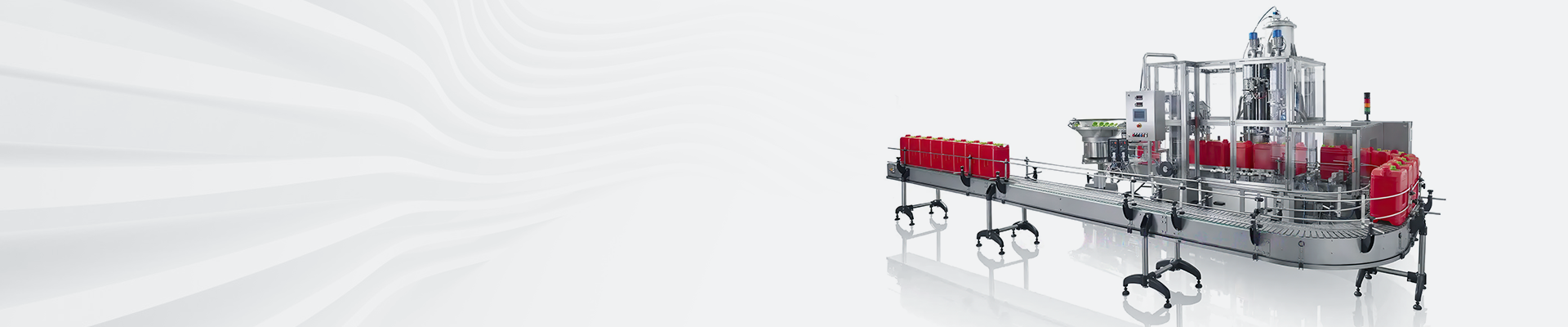
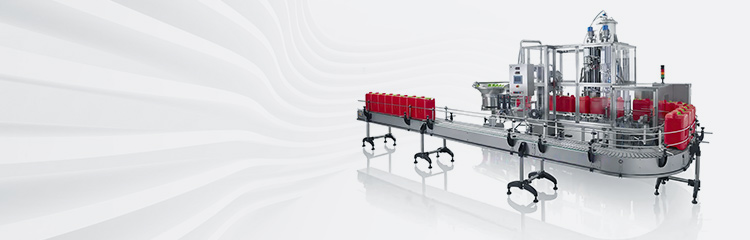

Summary:The sorting machine can be monitored through the control computer and can perform centralized switching operations. It can control the air source through the weight distribution manifold board, provide the controller with weight status information and display the weight value on the screen, and control the components through the given set value. Perform testing.
Plug & Play solutions for fully assembled modules save time and reduce costs. The new MT9928 sorting scale from CASGOOD is the best example of optimized air handling compared to earlier sorting machines.
CASGOOD is a leading manufacturer of checkweighers with integrated boards. These sorting machines are widely used by major manufacturers of microchips to ensure the high quality of the electronic components under test. These checkweighers are integrated at the back end of the component production line. Zero defects" is the basic rule here. This is followed by quality control, i.e. testing of the components by means of a given sorting machine (test weight checker) at any desired ambient temperature.
Quality and quantity require a fairly high reliability factor. Typically, the test handler runs continuously day and night. Due to the huge number of components, such a test handler has to supply 28,000 components per hour to the sorting equipment, so any downtime costs are enormous. In view of this, there is still a need for continuous improvement of this type of sorter, and in addition to reliability, ease of maintenance is a very important factor. The cost pressure of assembly operations is also another major challenge for CASGOOD. Connecting a number of gas handling components to make a gas handling system work is a time consuming task. To improve this situation, CASGOOD worked with its weight conveyor technology to find the best solution to improve the assembly efficiency of the MT9928 project.
Organize pneumatic components Due to the modular structure and the variety of air handling applications (e.g. also for cleanrooms), it was always the case in the past that the air handling unit, the complete set of pressure reducing valves, filters and valves were mounted directly on top of the sorter downstream of the air source. In order to facilitate maintenance, the pressure values can be read by means of pressure gauges mounted at several different locations on the sorter. As a result, a large number of air lines had to be installed, which increased installation costs and required more space. Sorting Equipment In this solution, all the important components of the air handling and feed weight sorter are concentrated in one main module, the sorter can be monitored by a control computer and can be switched centrally, downstream of the air source, directly on the sorter, with the air handling unit, the complete set of pressure reducing valves, filters and valves. The module is supplied completely pre-assembled, with all wiring and air lines installed, plug-and-play, reducing the workload. The modules require a variety of different pressures, which can all be realized through standard interfaces in the weight sorter.
Air handling units with 5 μm filters can barely be used in cleanroom applications before cleanroom class 1. Due to the close contact between the compressed air and the sorter components during transport, fine dust particles were deposited during continuous operation, resulting in sorter failures and high maintenance costs. In the new solution, three filters in the D-Series air handling units (LFMA and B) are connected in series. The compressed air is filtered sequentially through 5μm, 1μm and 0.01μm filters, thus ensuring compliance with cleanroom class 1, the most basic standard in semiconductor production. This ensures compliance with clean room class 1, the basic standard for semiconductor production, and eliminates dust-related sorter failures even during long periods of continuous operation. In addition, the D-Series air handling units can indicate when maintenance is required. Delayed operation means that all cylinder actuators can be run slowly rather than immediately to the target position, ensuring safety and reliability. the VLHE valve builds up hysteresis pressure when the weight sorter is switched on, reducing the risk of danger if the safety cover is removed while maintenance is being carried out.
Separate control, centralized distribution In the past, air handling units and pressure reducing valves were used in combination in order to generate different pressures, and the air supply was often impeded when the air handling unit became fouled. Now the air handling unit is no longer equipped with pressure reducing valves: the seven pressure reducing valves of the LRB series are installed downstream of the sorter, each one being responsible for supplying the pressure to the entire module and for depressurizing the weight sorter. The pressure reducing valves are equipped with analog sensors that provide the controller with information on the state of the sorter and display the pressure values on the screen. This was not possible before, as it was necessary to remove the end caps and read the pressure values on the corresponding pressure gauges.
Compact air distribution by means of air circuit boardsIntegrated technology has resulted in a customized component that is similar in nature to an air circuit board: Between the two aluminum boards there is a plastic board containing all the air inlet lines, which are connected to the corresponding pneumatic components. This solution is similar to the arrangement of electronic modules on a printed circuit board, except that it is the pneumatic lines that are closely arranged instead of the semiconductor components. In this solution, no separate complete air line system is required, thus significantly reducing the assembly workload for CASGOOD. Due to the relatively dense components, high functional reliability, in this dense configuration can be avoided to bend the complex piping system. MT9928 type test processor in the contact control box is such a configuration. Multiple valves and cylinders need to be installed in a limited space. Due to space constraints, the traditional air tube configuration is no longer suitable and a flat structure is required. Another unique feature is the switching module, which can be arranged in two different ways ("wiring diagram") with a single air circuit board, based on the principle of one module for several derivatives. This air circuit board is also supplied pre-assembled and tested. A total of four modules are installed on each sorter, offering CASGOOD great potential to reduce assembly and quality control costs. The module is also a very cost-effective solution for small production lines of around 100 units. A number of problems arising from the need to install air tube weight sorters in such a limited space can be avoided.