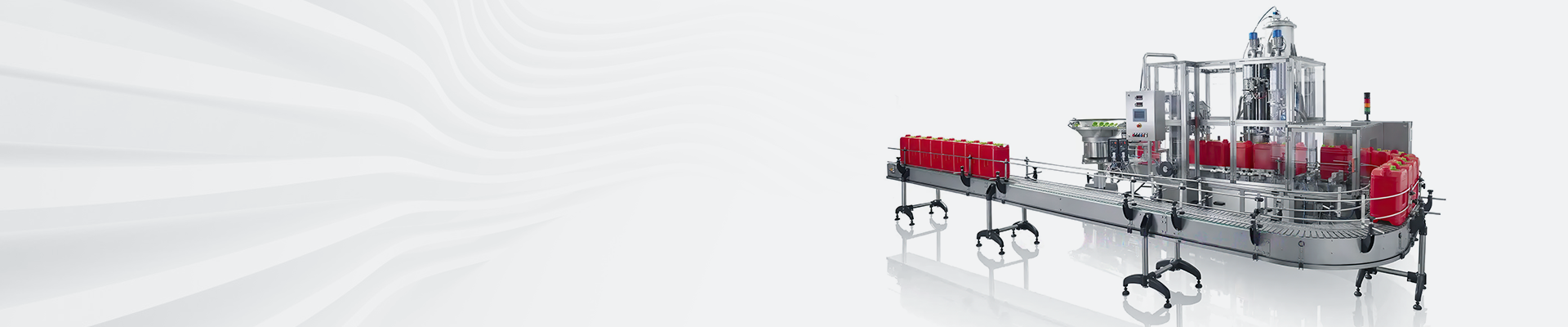
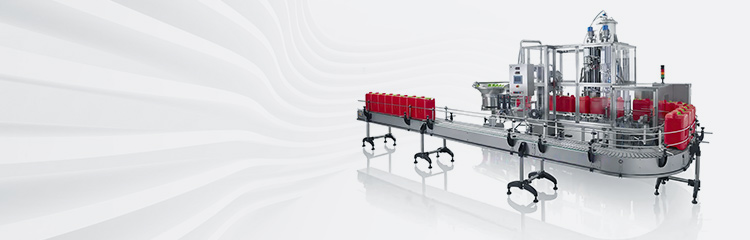

Summary:The ink dosage machine loads all the powdered raw materials into the powder silo through the bag opener, and the powder silo then transmits to the daily dosage silo to meet the powder required for the daily production of ink. The daily usage silo has upper and lower limit control, when the powder level drops to reach the lower limit value, the system will replenish the powder in time, and stop replenishing the powder when the material level reaches the upper limit. The same is true for crude oil material. Each bin or tank is equipped with a load cell, according to the formula transmitted from the upper computer automatically start the dosage. After the powder is dosed, it is transported to the mixing tank by the conveying device, and after the oil is dosed, it is also sent to the mixing tank.
1 Domestic and foreign ink automation production status
Most of the automated dosage machines of ink in foreign developed countries adopt DCS, FCS and other advanced computer control systems. Such as SunChemical, Michael Huber; FlintInk, Siegwerk and so on. And some large-scale domestic ink dosage machine mostly adopts PLC or computerized automatic control system. Automatic ink feeding system with computer automatic control system as the core, management software can complete the formula management, data reporting and dosing process of fully automatic control and remote monitoring and other functions, the degree of automation is high; Taiyuan Gao's Laurie Ink Chemical Co., Ltd. ink automation dosage machine using PLC control, ink automation system adopts a hierarchical, distributed, open system structure, mainly consists of the upper level of monitoring computer, PLC control station, on-site testing instruments and sensors, communication networks and other components.
Domestic small and medium-sized ink production enterprises ink product quality is not high mainly due to the degree of automation is not high, but the above automation for small and medium-sized enterprises in both price and function are too extravagant. Therefore, this paper proposes to industrial computer (IPC) + configuration software + data acquisition board to realize the ink automation feeder to meet the needs of some small and medium-sized ink manufacturers.
2 Introduction to the ink production process
Ink dosage machine through the bag opening machine will be incoming all powdery raw materials loaded into the powder silo, the powder silo and then transferred to the daily amount of silo, in order to meet the daily production of ink required for the powder. The daily usage silo has upper and lower limit control, when the powder level drops to reach the lower limit value, the system will replenish the powder in time, and stop replenishing the powder when the material level reaches the upper limit. The same is true for crude oil material. Each bin or tank is equipped with a load cell, according to the formula transmitted from the upper computer automatically start the dosage. After the powder is dosed, it is transported to the mixing tank by the conveying device, and after the oil is dosed, it is also sent to the mixing tank. The oil and powder are pre-mixed in the mixing tank by a high-speed mixer and then passed to the buffer tank. Buffer tank material is prepared for the grinder, pre-mixed material through the primary and fine grinder grinding, conveyed to the adjustment tank, adjustment tank ink that is the base ink, the base ink after testing, manual calculation of the amount of oil needed to adjust the amount of oil needed to be added through the next two adjustments to adjust the formula dosage, passed to the adjustment tank, to be adjusted to the qualified can be discharged.
