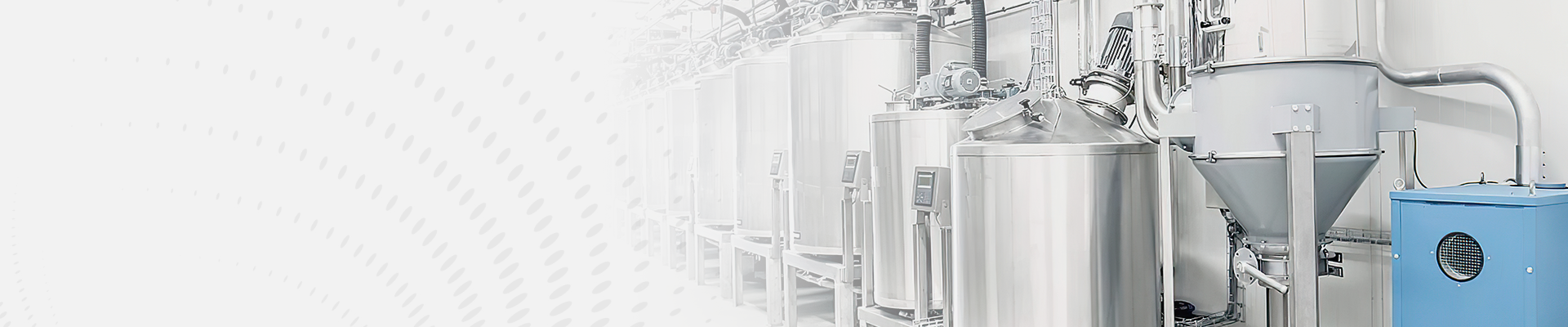
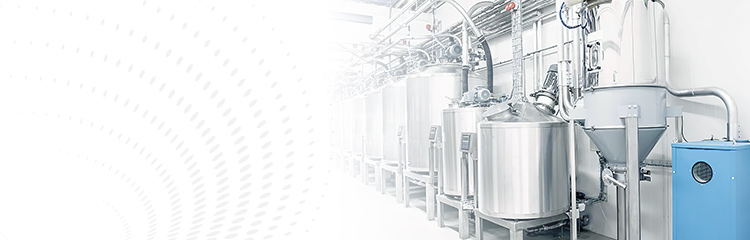
The belt scale adopts 8031 MCU as the control core of the system structure, constituting the belt scale controller BWF. the hardware part mainly consists of 8031 MCU, A/D converter (ADC0809) ROMD/A converter (DAC0832) Keyboard scanning circuit, display circuit, weighing module, amplifier circuit, latches, etc. The belt scale controller BWF is designed to control the flow of material, and to control the flow of material. Dosing is to rely on adjusting the speed of the belt conveyor to control the feed of raw materials, to complete the proportion of various raw materials, belt scales are used to measure and control the speed of the belt conveyor and material flow of real-time controllers, from the top of the belt structure there is a hopper, the belt movement of the material with the belt to transport it out of the conveyor belt driven by the slip motor M (electromagnetic speed-regulating asynchronous motor), the speed sensor SR The frequency of the output signal is proportional to the speed of the belt, the lower part of the conveyor belt is equipped with a weighing module, which outputs a voltage signal proportional to the material on the belt, the belt dosage scale controller BWF receives the speed signal of the SR and the weight signal, calculates the instantaneous flow of the material on the belt and displays it, compares the actual value of the flow rate and the set value of the flow rate, and outputs a current control signal through PID regulation via a preamplifier and a power amplifier Q to amplify the control signal. Through PID regulation, the output current control signal is amplified by preamplifier and power amplifier Q to control the conduction angle of SCR VT and thus regulate the rotational speed of the slip motor M, so that the material flow rate is stabilized at the expected set value.
