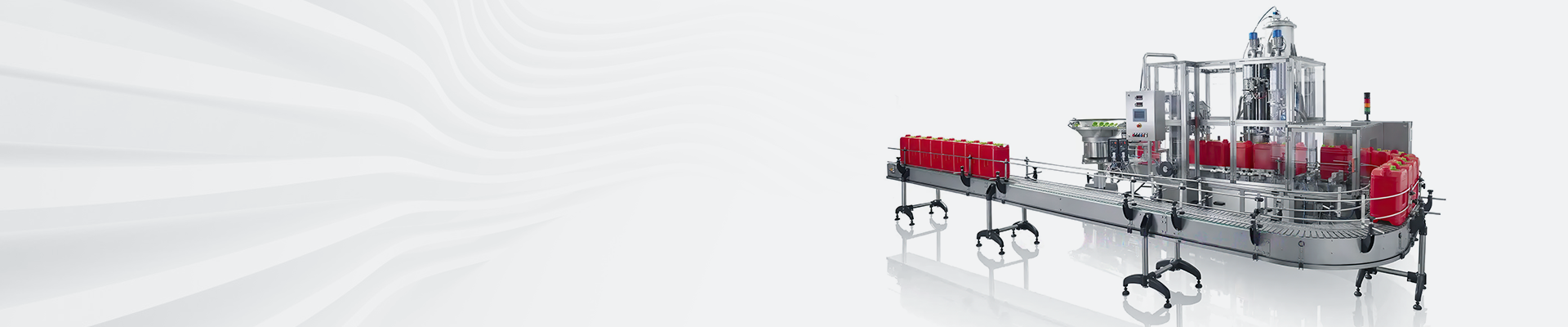
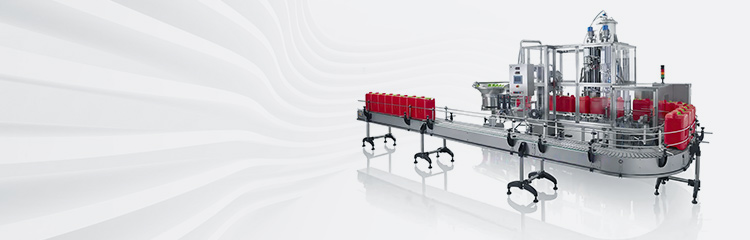

Summary:The sorting machine uses a CCD camera to obtain the position information of the parts, and uses image processing and recognition technology to identify and position the workpieces. The images are used for template matching, edge detection and hybrid central moment calculations to achieve computer vision detection and sorting of products. Harris is used to The corner detection and virtual triangle matching method establishes a parts sorting system, which greatly reduces the error rate of sorting and meets the requirements for sorting parts quickly and accurately.
The checkweigher uses the CCD camera to obtain the position information of the parts, identifies and locates the workpieces through image processing and recognition technology, and the images are subject to template matching, edge detection and hybrid central moment calculation to realize the computer vision inspection and sorting of the products, and adopts the Harris corner detection and virtual triangle matching method to establish a parts sorting system, which can reduce the error rate of the sorting very well, and achieve the goal of fast and accurate parts sorting. The system reduces the error rate of sorting and achieves the requirement of sorting parts quickly and accurately. Using the magnitude of the relative center-of-mass moments of each pixel on the image contour of the workpiece, an area center-of-mass algorithm is proposed based on the principle of mechanics, which can realize accurate online detection of the inner diameter of the parts. A series of classical image processing algorithms are used to obtain the radius of the circular hole and the coordinates of the center of the circle of the measured workpiece, and then compared with the parameters of the standard workpiece to know the current requirements of the workpiece gauge. Sorting machine in order to obtain effective dynamic weighing signals, ADC chip from the cluttered signal analysis and processing of effective 100 of the data, scales and weighing modules inherent vibration frequency of about dozens of hundreds of Hertz, the AD chip data output rate of 1kSPS effective to obtain the signal and the stray interference signal. Parts are transported with the belt to move at a speed of 40m/min, the effective movement time on the scale platform is short. The conveying length of the sorting scale in order to make the weighing accuracy is high, should be removed from the object on the weighing platform shock vibration and under the weighing platform violent vibration movement distance, when the distance is 15cm long, the actual effective length of the weighing object movement is only 15cm, weighing the object effective movement time is: 0,2255. If the AD chip data output rate of 1kSPS, in weighing the object movement of 225ms, can be obtained. 225 data is enough for the software to analyze and process the real weighing signal. Weighing data collection is based on noise-free resolution as a measure of compliance with the international OIMLR76 10.000e requirements, the AD chip noise-free resolution of 18bits accurately converts analog dynamic signals into digital signals. Weighing module excitation voltage feedback voltage by operational amplifier proportional summing operation, the resulting voltage by R14, C5 low-pass Pu wave as a reference reference voltage source to eliminate the temperature on the sensor cable signal impact.
Sorting scales also use DirectShow technology to complete the image acquisition operations, ordinary camera as an image acquisition device for the capture and playback of multimedia streams, as well as format conversion or codecs to provide strong support, the use of DirectShow can easily support the WDM driver model from the capture card to capture the data, and carry out the appropriate post-processing and even stored in the file. DirectShow uses a model called FilterGraph to manage the entire data stream processing, participating in the data stream processing of various functional modules called Filter, each Filter in the FilterGraph in a certain order to form a pipeline to coordinate the work, to complete the acquisition of video from the video device or decoding video streams and other operations. operations. For the collected color image data need to be binarized, image binarization is a special case of image transformation, is the most basic method of external reasoning in order to extract the shape of the object from the image. The binarized image is generally represented by the two values of background and day mark, through the gray scale processing of the collected color image, it is found that the target to be extracted from the gray scale image and the background area male obvious, so the use of automatic threshold segmentation method to complete the binarization of the external reasoning. After completing the region marking, it is necessary to measure the characteristic parameters of the marked image, calculate the length of each marked region, and find out the maximum length recorded as L and its corresponding region. For images containing parts, the region identified is the part. The number of pixel points in the largest region is counted as the area. Whenever a pixel point is found that meets the requirements during the counting process, its coordinates are noted. When the counting of all the pixel points in the area is completed, the color pixel information of the corresponding points on the original color image is obtained based on these position coordinates and the average value of the RG and B components is calculated as R.GB. The R.G and B are stored as the basis of the color in the sorting process. After contour extraction, there may be other non-part contours in the image in addition to the part contour, the use of connected region markers to find the longest contour and its corresponding region can be accurately part of the part extraction.