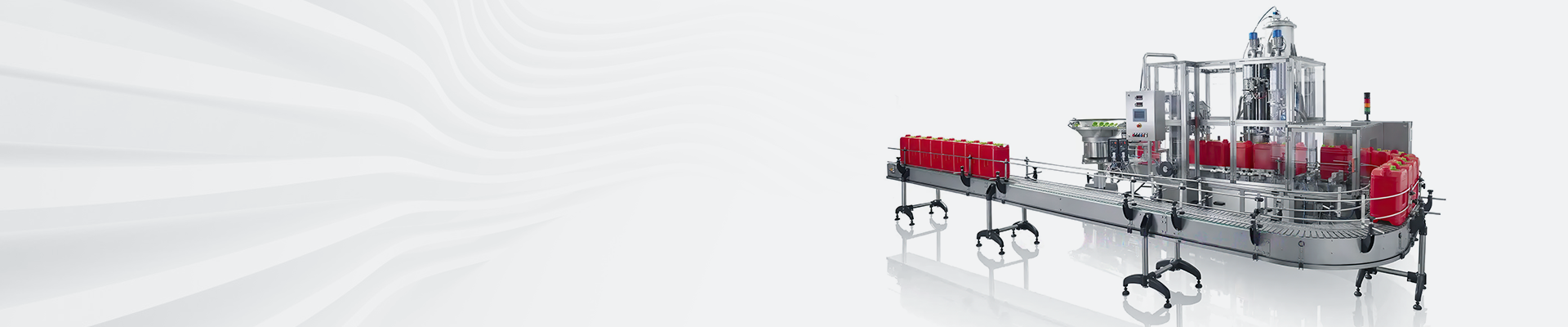
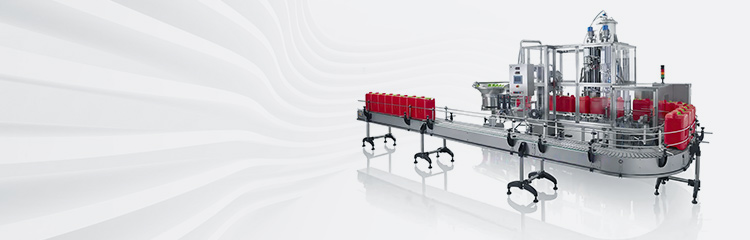

Summary:The belt scale converts this value into a corresponding voltage signal according to a certain conversion formula, and after a series of processing, it is converted into a digital quantity A and transmitted to the arithmetic unit. The speed sensor outputs the pulse number B after receiving the speed of the object transmitted on the belt and transmits it to the arithmetic unit. After receiving the data A and B, the arithmetic unit can calculate and process the total amount of the object in a measurement period, and the total amount of all the objects passing through the belt scale can be obtained by counting and accumulating each measurement.
Belt weigher is that the weight of the material on the transport belt linearly acts on the weighing module through the scale frame, so that the strain body in the sensor produces micro-strain, and then the resistance value of the resistance strain gauge of each arm of the bridge attached to the strain body changes. Under the excitation of the bridge voltage, there will be unbalanced potential output, and at the same time, the speed sensor measures the running speed of the belt. These two signals are sent to the microcomputer integrator to measure the instantaneous flow of the material after a series of operations. This type of belt weigher is the most basic and widely used. It receives analog signals from weighing module and speed measuring sensor in the system, displays instantaneous flow and accumulated flow after integration, and sends the instantaneous flow as an input signal to the computer system at the same time. The computer compares the signal with the set value and outputs the 4~20mA analog current signal to control the rotation speed of the feeding motor through the frequency converter, thus realizing the closed-loop control of the material discharge flow, and finally keeping the instantaneous flow and accumulated flow of several materials in batching.
The weighing belt conveyor consists of a bearing device, a weighing module, a speed sensor and a weighing display respectively. The bearing device is responsible for weighing the weight of the object on the belt and transmitting the data to the weighing module. The weighing module converts this value into a corresponding voltage signal according to a certain conversion formula and converts it into a digital quantity A through a series of processing and transmits it to the arithmetic unit. The speed sensor outputs the pulse number B after receiving the speed transmitted by the object on the belt and transmits it to the arithmetic unit. After receiving the data A and B, the arithmetic unit can calculate and process the total number of objects in a measurement period, and the total number of all objects passing through the belt scale can be obtained by counting and accumulating the measurement numbers at each time.
The belt scale also includes information acquisition part, driving device, information processing part and measuring instrument. The driving device consists of a variable frequency motor and a reducer. The variable frequency motor controls the speed of the belt, and the belt speed can be changed by changing the speed of the variable frequency motor belt, and the belt speed can be well controlled with the reducer. At present, the common belt is skirt belt, because it not only has high temperature tolerance but also can prevent the materials on the belt from falling. Such a belt has a long service life and can concentrate materials to avoid unnecessary waste. The carrier can measure the material on the belt and transmit this data (the accuracy of weighing can reach 1%), which has the functions of load, weight and gravity transfer. The signal acquisition part is mainly responsible for collecting data, including data transmitted by metering module and speed sensor. The data processing part is mainly responsible for processing the data transmitted to the arithmetic unit by the weighing module and the speed sensor. Specifically, it includes signal sampling, signal filtering and amplification, A/D conversion, etc. The instantaneous flow rate and cumulative flow rate of the belt scale can be counted, and the flow rate of the belt scale can be well adjusted and the adaptive parameters can be set according to the results of data processing.