3 Ink automatic dosage machine IPC system
3.1 Overall system design
The automatic dosage system adopts hierarchical and distributed system structure, which is mainly composed of upper industrial control machine, signal acquisition card, field control weighing instrument and weighing sensor, communication network and so on. The industrial control machine is responsible for the monitoring, operation control and report printing and management of the whole system. Signal acquisition card is responsible for signal acquisition of monitoring equipment and process parameters. The on-site detecting instrument and metering module are primary components, which are used to detect the operating parameters of the process, and are converted into standard signals by the weighing instrument and sent to the signal acquisition card for real-time and dynamic display in the upper computer. This system adopts industrial control machine + configuration software ten data acquisition board card to realize automatic ink dosage machine, in order to meet the needs of some small and medium-sized ink manufacturers. Through the weighing module to complete the field data collection, through the data acquisition board card processing and sent to the industrial control machine. Through the analysis of the collected data by the industrial control machine to complete the automatic dosage process, and use the configuration software "configuration king" to develop the upper computer monitoring system software, to realize the real-time monitoring and management of the dosage machine, alarm settings, trend curves, data report management and printing functions.
3.2 IPC system construction and program design
Ink automation feeder according to process requirements, the system program is divided into daily powder silo replenishment program, the original oil tank self-replenishment program, formula management program, mixing tank automatic dosage program, mixing tank mixing program, ink research program, the second feeding control program, adjust the tank mixing program.
3.2.1 Daily powder bin and crude oil tank replenishment program
All powder silos are equipped with weighing modules, weighing display instrumentation installed at the site, in order to facilitate the site unloading personnel to watch, each daily powder silo is equipped with upper and lower limit control, the program will automatically replenish the daily powder silo through the detection of powder. Crude oil tanks and powder bins are similar, since the replenishment program is basically the same as the powder.
3.2.2 Recipe management program
The function of this program is mainly through the configuration king comes with recipe management function, through the function call recipe, select the recipe to save, delete the recipe, but also can realize the recipe management.
3.2.3 Mixing tank automatic dosage program
This program is the most important part of the whole process, its function is to complete the control of the dosage process. The mixing tank is a high-speed pre-dispersing tank, the agitator on the mixing tank will fully mix the dosed oil and powder through high-speed pre-dispersing before the grinder can grind. Since the high speed pre-dispersion is a heat dissipation process, the mixing tank is equipped with a temperature sensor, when the temperature is higher than the upper limit set for the mixing tank, the system opens the cooling water valve for cooling; when the temperature is lower than the lower limit, the cooling water valve is closed. The mixing tank is equipped with an upper limit protection switch and a load cell, the actual value of the scale is displayed on the upper computer in kilograms, and when the liquid level is lower than a certain parameter value, the agitator on the mixing tank is turned off. Through the detection of the added material by the load cell at the bottom of the mixing tank, the upper valve body is controlled to open or close to complete the process of dosing. Specifically divided into oil dosing and powder dosing. Two kinds of dosage process is different, the oil is divided into batches of material, material 1 is put down after the completion of the closing of the corresponding valve, and start the preparation of material 2, material 2 after the completion of the start of material 3, material 3 after the completion of the closing of the corresponding valve. Oil preparation is completed, start the preparation of powder. Powder feeding is carried out through the powder flow meter, so three kinds of materials can be put down together, who first reaches a predetermined value, accordingly stop the materials put down.
3.2.4 Mixing program for mixing and adjustment tanks
The mixing program is the control of the motor and the control of the mixing time, so that mixing can only take place if the corresponding conditions are met. The control of time is a delay program and the program is relatively simple.
3.2.5 Ink research program
The program determines the start and stop of the inking machine and feed pump by detecting and judging the corresponding import and export pressure, temperature and material level of the buffer tank above.
3.2.6 Secondary feeding program
When a batch of grinding is finished, the inspector will carry out the inspection, through the calculation, if it needs to be adjusted, an adjustment process must be created, after the adjustment work formula is inputted, the control system will automatically start the secondary dosage program and discharge the dosage to the target tank.
4 Conclusion
The design of the dosage system takes into account both technology and economy, and has a very good cost performance. It basically eliminates the waste caused by occasional errors in manual dosing. The data for each batch and each type of material is recorded with date, batch number and data available, and the record is kept for a customized period of time. The preservation of these data enables us to find out the problems in time and make them corrected. The use of automatic ink weighing and dosing device provides a guarantee for the consistency and stability of the ink quality, eliminates the waste caused by human factors, and can basically satisfy the production requirements and market demand.