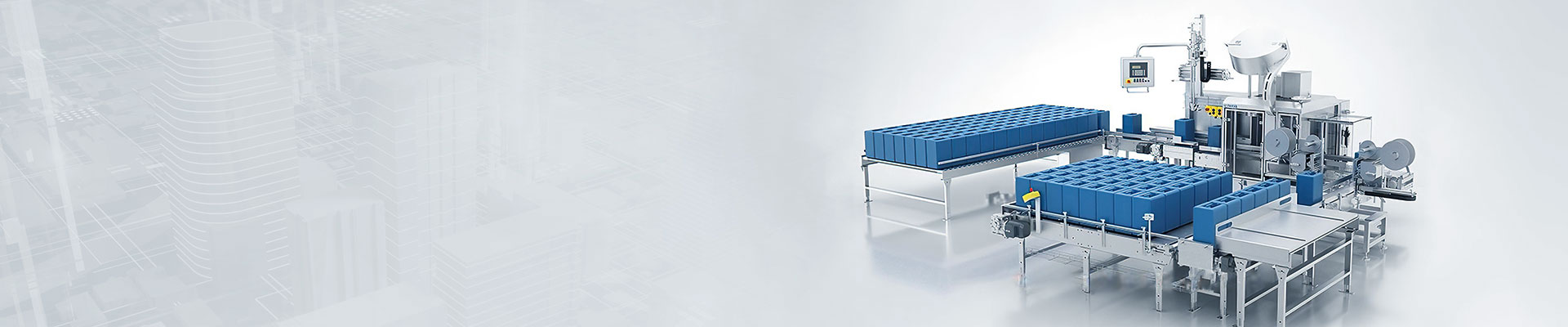
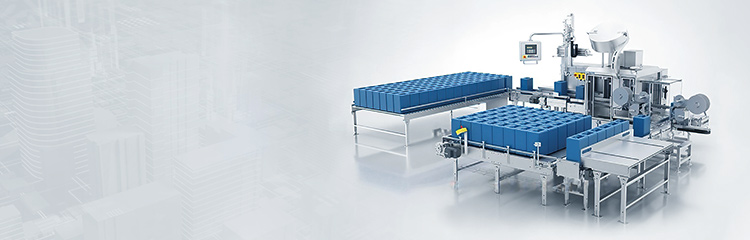
The feeding system is mainly used in plastic injection, extrusion or hollow process where a variety of raw materials are mixed according to weight ratio. The setting data will not be lost after the power is cut off by EEPROM, no battery is used; Use the human-machine interface status display touch keyboard data input, more convenient operation, but also can store a large number of formula data (500 groups); High speed and high precision AD grab weight faster and more stable; All the boredom is evenly mixed after gravity measurement, which can strictly control the accuracy. Check the weight data and the selected raw materials to ensure the precision and accuracy of the mix.

Automatic feeding systems (e.g. dosing containers containing a weighing device) read the weight value once every fixed time interval, and the difference between the previous and subsequent weights is used to calculate the reduction per time unit (i.e. the instantaneous flow rate). The weighing controller compares this actual measurement with the preset flow rate value, and at the same time controls the rotational speed of the auger Feeder to regulate the feeding volume. When the weight of the material in the hopper reaches the minimum setting value, it will automatically open the charging valve to carry out periodic charging operation. In order to ensure the correctness of the weighing results, an appropriate filter can be selected to filter the weighing signals during the measurement process.
The feeder adopts a new generation of single crystal chip microprocessor, with automatic compensation function, and can be automatically calibrated each time the machine is turned on to ensure accurate precision. This new series of products is mainly used in the plastic injection, extrusion or hollow type process where a variety of raw materials need to be mixed in proportion to their weight. Adopting single crystal chip microprocessor design, stronger function, smaller mention of anti-interference ability; Memory using EEPROM cut off the power supply after the set information will not be lost, free of batteries; The use of human-computer interface status display touch keyboard data input, operation is more convenient, and can store a large number of formula information (500 groups); High-speed and high-precision AD capture the weight of the more quickly and stably; All the boredom of gravity through the measurement of uniform mixing, can strictly control the accuracy. Uniform mixing, can strictly control the precision. The weight data and the selected raw materials used are calibrated to ensure the precision and accuracy of mixing.
The dosage machine integrates VB programming technology, microcontroller technology and sensor technology, etc. By taking the size of the feeding port, the pitch of the agitator, the rotational speed and the size of the discharging port as variable factors, one of them is taken as a variable factor when collecting the metering data, and the other parameters are written into the system as quantitative. The Weighing system transmits the actual discharging quantity to the batching machine through the communication port, and through the timer of this system, the discharging quantity, precision and efficiency can be calculated, and then all the information is transmitted to the database, and the metering data is processed to judge whether this screw feeder meets the relevant functional requirements. By using this system, the accuracy of data collection is greatly improved, the influence of human factor is reduced, the reliability of the device is improved, and the working performance of the device is more stable.