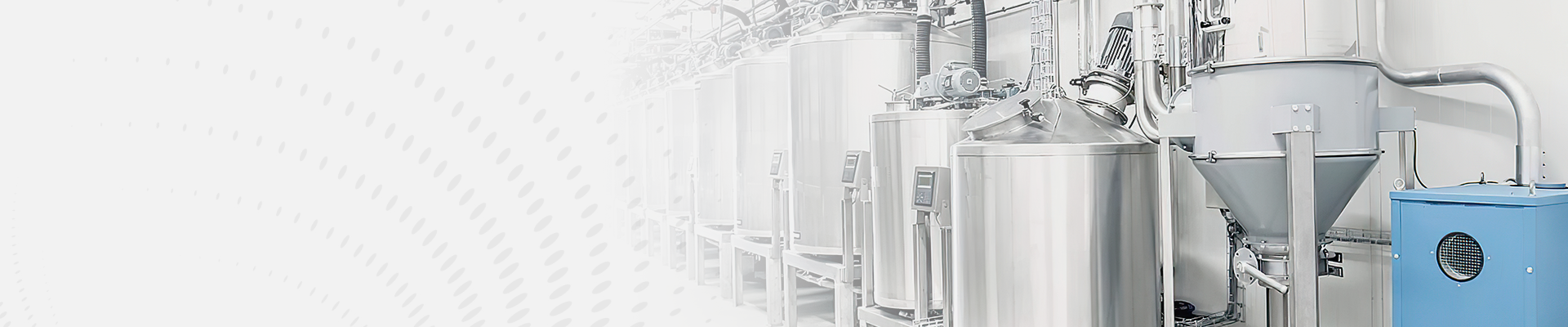
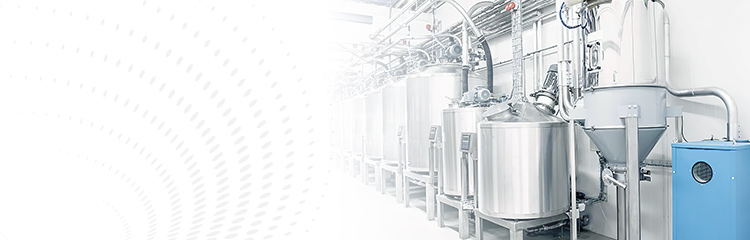
Powder dosage system program consists of industrial control machine, PLC, industrial weighing instrument, frequency converter, vibration motor, mixer, sensor, conveyor belt and other parts.
The whole automatic feeding system is composed of industrial control machine, PLC, industrial weighing instrument, frequency converter, vibration motor, mixer, load cell and other parts. The upper industrial control machine provides human-computer interaction interface, completes the control information input, data management, data display, storage, statistics and reports, etc. The upper computer adopts IPC810 industrial control machine, the main work is as follows:
Weighing and mixing machine firstly reads a certain number of formula according to the operator's instruction, then, according to the proportion and sequence of ingredients in the formula, it sends out the instruction to PLC to start dosage, which enables PLC to start a specific frequency converter. In the process of batching, the host computer of industrial control reads the status words of PLC in real time by polling, on one hand, to understand the operation status of PLC and PLC subordinate equipments; on the other hand, it reads the weighing data of the weighing instrument installed on the batching machine in real time, and according to the batching strategy, the host computer sends out the instruction of stopping the batching to the PLC when the weighing is close to the set value of the recipe. When all the materials on a formula are finished, the whole dosage process is suspended, waiting for the operator's instruction.
Weighing and batching system operation process, PLC and the host computer real-time communication, so as to ensure that the data displayed on the interface and the consistency of the actual data on the scene, the operator in the host computer issued by the operation command and set parameters can be sent to the PLC in real time, the main work of the PLC are:
(1) Receive the commands sent from the host computer, and control the start, stop, fast and slow of the vibration motor through the frequency converter;
2) write the running status of the frequency converter into the memory data area in real time for the industrial control machine to read.
(3) Prepare various states of itself in the form of status words for real-time reading by the total industrial control machine.
