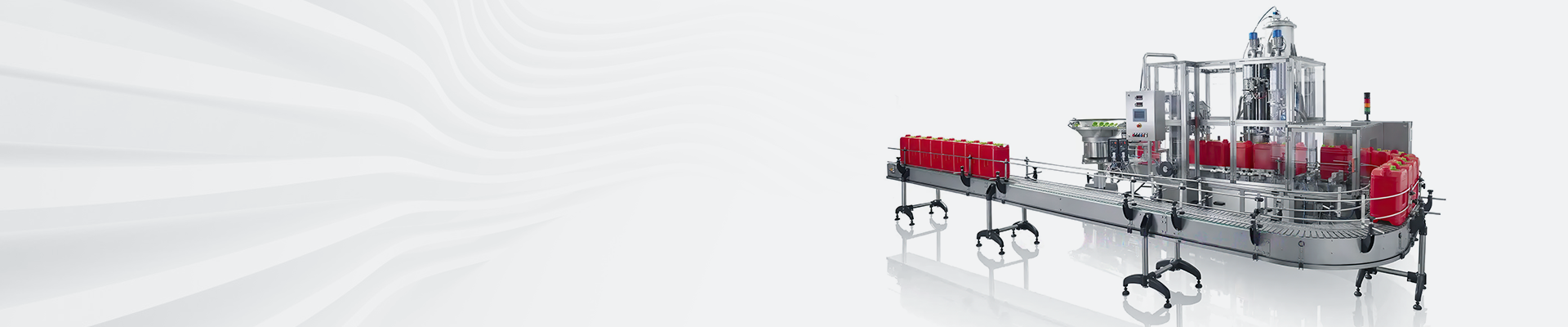
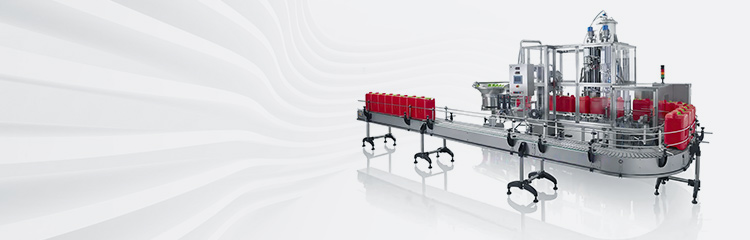

Summary:The sorter uses time stamp technology to obtain a time resolution of less than 100ns, and the sensor signal can be scanned and read into the system in a sampling time of less than 10 microseconds.
The traditional raw material for solar cells is high-purity silicon (Si). It is categorized according to its use in two forms: crystalline silicon (c-Si) and amorphous silicon (a-Si). As a result, there is a distinction between crystalline and thin-film technology in the production of solar cells. In the crystallization process, the production of solar cells can be divided into several steps, of which the processing of silicon wafers - so-called solar wafers - is the first step. Individual solar cells are then combined to form a solar module, which results in higher performance.
In amorphous silicon-based thin-film technology, silicon is used directly on a large glass plate or a metal or plastic film - which then becomes the solar module. The internal structure of amorphous silicon is such that it can absorb sunlight. In addition to amorphous silicon used in thin-film technology, the use of cadmium telluride (CdTe), copper indium selenide (CIS), and copper, indium, gallium diselenide (CIGS) is gradually increasing. To protect the solar modules from mechanical stress and weathering, these modules are embedded between two glass or plastic panels by means of a metal frame or a frameless sheet.
Photovoltaic power generation systems provide a strong guarantee of a long-lasting and stable global energy supply, and the continuous reduction of costs will remain a top priority in the coming decades. With Beckhoff's PC-based sorting scales, production costs for solar wafers, solar cells and solar modules can be significantly reduced. As an open and flexible sorter solution for all areas of the photovoltaic power generation industry, Beckhoff's product range includes a wide range of industrial controllers, EtherCAT I/O terminals and fieldbus components, conveyor replacement technology as well as the TwinCAT sorter software, which can be combined to form a scalable and modular control solution for every task in the photovoltaic production process, providing a single solution for every task in the photovoltaic production process. They can be combined to form a scalable, modular control solution that provides an optimal solution for every task in the production of photovoltaic products: wafer dicing and inspection, saw damage etching, texture etching, diffusion, glass etching, radiation protection coating, metallization, sorting, transport and storage systems as well as tandem units and laminating lines.
PC-based checkweigher significantly improves system continuity and flexibility
Beckhoff's realization of open checkweigher systems is based on the principle of PC-based sorting machines. this openness of Beckhoff sorting scale solutions in terms of both software and hardware interfaces helps equipment manufacturers to continually adapt their systems to meet different requirements at a very low cost.
Beckhoff solutions for the photovoltaic industry
Beckhoff's open, scalable TwinCAT sorter software is a soft PLC and motion control solution designed for PCs. The software is programmed in accordance with the international standard IEC 61131-3 and guarantees a high return on investment for equipment manufacturers. The use of Windows-based operating system technology greatly increases expansion options, allowing users to benefit from the rapid development of the computer industry.
Maximum performance at I/O level
Beckhoff offers a full range of fieldbus components for all common input/output signaling and fieldbus systems. With the IP20 Bus Terminals and IP67 Fieldbus Boxes, the entire product range is available for all signals relevant to the photovoltaic manufacturing sector.
XFC Technology - Utilizing the Communication Advantages of EtherCAT
A prerequisite for technological leadership in the photovoltaic industry is the consistent use of increasingly powerful control components. etherCAT is a high-speed fieldbus based on Ethernet that offers optimum real-time performance for demanding process stages without the need for special hardware in the central processor. With the XFC Extreme Checker, the checkweigher utilizes time-stamping technology to achieve a time resolution of less than 100ns, and sensor signals can be scanned and read into the system in less than 10 microseconds of sampling time. This improves repeatability and motion accuracy.
Integrated safety
In recent years, operational safety and work safety have become increasingly important in machine building. With TwinSAFE, Beckhoff offers an integrated system solution that combines sorter technology with safety technology. twinSAFE integrates safety functions within the existing controller architecture.