Before the belt conveyor is put into operation, the set value of the material flow on the conveyor belt is set by the operator on the keyboard. After the system is put into normal operation, the microcontroller samples the belt load signal (converted by ADC0809) and speed signal (T method of speed measurement), and multiplies the belt speed signal with the instantaneous weight of the belt per unit length to calculate the instantaneous flow rate of the material on the belt F(t). Instantaneous flow can be displayed through the six seven-segment digital tube for the operator to provide process data for reference. 8031 system and then compare the actual value of the flow with its set value, calculated by the incremental PID regulation operation to control the amount of Vi through the DAC0832 is converted to a current output signal (4 ~ 20mA), and then amplified to control the SCR's conduction angle, to achieve the function of regulating the excitation current of the electromagnetic slip motor clutch, and to achieve the function of regulating the excitation current of the slip motor, and to achieve the function of regulating the current of the electromagnetic clutch. Clutch excitation current function, so as to adjust the rotational speed of the actuator slip motor, so that the material flow on the conveyor belt as far as possible to stabilize in the vicinity of the set value, and has good static indicators and dynamic performance.
The belt scale is an automatic dosage system composed of centralized control center, communication network system, control substation, protection sensor and industrial TV system. Among them, the centralized control center is responsible for the monitoring and control of the whole system, and the upper computer system is responsible for the information exchange and transmission between the operator and the field equipment. The operator obtains the information of the field equipment through the human-machine interface, and sends out the control instructions to the field equipment when necessary. The communication network system adopts industrial Ethernet for data transmission, and the transmission medium is optical fiber, which is responsible for the communication between the upper computer of the control center and the field equipment, and transmits the information acquired by the field equipment as well as the internal information of the program to the upper computer management system on the ground, and at the same time, it can also transmit the control commands issued by the upper computer system to the controller. Control substation consists of a control box and operating station, the dosage system can be written according to the need for the corresponding control program to achieve specific control functions, responsible for the realization of the various control systems in situ manual, centralized control and other functions. TV system uses optical fiber as the transmission medium, adopts the point-to-point way to transmit the video signal to the ground, realizes the real-time monitoring of the site information through the industrial TV technology and combines with the computer image processing technology. The system can store the production real-time monitoring data in the production real-time data history database, can realize the history back to the display, history trend analysis, history report and other comprehensive analysis, save a certain alarm event information in order to check and analyze the cause or report to the higher leadership, can be saved as a text of the data information in the computer hard disk. The belt centralized control system combines the belt emergency stop, deviation, coal stacking and slipping during the belt transmission process, and provides a comprehensive analysis of all the alarm events.
System function
(1) belt scale transport centralized control is mainly composed of transport belt machine, coal feeder and other basic equipment using the control equipment communication module so as to achieve the remote control of the belt, so skidding piles, over-temperature, smoke longitudinal tearing, extinguish the dust speed of the run-off, coal level, and so on, many protections must be implemented to monitor, in the remote control must be viewed before it is normal, whether or not to achieve the centralized control of the belt machine and monitoring requirements;.
(2) control system using KDK8 drive control cabinet, KJD30Z data transmission network, to achieve different scale control. Completion of the system belt, coal feeder monitoring and control of the whole process, together with the centralized control room constitutes a perfect belt monitoring system.
(3)Realize the centralized monitoring of the belt conveyor system, real-time monitoring of equipment status and operating parameters and displaying data curves, and recording important information on hard disk.
(4) control mode can be in the centralized automatic / centralized manual / on-site, three ways to convert each other during normal production using the centralized automatic mode equipment in accordance with the process requirements of the order and flow of the central console automatically start and stop: centralized manual can be operated in the central console of the equipment without locking and linkage relationship: on-site. On-site operation.
(5) before starting the equipment by the centralized control console to send a preview signal, and through the belt voice down the call preview preview preview after 30 seconds if the site meets the conditions of centralized automatic start equipment can be automatically started in order. Emergency site and control room can be used to stop the start of the stop button.
(6) according to the "technical regulations" tape conveyor installed pull-wire switch, run-off protection, and can be used in the field and control room can be stopped by the stop button to stop the belt running when the first run-off in the control room to send a first alarm alarm fault alarm second run-off can make it stop the fault low-speed protection and so on.
(7) equipment failure and process parameters of the abnormal real-time alarm and sound and light prompts. General fault only alarm site abnormal parking or serious failure fault equipment and its upstream equipment emergency stop, downstream equipment downstream of the coal flow delayed blocking stop.
(8) Installation of voice intercom bells along the belt to facilitate the contact of operation and maintenance personnel.
