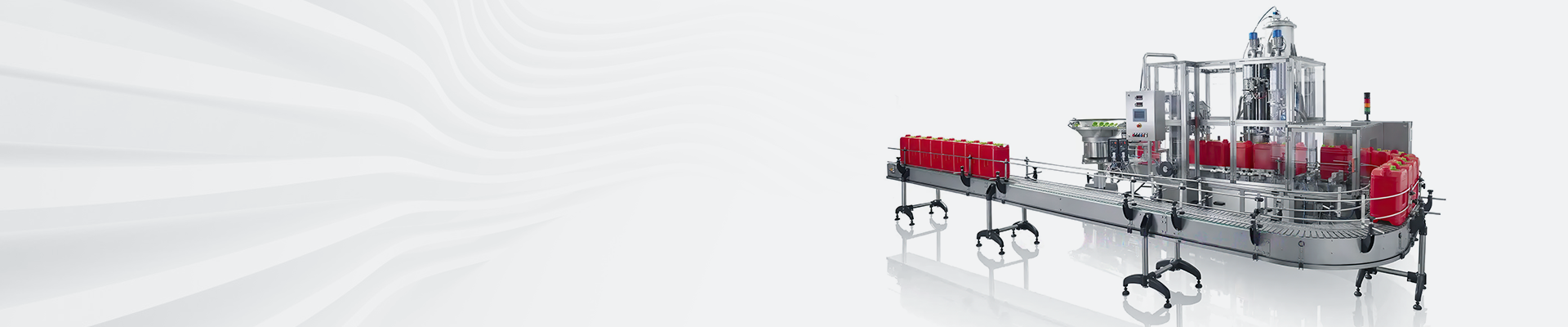
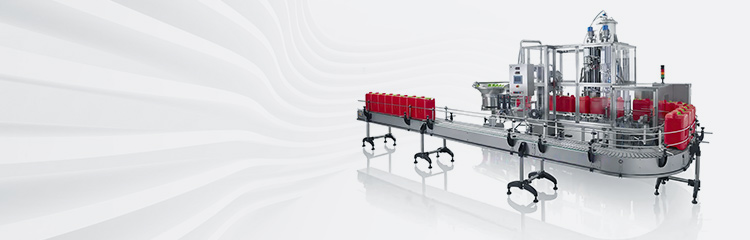

Summary:The fieldbus of the weighing and batching system is a product of the comprehensive application of microprocessor technology, network technology, communication technology and automatic control technology, which improves the accuracy of signal measurement, control and transmission.
1 Introduction
Raw material dosing is the core of plastic granule production process. Scientific proportioning and accurate measurement of raw materials is the first condition to ensure the quality of plastic pellets, and the design of automatic dosage system is the key to influence the quality of dosage process. At present, most of the weighing and batching system used in domestic plastic granule production line is distributed automatic batching system (DCS), and most of this batching control system is analog-digital mixing system, which has not yet formed a complete network from the measurement and control equipment to the operation and control computer, and it has great limitations in technology. Due to the use of a single signal transmission to poor reliability, poor interoperability, can not be very good on-site equipment for real-time control. Weighing and feeding system fieldbus is a comprehensive use of microprocessor technology, network technology, communication technology and automatic control technology products, improve the signal measurement, control and transmission accuracy. In recent years, with the promotion of fieldbus technology, the improvement of traditional automatic dosing into fieldbus-based weighing and feeding system has become an inevitable trend of scientific and technological progress. In this paper, combined with the actual engineering, introduces a fieldbus technology based on the design of automatic feeding system of plastic granules and achieved good results in practical applications.
2 fieldbus and fieldbus weighing and dosing
Fieldbus is a serial, digital, multi-point communication data bus between the field equipment/weighing instruments installed in the production process area and the automatic control devices/systems in the control room. The term "production process" includes both intermittent and continuous production processes. Or, fieldbus is a single decentralized, digital, intelligent measurement and control equipment as a network node, connected by a bus, to achieve mutual exchange of information, and jointly complete the automatic control function of the network system and weighing and batching system. Fieldbus development is rapid, has developed more than 40 kinds of fieldbus, of which the influential 5 kinds are FF, Profibus, HART, CAN, Lonworks.
