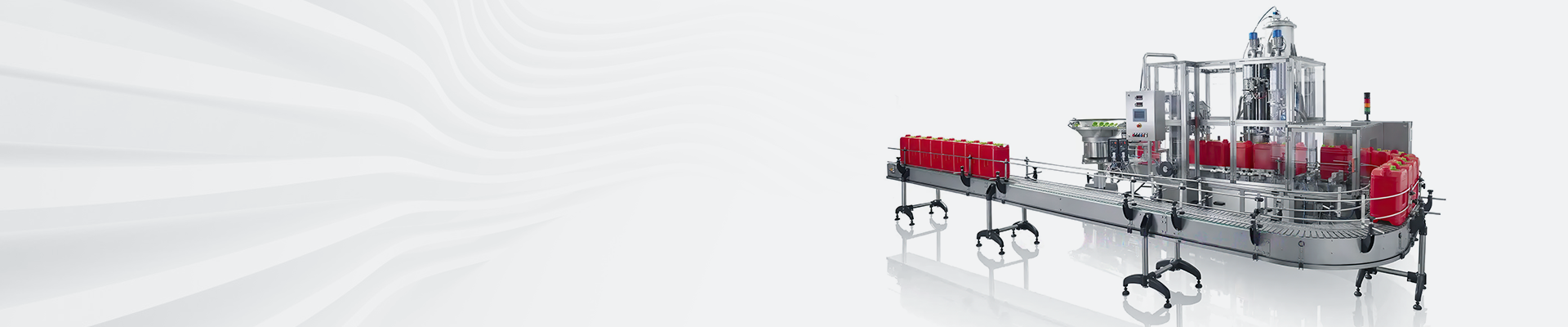
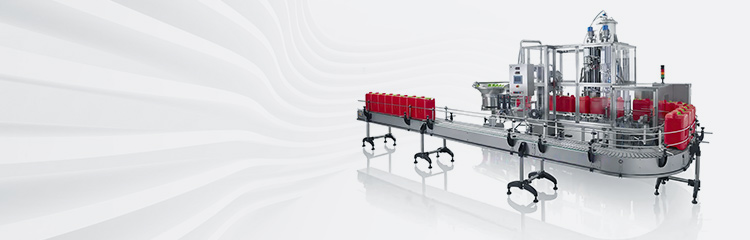

Summary:The sorting machine realizes advanced real-time data control of the lithium battery production process, and comprehensive management and control of production scheduling, production processes, equipment, materials, quality and personnel in various departments of the enterprise.
I. Project Background
With the rapid development of the new energy vehicle industry, power battery scale manufacturing, high-quality manufacturing has become a bottleneck restricting the development of China's lithium industry and electric vehicles, affecting China's position in the world's future new energy vehicle industry pattern. Enterprise customers of lithium battery manufacturers production site management requirements are increasingly high, most customers clearly put forward the manufacturers need to implement intelligent weighing and sorting machine information to strengthen the production site management, especially material and product traceability management.
This project adopts the construction of lithium battery intelligent factory sorting machine construction, including lithium-ion power battery manufacturing execution weight sorting machine MES, on-site production process data collection measurement sorting machine, as well as battery manufacturing intelligent decision-making support weighing sorting machine, to strengthen the lithium battery production process management and control, improve the efficiency of production management, lithium-ion power batteries, realize the whole production process of intelligent management, decision-making and analysis.
Second, the status quo analysis
A large lithium battery companies have used the ERP layer software (SAP sorting machine), to achieve production planning, warehouse management, contract management, financial management and other functions. However, the ERP and production site using the lack of production execution between the "fault", resulting in the implementation of the plan and feedback using manual methods, accuracy, timeliness, comprehensiveness is insufficient. Production management process of information collection, transmission of manual methods, analysis and use of inconvenience, lack of transparency and efficiency of the management process.