Advantages of the system in production
(1)There is an on-site operation control box next to the head of each equipment, on which there are working mode changeover switches and on-site start-stop knobs.
(2) All coal feeding points on the belt conveyor are equipped with coal pile protection and longitudinal tear protection to prevent the expansion of belt conveyor accidents.
(3) All tape machines are equipped with a two-pole deflection switch, the first deflection switch is used for fault alarm, and the second deflection switch is used for fault stop.
(4) All belt conveyors are equipped with pull-wire switches for emergency stops, and the installation spacing of the emergency stop pull-wire switches is determined to be configured in accordance with 100 meters in order to ensure the safety of the equipment and people.
(5) Horizontal belt conveyor tensioning device for the hydraulic adjustment mode, to provide a set of belt conveyor loose belt detection sensors, controlled by the drive controller to complete the automatic adjustment of the tension of the belt conveyor function.
(6) Provide a coal pile sensor at the head of the belt conveyor to prevent the occurrence of coal pile accidents on the belt.
(7) Belt speed sensor is set in the belt machine to detect the occurrence of overspeed and skidding accidents of the belt.
(8) Installation of a smoke sensor at the belt header to detect the occurrence of belt burning accidents due to friction between the header and the belt.
(9) Temperature sensors are installed in the main pulley of the belt conveyor to detect the temperature of the pulley at any time, and automatic water dispersal devices are equipped to realize automatic water dispersal and cooling of the main pulley when the pulley is over-temperature.
(10) Belt conveyor every 100 meters to set up a start-up warning device equipment before the start of the warning signal, prompting the relevant personnel should immediately stay away from the equipment.
(11)The real-time monitoring function of motor current can find some potential faults of mechanical equipment; real-time monitoring and analyzing of motor current during operation, alarming when the current exceeds the limit or changes suddenly, and stopping the machine when it is serious.
(12) Realize the locking of coal feeder and belt, and realize the locking function with the previous belt. With automatic, manual, maintenance and other control methods.
(13) Emergency shutdown, sequential shutdown or alarm sound and light signals can be carried out according to the nature of the fault of the tape machine system.
(14) In the centralized operation console can be centralized display of the working status of the tape machine, fault type fault location.
(15) This device can be configured according to the requirements of the driving sensor, in order to realize the coal driving without coal stop.
(16) According to the requirements of this system to install electronic scales, in order to calculate the coal production of the mine a day.
Stability of system software
(1)Adopt industrial Ethernet communication technology: the connection between each belt conveyor control substation and industrial camera uses mining single-mode anodized fiber optic cable, and all data and image information is transmitted by industrial Ethernet.
(2) Adopting networked industrial TV monitoring mode: real-time monitoring of the belt conveyor head, tail, coal feeder and monitoring links through industrial (explosion-proof) network cameras.
(3) Remote centralized control mode: through the ground computer to realize the control of underground belt conveyor control mode and belt conveyor protection action operation.
(4) Adopt redundant control technology: the centralized control room control adopts two computers as hot standby to improve the safety and reliability of the system.
(5) Adopt multiple control modes: it has multiple control modes such as underground local control, ground single equipment control, process automatic control, etc. Each control mode has priority interlock control.
(6)Adopt configuration software design: the system screen is beautiful and practical, and the man-machine interface is friendly and easy for operators to master the operation. Programming, modification is simple and flexible. Easy for engineers and technicians to master.
(7) with perfect control and protection links: belt machine protection substation access to a variety of mine safety regulations of the sensors and devices, the belt scale operation information collected to participate in the control. And there are voice previews, alarms and other signal prompts when starting, stopping, malfunctioning and other actions.
