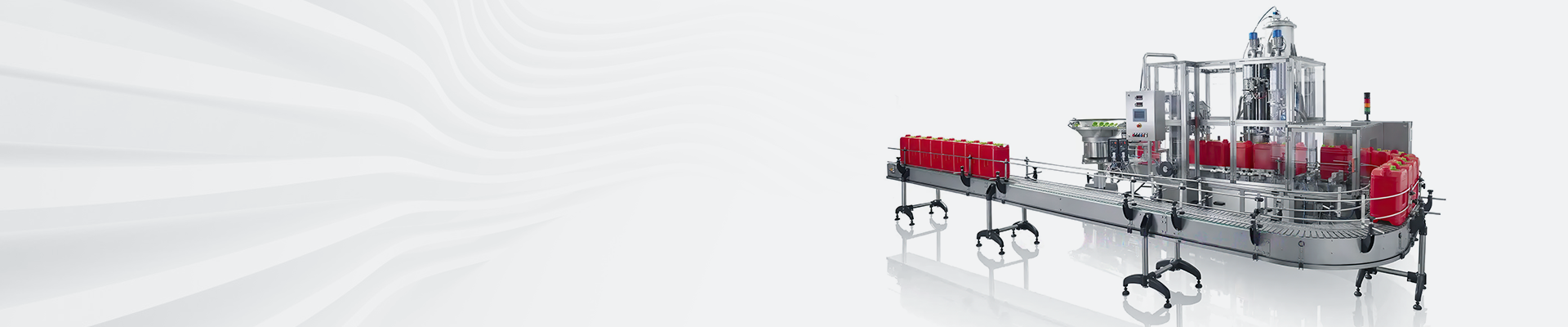
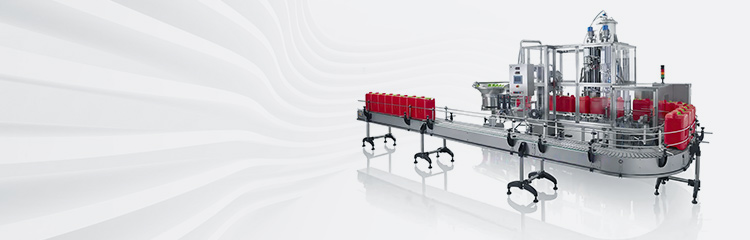


Summary:The application of automatic batching systems in mass production in the traditional Chinese medicine industry is becoming increasingly mature. It has the simple configuration of DCS and the high-performance computing and multi-tasking capabilities of PC.
1 Introduction
In this project, each production module of this pharmaceutical factory was and still is produced according to GMP standards, but the control technology is not perfect, and the designed production modules are accompanied by manual recipe input and instrument measurement operation. Therefore, this production module was the first to be upgraded.
In addition, the production department required a higher degree of automation and visualization of the entire plant, as the automated dosage systems for each segment were relatively independent. As a result, an automated dosage system centered on a touch screen was introduced in the 3rd quarter of 2009. The new system integrates a modular automated dosage system based on the S88 standard with a plant-wide control network as well as the company's corporate network.
2 Process description
Taking weighing and dosing as an example, there are 6 reactors producing multiple batches in parallel. Due to the highly variable nature of this product batch, it is often necessary to clean the equipment after a period of continuous production and re-change the dosage quantities to produce other batch sizes. This is because their basic process is the same.
From the point of view of the input feeding system, in the dosage into the line before the initial stage of the A reactor, it is necessary to check whether the B / C / D of these reactors has been properly completed the last formula of the feed, and the reactor pressure, temperature inside the reactor has reached the process preset values. Each product in each of its production steps are very strict reaction conditions detection, once a chain occurs, the process will require the control program according to the different reasons for the chain to the corresponding sub-steps until the chain conditions are completely lifted, in order to continue the operation of the dosage system.
3Batch System Design
Traditional batch applications initially came from advanced applications of DCS, such as the application of Emerson's DeltaV, Honeywell's PKS, Siemens' PCS7 and other systems. Due to the requirements of batch's own structure, the computerized automatic dosage system and controller provided for it must have features such as interface display, information integration on a database platform, and modular programming with configuration-based software. Traditional DCS system can basically meet the above requirements, but the general medium and low-grade PLC system is very difficult to meet the requirements of such a structure, because the PLC, whether combined with the configuration software or touch screen are required on both sides of the interface to define the communication and database address. This makes the PLC in the batch of applications in very few areas. The weighing and dosage system is very good to meet the basic requirements of the above points, because it is a programmable computer controller, but also has the HMI human-computer interaction function.
3.1 Hardware architecture
According to the process requirements of batch control and the number of I/O points to be controlled as well as the characteristics of field operation, the following Chinese medicine production batch system is constituted.