Belt weigher can measure the coal quantity at the end of a cycle or the accumulated coal quantity for a period of time, and the accumulated coal quantity is the result of accumulation. To measure the instantaneous coal value, it is necessary to measure the weight per unit length of the belt and the instantaneous speed of the belt. The instantaneous speed of the belt can be obtained according to the rotating speed of the belt scale. If the measured value of raw coal transmitted on the belt is q(kg/ m) in a certain unit length, and the transmission speed of the belt is v(m/s), then Q=qv, and 0 represents the instantaneous coal quantity. Because the coal flow at each moment is changing, the cumulative flow should be the integral value of instantaneous flow versus time.
Generally, the belt control cabinets are placed near the belt scale, which is convenient for on-site debugging and maintenance of the belt scale and regular calibration and correction of the belt scale. At the same time, it is convenient to change the flow setting and parameter setting of the belt scale by moving the belt scale nearby. Electrical control system and weighing instrument are also placed in the control cabinet of the belt weigher, which can reflect the running situation and recorded data of the belt weigher on site to the coal injection central control room in real time, and the central control room can change the flow setting of the belt weigher or start or stop the belt weigher according to the production needs or other considerations.
The belt control system mainly includes two systems: signal acquisition and signal processing. The function of the signal acquisition system is mainly to collect signals such as motor start-stop state, belt tearing and slipping, and to collect the switch and analog information of the equipment. The realization of this function is mainly completed by relays and various sensors. The function of the signal processing system is mainly responsible for the calculation and display of signals. The system is mainly composed of PLC and man-machine interface industrial computer.
S7-200 controller produced by Siemens is selected as the programmable controller. The PLC can adapt to the harsh underground working environment, and has strong anti-electromagnetic interference ability to other underground electrical equipment, high working reliability and flexible configuration. The CPU selected by PLC is CPU226, and the PLC uses EM231 analog input module as the expansion module. The main function of PLC is to collect all kinds of signals on site, calculate the collected signals through the program, control the start and stop of the equipment according to the calculation results, and transmit the signals to the upper computer, thus realizing the real-time monitoring of the belt conveyor. The function of system control is mainly to realize sequential control of coal feeder, belt weigher and vibrating screen, and the function of system protection is mainly to give an alarm for belt slippage, deviation and tearing.
The control system is mainly composed of control function and man-machine interface. The control function is realized by programming PLC, which is responsible for controlling the sequential start-up of conveyor and coal feeder, the start-up and stop of conveyor 1 and conveyor 2, giving an alarm signal when the equipment fails and handling the failure. The man-machine interface is realized by WINCC6.0 configuration software, which can process the signals collected by PLC and present the field equipment information to the controller in the form of sound, animation and image.
Mode of operation
A) automatic operation mode. The automatic control mode is realized by PLC program and configuration software, and the controller controls the start and stop of the equipment through the industrial computer. When the system is changed to automatic control, the system can automatically control the start and stop of the belt conveyor according to the sequence set by the program, and can analyze and calculate the collected signals, and realize the interlocking and alarm functions according to the analysis and operation results. In case of equipment failure or accident, the system can automatically stop and send an alarm signal. At the same time, it is assumed that each fault situation will be stored in the configuration system, and technicians can analyze the causes of equipment faults according to the stored fault information. The system can start emergency stop in case of emergency and stop all equipment in case of emergency.
B) Manual operation mode. In the manual operation mode, the controller can control the start and stop of any equipment. The system sets the mutual pin and unlock status for each belt conveyor. In the interlocking state, the controller can start and stop each belt conveyor according to the set sequence. In the unlocked state, the controller can control the start and stop of the belt conveyor out of sequence.
starting system
There are two ways to start the equipment: coal start and normal start. When there is no coal on the belt conveyor, start the 1 conveyor, and then start the coal feeder. When the 1 conveyor transports coal to the 2* conveyor, the 2* conveyor starts. This startup method can avoid the 2 "conveyor idling, which is called starting along the coal flow. When there is coal on the belt conveyor, start the 2 "belt conveyor first, then start the 1" belt conveyor, and then start the coal feeder, which is called reverse coal flow start.
Frequency conversion control
The motor of the belt scale is controlled by frequency conversion, and the soft start and stop of the motor can be realized by frequency converter to reduce the impact on the power grid when the motor of the belt conveyor starts and stops. The variable is communicated with PLC, through which the belt conveyor can be controlled to rotate at a constant speed.
Detection protection
In order to protect the safety of the system, the system can monitor and protect the belt scale and motor in real time. A pair of running deviation switches are installed at both ends of the belt scale and every 40m, which can give an alarm in case of primary running deviation, and can stop in case of secondary running deviation. The belt scale is equipped with pull switches every 40m to stop in case of failure, so as to ensure the safety of personnel and equipment. The real-time monitoring of the current and temperature of the belt conveyor can be realized through the connection of PLC and frequency converter. When the motor current or temperature is too high, the equipment stops running, and the system handles the fault to protect the motor of the belt conveyor. In addition, the system also sets other sensors such as smoke and tear to monitor the running state of the belt conveyor.