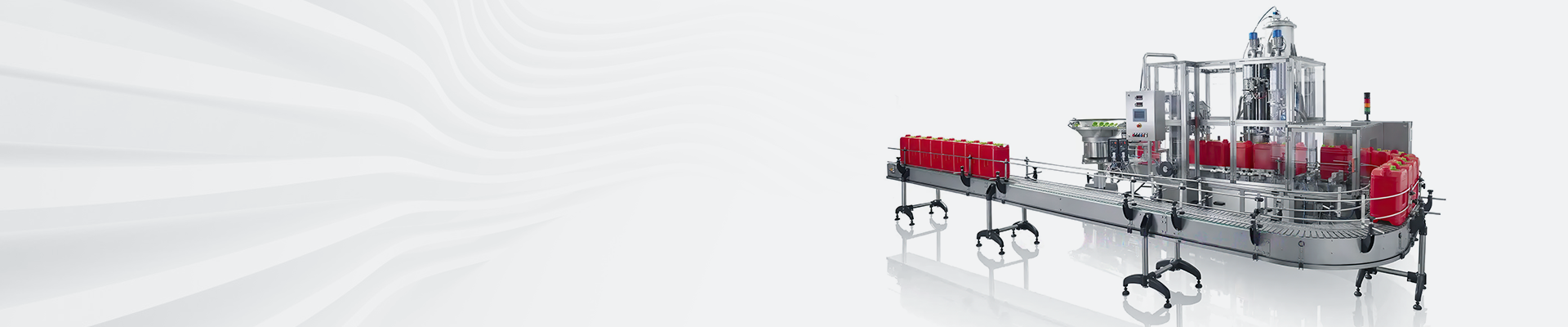
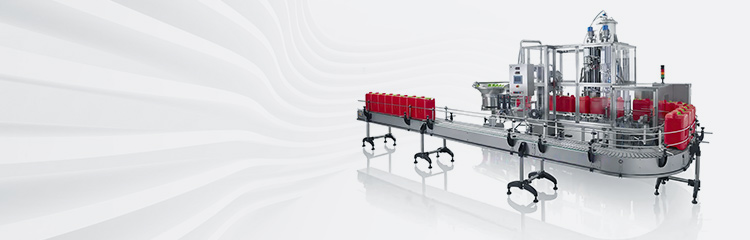

Summary:The automatic batching system is composed of 485 protocol, which outputs multi-stage control signals, directly accesses the PLC system, realizes multi-stage hot and cold temperature control, vacuum nitrogen filling, and quantitative filling control with measurable electrical signal output.
Since entering the 21st century, with the rapid development of the domestic lubricant consumption market, major domestic and foreign oil companies and local enterprises have begun to vigorously develop the business of lubricant oil products, through various means to improve product quality, reduce losses, optimize the operation, and improve corporate visibility . So as to enhance the profitability of its entire refined oil sales chain. In recent years, PetroChina Lubricants Company has built a new lubricant plant in East China, and combined with market changes have carried out several expansions and renovations in recent years in the process of designing the dosing control system, summed up the overall design ideas, here to share and discuss.
1 the main ideas of plant design
1.1 Determine the blending program
Before proceeding with the design, it is necessary to determine the blending program, because the blending program is the core content of the lubricant dosage control system, the use of different blending programs, which directly leads to the whole plant supporting the design of the content and the amount of work is different.
Lubricant dosage control system are generally modernized production mode as the goal, that is, the main production mode using automated blending. At present, the most advanced international blending method is mainly synchronous metering blending, referred to as (SMB) or pipeline online blending (referred to as ILB) based on different market objectives, using different blending methods. the working principle of the SMB is: according to the blending of the production objectives, the blending formula is automatically generated by the dosage system, the different components synchronized to enter the SMB each flow channel, the metering, through the converging pipe into the designated finished oil reaction tank. After metering, they flow into the designated finished oil reaction tank through the manifold, and the components that are not metered synchronously can also be metered individually and proportionally by the SMB and then enter the finished product tank. All the components in the blending formula enter the finished oil tank, and then the finished oil is formed by stirring uniformly.
