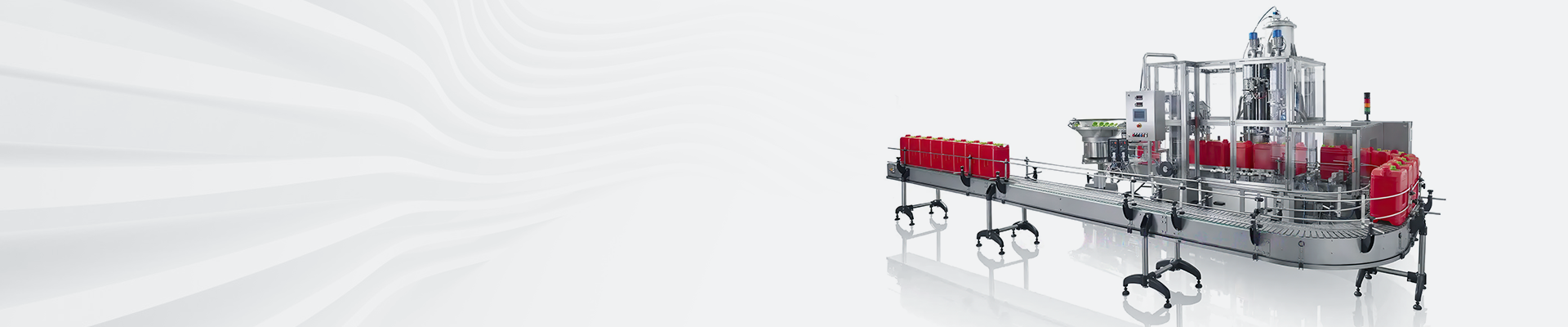
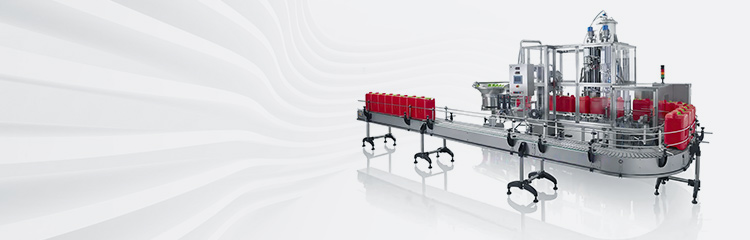
摘要:液体灌装机采用PLC对溶液的灌装进行精确计算后实现实时控制的,通过接收的模拟信号大小来控制变频器的转速从而改变进料流量。
0引言
近年来,我国工业的快速发展使得劳动力成本不断上升,这就导致劳动密集型的制造业对于自动化升级改造的需求迫在眉睫。本文开发了一套基于气压驱动、变频传送、机械传动技术,以PLC控制技术为核心的洗灌旋三合一称重灌装机,可以实现自动清洗、灌装、旋盖等工序,减少了企业对普工的需求,提高了劳动生产效率,为企业增加了效益。
自动灌装机灌装量的调整是用户根据所需灌装物料的容积或重量来决定的,因物料的比重有所差别,所以在装量计数器的数据有所差别。通过调节程控开关,可调整至用户所需的灌装量及精度。按照灌装和定量基本功能实施的不同原理,可以有以下三类不同包装形式:一是先灌装后定量。目前在用的灌装阀就是在灌装的最后阶段通过定液位(液位传感器或排气管)间接计量定量,此种灌装常用于含气饮料包装(等压灌装)。当气缸向前运动时,拉动活塞向后,料缸前腔产生负压。供料桶内的物料被大气压力压入进料管,通过进出料的单向阀进入料管。称重灌装机是指自动地将设定重量的液态物质装入容器的过程,集成了机器视觉、自动控制、计量检测及机电光一体化技术的高科技产品,由自动开盖、计量灌装、自动关盖、自动压盖、自动贴标、自动码垛等功能模块组成,其中自动开盖、自动计量灌装、自动关盖、自动压盖均采用了视觉寻址技术。用户可根据需要选择上述功能模块,组成视觉寻址全自动灌装系统。
1工作要求
定量灌装机的工艺过程为:将灌装桶放置于输送带后,由输送电机将其传送至灌装位置;此时布置于灌装位置的接近开关自动感应,并将感应信号传给PLC;PLC控制输送电机停止转动,同时控制升降气缸带动滚轮臂上升,将灌装桶移动至灌装枪位置;此时,位于灌装枪端口的光电传感器自动感应灌装桶的位置,并将信号传给PLC;当灌装桶到达预定位置后,PLC控制同步电机停止转动,同时吸盖装置启动将盖子吸走;然后灌装枪开始往灌装桶中灌装液体,由称重传感器将桶中液体的重量信号传给PLC;当达到预定重量时,PLC控制灌装枪停止灌装,吸盖装置自动将盖子封上,启动输送电机,将灌装桶运走。
本灌装机的工作任务是实现对饮料瓶进行清洗、灌装、旋盖等工艺的全自动化。采用液面上或液面下双速灌装方式,采用称重控制器, 适用于多种液体物料。设计独特的喷咀装置易于操作,灌注快速、精确高,最大限度地防止灌注完毕时残液滴漏;灌装操作简单,灌装过程无需人为去皮,装置可自动去皮称量。
液体灌装机以SCADA软件为平台,在此平台上进行灌装功能的二次开发,实现智能灌装过程管理控制。自动灌装机与传统的信息管理不同,功能围绕灌装等自动化程度高的设备,建立服务于自动化控制过程,使用计算机识别技术,打印技术,自动控制技术,信息技术,形成智能填充系统,满足客户对于灌装过程自动化,信息化,智能化的要求。
