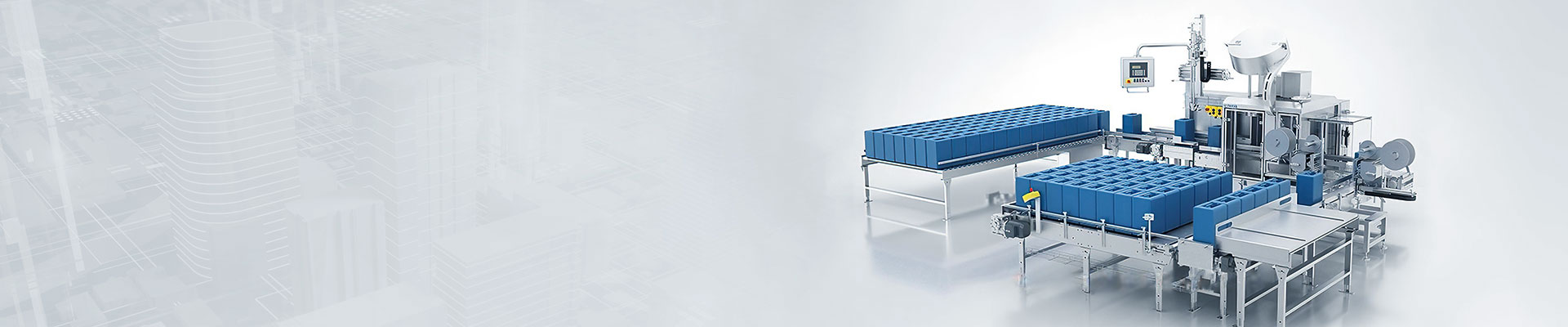
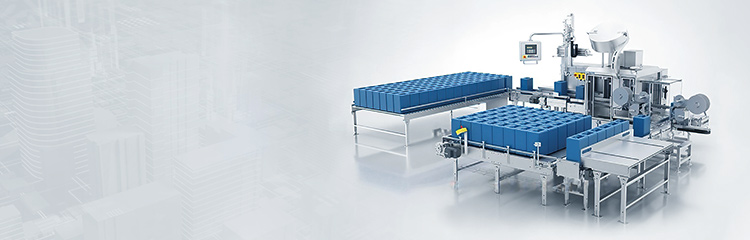
Weighing and dosing system adds a certain amount of raw material from raw material tank to continuous mixing tank, according to different requirements of dye color, a certain amount of pigment (containing blue, red and yellow primary colors) from three reaction tanks is sent to continuous mixing tank, and then stirred for a certain period of time at a certain stirring speed in continuous mixing kettle and discharged through pipeline according to different dosing ranges. By calling the corresponding unit in the controller, the final realization of the material batch production. The process functions of mixing, resting and layering, and product discharge are realized by the mixing and discharge, and the related data in the units shown in dotted lines.

Automatic Dosage system realized by means of Weighing modules and weighing controllers, with constant and ratio functions, which can be directly used for the process control of the production dosage. According to the standard signals entered into the weighing module, it realizes weighing and measuring, automatic control, data counting and uploading; according to the operating environment and the actual requirements, it is possible to set the minimum credible weight; if the proportioned material is less than the minimum set value, the weighing controller alarms on the display that the value obtained is not within the set range. The weighing controller is also equipped with an RJ45 standard Ethernet port, which allows access to the upper control system. The operator in the control room can monitor the weighing data, adjust the settings, generate reports, backup or restore the data through the control system, making it a complete solution for weight measurement and control. With the promotion of weight measurement and its successful application in other industries, we proposed a control program for weight measurement, which was adopted after many discussions with the process side and a comparison of the investment of the two programs. From parameter acquisition to process control forms a complete weighing monitoring system.
In the reaction kettle through the floor at an angle of 120 ° installed three weighing modules, three weighing modules were output signal 4 ~ 20mA to the weighing controller installed in the field, the weighing controller of the three-way value superimposed into the quality of the material, and at the same time on the quality of the inputs to the accumulation of a variety of materials. A shut-off valve is installed on the main pipe of all material lines into the reactor to interlock with the weight signal; the weighing controller communicates with the control system in the control room through PROFIBUS-DP bus, and the control system in the control room carries out the automatic metering and control of the material according to the stored or set formula ratio. The on-site controller has the functions of manual feeding and automatic feeding selection, and the weight of the materials fed manually and automatically are recorded and accumulated by the control system. At the same time in the automatic feeding state cut-off valves and pumps and set parameters automatically interlocked.
The feeding system adopts the weight control program, which reduces the two links of temperature and pressure compensation and density calibration in the volumetric weighing meter measurement, and the solid catalyst which needs a small amount can also be added by weight measurement, and ensures the dosing accuracy to reach 0.8 ‰; the cut-off valve on the kettle inlet pipeline replaces the cut-off valves on the branch lines, which reduces the investment of the valve equipment purchase and installation; the signal bus transmission is not interfered by other signals, and ensures the control system in the control room and the control system in the control room to be in line with the set parameters automatically. The signal bus transmission is not interfered by other signals and ensures that there is no deviation of parameters between the control room control system and the on-site controller.
The high precision of weight metering ensures the high quality of products; the bus transmission of weight metering improves the control system capability and reliability, thus perfecting the operation capability and liquid level of the whole reactor feeding system. With the rapid expansion of industrial automatic production scale, the industry competition is becoming more and more intense, the requirements of the control system from the simple completion of the production task, to the set of control, optimization, management, communication and other aspects as a whole, the weighing module monitoring system into the kettle feeding control use has a very good prospect.