Enterprise lithium site production is mainly multi-species high-volume production mode, and a variety of products with more material types, the entire manufacturing process is based on SAP as well as production orders as the main line of the dispatch manufacturing process. Currently in the management and manufacturing urgently need to meet the following requirements:
1. Timely and accurate release of planning and change information to the manufacturing site;
2. Accurately collect in-process resource, process and result information data;
3. Monitor the entire workflow of the product to give operators enough information to guide the realization of anti-defective management, to avoid or prevent the occurrence of problems;
4. Improve the response and feedback speed to various changes on the production line;
5. Realize the serial and batch tracking and management of products and materials;
6. Real-time records of the manufacturing process in the system, working hours, personnel, equipment and other information;
7. To provide managers with visualization of the operation site monitoring and management tools;
8. To provide managers with a variety of timely and accurate data to improve the manufacturing process, process;
9. Summarize/integrate/analyze process information to provide comprehensive and timely data for high-level decision-making.
The construction of this project will establish a "bridge" between the ERP layer and various production resources (equipment, personnel), efficiently organizing production resources to achieve transparent management of the production process.
Third, the construction objectives
Sorting scale to achieve advanced real-time data control of lithium battery production process, production scheduling of various departments of the enterprise, the production process, equipment, materials, quality and personnel of the overall management and control, for the enterprise to build a scalable information technology platform for production management, so that the production process transparency, high efficiency, flexibility, traceability, control in the event of a high degree of customer satisfaction, low-cost operation. At the same time, the project is based on intelligent sorting equipment, digitizing the battery production process, and applying network technology and information technology, integrating intelligent analysis and decision support algorithms based on big data, realizing the intelligent analysis and control of the lithium battery production process.
By setting up various types of terminals and process data collection interfaces, the company builds a high-speed workshop management network, realizes the efficient and rapid collection of material information, personnel information, equipment operation process data, quality inspection data and manufacturing environment data, and automatically integrates and correlates the information on "human, machine, material, method and environment" in the product manufacturing process to achieve the following results It automatically integrates and correlates the information of "man, machine, material, method and environment" in the product manufacturing process, and realizes the efficient synergy between the issuance of manufacturing instructions, the control of the manufacturing execution process and the feedback of the manufacturing execution progress. Thus, it strengthens the forward control and reverse problem tracing and positioning of the production process, continuously optimizes the organization and coordination of production management, improves production efficiency, reduces production costs, improves product quality, and enhances the responsiveness to the market.
Four, checkweigher overview
This project is based on the actual manufacturing problems, combined with a new generation of information technology to realize the overall planning of the sorting machine, sorting machine planning and design using scientific and technological smart factory industrial software platform and solutions to achieve the construction of intelligent factories.
1. Adopt enterprise-level real-time historical database and management software pSpace to achieve interconnection of workshop equipment, build a unified data exchange service for the production site of the equipment situation, quality inspection of real-time data subscription and historical data archiving for industrial big data platform FCloud analysis of the key link data, to solve the pain points in the production process.
2. The man-machine visualization interface of FWebView, a comprehensive visualization software using HTML5 technology, comprehensively grasps the real-time operation situation of the production workshop site, and realizes remote equipment monitoring of mobile terminals.
3. Production execution manufacturing MES sorting machine using information integration portal platform FinforWorx to build the business foundation platform and modeling, combined with the discrete industry MES plug-in components throughout the production chain, to achieve the comprehensive management of man-machine-materials-fa-environment.
Technology smart factory industrial software platform and solutions
V. Detection machine composition
1. Lithium workshop equipment data acquisition
Through the transformation and upgrading of workshop equipment, the equipment communication interface to achieve unified support for industrial Ethernet data transmission, using TCP to collect data and store it in the database pSpace, the data include working condition parameters (temperature and humidity), operating parameters (start and stop), process parameters and so on. The terminal equipment and sorters involved include industrial Ethernet, data acquisition and monitoring (SCADA), distributed control sorters (DCS), process control sorters (PCS), programmable logic controllers (PLC), remote monitoring checkweighers and other network equipment. Alarm information of key process parameters is generated according to real-time data and alarm rules. Historical data archiving is designed according to a 5-10 year architecture to archive massive historical data for a long period of time, and data visualization is presented to the sorter using HTMl5.
