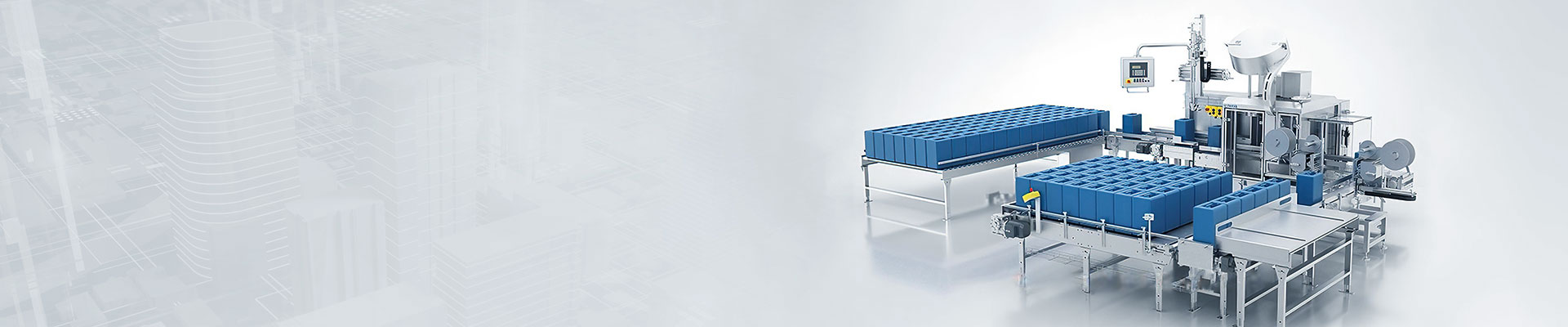
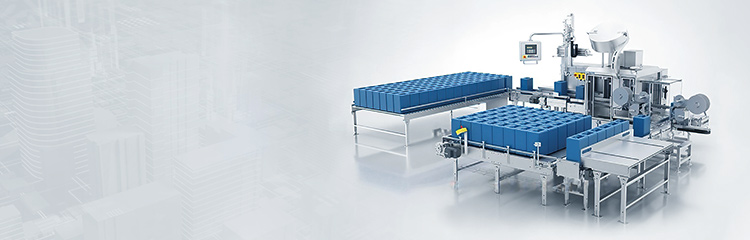
Checkweigher is used for automatic weight detection, upper and lower limit discrimination or weight grading selection on various automated assembly lines and logistics conveying systems. It adopts weighing controller technology, combined with servo motor machine iterative system and elaborate mechanical design, and is specialized in on-line dynamic weighing and classification of products passing through the automated production line. It can realize continuous dynamic checkweighing of products, detect unqualified products, alarm for overweight or light ones, and realize product classification and unqualified product rejection function through the structure of classification and rejection at the back-end.

Checkweigher is a medium-low speed, high-precision on-line checkweighing equipment, which can be integrated with various packaging production lines and conveying systems, mainly used for on-line checking whether the weight of the products is qualified or not, whether there are missing parts in the package or whether the weight of the products is archived. Measurement of the weight of the product is accomplished during the conveying process, and the measured weight is compared with the pre-set range, and the controller sends out commands to reject the products with unqualified weight, or distribute the products with different weight ranges to the designated area.
The automatic checkweigher consists of weighing conveyor, controller and inlet/outlet conveyor. The weighing conveyor collects the weight signals and sends them to the controller for processing. The in-feed conveyor ensures sufficient spacing between products by increasing the speed. The outfeed conveyor is used to transport the checked products out of the weighing area.
Weighing preparation: the product enters the infeed conveyor, the speed setting of the infeed conveyor is generally determined jointly with the spacing of the products and the required speed. The aim is to ensure that only one product can be on the weighing platform during the checkweighing process.
Weighing process: when the product enters the weighing conveyor, the system recognizes the entry of the product to be inspected into the weighing zone, according to external signals, such as photoelectric switches, or internal level signals. Depending on the speed of the weighing conveyor and the length of the conveyor, or on the level signal, the system determines the time at which the product leaves the weighing conveyor. From the time the product enters the weighing platform to the time it leaves the platform, the load cell will detect the signal, and the controller will select the signal in the stable agricultural area for processing to obtain the weight of the product.
Sorting process: When the controller gets the weight signal of the product, the system will compare it with the pre-set weight range and sort the product, the sorting type will be different according to the application, mainly the following types: rejected products, overweight and underweight were rejected, or transported to different places, according to different weight ranges, divided into different weight categories.
Report Feedback: Checkweighers are equipped with a weight signal feedback function, which usually feeds back the average weight of a set number of products to the controller of the packing/filling/canning machine, which will dynamically adjust the dosing volume to make the average weight of the products closer to the target value. In addition to the feedback function, the checkweigher can also provide a wealth of reporting functions, the number of packages per zone, the total number of packages per zone, the number of passes, the total number of passes, the average value, the standard deviation, and the total number of packages and the total total accumulation.