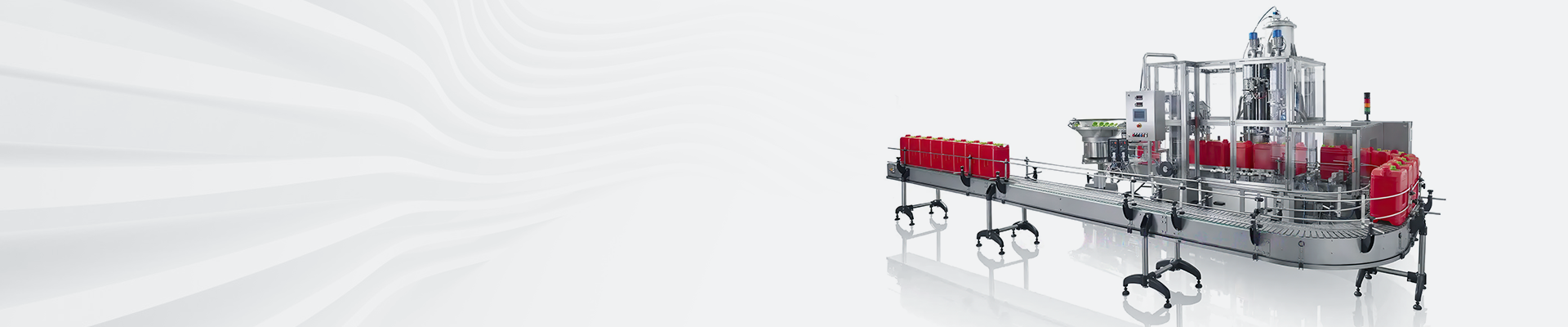
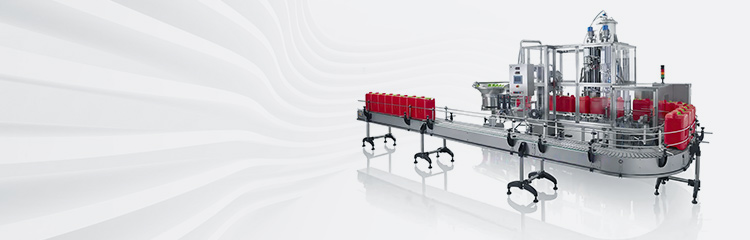

Summary:The batching system solves the problem of scientific and accurate construction of compound fertilizer data platform and decision-making.The weighing module scale body + data acquisition card + host (configuration software) form a strong network function.
Dosing is an extension of the application of measurement, dosing system is the core of the production site to solve the process control problems, the development of which has mainly experienced the following two stages: this stage of the weighing and dosing system is composed of: scales (load cell) + instrumentation, the feeding system better solve the process control and monitoring of the production site; the cumulative amount of data displayed on the record. With the continuous improvement of enterprise management level, many managers strongly realize that the production site management can not quickly and effectively feedback to the upper level managers. In response to this problem, technological development gained momentum, the emergence of the production site process control and timely data collection organic combination, and upgraded to the level of auxiliary decision-making, feeding system to solve the construction of the compound fertilizer data platform and decision-making scientific and accurate. Weighing module scale + data acquisition card + host (configuration software), constituting a strong network function.
This automatic dosage system is integrated with scale body (load cell) + data acquisition card + host (configuration software), which is mainly composed of scale body, industrial control computer, switch input/output card, data acquisition card and SuperView configuration software platform. The belt scale body adopts quantitative feeding and weighing. Configuration monitoring interface, field parameter modification and setting; data processing, exchange; data query, classification, reports, printing and process control and other functions. Control the belt scale and on-site switching quantity; weighing signal ground acquisition. Acquisition and processing of all kinds of weighing signals on site. Background monitoring, database management, formula management, data communication and report management.
Dosing Function
Real-time display of the load and operation status of belt scale and spiral scale;
Realize unmanned, automated management, data saving at regular intervals, set weighing range, sound and light alarm for exceeding the limit;
Weighing and batching system combines multiple fixed formulas and free formula setting;
Provide report editing function, define personalized report;
Provide automatic dosage calibration;
Free configuration of the automatic dosage system and editing of the personalized man-machine interface;
Data refreshing time <1 second;
Data can be saved to database server for internal inquiry;
Providing dynamic data tracking to monitor hopper operation condition;
Provide categorized data query (e.g. shift report, daily report, monthly report, process data, etc.) and printing function;
Provide OPC interface to realize data remote transmission;
The collected data can be converted into Word/Excel and other data formats as required.
Main technical indicators
Static linearity: 1%;
Dynamic cumulative error of automatic batching system: ≤0.01% scale error: ≤1%;
Repeatability: 1%;
Screen refresh time: <1s;
Data response time: ≤1s;
Signal transmission distance: 1000m.
IV. Urea automatic dosage system
Dosing main interface:
Flow curve
Realize unmanned and automatic management, save data regularly, set the range of melting ratio, and sound and light alarm for exceeding the limit;
According to the actual speed, it can automatically display the flow rate and cumulative weight of water, urea and melt, as well as the liquid level and temperature values;
The data can be saved to the database server for internal inquiry;
Provide report editing function to define personalized reports;
Provide categorized data query (e.g. shift report, daily report, monthly report, process data, etc.) and printing function;
Provide OPC interface to realize data remote transmission;
Material ratios can be set according to specific requirements;
Shift and user management can be set up according to requirements.