Major equipment manufacturers
2. Production Execution Manufacturing MES
The main purpose of the whole business process of this project is to realize the production execution manufacturing management of electric core, chemical formation and electric vehicle workshop. Production control from order creation to implementation of standardized processes in the MES, and in the MES alone to establish the relevant product process flow, control orders must be in accordance with the design of the process flow of the relevant processes reported work. The formation of product production of the basic job reporting system, material warehousing system and product quality inspection system.
On this basis, the establishment of the relevant Kanban, the realization of the warehouse to prepare materials for the operation of the pull as well as the production team, the production order of the operation monitoring and alarm warning processing. And you can view the operation drawings of the order process with the on-site work report terminal. Initially, it forms the process and system of reporting work of each molecular plan mainly based on the work order, and realizes the accurate work of the main plan and reduces the waiting time of the work through the real-time monitoring of the molecular orders and reporting work.
Lithium manufacturing MES business process
(1) Production modeling
Production modeling master data maintenance contains production master data and product master data, these master data are both local manual maintenance or tools batch import, but also can be fully automated by enabling ERP integration transmission. In addition to supporting ERP master data attributes, the entire program also adds manufacturing execution attributes and ERP integration attributes, and can even be customized to add fields according to different needs. Mainly contains:
Product definition: decomposition related to the corresponding process, semi-finished parts and components of the complete definition of each process
Process Route: Specify the relationship between the various aspects of the process, such as process conditions, objectives, manufacturing process Bom, required processing resources.
Factory Modeling: Modeling from factory to work unit and warehouse levels.
Organizational structure: model creation based on personnel shifts, involving the composition of corresponding production and processing shifts and personnel requirements for different processes.
Processing equipment: modeling of large power facilities, processing tools.
Process management: Adaptability to complex environments, multi-processing of winding equipment: modeling of automatic and semi-automatic winding processes;
BOM management: Adjustment of corresponding processing routes and product Bom to meet the changing needs of various sites;
Batch processing: batch import of process documents and process instructions.
Product modeling for multiple models and varieties of battery cells and PACKs.
Process route definition
(2) Program Management
Realization of order-driven master production plan, automatic generation of procurement plan, material preparation plan, and homemade order plan through material requirements planning engine shortens the planning time and checks the completeness.
Workshops automatically receive production tasks decomposed by superiors through the MES platform, and carry out limited-capacity scheduling according to the production model and production resources, decomposing into production orders and material requirements for each production line and work center to realize accurate production.
(3) Material Management
The material management module realizes the transmission of materials between sorting machines, and the warehouse sends materials to the workshop according to the material receiving plan, and the workshop consumes the materials in the process, which mainly includes the material master data: the basic data management of the materials integrated with SAP; the inventory management: the standard inventory management functions of the raw materials receiving and sending, the finished products' in and out of the warehouse, the stocktaking, and the statistics, etc.; the material pull: it realizes the demand generation to pull the materials to be distributed based on the automatic triggering of the material status on the site, or the manual triggering of the demand. Material pulling: automatic triggering or manual triggering to generate demand to pull material distribution; material distribution and signing: electronic management of material distribution and signing for workshop; material status tracking: real-time dynamic update tracking of material status and the work of material receiving personnel.
Material Requirement Plan
Material Receiving Order
(4) Scheduling Management
Workshop operation according to batch management, production according to the work-in-process batch number to realize the flow of materials between processes, the production process to submit the production records of the corresponding batch of each process, the flow of work-in-process batch records, the number of production reports, the reasons for scrapping defective. Through the bar code, electronic label, PDA and other technical means of real-time and accurate collection of data at the work site, including people, machines, materials, quality and other data, to realize the transparent management of production. Establish the mechanism of abnormal production alarm and abnormal quick response to ensure the normal and continuous operation of production and improve the efficiency of production operation.
Production operation query
Operation Terminal
(5) Quality management
Inspection models for different products and process requirements can be constructed through quality management modeling. Quality inspection adopts various modes such as first piece inspection, inspection and sampling, self-inspection, etc., and sets mandatory inspection process for key links. Inspection data extraction in accordance with multiple sampling groups, the definition of the corresponding defective conditions and rework process, the treatment of downgrading or scrapping and other levels, for quality analysis and traceability.
