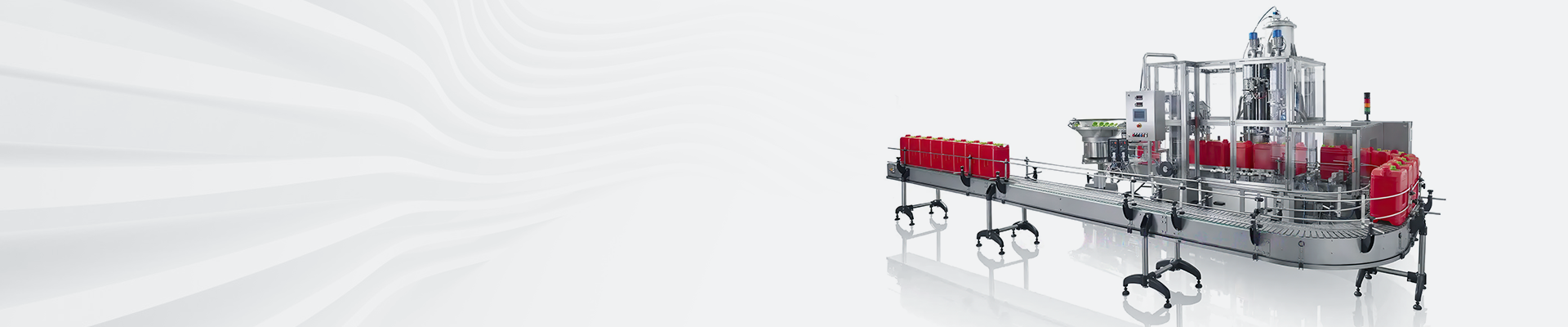
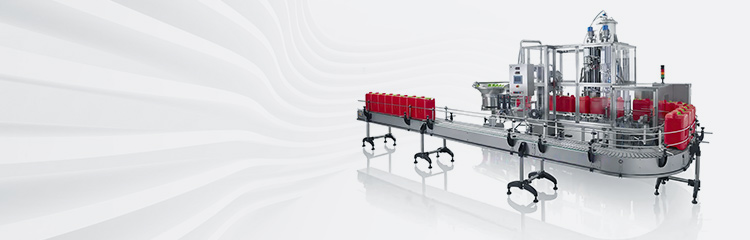

Summary:On the basis of fast and accurate distribution of additives, automatic filling machine adopts frequency converter to adjust the speed of pumping pump according to the viscosity of additives. The distributed transmission mode of "one machine and one independent pipeline" based on manipulator is adopted, which has the functions of additive consumption statistics, cost analysis and quality tracking.
In the production of printing and dyeing enterprises, the dosage of auxiliaries is an important process parameter, which affects the processing quality of fabrics and the energy saving and emission reduction of enterprises. At present, most printing and dyeing enterprises usually use manual distribution of auxiliaries in the field of auxiliary distribution, which has the following disadvantages: It is easy to make mistakes, low efficiency and serious waste of additives. The product quality is unstable, which leads to the low first-pass rate of products and the increase of production cost, which seriously affects the production efficiency of enterprises and aggravates the degree of environmental pollution; The labor cost is high, and the workshop environment also has adverse effects on the health of workers.
In order to solve the shortage of manual distribution, our company developed the measuring and conveying system of automatic filling machine for additives. The automatic filling machine uses electromagnetic valve, diaphragm pump and high-precision electronic scale, and the "weight method" is used to control the real-time weighing accurately and efficiently. However, the filling system still needs a lot of manpower to record orders and transport additives, which belongs to semi-automatic system. The filling system adopts the "bus-type" pipeline mode, and the additives are transported to the pipeline branch of the designated machine by controlling the three-way valve. When a three-way valve on the bus pipeline fails, the whole system will stop working, and it is not flexible to use. Moreover, because the rotation speed of the pumping pump cannot be adjusted according to the viscosity of the additives, it is easy to cause the additives pipeline to be blocked.
On the basis of fast and accurate distribution of additives, automatic filling machine adopts frequency converter to adjust the speed of pumping pump according to the viscosity of additives. Realize pipeline blockage prevention; The distributed transmission mode of "one machine and one independent pipeline" based on manipulator makes the system more flexible. The weighing system also has the functions of additive consumption statistics, cost analysis and quality tracking.
Additives filling system is mainly composed of additives distribution management, additives measurement and delivery control modules. The auxiliary agent distribution management system is connected with the central control management system of dyeing machine through industrial Ethernet, which obtains the feeding request of the workshop machine, optimizes the scheduling, and sends the feeding instruction to the auxiliary agent metering and transmission control system. After receiving the instruction, the auxiliary metering and conveying control system opens the corresponding auxiliary pipeline valve (auxiliary distributor) and uses weighing module, centrifugal pump and manipulator to measure and convey the auxiliary, and automatically conveys the auxiliary to the corresponding machine.
The liquid filling machine adopts Profibus system configuration, with PLC controller as the master station and ET200 distributed I/O as the slave station, to realize the control of the additive distributor, electronic scale, frequency converter and centrifugal pump, and to monitor the liquid level and manipulator of each additive barrel. Among them, the monitoring system of industrial computer is developed by configuration software MCGS, which completes the functions of state monitoring, alarm display and manual operation in the process of additive metering and transportation. At the same time, the function of off-line transfer of additives is reserved, that is, the code reader is used to scan the single number, quickly read the task information and complete the manual operation.
The working principle of the additive weighing system is that the industrial computer obtains and transmits the information of the designated machine, additive and weight according to the feeding instructions, and transmits these information to the PLC controller in the form of instructions, and the PLC controller completes the automatic measurement and transmission of additives.
Weighing and filling machine: firstly, open the auxiliary distributor, start the frequency converter to adjust the speed of the pumping pump according to the viscosity of the auxiliary, and the mass flowmeter begins to measure, and transmit the weight data to the PLC controller in real time; Secondly, when the weight value of the mass flowmeter reaches the target value of the operation information, close the corresponding auxiliary pipeline valve and stop the operation of the frequency converter, that is, stop the pumping pump, the mass flowmeter stops metering, and the auxiliary metering work is completed. Control the material transfer manipulator. The snap-in pipe interface of the material transfer manipulator (Figure 3) is embedded with the pipe mouth. Because of the distributed transfer method of "one machine and one independent pipe", that is, each dyeing machine is equipped with an independent transfer pipe, the outlet end of the material transfer manipulator selects the corresponding transfer pipe interface of the designated machine according to the instruction to the PLC controller, and quickly connects with the transfer pipe interface to ensure the correct transfer of additives.
The weighing control system is based on VB software to develop functional modules of task management, status monitoring, record statistics and parameter configuration, and the auxiliary distribution management system is managed by SOLSERVER database. The amount of auxiliary can be automatically recorded in real time, and the consumption cost of the order can be accurately counted. At the same time, the variety, density and pipeline of auxiliary can be configured according to the needs of users.