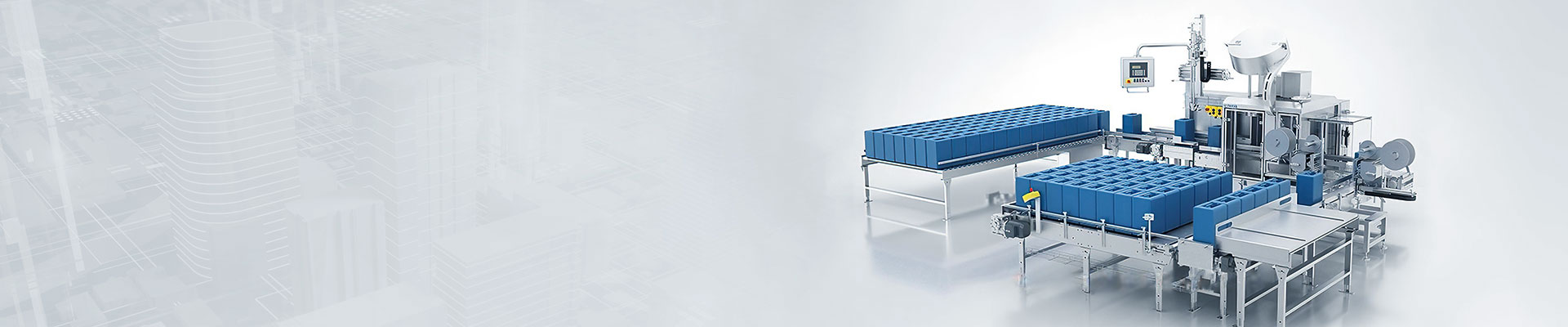
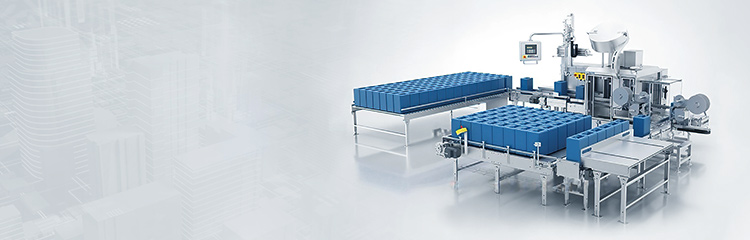
The weighing system has many functions, including Flash program memory, watchdog, EEPROM, synchronous/asynchronous serial port, TWI, SPI, A/D analog-to-digital converter, timer/counter, etc. It can be widely used in one, including reset system to enhance reliability, sleep mode to reduce power consumption and anti-interference, various interrupt systems, timer/counter with diversified functions such as input capture and comparison matching output, and I/O port with replacement function.

The weighing and Batching system (mixer) uses configuration software to complete data acquisition and process control, supports various communication protocols, provides users with various equipment support, colorful dynamic pictures and powerful functions of the system, which makes you easy to operate. The batching system has strong scalability, is easier to integrate with other systems, and protects users' investment more effectively. The redundant station uses two redundant CPUs, which improves the availability and security. According to the principle of alternative, the switch automatically switches from the running system to another system when a fault occurs. In this way, for a single station system, you can provide dual power supplies or industrial Ethernet communication modules for each subsystem and combine them. Safe, reliable, advanced and practical system design selects a mature and advanced distributed computer control system. Under the premise of centralized information management and scientific operation in the production process, the risks are dispersed and the reliability of the system is improved. Various data on site are collected by PLC and transmitted to the central control room for centralized monitoring and management through high-speed network. The host computer in the central control room also transmits control commands to the PLC measurement and control terminal through high-speed network to implement decentralized management of each unit.
The host computer of automatic batching system adopts industrial PC as the upper computer (industrial computer, which is completely compatible with ordinary computers and more suitable for harsh industrial environment)+PLC+ weighing module (or weighing signal sampling board)+weighing sensor+weighing actuator. It can include measurement control host computer (upper computer), weighing software (measurement software/control software), plc weighing instrument, weighing module, hopper scale and bin scale, which can be incremental scale and decrement scale); And in most cases, it is controlled by frequency converter.
The feeding system uses compressed gas as power source and conveying medium. Forced pneumatic conveying is adopted, and the closed pressure vessel (sending tank) is used as the transmitter. Generally, the air source pressure is 0.5 MPa ~ 0.7 MPa, and the operating pressure is 0.3 ~ 0.5 MPa. The sending tank can only adopt intermittent conveying mode, and the conveying distance can reach more than 1000m m.. The transportation of materials in the pipeline at low speed, sand dune state, fluidization or agglomeration state is called positive pressure dense phase transportation. High-pressure roots blower can also be used.
According to the transportation characteristics, the system can also be divided into two ways: positive pressure dense phase dynamic pressure transportation and positive pressure dense phase plug transportation. The way in which materials are transported in the pipeline in the state of medium-low velocity sand dunes or fluidization is called dense-phase dynamic pressure transportation; The way in which materials are transported in the pipeline at a low speed in an agglomerated state is called dense-phase plug transportation.
Basic principle:
Due to the pressure, the material enters the conveying pipe from the sending tank, and the compressed gas is opened and closed by the electromagnetic valve at a certain frequency to form a pulse airflow (air knife). With the help of the pressure of the air knife greater than that of the sending tank, the material is cut into material plugs, and the static pressure difference before and after the material plugs is used as the driving force to push the material forward. After reaching the separation device to separate the material from the gas, the material falls into the silo and the gas is discharged into the atmosphere, thus realizing the conveying.
Product features:
1. Low flow rate but large conveying capacity has little influence on material quality;
2. The system has high pressure and low gas consumption;
3. The control system is automatic, which has high requirements for various electrical components;
4. Multi-point feeding and multi-point discharging are possible;
5. Due to the low material conveying speed, the pipeline and material wear is low;
6. The sending tank (also called warehouse pump) is a pressure vessel, which is a compulsory signing equipment;
7. The air source is generally a screw air compressor, and the post-processing equipment must be matched;
8. The system is reliable and requires little maintenance, but it requires high quality of operating technicians.
9. The conveying gas volume is small, and the separation of material and gas is easy to realize.
10. The working pressure is high, so long-distance transportation can be realized; The booster can be used to realize ultra-long distance transportation;
Basic parameters:
1. Positive pressure dense phase dynamic pressure conveying:
Air velocity: 8m/s- 15m/s,
Transport capacity: 3- 50th,
Transport distance: up to 100-1000m,
Air source type: Roots blower, air compressor.
2. Positive-pressure dense-phase embolic transportation:
Air velocity: 4m/s- 12m/s,
Transport capacity: 2- 20/h,
Transport distance: up to 50- 200m,
Air source type: high-pressure air compressor.