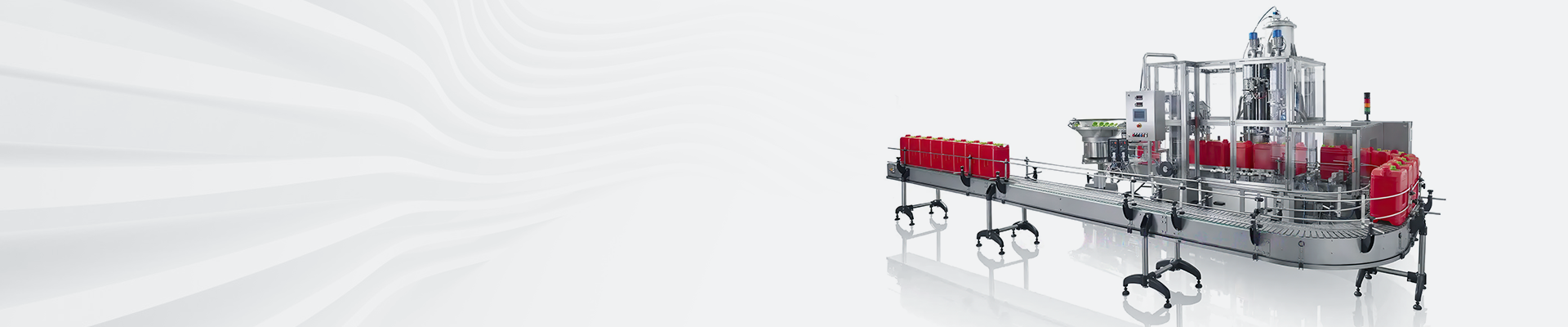
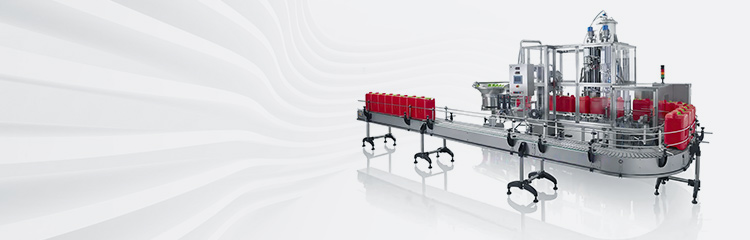

Summary:The automatic batching system for aluminum-plastic composite pipes adopts a multi-task operating system and communication capabilities. It uses a single-screw extruder with a main motor of 75kW DC and is driven by a digital DC speed control system.According to the current product production needs, the parameters and processes of the relevant formulas can be quickly changed in the first time to achieve the preset goals.
The automatic feeding system is equipped with a variety of standard control functions and supports a multi-task time-sharing operating system. Its hardware adopts a modular and flexible configuration, which can be plugged in and out with electricity and is highly reliable. Multi-processor and intelligent I/O technologies make it intelligent, and it uses open bus structure for easy communication with various systems. Provides a structured high-level language PL2000 (similar to C language), can also use ladder diagram (LAD), instruction table (STL) programming. And has a powerful data operation and processing capabilities. Batching equipment software, hardware features and CAS2005 as the master station, two CAS2003 for the slave station of the aluminum-plastic composite tube automatic batching.
