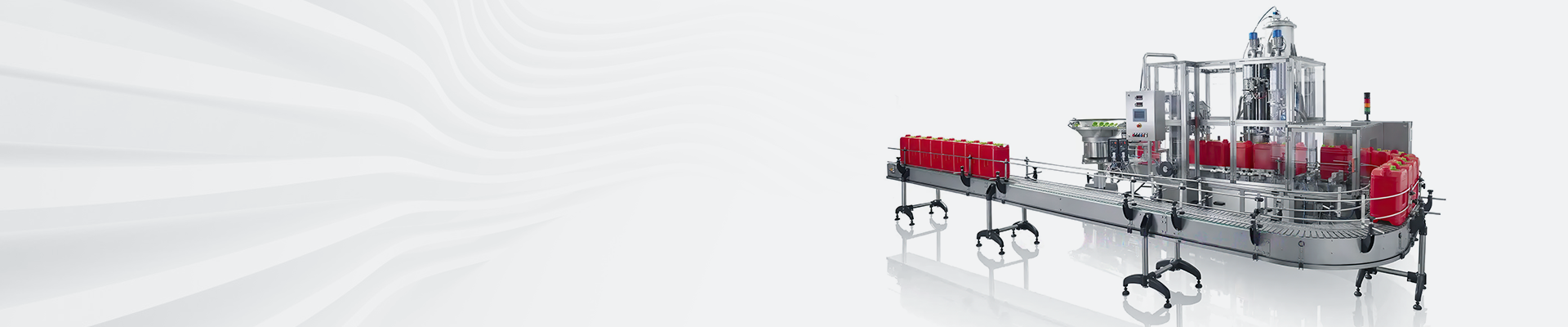
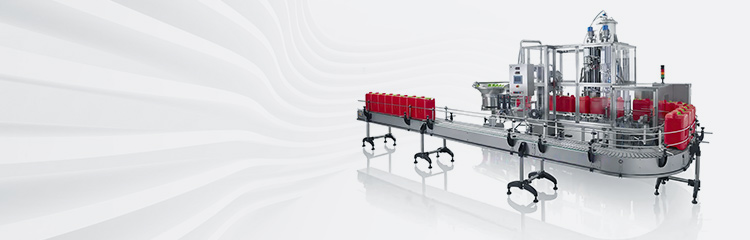
摘要:自动配料系统采用485协议组成,输出多阶段控制信号,直接访问PLC系统、实现多阶段热冷等温度控制、抽真空氮气填充、能够测量的电信号输出的定量灌装控制。
0引言
进入21世纪以来,随着国内润滑油消费市场的快速发展,国内外各大石油公司和地方企业开始大力发展润滑油产品业务,通过各种手段提高产品质量、减少损失、优化经营、提高企业知名度,从而在整个成品油销售过程中提高盈利能力。近年来,中国石油润滑油公司新建了华东润滑油厂,并结合市场变化进行了多次扩能改造。在近几年配料控制系统的设计过程中,总结了整体设计思路,在此分享和探讨。
1工厂设计的主要思路
1.1确定调合方案
在设计之前,需要确定调和方案,因为调和方案是润滑油配料控制系统的核心内容,采用不同的调和方案直接导致全厂配套设计内容和工程量的差异。
润滑油配料控制系统一般针对现代生产模式,即主要生产模式采用自动调合。目前,世界上最先进的混合方法主要是同步计量混合(SMB)或管道在线混合(ILB),根据不同的市场目标采用不同的混合方法。SMB的工作原理是:根据调合生产目标,调合系统自动生成调合配方,不同组分同步进入SMB的所有流道,经计量后均通过管汇流入指定的成品油反应罐。未同步计量的组分也可单独经SMB计量后进入成品罐,调合配方中的所有组分进入精炼油罐搅拌均匀形成精炼油。
ILB的工作原理是:根据调合生产目标,由计量配料系统自动生成调合配方,调合配方中的所有组分同时进入IB的所有流道。计量后,在管汇出口在线搅拌均匀后,可送至指定的成品油罐储存或直接送至装车、装车或灌装等终端设备。从SMB和ILB的工作原理可以看出,SMB实际上只是在管道中进行在线计量和混合,而不是在线调和,成品油的最终调和需要在成品油储罐中进行;然而,ILB是真正的管道在线调合,经过ILB的动态混合器后可以形成合格的成品油。
对于中小型配料控制系统,以及产品种类多、生产切换频率高的工况,或原料质量差异大的工况,一般适用SMB调合模式,其生产灵活,可满足不同的市场需求,特别适用于根据消费者市场需求确定生产目标的润滑油企业。对于大规模系统,特别是主要为特定客户生产订单式产品的配料控制系统,当原料来源非常稳定时,ILB调合法通常更适合,因为在线调合法可以节省油品运输和混合过程中的能耗,还可以节省大量成品油储罐用地,在节省投资的同时也便于管理。
在进行润滑油配料控制系统设计前,设计单位应该充分了解投资方的投资意向、市场目标、生产规模、油品来源、征地面积等各方面因素,从而协助投资方确定核心的调合方案,进一步确定调合控制方案、总图规划、配套设施各方面的设计方案。
1.2辅助调合设施
在确定核心调合方案后,应该进一步确定辅助调合设施的配置方案,,从而形成完整的调合系统。辅助的调合设施一般包括罐式批量调合投料系统(简称ABB)罐内搅拌设施、通球系统和通球管汇。
(1)罐式分批调合进料系统(ABB)ABB是一般润滑油进料系统中必不可少的辅助调合设施。其主要功能是调和小批量的成品油。各原料组分通过调配控制系统生成的配方依次进入调配釜,投料量由ABB配备的高精度称重仪称重控制,确保各组分投料量符合调配配方要求。
各组分在ABB调合釜内充分搅拌成为合格成品后,就可以直接转运出厂。
