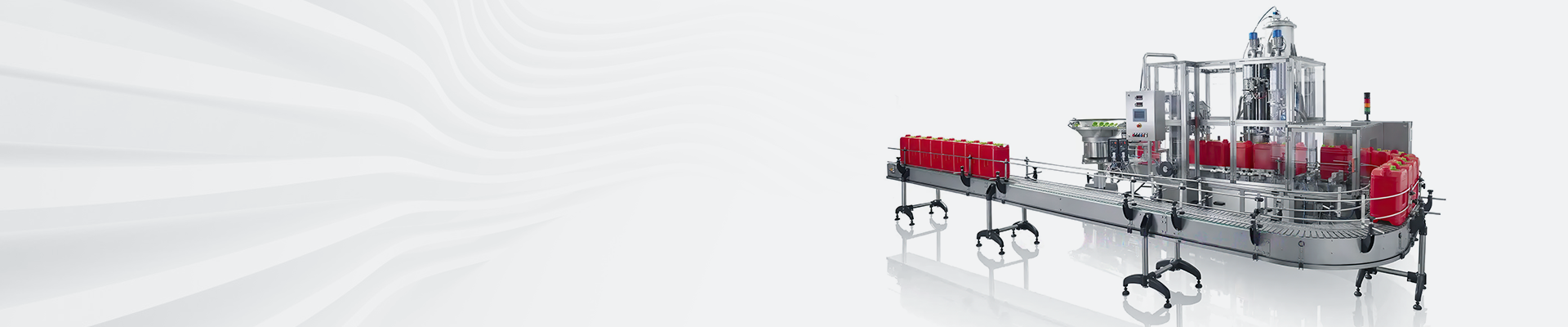
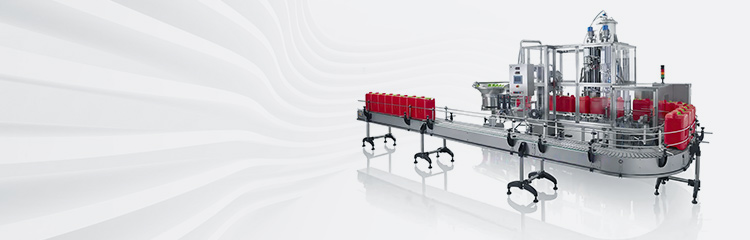

Summary:The belt scale monitors and controls the whole process of belt transportation through the monitoring screen, keyboard and mouse. You can choose automatic, manual and very manual modes to operate the belt scale and its transportation equipment. In the automatic mode, the reverse start and stop of process equipment are realized.
According to the actual situation on site, the belt weigher improves the detection of process equipment and automatic flow weighing control. The weight of that material on the convey belt linearly acts on the weigh module through the scale frame, so that the strain body in the weighing sensor generates micro-strain, and then the resistance value of the resistance strain gauge of each arm of the bridge attached to the strain body changes, and under the excitation of the bridge supply voltage, an unbalanced potential is output, and at the same time, the speed measuring sensor measures the running speed of the belt, and these two signals are sent to a microcomputer integrator to measure the instantaneous flow of the material after a series of operations. A self-made anti-blocking switch is installed at the discharge port of the belt conveyor, a pressure-sensitive belt tearing detection device is installed at the idler on the receiving port of the belt, a light-sensitive belt tearing detection device is installed at the bottom belt of the head pulley, a slip detection switch is added at the head pulley of the belt conveyor, a deviation detection switch is installed at the head, tail and middle section of the belt conveyor, and a travel switch is added at the tail pulley of the belt scale to detect belt blocking or pressing. Improve the network system, add some switches and lay optical fibers. Improve the video monitoring system, optimize the control program, improve the basic automation control program for the added detection equipment, and develop the belt operation and maintenance management system, flow statistics system, parameter diagnosis system, process inspection and maintenance system, belt cleaning management, belt consumption management, energy consumption cost analysis and statistics, etc.
Through the monitoring screen, keyboard and mouse, the whole process of belt transportation is monitored and controlled. You can choose automatic, manual and very manual modes to operate the belt scale and its transportation equipment. In the automatic mode, the reverse start and stop of process equipment are realized. All operation data and alarm and event information can automatically generate reports and print them by printer. When belt slipping, chute blocking and belt tearing are detected, the screen will give an alarm and interlock the equipment to stop. When the belt deviation is detected, the alarm will be given once, and the interlocking equipment will be stopped with a second delay. The centralized monitoring of various protective switches of belt weigher is realized. When a protective switch fails, the centralized monitoring computer can accurately display the location of the failure and the generated production report.