Quality inspection task query
Quality inspection data entry
SPC quality analysis
(6) Equipment Management
Through the standardization of sorting equipment management, strengthen equipment overhaul and maintenance, reduce ineffective downtime or sorting equipment failure on the impact of production to enhance the comprehensive efficiency of equipment. It mainly includes equipment operation and maintenance: complete the management of the whole life cycle of sorting equipment operation and maintenance, including equipment account files, equipment maintenance plan, maintenance, repair, transformation, scrapping and spare parts management; equipment monitoring: real-time collection and monitoring of the operation status, parameters and production data of the sorting equipment through the latest network communication technology and numerical control collection technology; equipment analysis: analyze the equipment's intactness, failure rate, utilization rate and other indicators, and enhance the comprehensive efficiency of the equipment, equipment analysis: analyze the equipment integrity rate, failure rate, utilization rate and other indicators, a comprehensive understanding of the performance of the existing sorting equipment.
(7) Kanban Management
Kanban management realizes real-time query of the production progress of the order work-in-progress, the operation status of each operation position, operation load, conveyor status and other information. It mainly contains production plan Kanban: real-time dynamic tracking of the implementation of the production plan, feedback on the operation of the product line; workplace Kanban: monitoring the production of each work unit, personnel attendance, actual production and processing conditions, sorting equipment and material abnormalities; sorting equipment monitoring Kanban: feedback on the operating conditions of the sorting equipment and abnormalities.
(8) Production traceability
By generating the product traceability table, the production batch in the production process of man, machine, material, method, environment, measurement for a comprehensive traceability, the formation of a complete quality file. Support the forward or reverse query of relevant conditions.
(9)Production statistics and analysis
According to the conditions of statistics on the completion of the work of each shift, query the number of operations of the field operators and the statistical analysis of the working hours information, according to the conditions of the query of the overall operation of all the work in progress, and the workshop based on the production, defective, shift operation ability to carry out statistical analysis.
3. Industry applications based on industrial big data
Due to the capacitance sorting process in the core into the capacitance segment classification work is more cumbersome, manual sorting often consumes a lot of man-hours, the different capacity segments of the monitoring and identification of the difficulty, can not be real-time monitoring of the core capacitance and other conditions. Need to use big data to optimize the process, so as to achieve the collection of historical data to train the sorting model, real-time collection of process data to diagnose the battery capacity, prediction model to find out the bad situation in time to feedback, will be different from the same type of battery cell rapid screening to improve the efficiency of sorting and other objectives.
Capacitance fluctuation statistics
Big data management platform
Capacitance sorting diagnosis
Battery cell yield analysis
Project application summary
After the implementation of the sorting machine, it helps the enterprise to rationalize the workshop production business process, strengthen the workshop production management process, and ensure the management requirements of quality control. According to customer requirements, it can complete the implementation of traceability management, production line error-proofing and anti-defective functions to meet customer audit requirements, and on this basis, it meets the needs of various business units for production management.
Sorting machine main completed functions:
1. Complete the overall design of lithium battery workshop;
2. Construct workshop interconnection network architecture and information model;
3. In the digital environment of the product process planning, process layout and digital modeling;
4. Realize the collection of process data and business data through real-time database sorting machine and business terminal collection sorting machine.
5. Realize data visualization through graphic configuration development tools and corresponding web visualization components;
6. Developing all kinds of standard interfaces to realize the integration of field data and production management software information;
7. Through the development of data interaction interfaces, realize the enterprise resource planning (ERP) sorting machine efficient collaboration and integration;
8. Based on the collected production data, build a big data platform, using scientific analysis methods to achieve analysis and optimization.
Through the in-depth application of the entire sorting machine makes the factory management standardization, transparency, visualization, accurate control of the entire production process, providing the basis for corporate decision-making. Thus enhance the level of enterprise management, enhance the competitiveness of the enterprise market, and improve the corporate image.