2整体设计方案
本计量灌装机主要由送瓶传送机构、洗瓶机、灌装机械、旋盖机、星轮传送机构等构成,工艺流程为送瓶—清洗—灌装—旋盖—出瓶。采用机械装置对输液瓶进行高速旋转-急停,然后由反光镜与摄像机相配合拍摄连续无视角偏差的序列灌装图像。首先由机械装置使进入旋转区的输液瓶加速旋转,在输液瓶即将离开旋转区域时停止加速,输液瓶作自由旋转(减少因振荡带来的气泡)。当输液瓶”完全进入急停区时,灯检机将控制机械装置使输液瓶急停,瓶内液体由于惯性作用将继续旋转,此时摄像机通过反光镜开始拍摄输液瓶”的连续序反光镜相应旋转一定角度,确保摄像机能跟踪捕捉到输液瓶的序列图像。 (注意此时由于需要一定的传送时间,输液瓶力-1还未完全进入急停区域)。输液瓶”继续向前传送,反光镜也继续作相应转动,直至输液瓶n-1完全进入急停区域,此时反光镜立即返回灌装机所示位置,开始跟踪下一个输液瓶。而同时也完成了对输液瓶的连续序列图像获取。
自动填充机的最新产品WinCC-flexible是一种面向HMI的组态液界面,具有更好的开放性,可扩展性和兼容性,提高了使用者界面的配置效率,带来了新的创造性的设备级自动化的概念。在SIMATIC产品中,可用于配置所有的基于WindowsCE的操作面板,从最小面板到触摸控制面板,多功能面板。由于上述种种优点,结合PLC的控制核心,来自SIMATICS7-300系列中的CPU313C来设计的触摸屏的配置。实现工业自动化的设计。自动灌装机具有一些良好的功能,包括手动操作,故障报警,配方管理,趋势图(显示及分析)和打印结果。该三合一液体灌装机的具体工作流程如下:
(1)灌装机开机,清洗机、灌装机、旋盖机等进行初始化,各传感器部件进行自检,各气缸进行测试动作,初始化检测完毕后,方可启动称重灌装机。
(2)启动后,主电机启动带动星轮、洗瓶机主轴、灌装机主轴旋转,同时启动旋盖机主轴旋转电机,2s后启动出瓶链电机,此时整台洗灌旋三合一灌装机进入生产状态。电子秤(具有RS-232/9标准串口)管理软件集成了配方管理、灌装称重、人员管理、报表生成、提供接口和数据管理,其中软件最关键的是解决计算机与电子秤的数据通信。主要包括以下模块。配方设置模块:是完成对配方中所选的原料及原料的标准重量与误差重量进行设置以及规定所选原料称重的秤号。该模块可以实现配方数据的保密性;在灌装现场操作的工人选择好操作的配方和槽数后,自动灌装机会依次自动产生所选配方的原料的数据和秤号,工人按计算机的提示将需要称重的原料放在指定电子秤上,此时,原料重量的数据会立即通过计算机串行口传给计算机,计算机能立即接收到原料的重量数据,并进行分析比较,如果所称的重量符合要求(实际重量—标准重量≤误差重量),自动灌装机将允许工人进行下一步操作,并将操作数据保存在数据库中,否则,计算机将会报警提示操作工人,直至将重量调整正确。该模块可以监控工人规范操作,保证被称原料测量数据精确。
