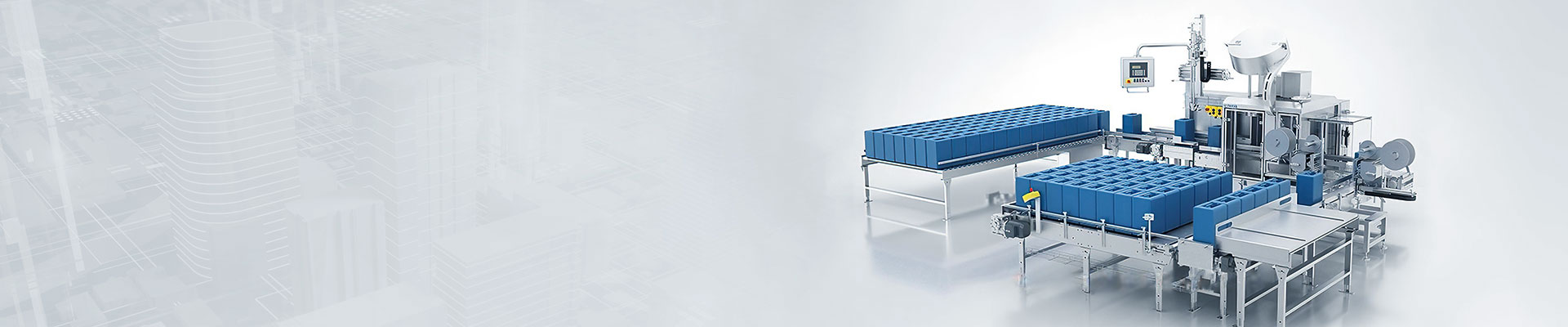
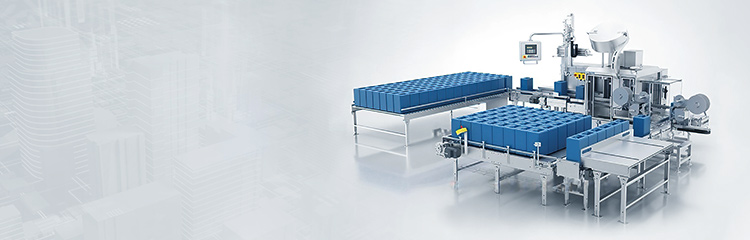
Urea filling scale adopts PLC to coordinate the whole control of bucket positioning, roller table operation, weighing filling, tank material and so on. The man-machine interface is used for manual, automatic and other modes of control, and the high-precision weighing module and high-stability weighing instrument are selected to control the filling process, which fully meets the precision and speed requirements of the system.

Automatic filling scale consists of programmable controllers and Electronic scales to form a two-stage computer control network, connecting field weighing instruments, control computers, PLCs, frequency converters and other equipment with higher intelligence and faster processing speed through field buses.PLC mainly undertakes fault detection, display and alarm of the automatic Filling machine and outputs signals to the frequency converter at the same time, which completes the role of the filling speed.
Liquid filling scale PLC is mainly responsible for manual/automatic processing flow selection, entering the judgment of the liquid level processing, various fault states under the alarm light display processing and control cycle, the liquid level processing is mainly responsible for the collected liquid level information and set value to compare to determine the height of the liquid level in the reaction tank, the liquid level of the level of the signal will be determined by the material pump opening and closing state. When the collected input value exceeds the maximum allowable value of the set liquid level, it will automatically limit it to a reasonable range to avoid abnormal situations. Automatic operation of the work process is the main filling control part, in the absence of other abnormalities and select the manual state, has been in accordance with the requirements of the process cycle back and forth, the value of its parts will be synchronized to display on the weighing interface, so that the control staff reference and monitoring.
Liquid filling machine adopts the most widely used in industrial control to adjust the weight for actual control, according to the weight deviation, adjust the speed of the electronic scale through the frequency converter, adjust the amount of feed to make it equal to the set value, and complete the automatic filling process.
Basic parameters:
Maximum weighing capacity: 300kg.
Minimum sensing capacity: 0.1kg.
Filling error: ±0.1-0.2kg.
Filling speed: about 150-180 barrels/hour.
Control: 2-speed control.
Filling method: Insertion type, liquid level up.
Gun head line: Teflon gun head, valve + Teflon hose.
Structure material: liquid filling machine host SUS304 stainless steel, conveying palletizing carbon steel anticorrosion paint.
Weighing platform size: 800 x 800mm (304 stainless steel power raceway).
Empty drum raceway: 800mm×2500mm (304 stainless steel power raceway) with another 1200mm slope unpowered roller.
Heavy drum raceway: 800mm x 2500mm (304 stainless steel power raceway, 2 sets).
Separate barrel device: for 200L barrels, carbon steel anticorrosive paint structure, 304 stainless steel raceway.
Palletizing equipment: pan-transfer type, suitable for pallets 1200×1200×140mm, including supplying pallets, palletizing, and lower pallet conveying.
Pipe pressure: 0.2-0.6MPa (related to material properties).
Material interface: 4 DN40 flange connectors, interface standards can be provided according to the user.
Air Connection: User supplied 12mm air hose connector for quick coupling connection.
Power supply used: AC220/50Hz (user supplied to one side of the machine).
Using air source: 0.4-0.8Mpa (provided by the user to the side of the machine).
Use temperature: -10℃-50℃.
Base condition: Horizontal solid concrete floor, concrete thickness should be more than 10cm.
Optional models: standard and explosion-proof filling scales.