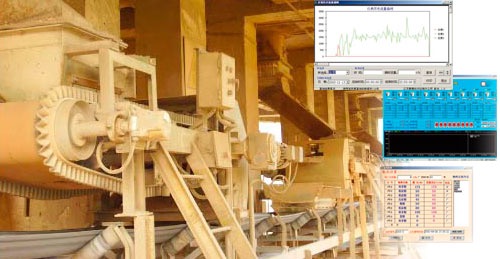
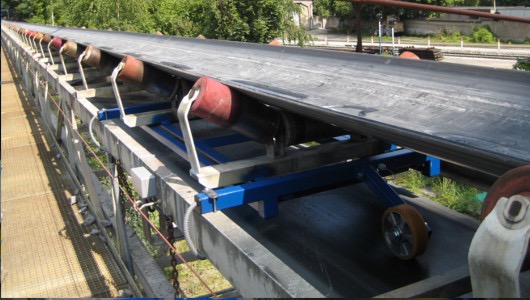
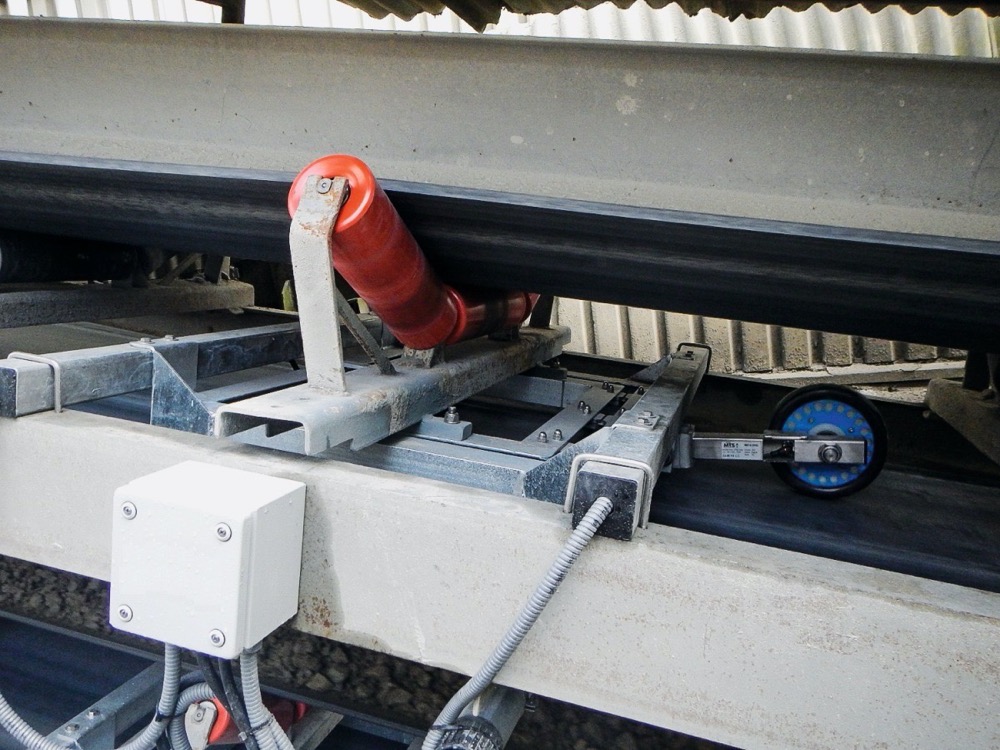
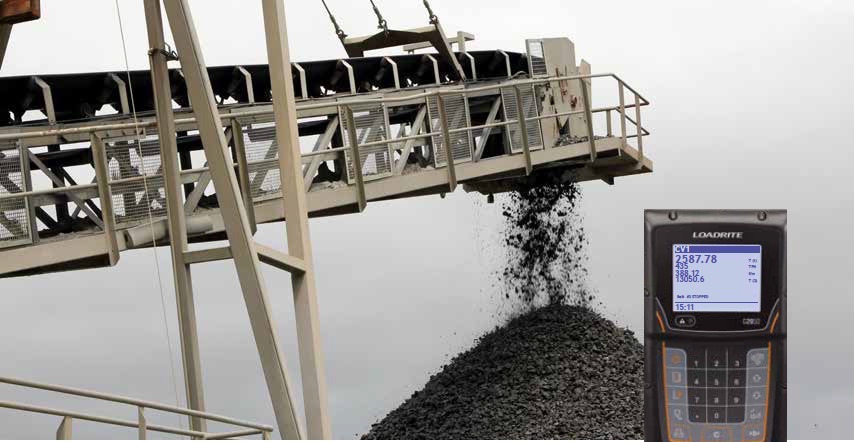