is an HMI-oriented configuration liquid interface with better openness, scalability and compatibility, which improves the configuration efficiency of the user interface and brings new creative concepts of device-level automation. In SIMATIC products can be used to configure all WindowsCE-based operator panels, from the smallest panels to touch control panels, multifunction panels. Due to all these advantages, the configuration of touch panels is designed in conjunction with the control core of the PLC, the CPU313C from the SIMATICS 7-300 series. Realize the design of industrial automation. The automatic filling machine has some good features including manual operation, fault alarms, recipe management, trend charts (display and analysis) and print results. The specific workflow of this 3-in-1 liquid filling machine is as follows:
(1) The filling machine is turned on, the cleaning machine, filling machine, capping machine, etc. are initialized, each sensor part is self-tested, each cylinder is tested for action, and the weighing and filling machine can be started only after the initialization and testing is completed.
(2) After starting, the main motor starts to drive the star wheel, bottle washer spindle, filling machine spindle rotation, and at the same time start the capping machine spindle rotating motor, 2s after the start of the bottle chain motor, at this time the whole washing, filling and rotating three-in-one filling machine into production. Electronic scale (with RS-232/9 standard serial port) management software integrates recipe management, filling and weighing, personnel management, report generation, providing interfaces and data management, of which the software is the most critical is to solve the computer and electronic scale data communication. It mainly includes the following modules. Recipe Setting Module: It is to complete the setting of the raw materials selected in the recipe and the standard and error weights of the raw materials, as well as to stipulate the scale number for weighing the selected raw materials. This module can realize the confidentiality of the formula data; after the workers operating in the filling site choose the formula and the number of grooves for operation, the automatic filling machine will automatically generate the data and scale number of the raw materials of the selected formula in sequence, and the workers will put the raw materials to be weighed on the designated electronic scale according to the prompts of the computer, at this time, the data of the weight of the raw materials will be transmitted to the computer through the computer's serial port at once, and the computer can receive the weight data of the raw materials immediately, and analyze and compare the data, and then the computer can analyze and compare the data. The computer can immediately receive the weight data of raw materials and analyze and compare them, if the weighed weight meets the requirements (actual weight - standard weight ≤ error weight), the automatic filling machine will allow workers to carry out the next operation and save the operation data in the database, otherwise, the computer will alarm and prompt the operator until the weight is adjusted correctly. This module can monitor the workers to standardize the operation and ensure that the measured data of the weighed raw materials are accurate.
(3) Empty plastic bottles are fed into the star wheel by the bottle feeding conveyor, and the star wheel transfers the empty plastic bottles to the No.1 washing machine through the crescent-shaped track. There are 6 stations on the washing machine: upper bottle station, sterilized water washing station, sterilized water drip-drying station, clear water washing station, clear water drip-drying station, and lower bottle station. When the empty plastic bottle is fed into the bottle washing clamp by the star wheel, the bottle washing clamp rotates with the bottle washing machine, when the bottle washing clamp is separated from the bottle clamping guide rail, it automatically clamps the empty bottle and inverts the empty bottle along the S-shape bottle guide rail of the bottle washing machine, and the mouth of the empty bottle is aligned with the mouth of the bottle washing valve, and then the bottle washing pump, disinfectant water washing valve and fresh water washing valve are opened, realizing the first time of washing the plastic bottles. Plastic bottles through the star wheel transfer to the second cleaning machine, cleaning process with the first cleaning, to achieve the second cleaning.
(4)The cleaned plastic bottles are transferred to the filling machine by the star wheel, and the feeding valve, return pump, exhaust valve, return valve, feeding CIP valve, return CIP valve are opened on the filling machine to fill the drinks or other beverages, and at the same time, the exhaust valve is opened on the top of the filling barrel of the filling machine, to avoid causing too high air pressure in the filling barrel.
(5) The filled plastic bottles are transferred to the capping machine by the star wheel, at the same time, the cap releasing cylinder releases the corresponding plastic caps to the capping machine according to the signal of the detection switch, and the capping machine completes the process of tightening the caps by suctioning and screwing the caps.
(6) After screwing the bottle cap is transferred to the bottle discharge chain by the star wheel.
(7) During the operation of the filling machine, the control to realize the washing and filling and spinning workflow cycle work, until the manual stop weighing and filling machine work.
3 main peripheral hardware design
This liquid filling machine uses PLC to achieve real-time control of the solution after accurate calculation, through the size of the received analog signal to control the speed of the inverter to change the feed flow rate to meet the process requirements, which solves the problem of filling ratio is not easy to control. The real-time process flow and real-time process parameter display are accomplished through programming, and the production parameters are monitored by a large-screen LCD monitor, and the feeding and discharging of materials are monitored on a single screen, with real-time data query, historical data query, real-time curve query, historical curve query, and equipment alarm query, etc. The monitoring equipment is placed in the duty room where the operator operates and monitors the equipment, and real-time alarm functions are accomplished by programming through configuration software. The real-time alarm function is programmed by the configuration software, so that any equipment failure is immediately displayed on the computer screen, and the maintenance personnel can quickly locate and remove the failure in time through the displayed failure conditions.