The working principle of ILB is: according to the blending production target, the blending formula is generated automatically by the metering and dosing system, all the components in the blending formula enter into each flow channel of IB at the same time, and after being metered and stirred uniformly at the outlet of the manifold by the on-line dynamic stirrer, they can be sent to the designated finished oil tanks for storage, or they can be sent directly to the terminal equipment such as loading ships, trucks or bottling. From the working principle of SMB and ILB, it can be seen that SMB is actually only pipeline online metering and mixing, and can not be online blending of finished products, which needs to be carried out in the final blending of finished oil products in the oil product storage tanks; whereas, ILB is the real pipeline online blending, which can form qualified finished oil products after passing through the dynamic stirrer of ILB.
For small and medium-sized dosage control system, and more product varieties, production switching frequency of high working conditions, or raw material sources of quality differences in the working conditions, generally suitable for the use of SMB blending, its production is more flexible, can respond to different market needs, especially suitable for lubricating oil companies according to the needs of the consumer market to determine the production goals. As for the large-scale system, especially the production of a single species, mainly for specific customers to produce order-based product dosage control system, in the raw material source is very stable, generally more suitable for the use of ILB blending method, because the online blending method can save the oil transfer and mixing process of energy consumption, but also a large number of finished oil tanks to save the occupation of the investment at the same time, but also easy to manage.
In the lubricating oil dosage control system design, the design unit should fully understand the investor's investment intention, market objectives, production scale, oil sources, land acquisition area and other factors, so as to assist the investor to determine the core blending program, and to further determine the blending control program, master plan planning, supporting facilities in all aspects of the design program.
1.2 Auxiliary blending facilities
After determining the core blending program, should further determine the configuration of auxiliary blending facilities, so as to form a complete blending system. Auxiliary blending facilities generally include tank-type batch blending feeding system (referred to as ABB) tank mixing facilities, through the ball system and through the ball piping.
(1) tank-type batch blending feeding system (ABB) ABB in general lubricating oil feeding system is a necessary auxiliary blending facilities, its main function is to blend small quantities of finished oil, the raw material components through the blending control system generated by the formula in order to enter the blending kettle, the amount of feed through the ABB with a high-precision weighing instrument for weighing control, to ensure that the amount of each component feed to meet the blending formula requirements.
After the components are fully stirred in the ABB blending kettle to become qualified products, they can be directly transferred to the factory.
Due to the specificity of the lubricant market, the blending kettle often needs to be used to produce some high-end products or special products in small batches according to the needs of customers, and SMB and ILB are seldom used in the production of small batch of products as little as 1~2t and up to 30t, because on the one hand, switching varieties, cleaning pipelines are more time-consuming, on the one hand, they also need to set up a separate small variety of tanks, which results in a lower utilization rate of the tanks. And ABB solves the problem of small varieties of production, so its use is very wide, not only the general lubricant dosage control system are configured, and has become the main production equipment additive plant.
(2) tank mixing facilities
Lubricant oil tanks are generally set up within the stirring facilities, for the SMB, the finished product storage tanks must have stirring facilities, the purpose is to mix the various components of the oil; ILB blending of finished products in the tank should also consider setting up the churning facilities, mainly to prevent long-term storage of oil layering caused by unqualified.
The main stirring methods include: nozzle circulation stirring in the tank, agitator stirring in the tank, pneumatic pulse stirring and other three ways. The first two ways are traditional stirring methods, while the emerging pneumatic pulse mixing is mainly through the installation of the air collection plate and high-pressure injector in the tank, the purified air instantaneous high-pressure injection to the tank, through the way of the drum bubbles, driven by the tank oil up and down the flow, so as to achieve the purpose of mixing evenly. At present, pneumatic pulse mixing due to its mixing medium safety, fast mixing speed, low energy consumption, automatic control level higher gradually occupied the main market of lubricating oil mixing, the general modern dosing control system will be preferred pulse mixing as a means of production of tank mixing.