由于润滑油市场的特殊性,调宽经常需要根据客户的需求小批量生产一些高端产品或特殊产品,而SMB和ILB很少用于生产小至1~2t和最多30t的小批量产品,因为一方面切换品种和清洗管道费时费力,另一方面需要设置单独的小品种储罐,导致储罐利用率低。另一方面,ABB解决了小规模生产的问题,因此具有广泛的应用范围。不仅配备了通用润滑油配料控制系统,而且它已成为添加剂工厂的主要生产设备。
(2)罐内搅拌设施
通常润滑油产品罐配有混合设施,对于SMB成品罐中必须有混合设施,以便均匀混合各组分的油。对于ILB勾兑的成品,还需要在储罐中设置搅拌设施,主要是为了防止不合格产品长期存放后分层。
主要搅拌方法包括:罐内喷嘴循环搅拌、罐内搅拌器搅拌和气动脉冲搅拌。前两种方法是传统的搅拌方法,而新兴的气动脉冲搅拌主要是利用安装在储罐内的集气盘和高压注射器,以高压将净化空气瞬间注入罐内,并通过吹气泡驱动罐内的油上下流动,从而达到均匀搅拌的目的。目前,气动脉冲搅拌因其搅拌介质安全、搅拌速度快、能耗低、自动化控制水平高等优点,已逐渐占据润滑油搅拌的主要市场。一般来说,现代配料控制系统将选择脉冲搅拌作为罐内搅拌的生产手段。(3)通球系统和通球管汇
由于润滑油产品质量的特殊性,其产品的分类方式很多,而为了保证质量,油与油之间往往不存在混输现象。但这种方法造成工厂内管道多,难以同时操作和管理,在过程中由于一些不可避免的共同管段或阀门切换错误,难以避免混油,特别是在灌装产品的灌装区域,为了将油库的输油管道连接到不同的自动灌装机生产线上,不同的管道往往采用软管连接的方式进行连接,这常常导致软管区域的地面上有油污,并且常常由于接错管线而造成油污。随着机械工业的发展,球歧管和球系统应运而生。事实上,通球歧管结合了软管连接站的技术功能并装备了它与通球技术相结合,它使用少量的管道实现多目标连接,高精度自动通球技术的应用使在一根管道中输送多种产品成为可能。通球系统和通球歧管简化了工艺流程并减少了工艺管道的数量,同时通过自动控制和高精度扫描降低了油品交叉污染的可能性。一般来说,通球系统和通球歧管是现代控制系统中必不可少的关键设备总的来说,在设计现代化配料控制系统时,上述的ABB、脉冲搅挫、通球系统和通球管汇都是必要的配置,但根据投资方的投资能力,上述设施的具体配置可以商榷,比如ABB选用多大的调合釜、是否选用计量釜等,或者管汇是选用全自动管汇还是手动管汇等,尤其是管汇方面,要与投资方充分讨论今后发展的可能性,以确定选用管汇的型式和预留接口的数量。
1.3配套生产设施
完整的润滑油配料控制系统,除了必须的核心调合设施、辅助调合设施外,一般还有一些配套的生产设施,比如灌装设施、熔胶设施和制桶设施。
(1)灌装设施
一般来说几乎所有的配料控制系统都需要灌装设施,大多数润滑油和成品油在销售终端以灌装的形式提供给消费者,配料机将配备微灌装、小灌装、中灌装和大桶灌装的灌装生产线。根据配料系统的生产能力和投资能力,可为散装产品配置高速自动灌装机生产线,并提供自动码垛设施,以提高生产效率并节省劳动力资源。一般建议配置自动或半自动灌装线和普通码垛机,以减少一次性投资。在选择灌装生产线时,需要充分了解投资者的需求,从而确定一些配套设施,如装桶机、封盖机、分瓶机、剔除机、贴标机、卷标机等。
(2)熔胶设施