Weighing and batching machine fieldbus technology will special microprocessor into the traditional measurement and control of weighing instruments, so that they have a certain degree of digital computing and communication capabilities, to become independent of certain control, communication tasks of the network node. They are through the twisted pair, coaxial cable, fiber optic and other means of information transmission, so that the formation of a number of measurement and control of weighing instruments, computers, etc., as a node connected to the network system. It can be considered that fieldbus is the extension of communication bus in the field equipment, allowing a variety of field equipment, such as transmitters, regulating valves, base-type controllers, recorders, monitors, PLCs and handheld terminals and weighing and dosage system, through the same bus for bidirectional multivariate digital communication.
Fieldbus weighing and dosage is another new type of industrial dosage system that appears after the centralized weighing and feeding machine (DCS). It is relying on microprocessor chips with detection, control and communication capabilities, digital weighing instrumentation (equipment) to achieve complete decentralized control in the field, and these scattered measurement and control equipment as a single point of the network node, connecting these points in the form of a bus to form a field bus weighing and batching system. Belongs to the lowest level of the network system, is the network integrated full distribution of weighing and batching, the original distributed DCS system field control machine functions, all decentralized in the various network nodes. For this reason, the original closed, specialized system can be turned into an open, standard system. It changes the original control system structure, so that the analog and digital mixing of distributed control, updated to all-digital control, with an open field bus network, the field of each controller and intelligent weighing instrument interconnections, constitute an operable field bus weighing and batching system. The control function is completely decentralized to the field, which really achieves decentralized control, decentralized danger, centralized monitoring and full digitalization. Therefore, FCS is an open, interoperable, thoroughly decentralized and distributed weighing and batching system, which is one step forward than DCS.
3 Profibus-based design of plastic granules
3. 1 Overview of Profibus Fieldbus
PROFIBUS is an open fieldbus standard introduced by SIEMENS, which is manufacturer-independent, and a wide variety of automation devices can exchange information through the same interface.PROFIBUS is used for distributed I/O devices, drives, PLCs, and PC-based automation systems.PROFIBUS consists of three compatible parts, namely PROFIBUS-DP, PROFIBUS-PA, PROFIBUS-FMS. where PROFIBUS-DP is a high-speed, low-cost communication connection for device-level weighing and dosing systems and decentralized I/O communication, which is real-time, with a data transfer rate of 9. 6kbps-12Mbps and a response time of a few hundred microseconds to a few hundred milliseconds. The data transmission technology is RS-485 and the transmission medium is shieldable twisted pair or optical fiber. In addition, PROFIBUS-DP provides the non-periodic communication required by intelligent field devices for configuration, diagnostics and alarm processing and the determination of parameters for complex devices in operation. The extended diagnostic functions of PROFIBUS-DP enable rapid fault localization, the diagnostic information is transmitted on the bus and collected by the master, and the open communication network allows for single- or multi-master systems.
PROFIBUS is outstanding in terms of its performance, openness, interchangeability and interoperability, as well as its industrial performance, so PROFIBUS bus was selected for the bus selection.
3.2 Overall system structure and working principle
The whole weighing and batching system is based on load cell combined with PANTHER weighing terminal, with S7-300 PLC as the control core, adopting PROFIBUS-DP field bus and computer to form an organic whole, combining with the peripheral execution equipment to complete the automatic control on the whole process of batching, conveying and mixing from the mouth of raw material silo to the batching and conveying silo of kettle, and at the same time displaying alarms and interlocks for the whole system. At the same time, it displays and monitors the alarms and interlocks of the whole system, and completes the management of the formula, production data and equipment operation status of the whole system, so as to meet the requirements of plastic granule production on the batching of mixed materials.
The batching system has three kinds of working mode: manual working mode, automatic working mode (PLC control), and fully automatic working mode under computer monitoring. In automatic dosage, the weighing station on site weighs the weight of the material in the silo, and the dosage system controls the discharging of the material according to the requirements of the formula using the "reduction method", the value of the discharging of the material in the reduction method is the value of the formula, and it adopts the method of weighing twice, and stops discharging when the value of the discharging of the material is satisfied. Discharge at the same time to start the transmission motor, the material will be sent to the mixing bin mixing, mixing to start the automatic water filling system to add water at regular intervals. After the mixing reaches the requirement, the storage tank motor sends the mixed material to the batching tank bin. The system completes the dosage task through this cycle again and again.