The loading system mainly consists of a weighing instrument and printer, a BR9300 bus connector, a Siemens S7-300 PLC (with a number of I/O modules), an OMRON PLC (with a number of I/O modules), a weighing instrument, and several barcode scanners. Through the built-in various communication interface cards (RS232/RS485/TCP-IP/CAN) and bus connectors to form an industrial data communication network. Among them, the automatic feeding system, as the core of the device, the server side and client side of the batch software, undertakes the tasks of process modeling, batch operation, recipe management, batch history database, reporting and security, querying the batch operation status, and setting up the relevant parameters in the batch operation process. In addition, it usually serves as an independent HMI for the process operator when the system is in normal operation, and also assumes the task of directly operating the field operations.
Combined with the analog and digital I/O modules of the underlying PLC, the touch station is also the main link in completing on-site measurement and control, executing all continuous volume control, logic control, and parameter setting and acquisition of batch function blocks, and realizing data acquisition and batch control of the process through the I/O modules of the underlying PLC.
3.2 Batch Software Design
3.2.1 Process Modeling
Establishing an appropriate model according to the process requirements of batch production is a crucial issue that all batch software engineers need to face. A good or bad model will directly affect the convenience of the batch grade library and parameter modification by the process engineers in the future daily application, and involves the creation of new products and new formulations.
In the use of modeling process, the use of the C language unique modular structure programming approach to each device by defining the module Functions Structures Members of the form, the definition of the name of the device (UNIT), the link between the device, but also need to be in accordance with the similar nature of the device and production capacity of the process level categorization. In the corresponding process level under the definition of a number of PHASE, PHASE will play a direct role in the process control, according to the measurement conditions to control the opening and closing of the valve and valve position changes. However, the most important thing here is to ensure the basic accuracy of the user modeling. Software for the user to provide an effective Batch configuration control environment SFC programming language and requires Batch software programming engineers in different stages of configuration, the use of the software provides a way to do a good job validating the work.
3.2.2 control logic encapsulation
Batch software itself contains a data management software, batch management control is through engineers to write C language program to establish UNIT PROCESSCLASS PHASE these functions. One of the most important is the PHASE, equipment PAHSE to control and monitor the execution of the batch.
PHASE is a stand-alone process control program that acts directly on the behavior of the production equipment. Although PHASE exists in different places, the interface between the batch management system and PHASE is certain. The project uses the custom library management that comes with it, and defines common interfaces in the form of function blocks on the interface input and output parameters, while polymorphic programming is achieved by using pointers to different structures for different parameter types.
3.2.3 Recipe Management
The dosing device builds the recipe editing structure by creating structure arrays in the software. The recipe structure is fully compliant with the ISAS 88.01 standard (American Society of Instrumentation standard). Each recipe consists of four parts: recipe header, equipment requirements, formula, and process.
The Weighing and Batching System Recipe Editor uses the graphical human-machine interface of an automated batching system to create an extremely intuitive, human-computer friendly and interactive configuration environment for the user. In this environment, the process personnel can quickly change the parameters and processes of the relevant formulas in the first time according to the current needs of product production to achieve the preset goals.
3.2.4 Electronic Records
The weighing and dosage system, in order to realize the process requirements of using electronic records, and to replace a manual system where all records are entered manually, a set of methods for recording electronic information confirmation and batch records through the Batch system was compiled, which employs the input of user names and passwords to record the current user's behavior. All the controls with manipulatable functions were programmed with their logging scripts, so that once any operation is performed by a current user, the system will record the current time, the operation behavior and the user name. In addition, the weighing of raw materials must be confirmed by two people (one confirming and one auditing) and the system is capable of using multiple electronic signatures. Thus, at all stages of a process it asks for the operator's electronic signature before performing any operation, and it is possible to view all the electronic records through a graphical interface.
When ingredients are added via barcode recognizers, the system automatically looks up the relationship between product resources and available raw materials. It also generates a unique identifying quantity for each batch process and places the appropriate number of bar-coded ingredients. As ingredients are added, they are scanned and confirmed by a barcode scanner. The great advantage of electronic record keeping is that it does not allow unorganized operations, reducing the chances of human error.
4 Conclusion
The batch software not only helps operators to query the data on site more conveniently and cope with unexpected events in the production process, but also reduces the maintenance workload of instrument engineers on the system. For the process engineers, it enables them to modify the formula according to the process demand on their own, independently of the auto-control maintenance personnel. Since the use of batch automatic dosage in this Chinese medicine factory, the advantages of high product production efficiency, stable equipment operation status, simple operation and complete historical data records have led to a great improvement in product quality and output, and factory benefits have also been improved. It shows that automatic dosage for small and medium-sized Batch has advanced, reliable, economic, flexible and other significant advantages.