Aluminum-plastic composite tube process
Aluminum-plastic composite pipe automatic feeding system using multi-tasking operating system and communication capabilities, the use of single-screw extruder, the main motor DC 75kW, driven by a digital DC speed control system. Its function is to extrude plastic granules into plastic tube as the inner tube of aluminum-plastic composite tube; vacuum sizing water tank is used for sizing and cooling of plastic inner tube; inner tube traction is crawler tractor, traction motor is three-phase AC motor, 1.5kW driven by frequency converter; inner tube gluing extruder, the main motor is DC 55kW driven by digital DC speed control system E590, and its function is to extrude hot-melt glue for bonding aluminum strip and plastic inner tube; the system is equipped with a single screw extruder, the main motor is DC 75kW driven by digital DC speed control system; its function is to extrude hot melt glue for bonding aluminum strip and plastic inner tube. The function is to extrude the hot melt adhesive to bond the aluminum belt and plastic inner tube; Aluminum belt uncoiling is to convey the aluminum belt used in the aluminum-plastic composite tube; Aluminum belt docking is to align and weld the head and tail of the two rolls of aluminum belt to ensure the production continuity and the product can be of any length; Welded tube hauling is the hauling of the aluminum belt wrapped around the plastic inner tube and the adhesive coated layer after it is composite molding and pressed into the tube shape, the main motor is a three-phase AC motor, 3kW, driven by the frequency inverter; The welded platform is to weld the tubular aluminum belt into the aluminum tube wrapped around the plastic inner tube. The welding platform is to weld the tubular aluminum strip into the aluminum tube wrapping the plastic inner tube, with argon arc welding machine, 9.7Kva; aluminum tube traction is also a crawler traction machine, the main motor is a three-phase AC motor, 5.5kW, also driven by the frequency converter; the outer tube gluing extruder, the main motor is a DC 55kW, driven by the digital DC speed regulating system E590, which functions in extruding the hot melt adhesive; the main motor of outer tube extruder is a DC 45kW, driven by digital DC speed regulating system E590, and the function is to extrude the hot melt adhesive; the main motor of outer tube extruder is a DC 45kW, driven by digital DC speed regulating system E590. The main motor of the outer pipe extruder is DC 45kW, driven by digital DC speed control system E590, and its function is to extrude the outer pipe of the aluminum-plastic composite pipe; the material-forming traction machine is also a crawler traction machine, and the main motor is a three-phase AC motor of 1.5kW driven by frequency converter; the cutter is a three-phase AC motor of 1.1kW with non-variable speed, and it is used for breaking the aluminum-plastic composite pipe in accordance with the length of the order; and the winding machine is used for winding the finished products of the aluminum-plastic composite pipe with the main motor of DC 1.5kW, and the speed of it is given by the analog module of Station 2#. The signal comes from the analog module of station 2#, and there is no communication link with CAS.
Characteristics of programmable computer controller
Compared with the industrial control computer (IPC), centralized automatic feeding system (DCS), programmable controller (PLC), it makes full use of the advanced and mature technology in microcomputer, field bus and software, adopts excellent and forward-looking design ideas, and represents the development direction of industrial automation products. High-performance 16-bit and 32-bit CPUs are adopted to ensure the operation speed. the I/O processors are mainly responsible for the management of the network and the dosage system. There are 3 processors on a module, which are both independent and interrelated (through DPR), so that the resources of the main CPU are reasonably used, and at the same time, the speed of the whole dosage system is maximized. At the same time, CAS adopts up to 100K~16M application memories in hardware (general PLCs are only tens of K), so that it can run larger software. Its multi-task time-sharing operating system, the entire operator interface can be divided into a number of different priority task level (TaskClass). TaskClasses with high priority have shorter execution cycles (which can be set by the user). Moreover, each TaskClass can contain multiple specific tasks, which can be subdivided into higher and lower priorities. Under the management of this operating system, the tasks with higher priority are always executed first, leaving the rest of the time for the execution of the tasks with lower priority. This allows the optimization of the whole automatic dosage system with a high real-time performance.
Dosing the introduction of intelligent distributed control ideas and fieldbus technology, so that has a powerful communication and network functions. Both through the PROFIBUS, CAN open standard field bus such as the composition of the application-oriented, future-oriented industrial control program, but also to provide users with FRAMEDRIVER (frame driver) to facilitate the realization of the third product connection and communication. In addition, remote programming and software maintenance can be realized via MODEM. The hardware and software of the equipment are modular, and can be combined according to the designer's control needs to form a special automatic dosage system with the characteristics of the manufacturer's application, and has the flexibility of free networking and expansion capabilities. The intelligent module of the equipment has its own CPU inside, and the closed-loop loop adjustment itself is completed by the intelligent module itself. The PID regulation of the process control can reach 50μs a loop.