3.3 System network control composition
Take S7-300 PLC as the center, the upper computer and PLC are connected by MPI network, PLC and high-precision weighing instrument are connected by PROFIBUS-DP network, the weighing instrument is a slave in the system, and the PANTHER weighing instrument will be connected with SIEMENS PLC network through the special PROFIBUS fieldbus interface.
The weighing feeder adopts STEPV5.2 for hardware configuration to realize the functions of system equipment monitoring, recipe management as well as data collection and recording, etc. The logic processor of the PLC chooses SIEMENS S7-3152DP CPU, which comes with an MPI communication interface and a PROFIBUS-DP interface. The upper computer carries out the unified management of the lower computer, the formula, printing and statistics, transmits the weighing formula to the lower computer, starts the weighing operation, monitors the various operating states of the lower computer with the monitoring software, and the lower computer carries out the on-site control of the dosage system respectively.
The STEP7 programming software installed on the PC communicates with the PLC via MPI, but these communication protocols are not publicly available, so it is necessary to use the PRODAVE toolkit provided by Siemens.PRODAVE's Dynamic Link Database (DLL) provides a large number of DDL functions based on the windows operating system for the user to solve the problem of data exchange between the PLC and the PC and data processing. data processing problems between PLC and PC. The host computer uses the communication function to read and write the data in PLC directly without writing the communication program on the PLC side.
The PROFIBUS-DP interface is in charge of the communication with the weighing instruments, in order to transmit the weighing data and the relevant parameters to the main control station in a timely manner. The weighing instrument adopts the widely used PANTHER weighing terminal, which collects the weighing data through the field junction box, and its own PROFIBUS-DP interface can complete the communication with PLC conveniently.
3.4 System control software design
The switching input module of the weighing mixer receives signals from the control site and operation buttons as well as feedback signals from the motor status. The switching output module realizes the start/stop control of the motor, cylinder, solenoid valve, and indicator light, and the analog output module controls the speed of feeding and discharging materials to the feeder in the on-site weighing station. The weighing results of the weighing instrument are transmitted to the processor via the PROFIBUS-DP bus. The processor sends out control signals to the on-site equipments according to the received button signals, status feedback signals and weighing value signals, and the whole system runs automatically with the predetermined program.
3.5 Analysis of system characteristics
(1) weighing mixer due to the control structure of the FCS, compared with the traditional DCS saves a lot of hardware equipment. The use of FCS can reduce 1/2 ~ 2/3 of the isolator, terminal cabinets, I / O terminals, I / O cards, I / O files and I / O cabinets, which saves the space of the I / O device and device room; at the same time to reduce a large number of cables, so that the construction and commissioning is greatly simplified.
(2) Fieldbus can get a lot of rich information from the field devices, to better meet the factory automation and CIMS system information integration requirements. Fieldbus is a digital communication network, it does not simply replace the 4-20mA signal, but also to achieve the state of the equipment, fault, parameter information transfer. In addition to remote control, the system can also complete remote parameterization. Therefore, it improves the precision and reliability of weighing and batching system.
(3) As the field control equipment has the ability of self-diagnosis and simple troubleshooting, and sends the relevant diagnostic and maintenance information to the control room through digital communication, the user can query the operation and diagnostic and maintenance information of all the equipments, so as to analyze the cause of the faults at an early stage and eliminate them quickly. Shorten the maintenance downtime, at the same time due to the simplification of the system structure, connecting simple and reduce the maintenance workload.
(4) weighing feeder using STEP7 software unified programming and configuration, so that the debugging of the system is more simple and convenient, while greatly reducing the intensity of system maintenance.
4 Conclusion
The dosage system adopts the field bus which is open and has the interoperable network to interconnect the field controllers and weighing instruments, constituting the field bus weighing and dosage system, meanwhile, the control function is completely decentralized to the field, which reduces the cost of debugging, installation and maintenance. The system has been put into use in many projects of METTLER TOLEDO weighing and batching, with good operation, stable and reliable communication and control, so it has great popularization value in the field of industrial control.