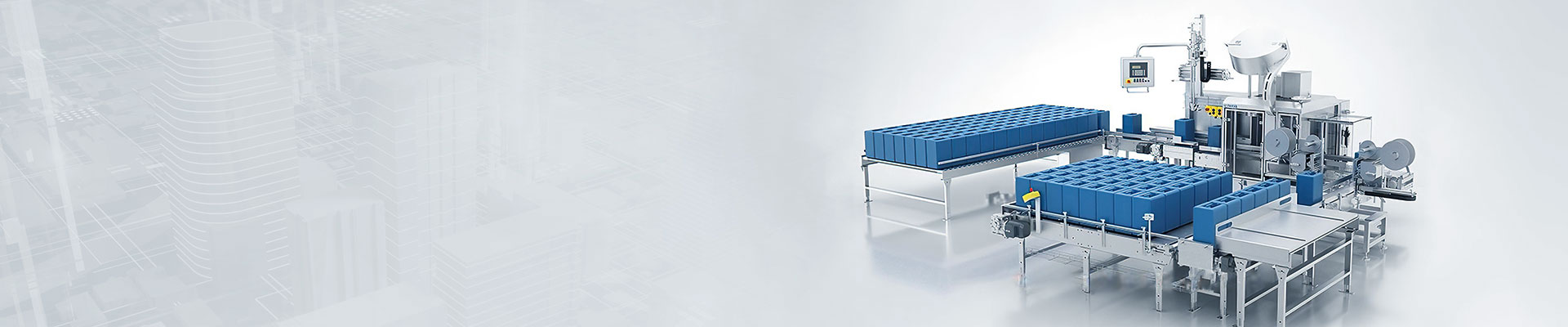
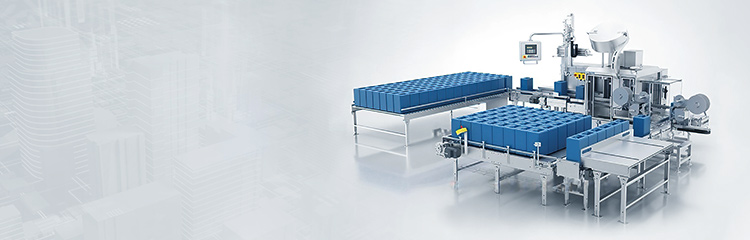
The role of the automatic heavy machine is according to the sorting instructions issued by the control device, when the commodity with the same sorting signal passes through the device, the device acts to change the running direction of the automatic detection machine into other conveyors or into the sorting road. Its main function is to make the goods to be sorted through the control device, the measurement and detection machine on both sides, generally to connect a number of sorting crossings, so that the classified goods slide down the main conveyor (or main conveyor belt) for subsequent operations.

The role of the sorting scale is based on the control device issued by the sorting instructions, when the goods with the same sorting signal through the device, the device action, so as to change the direction of operation in the automatic inspection machine into other conveyors or into the sorting roadway. There are many kinds of measuring and checking machines, generally there are several kinds of push-out type, floating type, inclined type and branch type, different devices have not exactly the same requirements for the packaging materials of the sorted goods, the weight of the package, the smoothness of the bottom of the package, and so on. The main component is a conveyor belt or conveyor, its main role is to make the goods to be sorted fish through the control device, measurement and detection machine, and automatic detection machine on both sides, generally to connect a number of sorting roadway, so that the sorting of goods slides down the main conveyor (or the main conveyor belt) in order to carry out the subsequent operations.
The product enters the "acceleration section" of the checkweigher: the distance between the products is increased, ensuring that it enters the "weighing section" as a single product and not as multiple products. When the product sorting is irregular, it can also be sorted out by the "accelerating section"; the product enters the "weighing section" of the checkweigher: the Weighing system quickly detects the weight of the product; and immediately makes a judgment on whether the weight of the product is within the target weight range. If the weight of the product is qualified, it will be transmitted out of the weighing machine without any error; if the weight of the product is unqualified, it will give a delayed signal for rejecting. At the same time, the system will automatically record the number of qualified products and the number of unqualified products; the products enter the "reject section" of the Sorting machine: when the reject section detects the reject delay signal, it will make the rejection action at the right time, and accurately reject the unqualified products.
Technical Parameters
Sorting range: 4.0~300.0g (600.0g also available)
Sorting speed: Max. 60 times/minute
Sorting accuracy: ±0.2g
Minimum display: 0.1g
Sorting object: (length 20~100mm) (width 20~100mm) (height 5mm or more)
Power supply: AC110/220V,50/60HZ)
Use temperature: 0℃~35℃