Composition and function
1 Hardware composition
Aluminum-plastic composite pipe weighing and batching system selects CAS2005 as the master station, including power supply module PS465, processor module and interface module IF060, and two slaves select CAS2003, including temperature input module, analog input module, analog output module, digital input module, digital output module, and 1#slave controls the inner pipe part and 2#slave controls the outer pipe part, and the master and the two slaves control the inner pipe part through the CPU. The master station and two slaves realize real-time communication through the field CAN bus. The programmer running the programming platform PG2000 (available microcomputer running Windows operating system) is connected to the master station for programming, and Provit5000 is used for the operation, display and control of the master station. Two Panelware2000 are used for the display and operation of the two slave stations respectively. 4 sets of E590 DC speed control system drive the DC motors of inner tube extrusion, inner tube gluing and extrusion, outer tube extrusion and outer tube gluing and extrusion respectively, which communicate with CAS through the IF2 port of the processor module of the master station via RS422, and CAS adjusts the control parameters and the given values in a unified way. 5 sets of frequency converters are used for 5 sets of frequency converters are used to drive three-phase AC motors for inner pipe traction, inner pipe gluing traction, welded pipe traction, aluminum pipe traction and material forming traction respectively, which communicate with CAS by RS485 through the IF2 port of the master station interface module.
2 System Software Design
The weighing and feeding system utilizes the preparation of user programs, and a significant advantage over traditional PLC programming is its multitasking capability. Very suitable for the control of complex functions, high requirements for real-time aluminum-plastic composite pipe automatic dosage system. Based on the CPU time-sharing multitasking operating system and PG2000 programming software package provides flexible and diverse support, the control program of the entire system using PL2000 high-level language and LAD (ladder diagram) mixed compilation, according to its different functions of the independent program program block, and according to the real-time requirements to set the priority. Aluminum-plastic composite pipe automatic dosage system of the main tasks (application program module) and programming points are.
(1) traction speed control and coordination
Control of haul-off speed in the production of aluminum-plastic composite pipe is crucial. It directly affects the extruded pipe size and welding quality. If the traction speed is too slow, the weld head in the aluminum belt to stay a long time, easy to weld through the aluminum belt; if the traction speed is too fast, the welding speed can not keep up, the weld is not secure. Traction speed should also be matched with the extrusion speed, such as traction speed is too large, the surface of the tube will appear bamboo phenomenon; traction speed is too low there will be too large a diameter of the pipe and super poor.
The traction speed in the system is based on the welding speed, extrusion speed according to a certain formula to calculate the speed of the given value, through the master interface module of the IF2 port, RS485 communication to the frequency converter, and in the software will be set to compare the speed with the actual speed, the formation of the speed closed-loop control.
(2) Control of temperature
Extrusion temperature, mold temperature and preheating, cooling temperature directly affects the surface quality of the finished pipe. The temperature in the dosing system is controlled centrally, and the actual temperature and the set temperature can be displayed directly on the man-machine interface, so that the heating and cooling units can be monitored and processed, and the alarm can be given to the over-temperature and low-temperature. Self-learning function is also adopted in the software, i.e., the parameters required by the system at different times, different raw materials and different molds are automatically recorded and stored in the data module of CAS. The software can automatically calculate the PID parameters required for different temperature control, and the temperature control accuracy can reach ±1°C.
(3) Extrusion amount control
The extrusion amount of the weighing and batching system is adjusted by the communication port IF2 on the processor of the main station of the equipment, which communicates with the E590 DC drive system by RS422 and adjusts the speed of the DC motor (i.e., the speed of the screw of the extruder). The extruded amount is calculated by the formula according to the pipe diameter and the haul-off speed, with the inner and outer pipe diameters conforming to the standard and the surface being smooth and clean.
(4) Communication program
The communication procedure is critical in the application of the weighing and batching system to the aluminum-plastic composite pipe. Between the master and slave stations of the equipment, the master and the DC speed control system of the extruder, and the master and the frequency converter of the traction machine all rely on communication for data exchange. The communication between master and slave is realized via the CAN bus, a control bus with a good performance-price ratio. In order to facilitate the realization of CANBUS, the device products provide hardware modules supporting CANBUS and come with CAN interfaces. Therefore, it is easy to realize CANBUS physical connection and communication between CAS series products through simple parameter settings.
Traditional PLCs have poor scalability and openness, especially when introducing third-party devices and applying multiple communication protocols. The Frame Driver is a software toolkit designed to realize communication with third-party devices. Usually for data communication, the user must know the details of the port very well in order to program the pins of the interface.