(3)Ball-through system and ball-through manifolds
Due to the special nature of lubricant product quality, its product classification, and in order to ensure the quality of the oil is often not allowed to have any mixing, the traditional production method will generally be dedicated oil delivery, so as to avoid mixing oil, but this way to cause the plant pipeline, operation and management difficulties, and at the same time, due to the process of some of the unavoidable utility pipeline, or valve switching errors and other reasons, mixing oil is difficult to avoid, especially in the filling products filling products. Especially in the filling product filling area, in order to tank the oil pipeline to a different automatic filling machine production line, often using the hose connection for the connection of different pipelines, often resulting in the hose area of the ground oil stains, and often because of the wrong pipeline and cause oil pollution. With the development of the machinery industry, the through-ball hose manifold and through-ball system came into being. The ball transfer is actually a combination of the technical functions of the hose connection station, its equipment, and ball technology, the use of combination principles using a small number of pipes to achieve multi-purpose connection, and the application of high-precision automated ball technology, making it possible to transport a variety of products in one pipeline. Ball pass systems and ball passable manifolds simplify the process by reducing the number of process pipes, while reducing the possibility of oil cross-contamination through automated control and high-precision line sweeping. In general, ball pass systems and ball passable manifolds are essential key equipment within a modern control system.
In general, when designing the modernized dosage control system, the above ABB, pulse churning, through-ball system and through-ball pipe sinks are necessary configurations, but according to the investment ability of the investor, the specific configuration of the above facilities can be discussed, such as how big the mixing kettle of the ABB is used, whether to use the metering kettle, etc., or whether to use the pipe sinks are fully automated pipe sinks or manual pipe sinks, etc., especially in the case of the pipe sinks, to fully discuss the possibilities of future development with the investor. Fully discuss the possibility of future development with the investor to determine the choice of the type of pipe sinks and the number of reserved interfaces.
1.3 Supporting production facilities
A complete lubricant dosage control system, in addition to the necessary core blending facilities, auxiliary blending facilities, there are generally some supporting production facilities, such as filling facilities, melting facilities and barrel facilities.
(1) Filling facilities
Generally speaking filling facilities is almost all the dosage control system needs, because the lubricating oil finished oil is generally in the sales terminal most of the products are in the form of filling to consumers, so the dosage control system will be configured with micro-filling, small filling, medium filling and vat filling filling filling production line. According to the production capacity and investment ability of the dosage system, it can be configured with high-speed automatic filling machine production line for bulk products and supporting automatic palletizing facilities in order to improve the production efficiency and save labor resources Filling of small products is generally recommended to configure automatic or semi-automatic filling line, supporting the ordinary palletizing machine, in order to reduce the one-time investment. Filling line selection to fully understand the needs of the investor to determine whether to support a number of optional facilities, such as barrel machine, capping machine, bottle machine, reject machine, labeling machine, labeling machine, roll-up machine and so on.
(2) Melt facilities
At present, the lubricant dosage control system is generally to save costs are self-produced OCP (viscosity index improver) diluent, OCP diluent production process is generally manual cutting, glue, melt glue repeatedly tank stirring and other artificial means of production, need to consume a long time and manpower, with the increase in labor costs, labor protection of workers to improve labor protection and the need for high-efficiency production, some of the current Dosing control system began to use some new means to assist production, such as automatic crusher, conveyor belt feeding, high-pressure homogenizer and other equipment, which can greatly improve production efficiency and reduce labor intensity. However, the above new equipment are brought about by the increase in investment costs Therefore, OCP production methods and equipment should be selected according to the investment capacity of the investor, should be considered in a comprehensive manner the annual volume, labor costs, energy costs and other factors, if the annual volume is not large, it is not always necessary to choose a high degree of automation of the production facilities.