(3)空塑料瓶由进瓶传送带送入星轮,星轮通过月牙形的轨道将塑料空瓶传送到一号清洗机。清洗机上共有上瓶工位、消毒水洗工位、消毒水滴干工位、清水洗工位、清水滴干工位、下瓶工位6个工位。当塑料空瓶由星轮送入洗瓶夹后,洗瓶夹随着洗瓶机旋转,当洗瓶夹脱离夹瓶导轨后,自动夹紧空瓶并沿着洗瓶机的S形导瓶导轨将空瓶倒转,翻转后的空瓶瓶口对准洗瓶阀口,洗瓶水泵、消毒水洗洗瓶阀、清水洗洗瓶阀开启,实现第一次清洗塑料瓶。塑料瓶通过星轮传送到二号清洗机,清洗工序同第一次清洗,实现第二次清洗。
(4)清洗后的塑料瓶由星轮传送到灌装机,灌装机上的进料阀、回流水泵、排气阀、回流阀、进料CIP阀、回流CIP阀开启,进行饮料或其他饮料的灌装,同时灌装机灌装桶上方的排气阀开启,避免造成灌装桶内气压过高。
(5)灌装好的塑料瓶由星轮传送到旋盖机,同时放盖气缸根据检测开关的信号放相应的塑料盖到旋盖机,旋盖机通过吸盖、旋盖,完成旋紧瓶盖的工序。
(6)旋紧瓶盖后由星轮传送到出瓶链。
(7)灌装机运行期间,控制实现洗灌旋工作流程循环工作,直至人工停止称重灌装机工作。
3主要外围硬件设计
本液体灌装机采用PLC对溶液进行精确计算后实现实时控制的,通过接收的模拟信号大小来控制变频器的转速从而改变进料流量,以达到工艺要求,这样就解决了灌装比例不容易控制的问题。通过编程完成了实时工艺流程及实时工艺参数的显示,采用大屏幕液晶显示器对生产参数进行监控,进、出料都在一个画面进行监控,有实时数据査询、历史数据查询、实时曲线査询、历史曲线查询和设备报警查询等,监控设备安放在值班室操作人员进行操作、监控,通过组态软件编程完成实时报警功能,无论任何设备发生故障,都会立即显示在电脑屏幕上,维修人员通过显示的故障情况可以较快地将故障定位,并及时排除。
3.1洗瓶夹
其工作原理为:当开夹滚轮未脱离开夹导轨时,开夹滚轮上的圆柱销通过椭圆形槽中的前移运动带动开夹转轴顺时针旋转,此时夹瓶块打开,塑料瓶可由星轮传入洗瓶夹;当洗瓶夹在走轨道导块的牵动下脱离开夹导轨时,开夹滚轮上的圆柱销通过椭圆形槽中的后退运动带动开夹转轴逆时针旋转,此时夹瓶块夹紧,洗瓶夹完成夹紧塑料瓶。安装块用以将洗瓶夹固定在清洗机上,而翻转转轴用来实现塑料瓶的翻转。整个自动灌装系统由工控机、PLC、称重终端(LYNX),变频器、振动电机、混料机、称重传感器等部分组成。上位工控机提供人机交互界面,完成控制信息输入、数据管理、进行数据显示、存储、统计和报表等功能,上位机釆用IPC810I控机,它的主要工作有:通过主机键盘输入配料的重量,根据液体的灌装配比,生成各种液体的重量,通过通信传送给PLC。计量灌装装置灌装过程中,进行动态实时监视,定时收集各从机发送来的各液体重量,累计下料量,各液体重量给定值等信息,在CRT±进行显示,并形成有关的数据库文件,在需要时打印出各种管理文件和报表。与上位机实时通信,从而保证界面上显示的数据与现场实际数据的一致性,操作人员在上位机上发出的操作命令和设定参数都可以实时送到PLC上执行。PLC的主要工作有:接收上位机发送来的命令和数据,通过变频器控制振动电机启停、快慢,检测和控制系统中的其它开关量,实时收集各物料的重量信号并与给定信号比较,决定下一步的控制方案,同时将重量信号传送给上位机。
