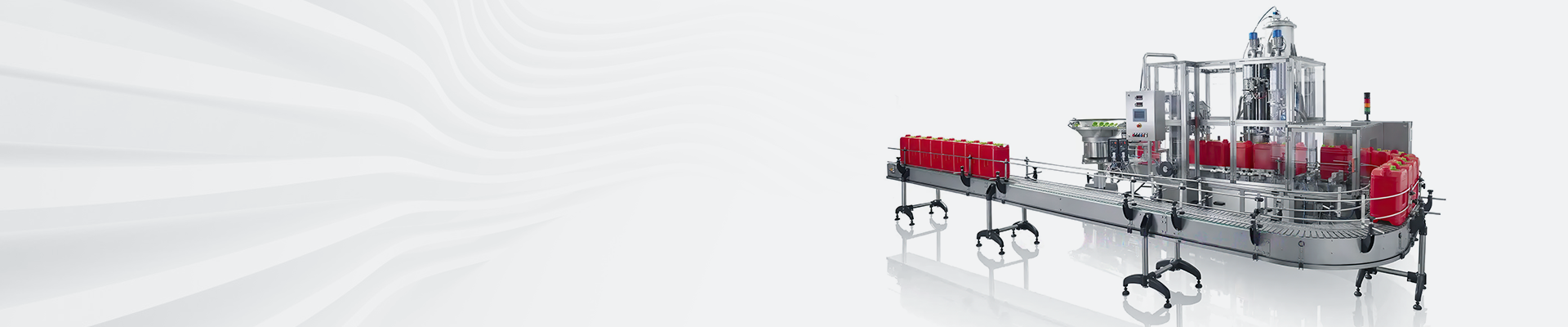
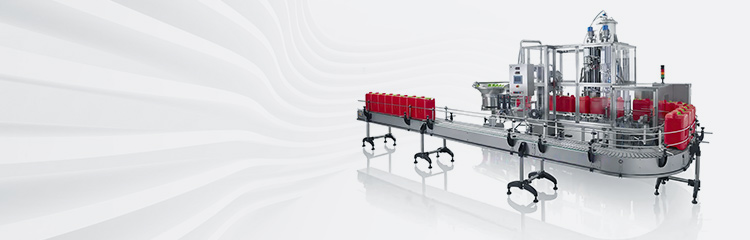

Summary:The reaction kettle weighing adopts large flow rate and low temperature difference circulating cooling process, the heating medium is saturated steam, and the jacket cooling water is industrial water. During the reaction process of polymerization kettle, the heat generated by the polymerization reaction of materials in the polymerization kettle is taken away by the jacket and four cooling pipes inside the kettle, so that the temperature of the kettle is kept stable during the polymerization reaction process until the end of the reaction. Through the combination of load cell, weighing instrument and control system, it can achieve the weighing and measuring work of the reaction tank, so as to control the system.
he most critical quality index of PVC products is the degree of polymerization, which is not related to the amount of initiator and the conversion rate, but is greatly related to the polymerization temperature. The polymerization temperature is almost the only factor to control the molecular weight of PVC. Therefore, the polymerization temperature must be strictly controlled in order to obtain PVC products with uniform molecular weight distribution. The general requirements of the polymerization kettle temperature fluctuations ≤ ± (0.2 ~ 0.5) ℃.
1 Process introduction and control method study
Reaction kettle weighing using a large flow of low-temperature difference circulation cooling process, the heating medium for saturated steam, jacket cooling water for industrial water. Polymerization kettle reaction process, through the jacket and kettle 4 internal cold pipe to take away the polymerization kettle material polymerization reaction heat, so that the kettle temperature in the polymerization reaction process to maintain stability until the end of the reaction. The temperature control process of polymerization kettle has four stages: warming, transition, constant temperature and discharging. Polymerization kettle capacity, temperature lag is relatively large, due to the polymerization reaction in the reaction of the early, middle and late exothermic are different, and PVC product price fluctuations, the production load is often in a state of shock. Therefore, it is a better improvement measure to adjust the parameters of Kp, Ki and Kd of the main circuit in different periods. On the basis of summarizing the knowledge and experience of excellent operation technicians and instrumentation control technicians, a set of correspondence between operation variables and process description states is summarized, which constitutes a serial+partitioned+FuzzyPID adaptive control algorithm by performing state detection, transformation and inference. In this control scheme, the main regulator adopts online self-tuning control of PID parameters, and the sub regulator adopts variable proportional control, which transforms the proportional parameters in the pre-, mid-, and post-periods of the reactor, and is mainly used for coarse tuning of disturbances. Split-range regulation is adopted to use two regulators as one regulator, thus greatly expanding the adjustable range of the regulator and improving the regulation quality of the process control. The control scheme combines the advantages of conventional control and control, eliminating the tedious process of establishing mathematical debugging, and at the same time avoiding some of the defects of conventional PID control, which can well overcome a variety of disturbances, the polymerization kettle temperature can be implemented accurately control, to ensure that the control accuracy required by the production process.