3.1 Bottle washing clamp
Its working principle is: when the open clip roller is not out of the open clip guide, open clip roller on the cylindrical pin through the oval groove in the forward movement driven by the open clip spindle rotating clockwise, at this time the bottle clamping block is open, the plastic bottles can be passed from the star wheel into the bottle washer clamps; bottle washer clamps in the track guide block under the traction out of the open clip guide, the open clip on the cylindrical pin through the elliptical groove in the backward movement driven by the open clip rotary axis rotating counterclockwise, the bottle washer clamps, the bottle washer clamping, the bottle washer clamps, the bottle washer clamps, the bottle washer clamps. At this time, the bottle clamping block is clamped, and the bottle washing clamp completes the clamping of plastic bottles. The mounting block is used to fix the bottle washer clamp on the washing machine, and the overturning shaft is used to realize the overturning of plastic bottles. The whole automatic filling system consists of industrial control machine, PLC, weighing terminal (LYNX), frequency converter, vibration motor, mixer, load cell and other parts. The upper computer provides human-computer interaction interface, completes the control information input, data management, data display, storage, statistics and reports and other functions, the upper computer pro-IPC810I controller, its main work is: through the host computer keyboard input the weight of the ingredients, according to the filling ratio of the liquid to generate a variety of liquids in the weight of the liquid, through the communication to the PLC. metering filling device filling process, dynamic real-time monitoring, regularly collect the weight of each liquid, through the communication to the PLC, and the weight of the liquid. Dynamic real-time monitoring, regular collection of the slave machine sent to the weight of each liquid, the cumulative amount of material, the weight of each liquid given the value of information in the CRT ± display, and the formation of a database file, when necessary, to print out a variety of management documents and reports. Real-time communication with the host computer to ensure the consistency of the data displayed on the interface with the actual data on the site, the operator in the host computer issued by the operating commands and set parameters can be sent to the PLC in real time to perform the main work of the PLC: receive the commands and data sent by the host computer, through the frequency converter to control the vibration motor start-stop, fast and slow, detection and control of the system's other switching, real-time collection of the weight of each material signal and with the given value of liquid weight, and so on. The weight signal of each material is collected in real time and compared with the given signal to decide the next control program, and at the same time, the weight signal is transmitted to the upper computer.
Structural principle of filling mechanical valve: when the plastic bottle is clamped by the bottle holder on the filling machine and rotated to the filling area with the guide rail, the mouth of the plastic bottle enters into the valve head of the filling mechanical valve, the connecting tube produces upward movement in the valve cavity under the action of the guide sleeve, and the sealing ring is moved upward to realize filling.
The structural principle of the capping head: when the bottle cap falls into the capping head from the lower cap groove, at this time, the capping head moves downward due to the action of the capping cam to snap the bottle cap into the capping mouth, and at the same time, the capping head realizes capping under the driving of the capping arm and capping turntable. The guide bar is used to push down the empty cap.
3.2 Lower cap groove
The structural principle of the lower cap slot: the cap falls into the lower cap slot from the cap manager, when the top face of the cap is facing the groove wheel, this is the positive cap direction, the cap will fall through the groove wheel under the action of self-weight, when there is a bottle detecting element detects that there is a bottle over, the gear lever will be released under the drive of the cap cylinder to put the cap into the spinning head; acetone cyanohydrin metering and explosion-proof filling machine when the bottle cap is reversed against the groove wheel, for the reverse cap, the bottle cap will be hung up by the groove wheel, this time At this time, the anti-cap detecting element sends out a signal, and the anti-cap rejecting cylinder drives the push cap plate to reject the cap out of the lower cap slot.
3.3 Pneumatic control circuit design
This automatic filling machine bottle washer on the bottle washing valve opening size, filling CIP valve, reflux tank, water lubrication valve, etc. need to be adjusted according to the number of empty bottles transmitted over the conveyor chain, taking into account the application of the environment, productivity and structural design of the pneumatic drive to complete the part of the work, and its control is mainly used electromagnetic directional valves and single-acting cylinders to control the valve opening size. In the conveyor chain on the bottle and bottle blocking, capping machine on the release of the cap and anti-cap rejection, etc. are used electromagnetic directional valve, one-way throttle valve and double-acting cylinders to complete.
4 PLC development and design
Metering filling machine using PLC as the central controller to complete the pneumatic drive, frequency transmission, out of the bottle to release the cap and other work control requirements, a total of 49 input signals, 30 output signals for the control of the electromagnetic reversing valve, motor, buttons and indicators. In the production activities of various industries, the most commonly used way is to start filling, the use of flow meter flow accumulation controller to control the feed valve, according to the ratio to determine the amount of material added, and finally complete the filling production.
5 Conclusion
This automatic filling machine application of pneumatic technology, mechanical transmission and other technologies, Siemens PLC liquid filling machine as the central controller, the development of washing, filling and spinning three-in-one liquid filling machine, programmable controller PLC as the core, in the injection of mixed liquids station to control the two raw material tanks (A tank and B tank) corresponding to the pumps to the mixing tank to refill the raw materials (the specific recipe in the filling system by the touch screen to set the recipe parameters) ). The two raw material tanks are equipped with level switches and level sensors, which are used to detect the amount of liquid in the raw material tanks and the electrical protection of the raw material injection pumps. The mixing tank is equipped with a liquid level sensor to control the injection volume of tanks A and B according to the liquid level value read by the AD module, and to meet the recipe setting requirements of the filling machine. After the two raw materials are injected, the mixer mixes the two liquids fully. After the mixing is completed, open the discharge solenoid valve to inject the mixed liquid into the heating tank for processing (heating), when the temperature reaches the set point, the processing step is completed, at this time, the bottle filling mechanism begins to bottle on the conveyor belt, bottles on the conveyor belt through the encoder of high resolution positioning control, bottles arrive at the refilling position when the conveyor belt to stop running. When the bottle reaches the filling position, the conveyor belt stops running. The solenoid valve of the heating tank opens, and the liquid is injected into the bottle by the filling nozzle through the metering, and then sent to the capping position through the conveyor belt after the set amount is injected. The cap will be sent to the bottle to the position by the capping mechanism and then cap the bottle, after the completion of the conveyor belt will be filled with liquid and capped bottles sent to the finished product area. At this point, the entire automatic filling machine all processes are over.