灌装机械阀的结构原理:当塑料瓶由灌装机上的托瓶装置夹住并随导轨旋转到灌装区时,塑料瓶口进入灌装机械阀阀头,连接管在导套的作用下在阀腔内产生向上运动,密封环上移,实现灌装。
旋盖头的结构原理:当瓶盖由下盖槽落入旋盖头正下方,此时旋盖头因旋盖凸轮的作用向下运动将瓶盖卡入旋盖口,同时旋盖头在旋盖臂和旋盖转盘的带动下实现旋盖。导杆用于将空瓶盖顶落。
3.2下盖槽
下盖槽的结构原理:瓶盖自理盖器落入下盖槽,当瓶盖的上顶面对着槽轮时,此为正盖向,瓶盖会在自重的作用下通过槽轮落下,当有瓶检测元件检测到有瓶过来,档杆会在放盖气缸的带动下放盖进入旋盖头;丙酮氰醇计量防爆灌装机当瓶盖反向对着槽轮时,为反盖向,瓶盖会被槽轮挂住,此时反盖检测元件发出信号,反盖剔除气缸带动推盖板将盖剔出下盖槽。
3.3气动控制回路设计
本自动灌装机洗瓶机上洗瓶阀开口大小、灌装CIP阀、回流罐、水润滑阀等需根据传送链上传送过来的空瓶数进行调节,考虑到应用环境、生产效率及结构设计上采用气压传动来完成本部分工作,其控制主要采用电磁换向阀及单作用气缸来控制阀口大小。在传送链上的阻瓶和落瓶、旋盖机上的放盖和反盖剔除等均采用电磁换向阀、单向节流阀及双作用气缸完成。
4PLC开发设计
计量灌装机采用PLC作为中央控制器,完成对气压传动、变频传送、出瓶放盖等工作的控制要求,共采用了49个输入信号,30个输出信号,用于控制电磁换向阀、电机、按钮和指示灯。在各个行业的生产活动中,最常应用的方式是在开始灌装时,使用流量计的流量累积控制器对进料阀门进行控制,根据配比确定物料的加入量,最终完成灌装生产。
5结束语
本自动灌装机应用气动技术、机械传动等技术,以西门子PLC液体灌装机为中央控制器,进行了洗灌旋三合一液体灌装机的开发,以可编程控制器PLC为核心,在注入混合液体工位上控制两个原料罐(A罐与B罐)对应的泵向搅拌罐加注原料(具体配方在灌装系统中由触摸屏来设置配方参数)。两个原料罐都装有液位开关及液位传感器,用来检测原料罐中液体量及原料注入泵电气保护。搅拌罐装有液位传感器,依据AD模块读入的液位值控制A罐与B罐的注入量,并符合灌装机配方设置要求。两种原料加注后,搅拌机对两种液体进行充分混合搅拌。搅拌完成后开启出料电磁阀向加热罐注入混合后的液体进行加工(加热),待温度达到设定置时加工步骤完成,此时,加注瓶机构开始向传输带上瓶,瓶子在传输带上通过高分辩率的编码器进行定位控制,瓶子到达加注位时传输带停止运转。加热罐出料电磁阀开启,液体经计量由加注嘴向瓶中注入设定量后经传输带送至加盖位。上盖将瓶送到位后由加盖机构再向瓶子加盖,完成后传输带将加注过液体和盖好盖的瓶送至成品区。至此,整过自动灌装机所有流程结束。