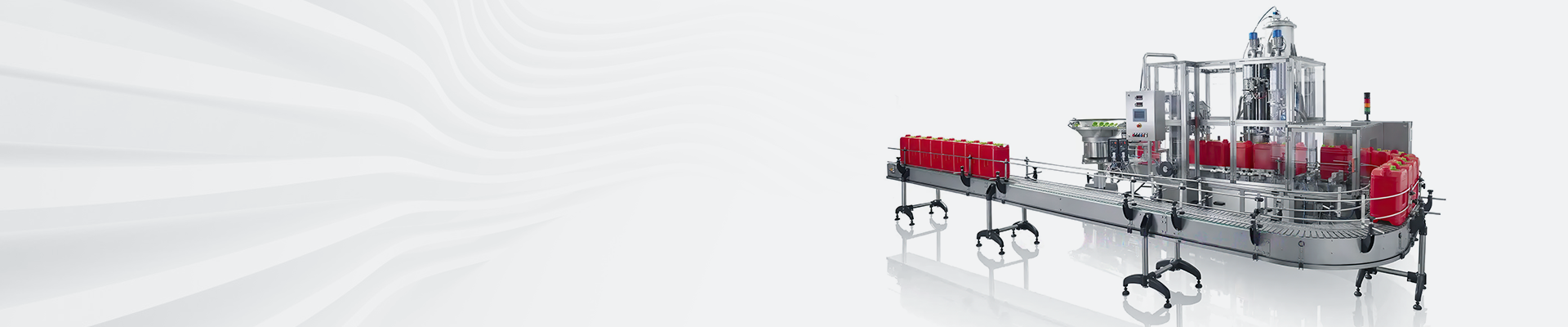
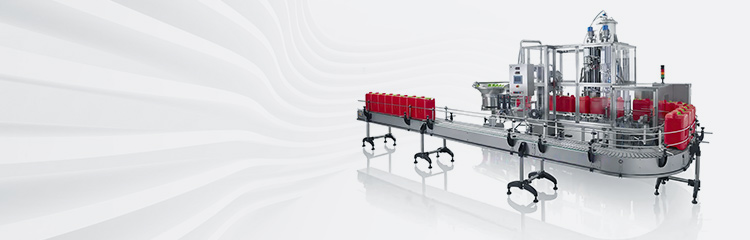

Summary:The automatic batching system automatically detects and controls the process on site to ensure the continuity of the batching operation of alumina production, achieve the goal of few or no people on duty, and ensure the quality of the final product.
Process requirements:
1 Introduction to the dosing process
a. Materials to be added: hot coke, sintered blocks (hot and cold two kinds), miscellaneous materials (intermediate materials in the plant), regimentation of aluminum.
b. Charging process by function, can be divided into the following functional sub-loading system: loading, discharging feeding system; material tanker transfer system; crane lifting and crane walking system; furnace top material bell opening and closing system; furnace top material level detection automatic dosing; coke preheater plus cold coke automatic dosing.
c. Charging frequency: generally 7-8 times/hour, the fastest 10 times/hour.
d. Charging area loading mode: double material port to double material tank discharge; single material port to double material tank discharge; single material port to single material tank discharge.
2 charging process:
Charging program designed for a single material corresponding to the furnace, the material position program, that is, each material on the charging position of any one or several charging position in several batches of charging, according to the instructions to enter the next material charging process; each charging process can be carried out automatically between the cycle or at any time there is an operator instruction to carry out a single batch of materials or modify the cycle of charging order. If a device fails during normal operation, the PLC can automatically stop the device before the source of material, cut off the source of material, and at the same time, the device after the equipment delayed operation for a period of time, to ensure that the feeding process will not appear in the phenomenon of blockage. Feeding process time can be automatically or manually modified at any time through the host computer to set the parameters.
Material from the silo into the feeder, the weighing signal of the material into the weighing funnel, weighing signal processed by the controller to control the vibration feeder to a certain downstream speed downstream: when the measurement of the material reaches the set value, feeding stops; confirmed by the detection of the charging trolley in the specified charging position, and to confirm that there is no material in the trolley, according to the operator's instructions or the automatic program metering charging is open, the material enters the feeding trolley; when the measured material is all in the charging trolley, the material is not blocked, and the material will not be blocked. Measured material all into the charging trolley, and confirm the measurement of the material to the warehouse door is closed, according to the operator instructions or automatic procedures to add the next batch of material, the same start according to the operator instructions or automatic procedures to start the charging trolley walking motor, complete the lifting process, charging trolley to reach the designated location, the trolley stops, the blast furnace door opens, charging, material poured into the blast furnace; when the charging trolley of all materials in the When all the materials in the charging trolley are poured into the blast furnace, the charging trolley returns to its position, the door of the furnace closes, and the charging trolley returns to the designated bin to start the next batch of charging. The high-speed counting module from the frame is used to receive the encoder signals of crane lifting and lowering, crane traveling and tank transferring vehicle traveling, which are processed by PLC as position (displacement) signals to participate in the position detection, travel correction and control of the automatic dosage system (travel switches are given priority in the automatic dosage system).
Automatic batching system selection and overall performance:
Based on the characteristics of the industry and the technical requirements of the batching machine, the world-famous ModiconTSXQuantum automation series PLC automatic batching system of Schenider, FIX software products of Intellution and DELL network operation station products of the United States are selected for this project with the characteristics of high performance, high reliability, high stability, compatibility, openness and easy to upgrade. and American DELL network operation station products, provide a full set of advanced, technically reliable PLC automatic batching system.
All the equipments participate in interlocking, the start-up direction is the motor start-up direction, start in sequence; the stopping direction is the motor stopping direction, requiring all the equipments to be stopped to be stopped only after a delay, realizing the process interlocking of start-up and stationary, and carrying out the control automatically.
Feeding program and weighing control unit can be automatically or at any time offline operation between the feeding system can be realized when a measuring hopper control unit failure, by manual to the PC system to send out feeding, bin door opening, closing, bin full, bin empty and other signals, you can carry out the feeding cycle. When the PC automatic dosage fails, the metering automatic dosage system operates reliably; when the whole automatic dosage fails seriously, the automatic dosage operation is put into manual state to complete the dosage filling.
The operating system (upper monitoring software) has convenient and flexible Chinese operation interface: real-time data acquisition, display (e.g. weighing) and processing; control operation and control output; equipment and status monitoring; alarm monitoring and processing; data communication with DCS system of blast furnace; historical data management; log record; generation and display of process flow screen, dynamic screen of crane (lifting and walking) and tank transfer vehicle operation. Display; automatic dosage initialization and dosage process sub-automatic dosage initialization processing; on-line calculation, on-line modification; automatic dosage system self-diagnosis and self-recovery; database maintenance; report printing; automatic dosage system's expandability; communication interface with the management level and so on.