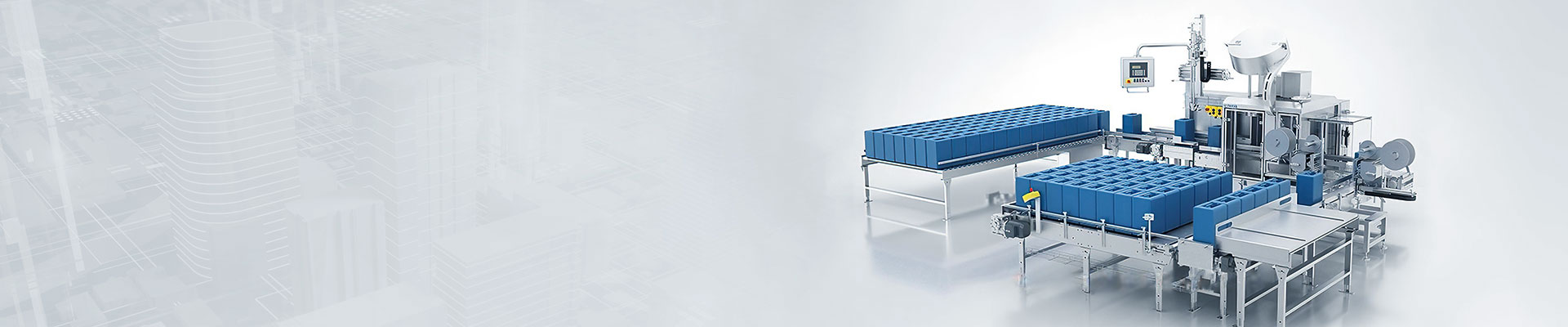
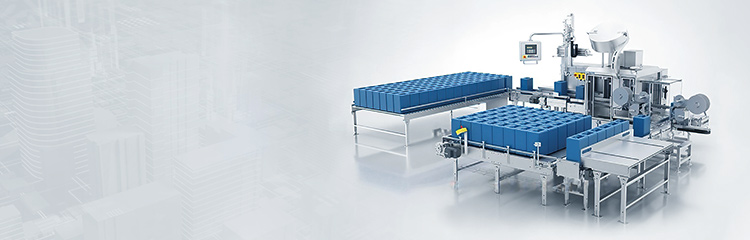
The design process of spiral scale is based on raw material→storage→measurement→drying→conveying→use, which is used together with the central dryer (dehumidifier) system, which enables the dry air to dry the raw material again and prevents the moisture back of the dried plastic, and meanwhile, it cleans the conveying pipe after each conveying cycle to ensure that there is no residue in the pipeline. According to the pre-determined formula, all kinds of different raw materials are mixed proportionally. In order to improve the precision and speed of batching, ensure the quality of products and increase the output, microcomputer control technology is adopted.

Screw scales are mainly involved in continuous dynamic metering and controlled feeding of powdered or loose granular materials into a metering reamer unit using a screw conveyor. A load cell mounted on the metering reamer detects the weight of the material and generates a voltage signal proportional to the weighing load, which is then fed to the controller. The controller receives preset reamer speed data. Normally, in double tube metering, the metering reamer is kept at a constant speed, i.e. the speed signal is the design value of the metering reamer. From this data, the controller is able to calculate the instantaneous flow rate and the cumulative weight value.
The control system compares the actual flow signal with the set flow signal, and outputs a control signal to the frequency converter through PID regulation, thus dynamically adjusting the speed of the feeding reamer to realize quantitative feeding. This process ensures that the material flow rate can be stabilized at the set flow rate. Spiral weigher also adopts a feed-forward adjustment system, according to the set feeding amount to continuously adjust the speed of the powder balance locker, in order to achieve accurate, stable and continuous feeding.
The spiral weigher also has the following performance characteristics:
Adoption of advanced feed-forward regulation system control system;
The use of a powder balance locker ensures stable feeding;
Simultaneous adjustment of the powder balance locker and metering screw improves metering accuracy;
The use of large feed opening, variable diameter, variable distance, overflow outlet design, to ensure that the material is uniformly sunk, stable and controlled;
Using high precision digital weighing module and digital transmission technology;
The controller adopts touch display technology with Chinese and English graphic display;
It can be connected with 485 communication, CAN communication, DCSPLC and other interfaces;
Adoption of GPRS wireless digital transmission function, support SMS report, remote diagnosis and calibration scale and other functions.
These features make the spiral scale suitable for a variety of industrial fields, such as electric power, metallurgy, coal, chemical industry, etc., especially in application scenarios that require continuous, dynamic measurement and control of powdery or bulk materials.