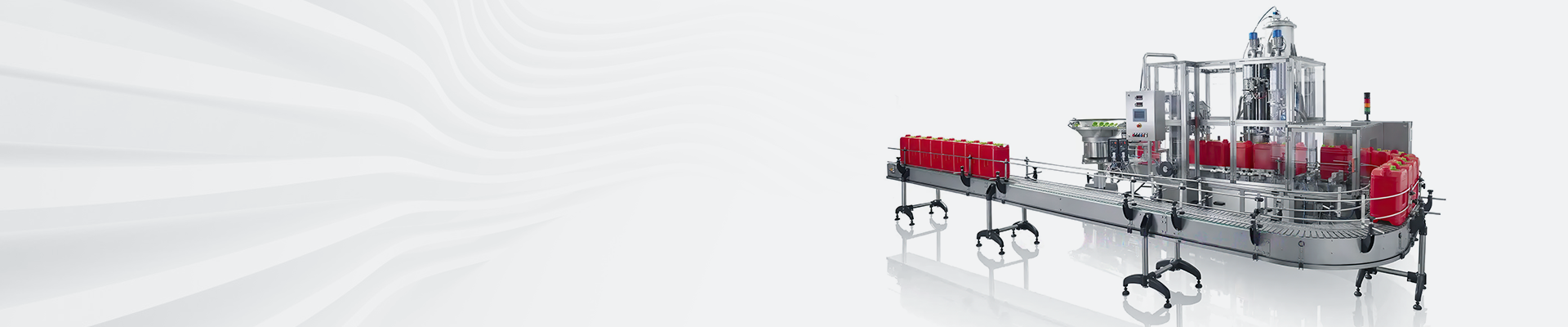
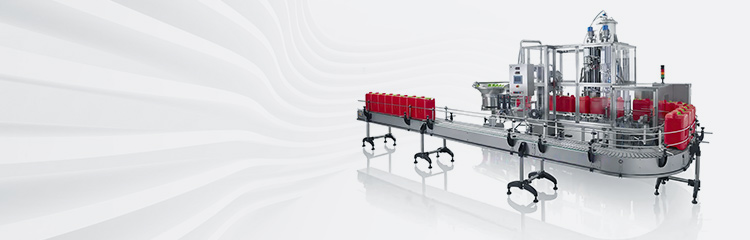

Summary:The raw slurry batching process is an important process in the production of sintered alumina. In order to control this process, the batching control system for this process was first designed and developed using Rockwell's ControllogixPLC, combined with Rockwell's ControllogixPLC. The advanced three-layer network, namely EthemeVIP, ControlNet, and DeviceNet, realizes various control functions of the batching process; the RsViewStudio configuration software is used to develop rich monitoring screens and realize functions such as process monitoring, parameter recording, and reporting: in the above work On this basis, in order to verify the effectiveness of the development program before actual operation, a physical test platform for the raw slurry batching process consisting of a PLC control system and a PC was developed and tested.
Raw slurry batching process is an important process for mixing raw materials in sintered alumina production. In this process, various raw materials are transported to the ball mill for mixing and grinding to form raw slurry. The quality indicators of the raw slurry affect the quality and yield of the final alumina product. The dosing system takes the raw slurry dosing process as the application background, and utilizes the hardware and software resources of the weighing and dosing system to design and develop the dosing control system for the raw slurry dosing process. The main contents of the automatic dosing system day include the control scheme, the control logic, and the development of the monitoring screen, etc. The dosing control system is designed and developed to ensure the quality of the raw slurry. In order to verify the effectiveness of the development program before the actual commissioning, specifically designed the raw slurry dosage process of physical test platform, the main content includes the test platform structure design and debugging, etc., through the physical platform to achieve the validity of the developed raw slurry weighing control system program verification.
1 control system design and development
1.1 control program
In order to achieve the control of alumina raw slurry batching process process indicators, the main use of the following program to achieve: the weight of various raw materials and ball mill through the weighing module, density sensor and current transformer feedback to the PLC controller, the PLC through the frequency converter to control the speed of the belt scales and pumps, thereby controlling the flow of various raw materials, and through the monitoring computer to monitor the operation of the entire system. This design adopts the Controllogx controller of Rockwell Corporation of the United States, combined with ControlLogixPLC and Rockwell's Ethernet/IP, DeviceNet and other three-layer network, PLC communicates with the host computer and the inverter through Ethernet and DeviceNet, respectively, and the inverter is connected to the pump and the belt scale. The model number of the power supply module is 1756-PA72/C, the model number of the CPU module is 1756-5561, the model number of the Ethernet module is 1756-EN-BT/A, the model number of the device network module is 1756-DNB, and the /0 modules used are 1756-IB16/A and 1756-IF8 modules. Taking the individual mill system as an example, L1, I2 and 13 are AC three-phase power supplies, and 0A0 is a circuit breaker for protection. The frequency converter is connected to the AC three-phase power supply through contactors QA1~QA5. Alkali powder belt scale, red mud slurry pump, alkali red mud slurry pump, mixed ore belt scale, limestone belt scale are connected to the frequency converter through the thermal relay driver parts BB. When the slurry pump and belt scale are working, if the working current is too large, it will make the thermal relay driver BB work to disconnect the current connected circuit and play a protective role.
1.2 Control program
The control program includes two categories: logical control program and continuous control program. Logic control program refers to the start-stop control and interlock control of key equipment, mainly including:
(1) Start-stop and interlock control of alkali powder belt scale, ore mixing belt machine and limestone belt scale;
(2) Start-stop control of red mud slurry pump and alkali red mud slurry pump;
(3) Ball mill start-stop control.
Continuous control program refers to the flow control program for various raw materials, and the flow control loop program includes:
(1) Alkali powder flow control loop;
(2) Red mud slurry flow control loop;
(3) Alkali red mud slurry flow control loop;
(4) Mixed ore flow control loop;
(5) Limestone flow control circuit.
All flow control adopts PI control algorithm.
1.3 Monitoring screen
The monitoring screen includes the login screen of the monitoring system, the help screen, the general screen of the process flow, the monitoring screen of each mill, the monitoring screen of the alkali addition system, the monitoring screen of the red mud slurry tank, the monitoring screen of the raw material slurry tank, the monitoring screen of the equipment status, the monitoring screen of the parameter overview, the monitoring screen of the alarm window, and the monitoring screen of the data trend graph.
2 Design and development of physical test platform
The physical test platform is an advanced method to combine the real PLC control system with the object equipment. The control program is written in ControlLgixPLC, the PLC outputs the operation results to run in the object equipment, the object equipment computer calculates the control object, and the calculated results are fed back to the controller, so that the closed-loop control of the raw slurry batching process can be realized, thus verifying the effectiveness of the developed control system program.