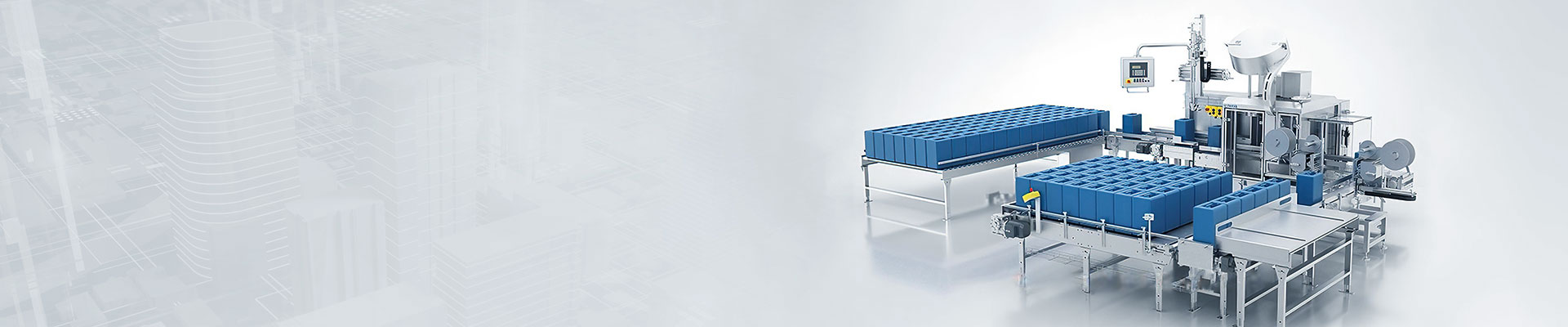
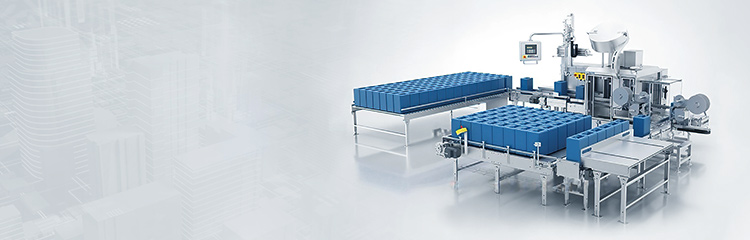
All the data input by the components of the weighing system serve the communication module. Click on the data change to display the latest data, and then the calculation can be carried out. The system will get the best S load, discharge quantity, control quantity and other production data required for batching according to the written process and algorithm.

All the data input by the components of the Weighing system serve the communication module. Click on the data change to display the latest data, and then the calculation can be carried out. The system will get the best S load, discharge quantity, control quantity and other production data required for batching according to the written process and algorithm. In order to get the best calculation result of ingredients, the operator can adjust the dosage of raw materials and auxiliary materials at any time to make the actual output and achieve the best effect. Weighing system (batching equipment) is a high-efficiency, high-precision and fully automatic Batching system developed for rubber, feed, food, pharmaceutical and chemical industries.
Automatic batching system can obtain stable size and uniform particles, innovative heating system, uniform distribution, temperature and the geometry of the bottom vat provide higher performance. Multiple parameters can be programmed by PLC and controlled by integrated touch screen. You can choose to use CIP cleaning system, or you can equip with channels and service platforms.
The weighing control system has the function of automatically weighing and distributing powder (carbon black, etc.), granular material (paraffin, etc.), oil and other materials according to the required production formula, and can adapt to high-precision batching of ±0.1g Weighing system can be used for single material batching, multiple material batching, mixed batching and other metering methods.
Mature and stable control+plc+weighing instrument is the main control, centralized control formula, the system is mature and stable, the batching control accuracy is high, and the production process data can be traced. The combination of centralized control of production operation and on-site man-machine interface makes manual operation simple, and the screen has visual information prompt. Batching conveyor, weighing equipment, high-precision weighing module, weighing instrument, industrial computer, frequency converter, electrical control cabinet, process simulation screen.