2 Serial + split-range + FuzzyPID adaptive control strategy
2.1 Main regulator PID parameters adaptive control
Through the combination of load cell, weighing instrument and control system, it can achieve the weighing and measuring work of the reaction tank body and thus control the system. It mainly consists of multiple metering modules, multi-way junction box (including amplifier), weighing instrument, and output multi-range control signal. The system can be applied to a variety of batching equipment, etc.. Users can directly access the PLC system, terminal control system, to realize multi-range control and automation control. The system digitizes the weak weight signals output from the weighing module and obtains high-precision weighing data. Rich digital filtering technology is set up in the software, as well as emergency software to prevent interference with the system from getting out of control.
Main regulator PID parameter adaptive control can detect and analyze uncertain conditions, parameters, delays and disturbances during the control process, and realize the online self-tuning of PID parameters Kp, Ki and Kd by reasoning method, which not only maintains the advantages of conventional PID dosage control system, such as simple principle, easy to use, strong robustness, etc., but also has greater flexibility and adaptability, and better control accuracy. It is a more advanced dosage control system at present.
In the dosage control system, the main regulator is designed as a controller. Considering the simplicity and rapidity of the realization of the dosage control system, a two-dimensional control structure is adopted. In this design, the temperature deviation e and its change rate ec are used as input variables, and the two-dimensional control structure is adopted, and the three parameters of the PID of the main regulator are adjusted in real time after reasoning to complete the temperature control of the polymerization kettle. Since the incremental PID algorithm is characterized by small calculation error, shock-free switching and high reliability, this algorithm is adopted in this system.
Applying the set theory to establish the binary continuous function relationship between parameters Kp, Ki and Kd and the absolute value of system error lel and the absolute value of error change rate lecl, and using the controller to self-tune the PID parameters on-line according to different lel and lecl is the core of the design of this dosage control system. According to the author's many years of practical experience and relevant professional literature, the system is summarized in the process of being controlled for different absolute value of the error lel and absolute value of the error rate of change lecl, the parameters Kp, Ki and Kd of the principle of adjustment:
1) When the error lel is large, in order to make the system have better fast tracking performance, regardless of the trend of the error, should take a larger kp and smaller kd, at the same time, in order to avoid large overshooting of the system response, should be limited to the integral role, take a smaller value of ki, usually take the Ki = 0. When the value of lecl is smaller, Kd to take a larger.
2) When the error iel is in medium size, in order to make the system response has a small overshoot, kp should be made smaller, and at the same time to ensure that the system response speed, ki and kd size should be moderate. When the value of lecl is large, Kd takes a smaller value.
3) When the error lel is small, in order to ensure that the system has a better steady state performance, kp and ki should be made larger, at the same time, in order to avoid the system in the set value near the oscillation, and to consider the system's anti-jamming performance, when lecl is small, kd can be taken as a larger value, when lecl is larger, kd should be taken as a smaller value.
2.2 Sub-regulator variable proportional and split-range control
In the reaction kettle in the early, middle and late, the polymerization reaction is not the same degree of intensity, the reaction of the early, the kettle material has just begun to trigger the polymerization reaction, this time the polymerization reaction is still very unstable, the reaction of the exothermic heat is also relatively small, and the exothermic heat is not uniform. In the middle of the reaction, the polymerization reaction is intense exothermic, exothermic quantity is large, and the temperature rises quickly. Therefore, the dosage control system exists stage by stage nonlinear factors, for these stage by stage characteristics, the proportional parameter of the sub-regulator in different stages of adaptive jacket temperature control, while the use of split-range control, the reaction is milder, adjusted by the small control valve, when the reaction is intense, the reaction is controlled by the large and small control valves at the same time, not only to avoid the jacket temperature drop too quickly caused by the decline in kettle temperature, and also can be the jacket temperature to drop to the appropriate temperature quickly, to ensure the kettle temperature. It can not only avoid the jacket temperature dropping too fast to cause the kettle temperature to drop, but also can quickly reduce the jacket temperature to the appropriate temperature to ensure that the kettle temperature is stably controlled at the set reaction temperature. In specific implementation, the ratio of jacket temperature regulator is calculated according to some actual process parameters and set parameters.
3PID controller design
In this design scheme, the idea of PID parameter self-tuning is to first find out the relationship between the three parameters Kp, Ki and Kd of the PID controller and the absolute value of the error lel and the absolute value of the error rate of change lecl. In operation, by constantly detecting lel and lecl, the three parameters are modified online according to the control rules to meet the different requirements of different lel and lecl on the controller parameters, so as to make the controlled object have good dynamic and static performance.
(1) The establishment of input and output variables
Based on the above analysis of the system, we take the error E and the error change rate ec as the inputs of the controller, and the PID parameters Kp, Ki and Kd of the main regulator as the outputs.
(2) Language description of input and output variables
Set the subset of the language values of the input variables lel and lecl as {negative big, negative middle, negative small, zero, positive small, middle, positive big} and abbreviate it as {NB, NM, NS, ZO, PS, PM, PB}, and quantize the error e and the error change rate ec into the region of (-3.3). Similarly, the subset of the design outputs Kp, Ki and Kd is {ZO, PS, PM, PB}, and it is quantized into the region (0.3).
4 Application effect
Practice shows that the scheme of cascade+split +FuzzyPID adaptive control not only has the advantages of flexible control, fast response speed and strong robustness, but also has the characteristics of high precision of classical PID control. The whole polymerization process time is shortened, which not only meets the control requirements of process production, but also improves the excellent product rate. It is superior to the conventional cascade PID control algorithm in transition process time and maximum overshoot.