This batching system is specially designed for automatic batching of small materials, the whole system mainly consists of frame, storage hopper, material crushing and mixing device, screw feeding device, automatic weighing and batching trolley and automatic weighing module, the system has two functions of automatic and manual, users can choose conveniently according to their own situation. Under the automatic state, the operator only needs to select the pre-set formula number and click the start button, which can add materials according to the set formula and control the corresponding screw feeding device.
The whole batching process is controlled by PLC. The human-machine interface is controlled by PLC. DELL computer and general-purpose configuration software of Configuration King are used for real-time display of dosage weight. The actual dosage amount is displayed on the screen immediately after each dosage is completed, until the next dosage starts to refresh to zero. The dosage quantity of each bin is kept in the database of the system, which can be conveniently called for querying, comparing and printing, and generates and prints daily and monthly reports. The data recorded by the system cannot be modified, deleted or moved by the operator, so that the management personnel can fully grasp the real situation of each batching.
Characteristics of dosage equipment:
(1) This weighing and batching equipment adopts screw feeding, which is characterized by accurate, stable and reliable feeding. The maximum feeding capacity is up to 500g/min.
(2) PLC control, human-machine interface using Lenovo computer and configuration king general-purpose configuration software, with accurate control, high reliability, intuitive and friendly interface and other characteristics.
(3) The weighing system integrates recipe management and ingredient weighing management. The whole system is easy to operate, and for ordinary staff, they can also operate according to the information appearing on the screen. Thus, accurate weighing and operation efficiency are obtained.
(4) Save the dosage and weighing records, and output reports, so that each product can be traced.