The belt centralized intelligent control system has great flexibility, strong processing ability and large I/O capacity when configuring the system. The programmable control with good adaptability is controlled by program. When the user's requirements change, just change the program. Therefore, the system can be flexibly and conveniently configured to form control systems with different scales and functions, and the adaptability is very strong. It can control both a single machine and a production line, and at the same time, it has multiple operation modes, and the operation is simple and flexible, which can be controlled both on-site and remotely.
The PLC program is simple, intuitive and user-oriented. Programming is simple and easy to learn, and it is convenient to modify the program and adjust the values of timer and counter to meet the requirements of field equipment operation.
When the belt is dangerous to equipment and people, the operator can stop the process instantly through the stop button on the field console or HMI, and after the operator resets the emergency stop button, he will inform the operator in the main control room to restart the process.
The belt longitudinal tear sensor is installed under the belt. When the belt longitudinal tear fails, the transported material falls on the sensor, and the sensor will give an alarm and stop.
Belt deviation switch can be used to monitor and protect belt transportation deviation, and belt slippage protection: speed sensor is used to detect the speed and acceleration of belt conveyor to realize slippage protection.
The contact weighing module is used for flow monitoring, which can make the belt system start and stop according to the material situation in the automatic state, saving electric energy and statistical flow.
When a slight fault occurs, such as slight belt deviation, HMI displays a fault alarm, and at this time, the equipment can continue to operate normally, and only an alarm is issued to remind the operator; When the belt slips and runs seriously, the fault point and its upstream equipment stop instantly, and the downstream equipment at the fault point keeps the original working state unchanged. After the fault is resolved, the equipment can be restarted from the fault point to the upstream, or the equipment can be delayed from the downstream of the fault point when the fault is not resolved. On the HMI, you can see the latest faults and equipment start-stop status in real time in the form of scroll bars and reports.
If there is an emergency at the site, the site personnel can immediately pull the accident rope switch. At this time, the fault point and its upstream equipment will stop instantly, and the downstream equipment at the fault point will remain in the original working state. After the emergency switch is reset, notify the personnel in the main control room to press the "sequence start" button, and then automatically resume production from the fault point.
The intelligent belt management and control system can display the start-stop status and power indication of each belt conveyor on HMI, and display the signals of deviation, locking, longitudinal tearing, overtemperature, slipping, stacking, watering and motor failure of each belt conveyor on HMI, and can query and display the belt protection point, communicate and configure the loudspeaker phone and the language alarm device before starting.
Maintenance personnel can contact with each belt substation through the loudspeaker telephone set along the belt. During fault protection, the system will give a language alarm through the language device along the belt, which is convenient for maintenance personnel to find the fault point and save the fault inquiry time. In the automatic operation mode, the equipment can be started and stopped automatically according to the program set inside the PLC, and the equipment can be operated independently as needed. When the equipment is overhauled, the operation mode can be switched to the overhaul state, and the maintenance personnel can start and stop the equipment through the intrinsically safe local box placed at the nose and tail.
Through the statistical analysis of equipment operation status and belt protection action information, the content of spot inspection is dynamically updated to reduce false inspection and missed inspection. The routine inspection information is archived and managed by manual input, and the routine inspection data is evaluated by the equipment basic parameter diagnosis module, and the maintenance plan is automatically generated. Realize the management of belt cleaning grade, reorganize and classify the belt according to its usage, establish the management standard of belt grade, and stipulate the cleaning grade. For each cleaning, the operator will input the implementation into the system, and the system will dynamically adjust the belt cleaning grade and cleaning plan according to the actual operation, and finally realize the continuous improvement of belt cleaning interval. The system automatically records the running current, running time and downtime of each belt conveyor in the running log of the belt scale. The system automatically records the number of protective actions of each belt conveyor, and records the operation faults and treatment methods of belt scales in each shift through manual entry. Through the statistical analysis of the historical data of the running current of the belt scale, the rationality of the design of the motor capacity of the belt scale is evaluated, and the problem that the running efficiency of the belt conveyor is reduced due to the "big horse-drawn car" is solved. Through the statistics of safe running kilometers and downtime of each belt scale, the reliability of equipment operation is quantitatively evaluated. According to the process, the energy consumption of belts and the weight of transported materials are counted, and the power consumption of tons of materials in each shift is obtained, and the transportation volume and energy consumption are quantitatively assessed to reduce the increase of energy consumption caused by belt idling.