(3) Barrel facilities
As there is a need for the production of filling products, there is a need for the supply of filling barrels. According to some of the dosage control system costing report, in general, the cost of their own barrels is lower than the cost of buying barrels, but the one-time investment in barrel equipment and energy consumption are larger, in the investment permit, wide area of land resources permit the premise, you can consider their own barrels, but harmful to the full combination of the investor's willingness to invest in the ability to require. If the investment capacity is limited, but considering the possibility of future development, the design should take into account the reservation of the space location of the barrel-making equipment and the corresponding power distribution, air supply and cold exchange facilities.
1.4 Storage system
The materials of lubricant dosage control system are generally divided into three types: bulk oil, barrel oil and solid additives. At the initial stage of design, it is necessary to have a comprehensive understanding of the approximate annual consumption of various materials, storage methods, and ways of entering and leaving the plant, which is used to determine the capacity allocation of storage tanks, warehouses, and so on. For example, base oil, generally bulk oil products into the plant, into the plant, including ship unloading, unloading trucks and pipeline transportation, according to the base oil consumption and the expected proportion of the way into the plant, according to the specification or the owner's special requirements for the number of days of storage, the calculation of the required storage tank capacity.
Additives and refined oils are generally categorized as both bulk tank storage and drum storage. Additives bulk oil and barrel oil distribution ratio is generally based on the owner's procurement channels to determine the tank capacity and warehouse volume in the consideration of additives, to fully take into account the owner's needs at the same time, due to the additives to absolutely avoid mixing of oil, additives single product needs to be individually set up tanks for storage, so the bulk additives can not be based on the total consumption of the calculation of the required tank capacity, it should be combined with the consumption of a single product to calculate the tank The number and capacity of storage tanks should be calculated in combination with the consumption of individual products to avoid the problem of insufficient number of storage tanks in the actual production process.
If SMB is used for blending, the storage tanks of finished oil should calculate the required tank capacity according to the number of storage days required by the specification, based on the annual production, and carry out detailed allocation of storage tanks according to the planned product varieties, so as to ensure that there is enough tank capacity for each different finished oil variety to be stored separately. At the same time, refined oil products need a certain amount of filling storage space, because the lubricating oil has its own special market demand, peak season and off-season is relatively clear, so the refined oil filling warehouse should fully consider the sales volume of the peak season combined storage capacity, it is generally recommended to calculate the refined oil filling capacity according to the average daily production of 15 days. If ILB blending is used, finished oil tanks can be set up without or a small number of tanks as a buffer can be set up, if there is a filling production conditions, the finished product warehouse still needs to be set up, but the capacity can be appropriately reduced.
In addition, there are melt glue production and barrel production of dosage control system, but also give due consideration to dry glue storage, OCP dilution tank storage, barrel raw material storage and filling material empty barrel storage.
1.5 heating program
Lubricating oil has viscosity, low pour point characteristics, in the storage process, because it is difficult to freeze and condense, generally room temperature storage, and in the conveying process and churning process needs to be heated to a certain temperature, in order to reduce the viscosity of the oil to ensure that the conveying speed. Therefore, the heating of lubricating oil is generally characterized by intermittent heating and rapid heating.
Conventional heating method, generally is the use of tank heater on the tank oil heating, pipeline oil with external heat insulation storage tank internal heating medium is generally used steam or hot water, pipeline heat source is generally used steam, hot water and electric heat tape way. Should according to the dosage control system dosage quantity supply situation, compare the cost of heat source consumption, preferred heating heat source.
At present, in part of the blending), the tank heating adopts the local heater technology, that is, in the tank set up the floating head type local heater, only to the tank local oil product for rapid heating, that is, need to use how much oil product on how much oil product heating, avoid the traditional tank heater need to the whole tank heating and cause the heating time is longer, the production of the problem of the need to preheat before. However, the local heater unit time energy consumption is very high need to dosage control system construction location can provide sufficient heat source, if you rely on blending, self-built boiler to produce steam, in order to reduce the load on the steam boiler, it is recommended that the tank is still used in the tank heating coil for heating.
2 Conclusion
Summarize the above different blending production plants have their different market objectives and dosage production methods, but also therefore require different design ideas.