The system successfully solved the enterprise in the production activities of manual dosage labor intensity, low productivity, poor working environment, mismatch, leakage and other phenomena, so that the dosage accuracy, production efficiency increased exponentially, resulting in huge economic benefits.
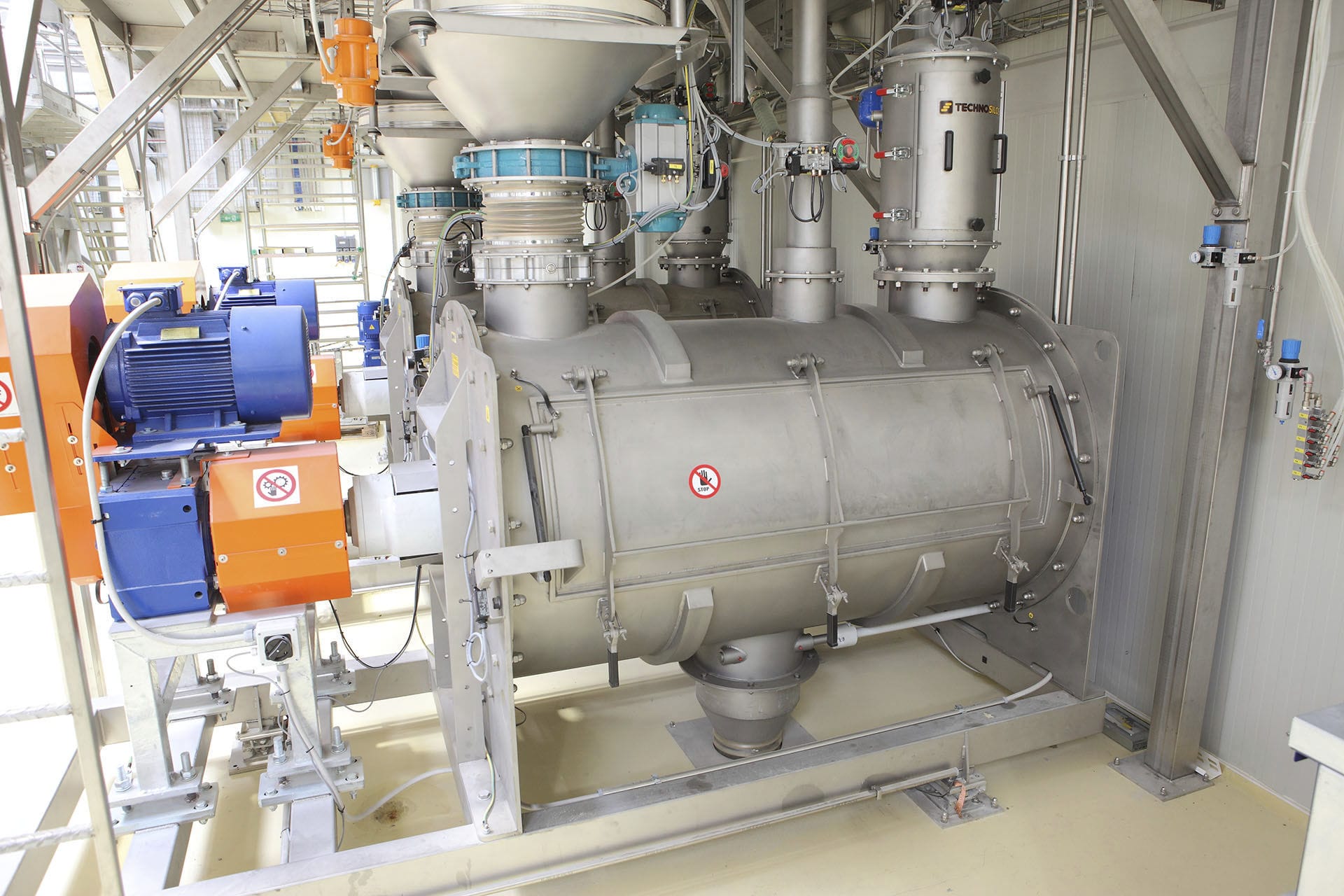
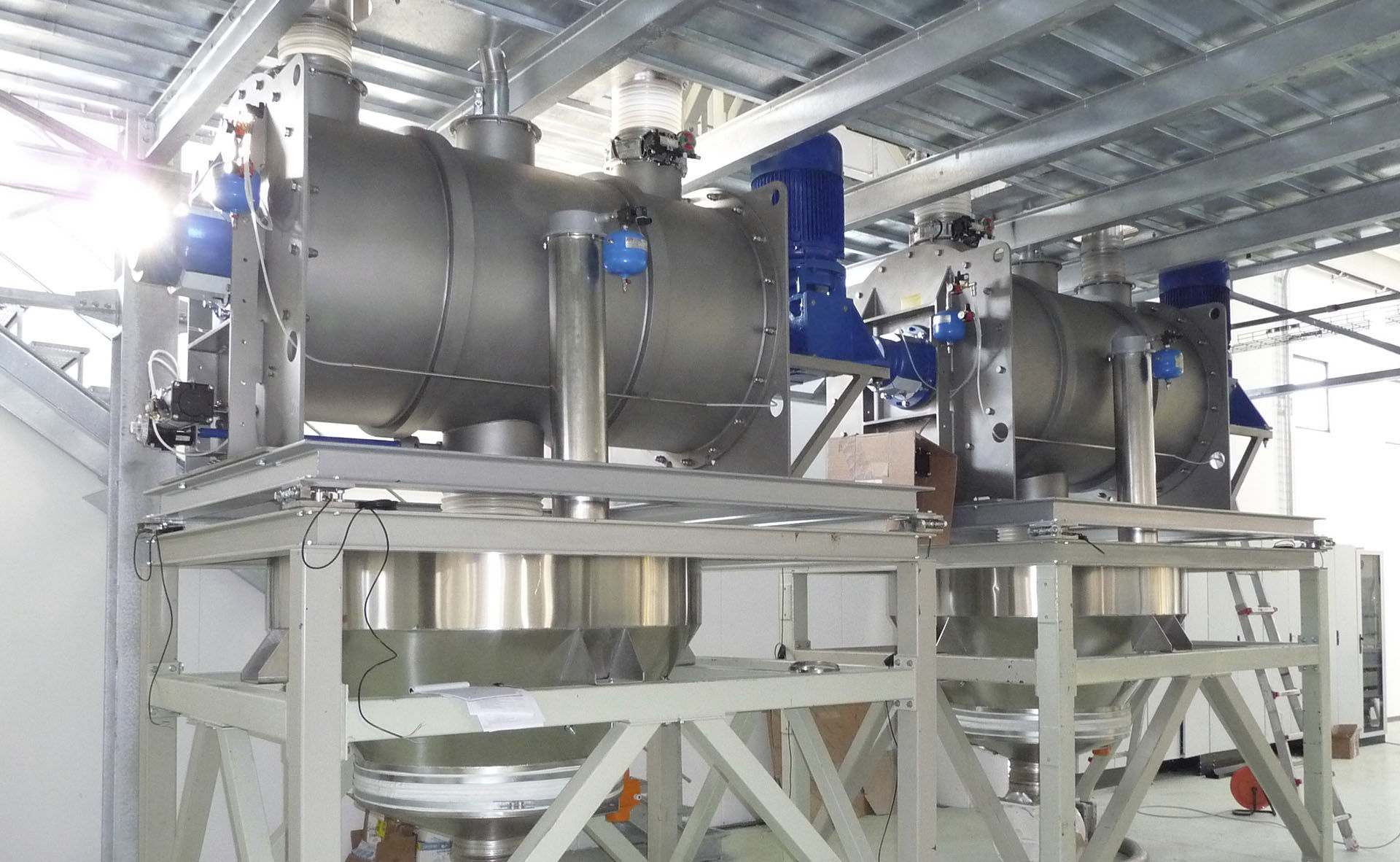
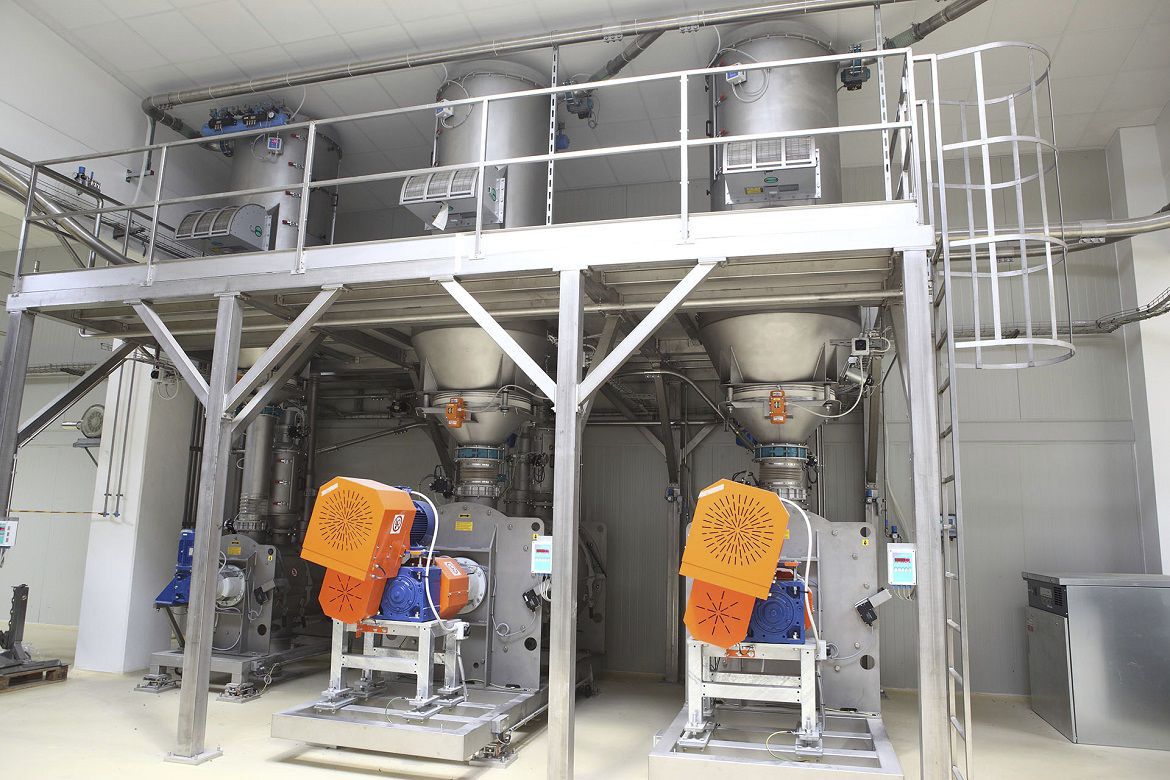
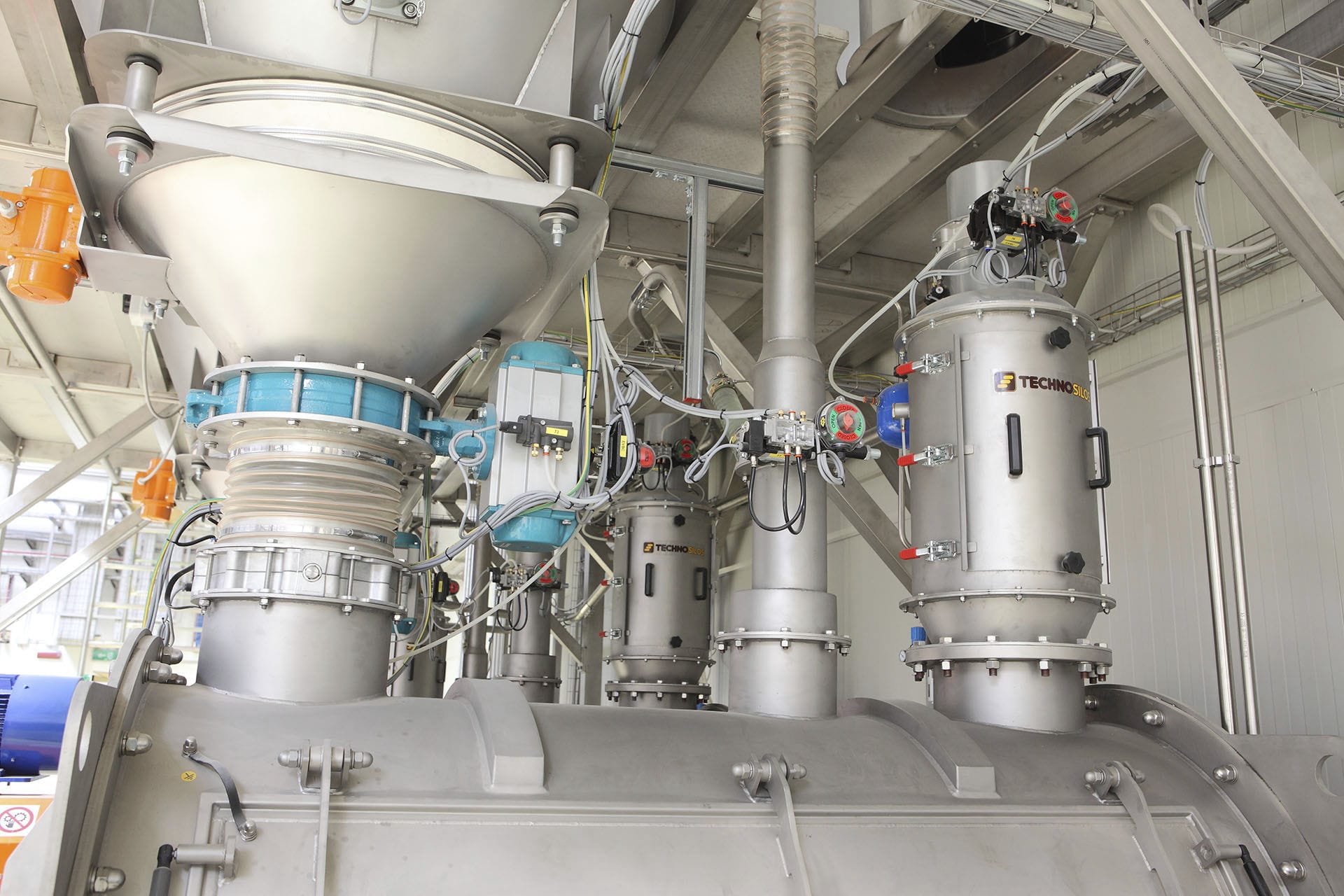
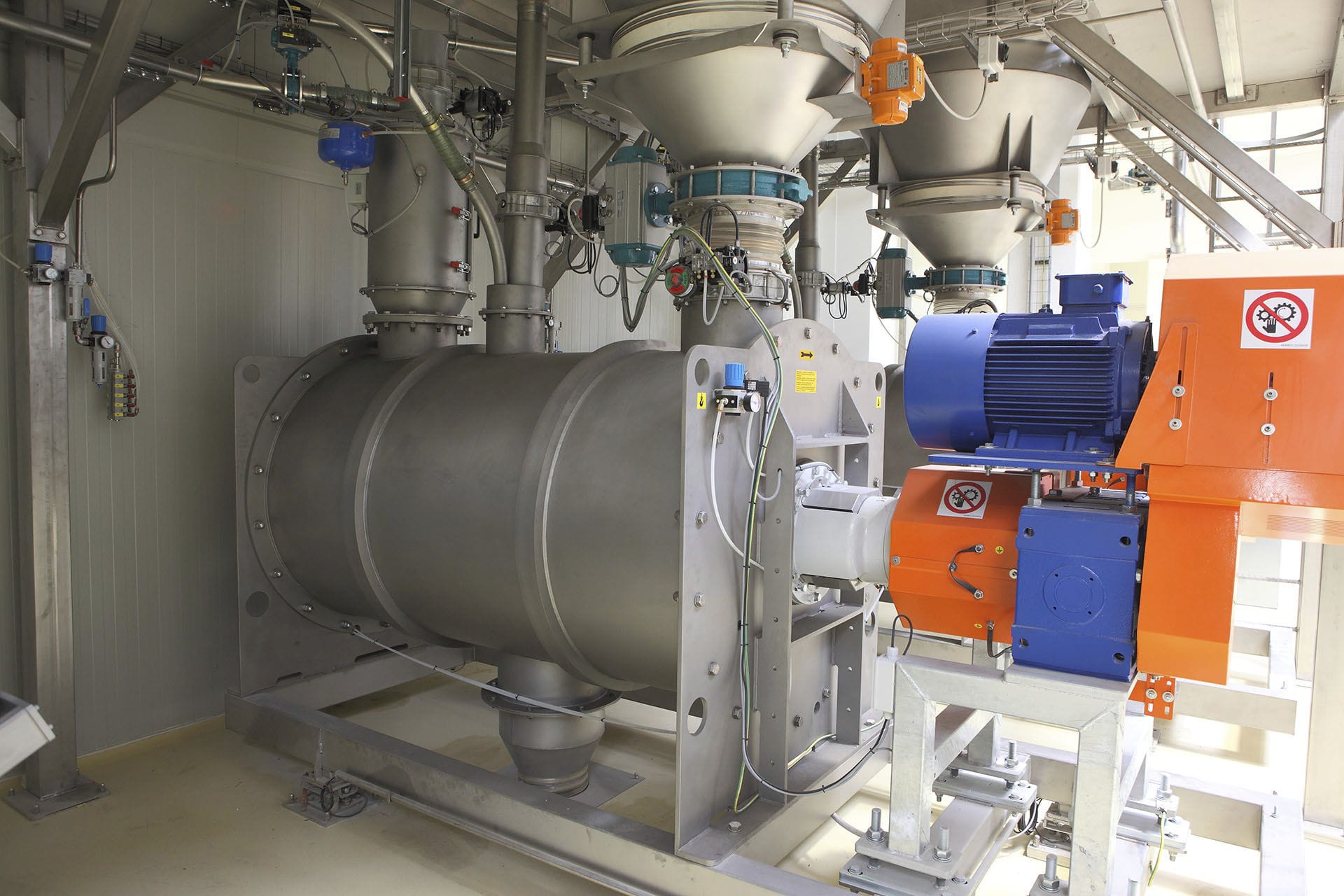