目前润滑油配料控制系统为了节约成本,一般都是自己生产OCP(粘度指数改进剂)稀释剂。OCP稀释液的生产工艺一般采用切胶、上胶、罐内反复搅拌等人工手段生产,耗时耗力。随着人工成本的增加,工人劳动保护水平的提高和高效生产的需要,一些配料控制系统开始采用一些新的手段来辅助生产,如自动破碎机、传送带送料、高压均质机等设备,可以大大提高生产效率,降低劳动强度。但上述新设备会增加投资成本。因此,应根据投资者的投资能力选择OCP的生产方式和设备,并综合考虑年消耗量、人工成本、能耗成本等多种因素。如果年消耗量不大,就没必要选择自动化程度高的生产设施。
(3)制桶设施
由于罐装产品的生产需要,需要供应灌装桶。根据配料控制系统的一些成本核算报告,一般来说,自己造桶的成本低于购买桶,但造桶设备的一次性投资和能耗较大。在广泛地区的投资许可和土地资源许可的前提下,我们可以考虑自己制造桶,但充分结合投资者的意愿和投资能力要求是有害的。如果投资能力有限,但考虑到未来发展的可能性,在设计中应考虑制桶设备的空间位置预留以及相应的配电、送风和冷却设施。
1.4储存系统
润滑油配料控制系统的物料一般分为三种:散装油、桶装油和固体添加剂。在设计初期,需要充分了解各种物资的大概年消耗量、储存方式和交付方式,用于确定储罐和仓库的容量配置。比如基础油一般是散装进厂,发货方式有船卸、卸油和管道运输。根据基础油的消耗量和预期交货方式的比例,根据规格或业主特别要求的储存天数计算所需的储存量。
添加剂和成品油一般分为散装罐储存和桶装储存。添加剂的散装油和桶装油的分配比例一般根据业主的采购渠道决定。在考虑添加剂的储罐容量和仓库容量时,应充分考虑业主的需求。同时,由于添加剂应绝对避免与油混合,添加剂单品需要储存在单独的储罐中,因此散装添加剂不能按总消耗量计算。储罐的数量和容量应根据单个产品的消耗量进行计算,以避免实际生产中储罐不足的问题。
如果采用SMB进行调合,应根据规范要求的储存天数和年产量计算成品油罐所需的罐容量,并根据计划的产品品种进行详细的罐分配,以确保不同的成品油品种分别有足够的罐容量进行储存。同时,成品油需要一定的储存空间用于填充材料。由于润滑油有其特殊的市场需求,旺季和淡季截然不同。因此,应充分考虑成品油灌装材料在旺季的储存能力,一般建议按照15天的日均产量计算成品油灌装材料的储存能力。如果采用ILB调和,成品油罐可不设或设少量储罐作为缓冲。如果有灌装生产条件,成品仓库仍需设置,但储存量可适当减少。
另外,有熔胶生产和制桶生产的配料控制系统,还要适当考虑干胶储存、OCP稀释液罐储、制桶原料仓储和灌装物空桶的仓储。
1.5加热方案
润滑油具有高粘度、低倾点的特点。在储存过程中,由于不易冻结,一般在室温下储存,但在运输和搅拌过程中需要加热到一定温度,以降低油的粘度并保证运输速度。因此,润滑油的加热一般具有间歇加热和快速加热的特点。
常规加热方式一般采用罐内加热器对罐内油品进行加热,管道内油品采用外部伴热。储罐内的加热介质一般采用蒸汽或热水,管道伴热的热源一般采用蒸汽、热水和电伴热。根据配料控制系统中配料量的供应情况和热源消耗成本,对加热热源进行优化。
目前罐内加热采用的是局部加热器技术,即在储罐内设置浮头局部加热器,只对罐内局部油品进行快速加热,即需要多少油品就加热多少,避免了传统罐内加热器需要对整个罐进行加热,导致加热时间长、生产前预热的问题。然而,局部加热器的单位时间能耗很高,这要求配料控制系统所在的位置能够提供足够的热源。如果蒸汽由掺烧和自建锅炉产生,建议使用罐中的加热盘管进行加热,以减轻蒸汽锅炉的负荷。
2结论
综上所述不同的调合生产厂有其不同的市场目标和配料生产方式,也因此需要不同的设计思路。